ImProdis MES – production management and effectiveness monitoring
From efficient data collection to decision verification. We present a comprehensive solution combining a process approach to data analysis and the development of employee competences with the automation of operational data collection and processing.
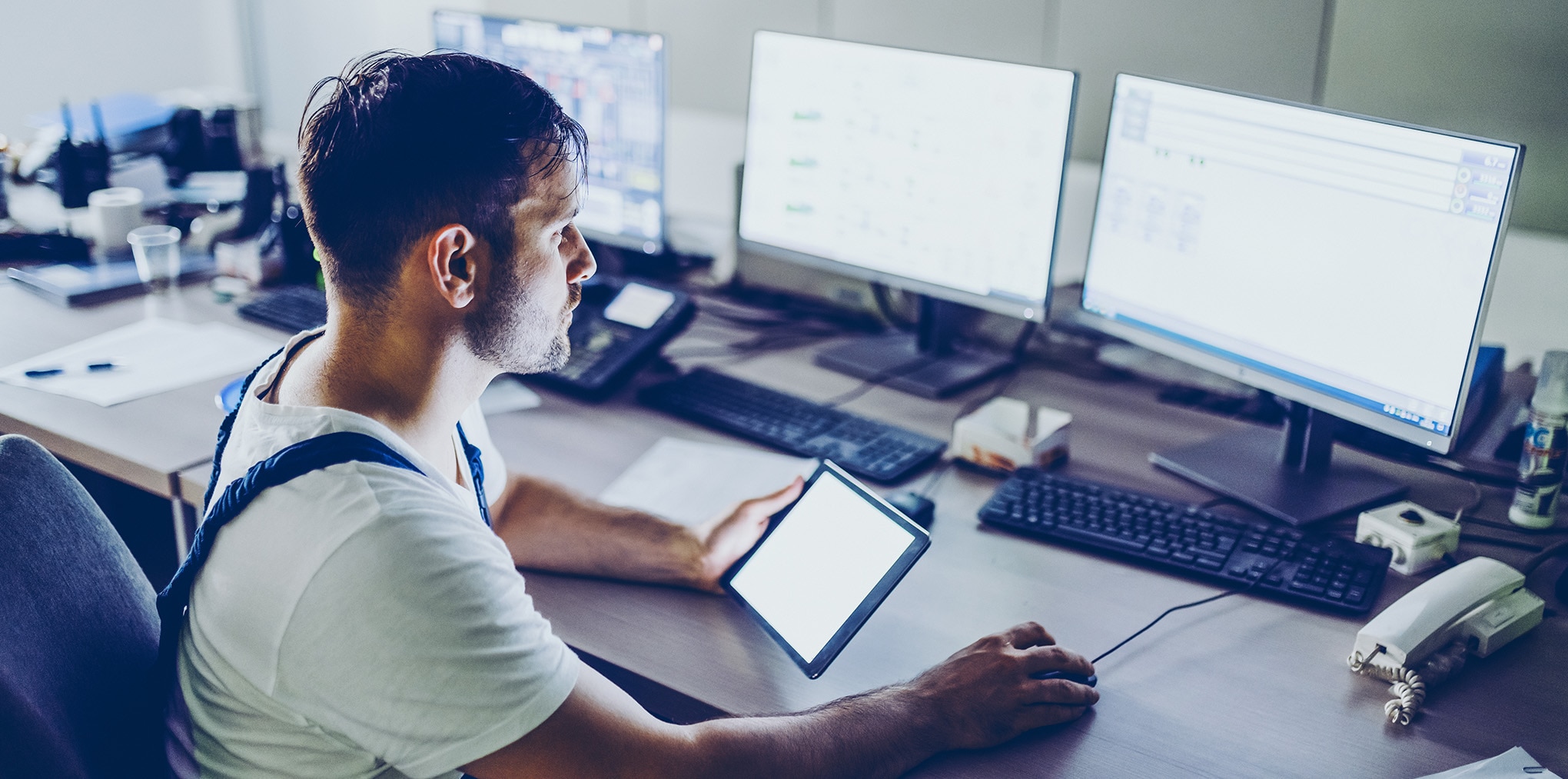
Improdis MES
ImProdis MES is an informational indicator, analytical and reporting system, as well as a set of training and workshops supporting in the preparation and implementation of changes in the organization, consisting of the implementation and digitization (or optimization of the existing) indicator system.
Main Capabilities
Complete set of functions to efficiently manageand document operational processes and material flow in industrial manufacturing plants
Try the ImProdis MES system now!
Starter set with monitoring for 5 machines
from 21,000 PLN annually
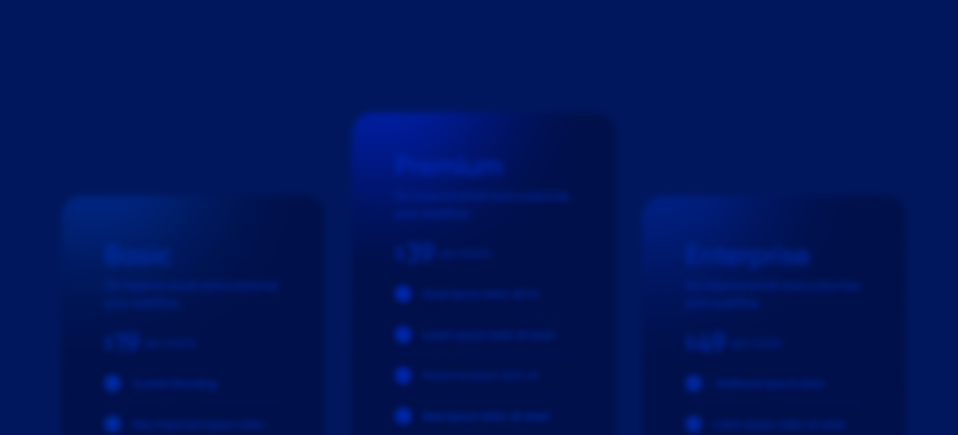
Delivery process
See how we combine agile and waterfall approaches to achieve significant flexibility while guaranteeing high quality, on-time and on-budget.
Step 01
Project preparation
Step 02
Preparation of the implementation concept
Step 03
Preparation of the production environment
Step 04
Implementation
Step 05
Strabilization
Phase
Step 06
Guatantee
Period
We start the project with a deep and comprehensive analysis, during which a great deal of attention is paid to talking to the operators in the gemba. We conduct workshops and meetings at all levels of the organisation gathering information about problems, needs, challenges and goals. For very large projects, the analysis phase can be split off into a separate project. The analysis carried out in this way serves as our upstream kanban and creates the backlog for the next stages.
We divide each implementation phase into smaller sprints, during which selected elements from the backlog are implemented, but we also confront the scope on an ongoing basis with the client, modelling the value to be delivered at the end of the sprint. In the next step, a demo or mock-up is created to show the conceptually designed element.In the final stage, the actual development is carried out and feedback from the User is collected upon completion. Once accepted, the solution is put into production or added to the already created part of the project.
Achieve even more with the APS system integration!
Discover the advanced Advanced Planning and Scheduling (APS) system from PlanetTogether, which allows you to plan work, increase control over resources, and shorten response times to unforeseen events.
See the APS solution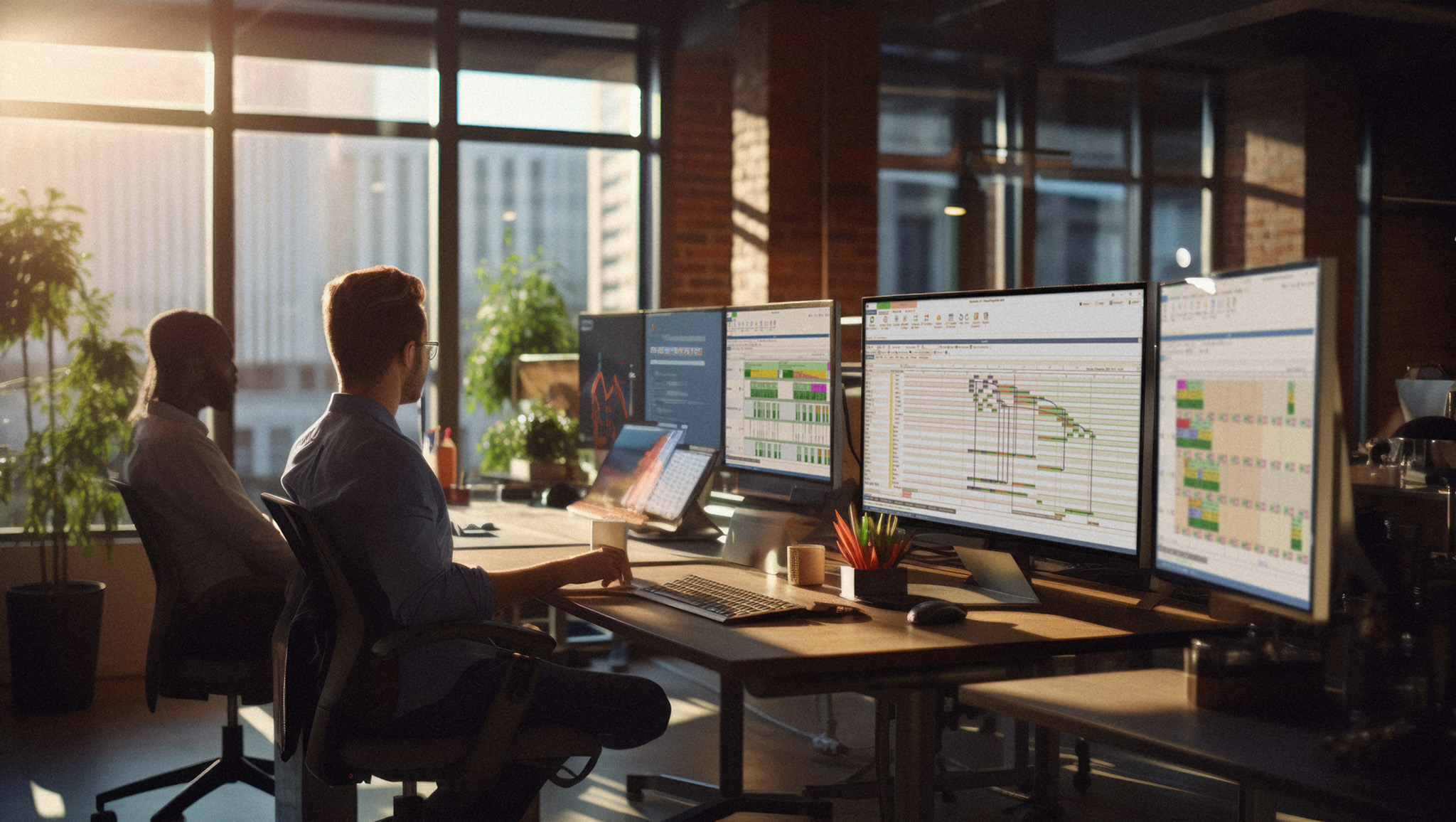
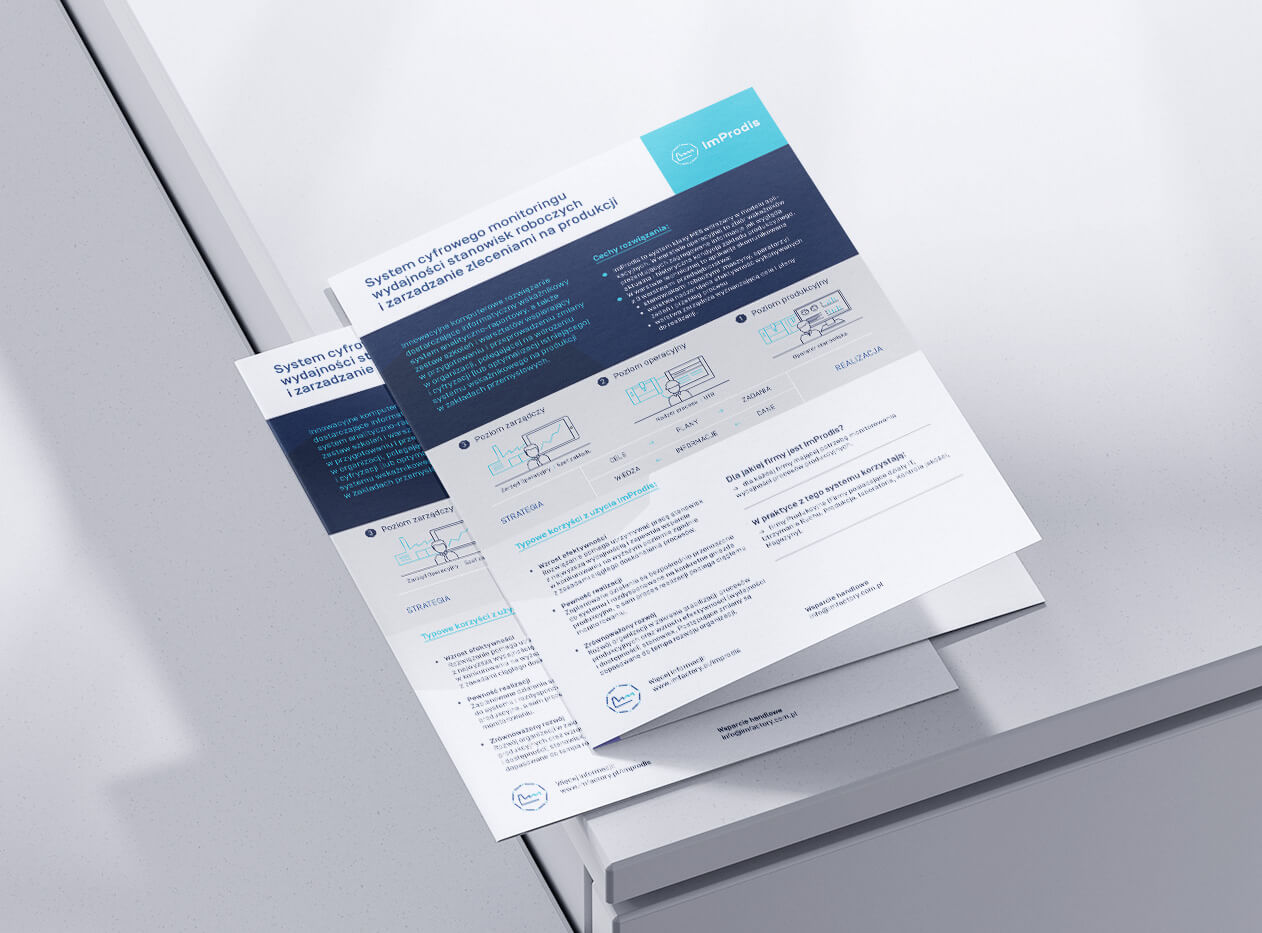
Management by facts
The decision-making process in a manufacturing organization needs to be standardized so that the right and necessary information is always “at hand” and the effectiveness and efficiency of key decisions are increasingly high.
What do we deliver to our clients? How are we operating?
FAQ
See what customers interested in the ImGosystem most frequently ask about and expand your knowledge on this topic.
ImProdis MES is an informational indicator, analytical and reporting system, as well as a set of training and workshops supporting in the preparation and implementation of changes in the organization, consisting of the implementation and digitization (or optimization of the existing) indicator system.
Using the ImProdis MES positively affects OEE and productivity. It helps improve product quality and ensure better equipment availability. Implementing the ImProdis MES can also contribute to reducing production costs.
The ImProdis MES offers a variety of integration possibilities. The most commonly recommended option is the use of an Enterprise Service Bus (ESB), which organizes and secures the continuity of communication in key channels, such as retrieving orders from the ERP and posting production or fetching the schedule from the APS and reporting back on plan execution progress. Other integration examples include setting up tasks in the CMMS for maintenance departments after a workstation failure is detected, or reporting component demands in the WMS.
Just like any other project, the ImProdis MES implementation project begins by defining the problems, needs, or challenges the system should address and to what extent. Only after establishing these matters can we begin the work with identifying key users, project stakeholders, taking inventory of existing machinery and systems, and specifying the requirements. At this stage, involving an external consultant can be beneficial.
Starting the implementation of the ImProdis MES is best initiated by preparing a demonstration version, such as a Proof of Concept or Proof of Value. This involves implementing a version of the system limited in functionality or scope, showcasing that it will be capable of fulfilling the project’s main objectives. This phase serves as the business justification for the investment and results in the delivery of the Minimal Value Proposition (MVP).
The cost of the ImProdis MES varies based on many factors and can range from thousands to tens of thousands PLN. Key factors determining the ImProdis MES cost include the number of connected machines and automatic signals, user count, functional scope, licensing approach (perpetual or subscription), and hosting method (local, cloud, hybrid).
ImProdis MES is used in all industries related to manufacturing, but it excells in discrete manufacturing.
Post-implementation support is divided into warranty and post-warranty (maintenance) phases. Irrespective of the period, post-implementation support involves handling Service Requests (SR), which include preparing patches and workarounds for reported errors, software version updates, system performance monitoring, and other issues to ensure continuous operation according to SLA provisions. Another stream of requests is Functional Requests (FR), aimed at introducing improvements, optimizations, configuration changes, adding new features or areas – in essence, expanding the system. Additionally, during Gemba walks in the facility, consultants assess system usage and gather feedback directly from users.
Common areas of ImProdis MES development include: • adding new functions not yet implemented, • expanding the system to new areas, such as previously undigitized departments, • integrating with external systems lacking communication channels. Naturally, these areas can occur in various combinations and scopes.
ImProdis MES stores data in a standard Microsoft SQL or PostgreSQL database, which is accessible to users with appropriate permissions. This accessibility allows the ImProdis MES database to be seamlessly connected as a data source to any BI solution and other tools, including Excel spreadsheets, Google Sheets, Minitab, or Statistica.
The ImProdis MES serves the purpose of managing production execution and monitoring the equipment. This functionality is achieved with Device Integration Platform (DIP), which acts as a middleware between the deterministic OT world housing the machines and automation systems, and the event-driven IT world where the ImProdis MES operates. AVEVA System Platform is an example of such a solution, offering integration with both the ImProdis MES and the execution devices and control systems. This setup provides a wide array of communication drivers available as standard.
The ImProdis MES serves as a valuable source of accurate manufacturing data for departments focused on Continuous Improvement, Lean, and SixSigma. These departments can leverage this data to identify sources and root causes of losses, plan corrective and optimization actions, and monitor progress. 13.
The ImProdis MES provides information on various indicators, including Overall Equipment Effectiveness (OEE) and its components: performance, availability and quality. The ImProdis MES openness to reporting allows for the calculation of additional KPIs that can be defined in custom reports using the rich data source provided by the ImProdis MES.
Check if Digital Transformation is the Answer to Your Company’s Needs
The Free Consultation Process:

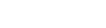
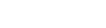
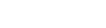
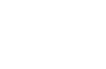
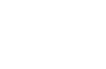
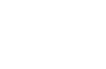
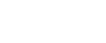
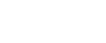
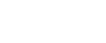
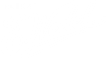
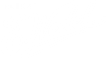
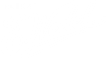
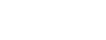
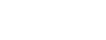
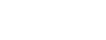






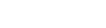
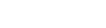
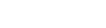
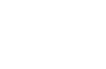
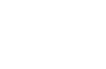
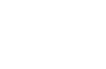
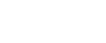
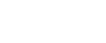
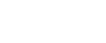
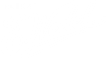
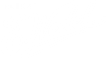
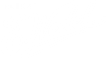
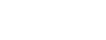
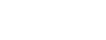
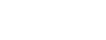






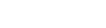
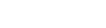
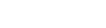
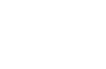
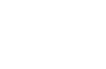
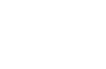
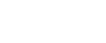
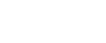
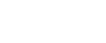
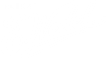
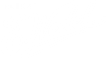
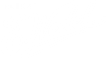
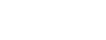
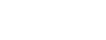
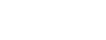






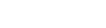
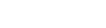
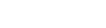
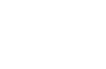
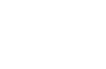
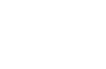
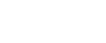
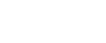
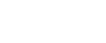
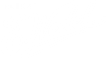
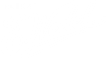
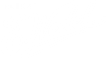
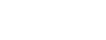
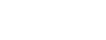
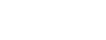


