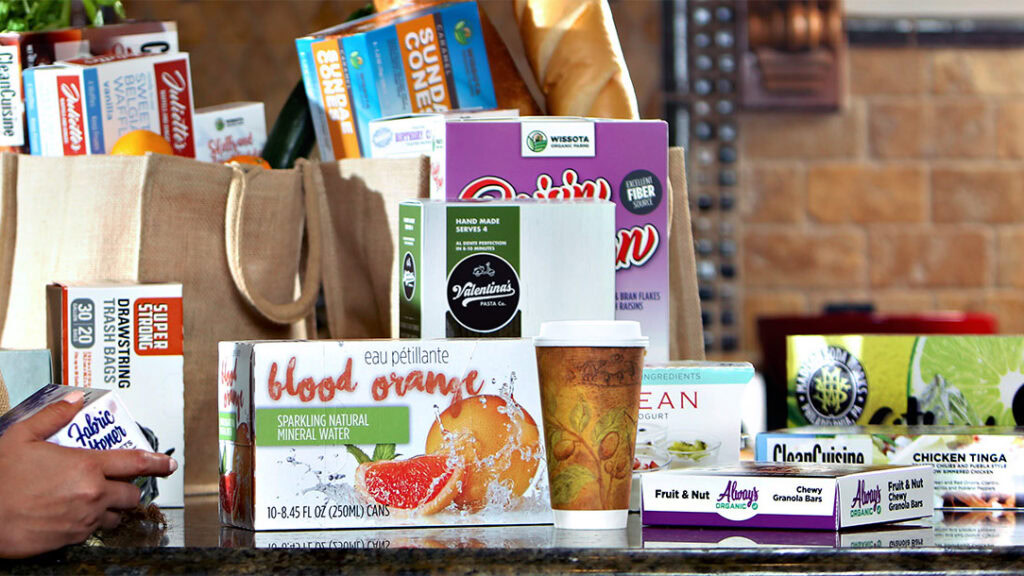
Driving strategic planning and operational excellence in international packaging leader GPI
CLIENT: Graphic Packaging International
INDUSTRY: Packaging
CUSTOMER PROFILE: Graphic Packaging International
Dean Dietrich, with 25 years of manufacturing experience, discusses his role as Vice President of Sales and Operations Support in a make-to-order manufacturing company. The company specializes in producing unique SKU variations for consumer packaging, particularly in the food industry. Dean was managing a $2.1 billion business unit that had 20 plus manufacturing or converting sites servicing 2000 customers and shipping more than 45000 different SKUs annually.
PlanetTogether was founded in 2004 as the culmination of decades of academic research at Cornell University. Combined with over 20 years of industry experience, we focus on making manufacturers more successful by applying software that solves production planning and scheduling problems. With our powerful, easy to use, integrated software tools and education, manufacturers can attract and retain customers by delivering faster — and do it more profitably by minimizing resource and inventory costs. PlanetTogether is on a mission to make the planet more productive, one manufacturer at a time.
One of the major challenges faced by large multinational companies is maintaining consistency in their operations and relationships with customers and suppliers. Mergers, acquisitions, and different processes can create variations in culture and approach, making it difficult to build a consistent brand and provide the required flexibility for customers.
Dean Dietrich, VP at Graphic Packaging International, explains that “We needed a tool like PlanetTogether which provides structure, consistency, and execution at the individual plant level while enabling flexibility and optimization across the manufacturing footprint. This tool proved essential for our large-scale organization, complementing the efforts to build a successful brand and meet customer demands. We explored various ERP systems, including those tailored to their printing industry, but none like PlanetTogether.”
Graphic Packaging International sought a solution outside of their SAP enterprise system as the available planning and scheduling tools were inadequate.
The company conducted a Proof of Concept to demonstrate the benefits of the software using live data from their enterprise system.
Dietrich reveals that “The proof of concept allowed us to fine-tune our capital request and show the tangible results of implementing PlanetTogether. The system helped improve planning, scheduling, and customer satisfaction while also considering operational efficiencies and trade-offs.”
The company had a good experience working with PlanetTogether, finding them knowledgeable and easy to work with.
Dean states that “I considered the flexibility, cost, and risks associated with choosing a smaller, more nimble provider like PlanetTogether compared to larger, more established ones. The implementation impacted individual schedulers, freeing them up to focus on improving the business rather than spending time on manual scheduling tasks.”
Graphic Packaging International also ensured that the system could be adapted for other divisions within the organization. The IT organization gave positive feedback on the resources provided by PlanetTogether.
Dean explains that “Business today faced the challenge of meeting increasing demands for shorter lead times and better profitability while maintaining top-line growth. To address these challenges, we turned to PlanetTogether, a tool that provided objective information to guide decision-making and freed up time and energy within the organization. PlanetTogether helped to reduce infighting between sales and operations as well as frustration from the back-office support team.”
By working on the master data and being realistic about their capabilities, Dean’s team was able to provide meaningful information to their customers and suppliers. PlanetTogether proved to be an essential tool in addressing the elephant in the room and meeting the demands of the ever-changing business landscape.
According to Dean, “The more flexibility we have in optimizing across our manufacturing footprint, the more flexibility we’re granted from our customers’ perspective, the easier it is for us to optimize our business, satisfy all 2000 customers in a way that’s not cost-prohibited.”
Planet Together is known for stellar performance in production scheduling for multi-plant manufacturers. Founded in 2004 by Cornell University engineers, this San Diego-based software developer thrives on the challenge of algorithms and easy-to-use tools to drive manufacturing efficiency. Planet’s showcase product is the PlanetTogether APS production scheduling platform, whose muscular functionality cuts inventory and labor costs in half, boosts productivity by double digits, and connects multi-plant operations with precision. Fully customizable, PlanetTogether integrates to virtually any ERP system, typically in one to three months, and pays for itself in six.
See also
Want to learn more? Visit our Knowledge Base, where you'll find articles and webinars by experts to expand your knowledge.
Check if Digital Transformation is the Answer to Your Company's Needs
The Free Consultation Process:

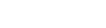
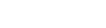
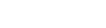
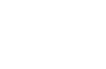
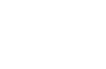
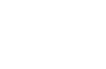
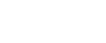
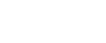
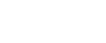
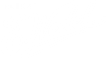
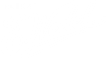
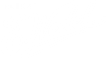
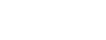
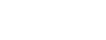
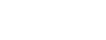






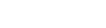
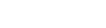
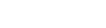
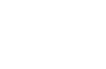
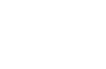
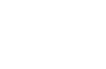
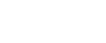
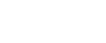
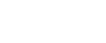
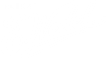
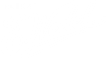
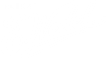
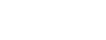
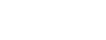
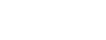






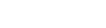
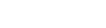
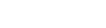
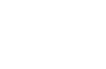
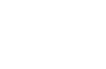
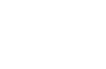
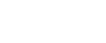
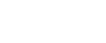
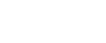
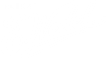
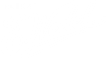
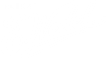
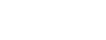
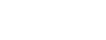
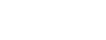






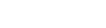
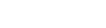
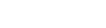
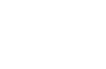
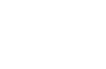
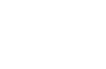
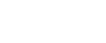
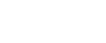
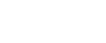
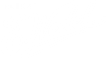
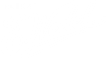
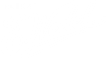
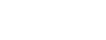
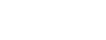
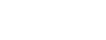


