According to the international ANSI/ISA-95 standard, which defines concepts related to management systems in companies and specifies how data should flow between them, there are four levels of a business hierarchy. The lowest level represents the physical plant, including machinery, equipment, and sensors. The second level is the process control layer, with controllers, object controllers, as well as monitoring and visualization devices and software, such as operator panels and HMI/SCADA stations.
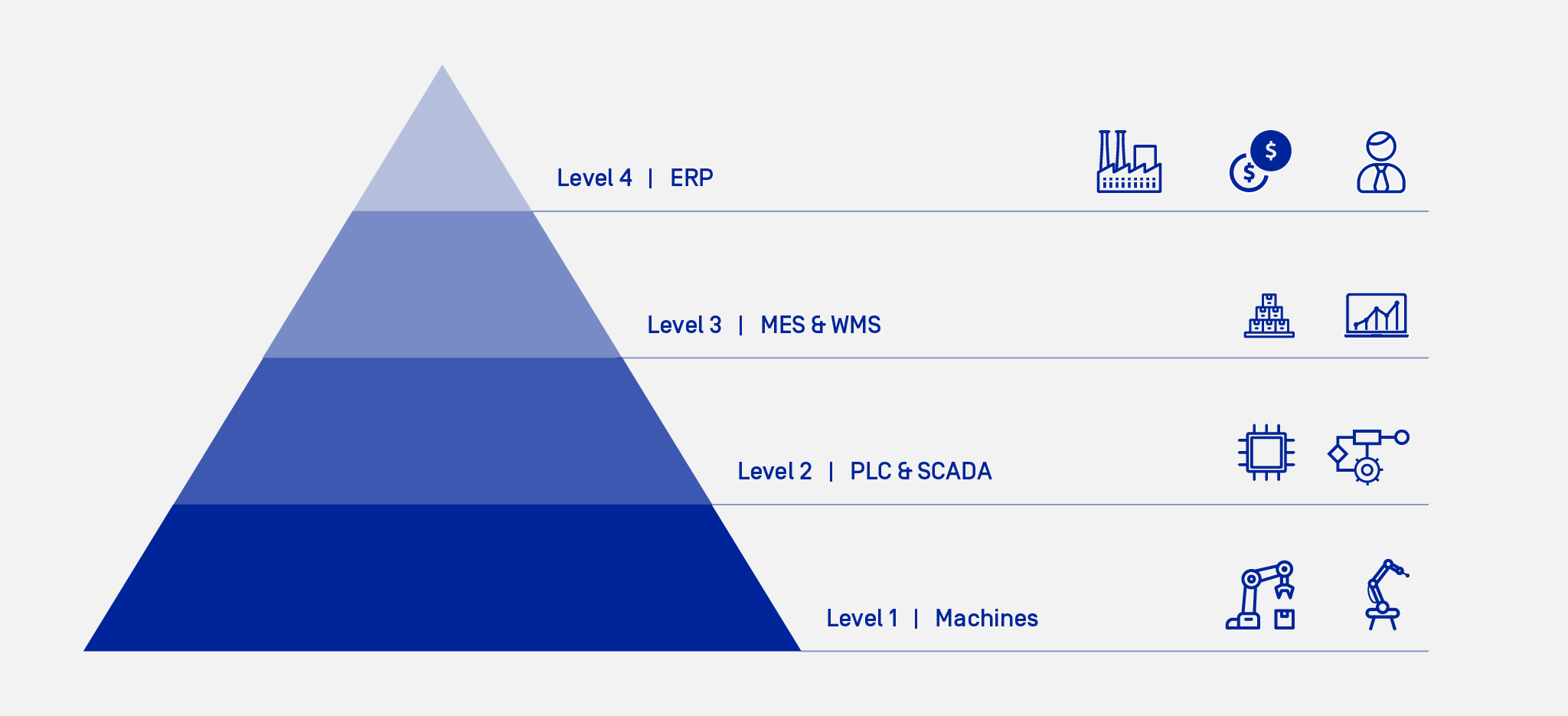
Four levels of control and management systems in a company. Source: ImFactory
The remaining top two levels comprise the management layer. The uppermost fourth level encompasses systems that manage the entire company and its finances, planning, and logistics. This is where the Enterprise Resource Planning (ERP) system is positioned. The third level, in turn, is the production management layer, responsible for scheduling, monitoring task execution, and optimizing the manufacturing process. It is at this level that Manufacturing Execution Systems (MES) are placed, serving as a bridge between the production and business layers.
The tasks performed by an MES can be simplified into three main areas:
- managing production efficiency,
- managing production orders and tasks,
- managing production quality.
By covering these three areas, an MES enables full control over the entire production process. However, it’s worth noting that it’s also possible to implement a system whose role will be to cover only some of these tasks.
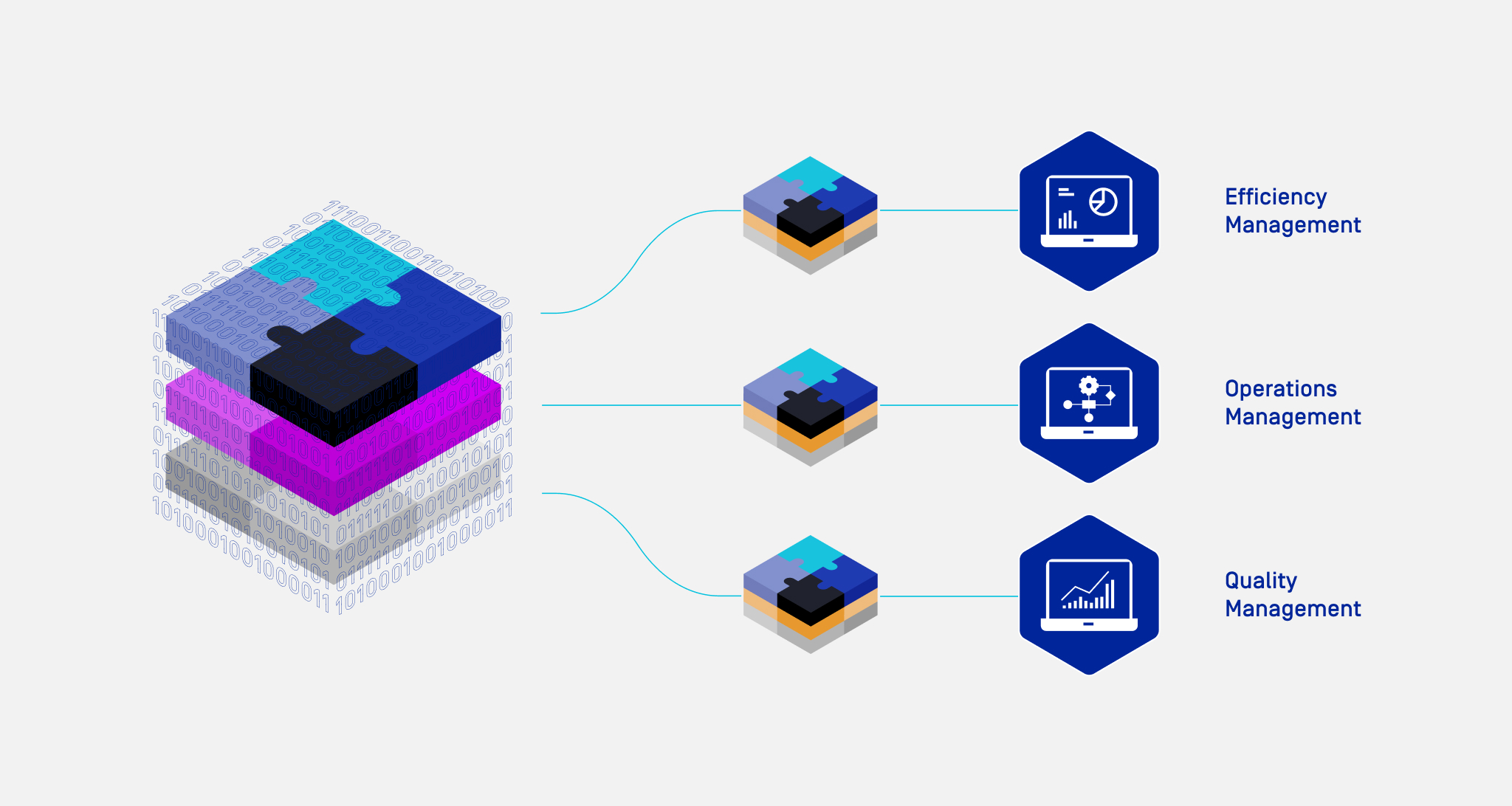
MES modules. Source: ImFactory