Every business activity incurs costs that play a direct or indirect role in revenue generation. Various factors, including the nature of business activities, influence the magnitude of these costs. Nevertheless, to efficiently manage a company, optimize costs, and implement innovations, it is essential to understand how to classify different expenses.
The most general and commonly used method of cost allocation in companies is the division to direct and indirect costs.
Direct costs can be easily associated with revenue generation. Examples of such costs include the consumption of raw resources, materials, packaging, workers’ wages, energy consumption, equipment uptime. Direct costs can be further classified as:
- direct materials,
- direct labor,
- other direct costs.
Indirect costs are the expenses also related to revenue generation, but not in a direct manner. These include depreciation, tool wear, costs related to purchases, management and administrative costs, outside processing commissioned to contractors. Indirect costs are categorized into:
- department costs,
- general and administrative costs,
- selling costs.
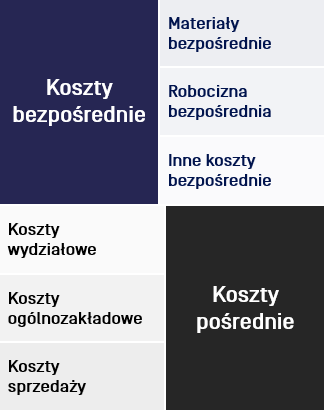
Clearly, these costs are incurred throughout the entire process, spanning from material delivery and manufacturing to the end-to-end sales process to end customers, be it retail or B2B.
A crucial aspect of cost analysis in any manufacturing company is the Technical Manufacturing Cost (TCM). It serves as the foundation for calculating the product price. Simply put, TCM encompasses all costs related to manufacturing a product, including all direct costs and department costs falling into the category of indirect costs.
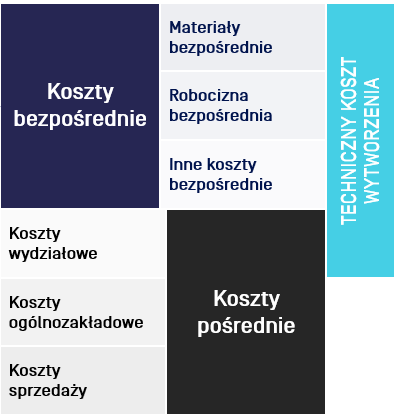
Incorporating general and administrative costs into TMC yields the Total Manufacturing Cost. Additionally, the inclusion of selling costs leads to the calculation of the Cost of Goods Sold.
The first category of direct costs includes direct materials, known as Bills of Materials (BOM). These encompass all elements necessary to manufacture a specific product. How to register the cost of such materials? There are three fundamental methods:
- Backflush: logging based on registered production and BOM. Goods issue notes can be generated automatically based on this list. Batches are typically selected using known algorithms, such as First In, First Out (FIFO), or Last In, First Out (LIFO), depending on the industry.
Benefits: No need to involve an operator or build automated systems.
Drawbacks: There is a potential for errors, for example, if a different material is delivered than indicated by the algorithm.
- Direct registration of consumption: clearly determining each batch and quantity based on actual consumption rather than BOM consumption.
Benefits: High accuracy, relying on actual data.
Drawbacks: Time-consuming, as the data must be manually entered or a suitable data acquisition system based on automation needs to be developed.
- Hybrid Approach: using backflush for standard situations, and engaging an operator in direct registration in non-standard scenarios.
This is a compromise between the two previous approaches: the involvement of an operator or automation is limited but not eliminated entirely.
Acquisition with or without reservation
When discussing consumption registration, two approaches should be noted:
- Reservation Model: Materials are assigned to specific orders.
Benefits: Avoids errors related to using the wrong material from another order. This also eliminates issues of picking materials that belong to another order.
Drawbacks: Requires additional workload. What is more, in non-standard situations, when an element has to be added, an inter-warehouse transfer needs to be made and a reservation needs to be made again, leading to delayed reaction times.
- Non-Reservation Model: if materials are available on the shop floor, workers or machines can simply take them if they fit the process.
Benefits: Streamlined workflow. When a material is available, work can start immediately. There is no delay, no additional document circulation, or the need for transfers and reservations. Logistics is simpler as we deliver a specific material to one production area and not a particular place.
Drawbacks: Potential for taking materials from the wrong order, which can negatively impact the schedule.
Another category of direct costs is direct labor, involving human work and associated compensation. Compensation should align with the time spent on manufacturing. How can we register this time to obtain reliable data?
The operator’s log-in time to a workstation or machine can be identified using:
- Login and password
- PIN
- Work badge
The time spent within a machine’s working area can be registered through a passive RFID (Radio-Frequency Identification) tag gate or antennas receiving data from active tags. This allows registration of entire crews or individual operators.
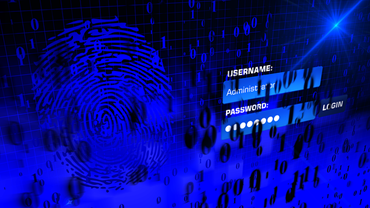
Other direct costs and department costs make up the remaining cost groups within the TMC. Other direct costs include expenses related to material acquisition and relocation, energy and manufacturing utilities, tool wear, outside processing costs, and the costs of preparing and implementing new production. Though not immediately apparent, these areas offer significant opportunities for savings through precise measurement, analysis, planning, and optimization.
Department costs also present numerous opportunities. When viewed in the context of overall company costs, they are not as marginal as one might initially think.If asked whether they would be interested in cutting these costs by 20%, any CFO of a medium or large company would undoubtedly say yes. And often it turns out that achieving this is not as difficult as it may seem.All that’s needed is to analyze these costs in relation to production.
Direct costs are allocated directly to specific products in a straightforward, linear manner. Classifying department costs isn’t quite as simple and it requires an intermediary. These intermediaries are allocation keys that determine the proportion in which a product can be charged with the sum of generated department costs.
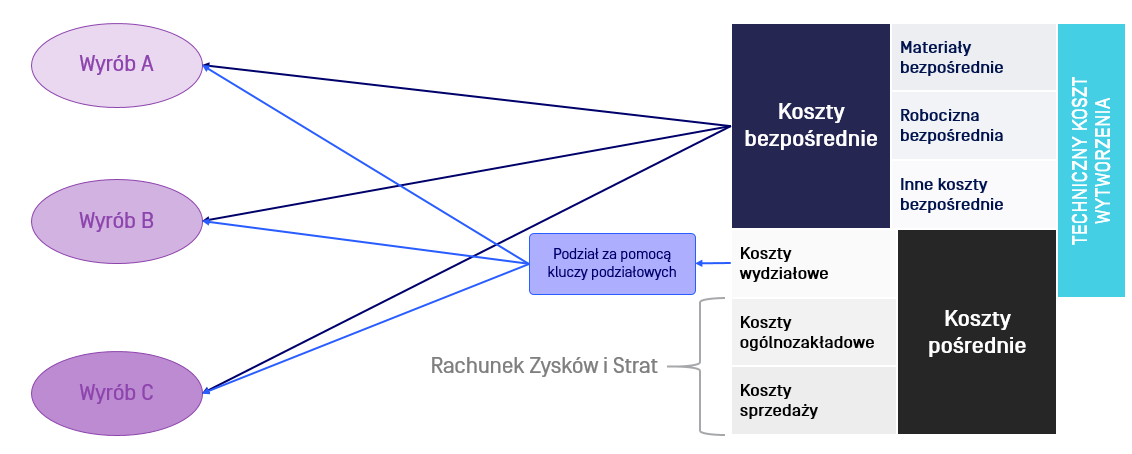
Understanding how to classify different costs provides control over all of a company’s expenses, ensuring that money is spent judiciously. Division into groups and linking expenses to particular products makes it significantly easier to find savings, even in areas where they might not be immediately apparent.
See also
Want to learn more? Visit our Knowledge Base, where you'll find articles and webinars by experts to expand your knowledge.
Check if Digital Transformation is the Answer to Your Company's Needs

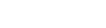
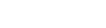
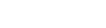
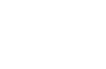
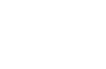
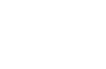
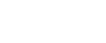
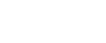
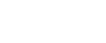
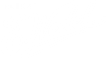
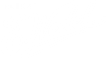
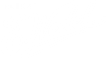
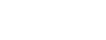
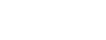
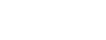






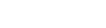
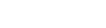
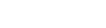
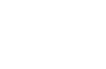
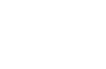
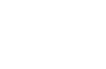
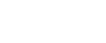
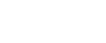
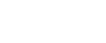
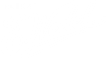
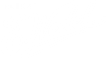
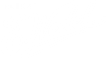
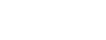
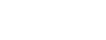
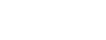






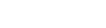
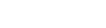
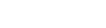
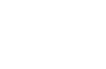
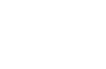
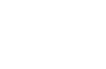
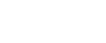
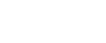
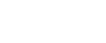
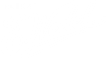
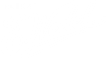
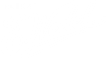
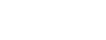
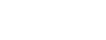
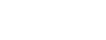






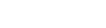
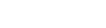
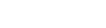
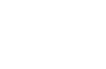
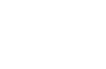
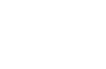
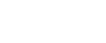
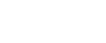
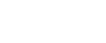
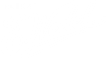
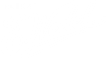
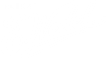
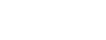
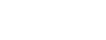
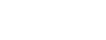


