AVEVA™ Manufacturing Execution System
Maximize the productivity, quality, and compliance of manufacturing operations. Lower the cost and complexity of MES standardization.
Learn more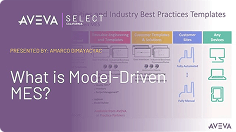
Watch the video
Present by: Amarco Dimayacyac
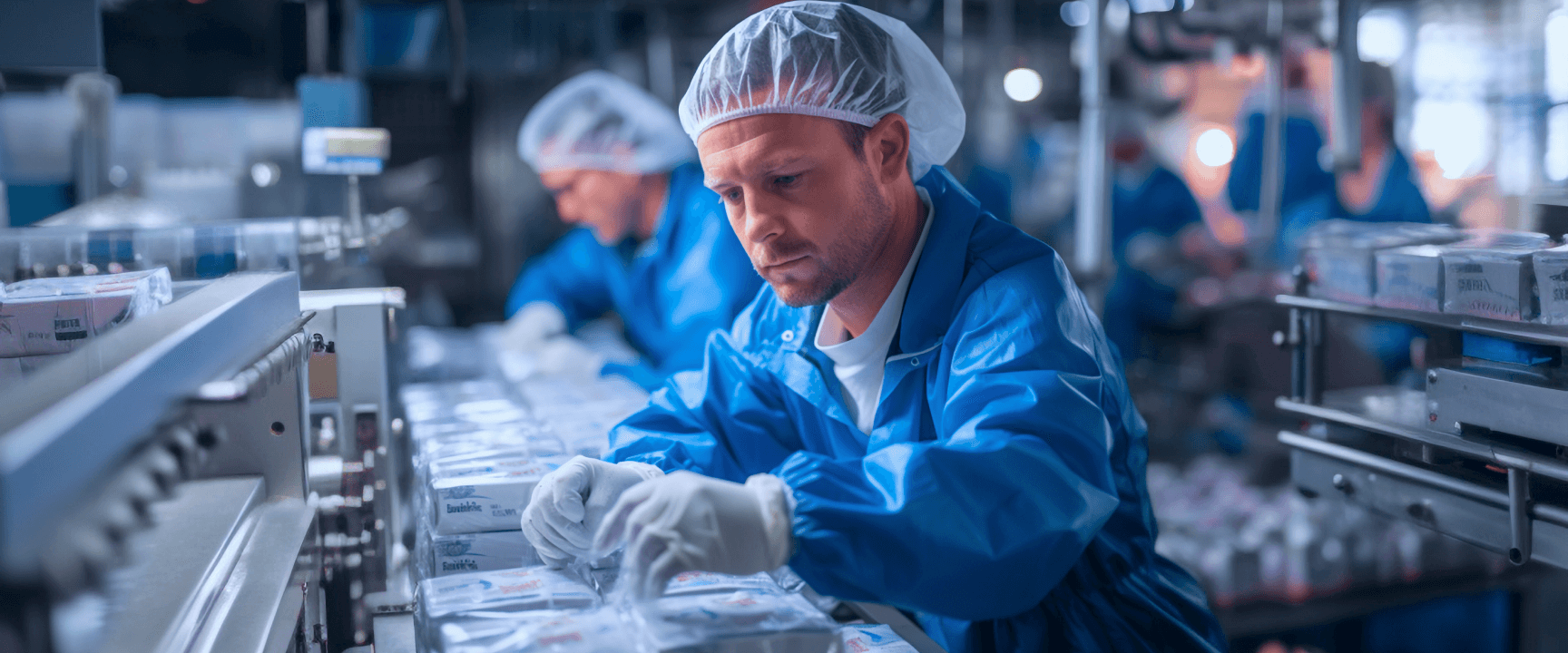
Key Benefits
Why should you implement an MES? Explore the major benefits for your company
Quality
Improvement
More Equipment
Uptime
Reduction
in Manufacturing Costs
Increased
Productivity
OEE
Improvement
Main Capabilities
Complete set of functions to efficiently manageand document operational processes and material flow in industrial manufacturing plants
Delivery process
See how we combine agile and waterfall approaches to achieve significant flexibility while guaranteeing high quality, on-time and on-budget.
Step 01
Project preparation
Step 02
Preparation of the implementation concept
Step 03
Preparation
of the production
environment
Step 04
Implementation
Step 05
Stabilization
Phase
Step 06
Guatantee
Period
We start the project with a deep and comprehensive analysis, during which a great deal of attention is paid to talking to the operators in the gemba. We conduct workshops and meetings at all levels of the organisation gathering information about problems, needs, challenges and goals. For very large projects, the analysis phase can be split off into a separate project. The analysis carried out in this way serves as our upstream kanban and creates the backlog for the next stages.
We divide each implementation phase into smaller sprints, during which selected elements from the backlog are implemented, but we also confront the scope on an ongoing basis with the client, modelling the value to be delivered at the end of the sprint. In the next step, a demo or mock-up is created to show the conceptually designed element.In the final stage, the actual development is carried out and feedback from the User is collected upon completion. Once accepted, the solution is put into production or added to the already created part of the project.
What is Modern-Driven MES?
All you need
A single platform for the digital transformation in manufacturing operations
An open engineering and runtime platform
A flexible environment that allows you to create, develop and deploy industrial applications perfectly suited to your production needs. Unbounded, with full control over the architecture.
A scalable MES application with broad manufacturing management functionality
From a single line to an entire factory, the system grows with your business. It provides monitoring, reporting, order accounting and efficiency analysis – all in one place.
A reusable work process and related user experience modeling approach
Optimized processes and interfaces that are not only functional, but also intuitive for the user. Standardization makes implementations faster and daily work simpler and more efficient.
Success Stories
Get inspired by the successes of our customers achieved through the implementation of the AVEVA MES
We assist in digitalization
Among our satisfied clients, we serve companies across a diverse range of industries, including food, consumer packaged goods (CPG), pharmaceuticals, automotive, and manufacturers of construction materials.
FAQ
Expand your knowledge on the topic by seeing the most frequently asked questions from clients interested in creating a Manufacturing Execution System (MES)
An MES, short for Manufacturing Execution System, is an IT solution that facilitates the digital flow of production orders, communication and monitoring the progress of the production plan, and management and supervision over the equipment. The functionalities of the MES are specified in the ANSI\ISA-95 standard.
Using the MES positively affects OEE and productivity. It helps improve product quality and ensure better equipment availability. Implementing the MES can also contribute to reducing production costs.
Integracja systemów MES i APS pozwala na pełną synchronizację operacji produkcyjnych z optymalnym harmonogramem. Dzięki temu firmy mogą szybko reagować na zmiany, optymalizować procesy produkcyjne, minimalizować marnotrawstwo i zapewniać zgodność z normami jakościowymi i regulacyjnymi.
The MES offers a variety of integration possibilities. The most commonly recommended option is the use of an Enterprise Service Bus (ESB), which organizes and secures the continuity of communication in key channels, such as retrieving orders from the ERP and posting production or fetching the schedule from the APS and reporting back on plan execution progress. Other integration examples include setting up tasks in the CMMS for maintenance departments after a workstation failure is detected, or reporting component demands in the WMS.
The revolutionary Model Driven MES approach involves a shift in mindset. Unlike the traditional approach, where organizational processes are tailored to fit the system’s operations, with MDM, processes within the organization are first studied and modeled. Subsequently, MES functions are implemented precisely in those areas and moments where they are required by the process. In this way, MDM promotes a company’s best practices and experiences, rather than enforcing a one–fits–all solution. The Business Process Modeling (BPM) utilized in this approach allows for versioning and modifying established standards, facilitating their transfer to other areas.
Just like any other project, the MES implementation project begins by defining the problems, needs, or challenges the system should address and to what extent. Only after establishing these matters can we begin the work with identifying key users, project stakeholders, taking inventory of existing machinery and systems, and specifying the requirements. At this stage, involving an external consultant can be beneficial.
Starting the construction of the MES is best initiated by preparing a demonstration version, such as a Proof of Concept or Proof of Value. This involves implementing a version of the system limited in functionality or scope, showcasing that it will be capable of fulfilling the project’s main objectives. This phase serves as the business justification for the investment and results in the delivery of the Minimal Value Proposition (MVP).
The cost of the MES varies based on many factors and can range from tens of thousands to several million PLN. Key factors determining the MES cost include the number of connected machines and automatic signals, user count, functional scope, licensing approach (perpetual or subscription), and hosting method (local, cloud, hybrid).
A typical MES implementation project should outline the following cost components: pre-implementation analysis service, programming work related to system installation, configuration and customization, integration with shopfloor equipment, integration with other systems, such as ERP or APS, costs, or at least hardware requirements, necessary for deployment (server environment, client terminals, and peripherals if needed), MES licensing fees, third-party licensing fees, e.g., database systems (or at least requirements for such), SLA and post-warranty costs (maintenance). scope of IT-related tasks for the ordering party, e.g., ERP system maintenance, warranty costs and terms, SLA and post-warranty costs (maintenance).
When selecting an MES provider, it’s important to consider whether their proposed solution holds a strong market position, as well as the provider’s own reputation. You should verify whether they consistently release software updates, have a product development roadmap, and offer support services for patches and fixes. Additionally, it’s valuable to assess the availability of implementation partners for the chosen solution, so that you are not limited to collaborating with a single company, which could potentially jeopardize the system’s operational continuity.
When selecting an MES provider, it’s important to consider whether their proposed solution holds a strong market position, as well as the provider’s own reputation. You should verify whether they consistently release software updates, have a product development roadmap, and offer support services for patches and fiProduct training for the AVEVA MES is divided into three main blocks related to the system’s functionalities: perfromance management and monitoring, production processes and operations modeling, quality control and SPC. Additionally, the training program includes workshops on the AVEVA System Platform, which enables integration with shopfloor equipment, SCADA functions (including visualization), and the Enterprise Integration tool (data bus for communication with other business systems). These training sessions are conducted by certified AVEVA training centers worldwide. xes. Additionally, it’s valuable to assess the availability of implementation partners for the chosen solution, so that you are not limited to collaborating with a single company, which could potentially jeopardize the system’s operational continuity.
MES are used in all industries related to manufacturing, encompassing process, batch, and discrete manufacturing.
ERP systems were designed to support high-level management of enterprise resources, primarily in the areas of inventory management, order management, and financial transactions. As a result, they operate with data aggregations over longer periods, often considering not only days but weeks, months, or even years. On the other hand, MES were developed to address the growing needs for operational management of manufacturing processes, leading to more detailed data and shorter timeframes, such as a day, a specific shift, or hours. Additionally, MES can provide real-time information for selected processes.
Post-implementation support is divided into warranty and post-warranty (maintenance) phases. Irrespective of the period, post-implementation support involves handling Service Requests (SR), which include preparing patches and workarounds for reported errors, software version updates, system performance monitoring, and other issues to ensure continuous operation according to SLA provisions. Another stream of requests is Functional Requests (FR), aimed at introducing improvements, optimizations, configuration changes, adding new features or areas – in essence, expanding the system. Additionally, during Gemba walks in the facility, consultants assess system usage and gather feedback directly from users.
Common areas of MES development include: adding new functions not yet implemented, expanding the system to new areas, such as previously undigitized departments, integrating with external systems lacking communication channels. Naturally, these areas can occur in various combinations and scopes.
Modern MES offer robust security mechanisms, beginning with standard protections derived from the database engine used. For AVEVA MES, this engine is Microsoft SQL Server, and its security is managed by Microsoft. AVEVA MES allows configuring user authentication processes using both an internal mechanism and Active Directory, which significantly simplifies the process of managing access and permissions from the IT department. What is more, AVEVA solutions provide encrypted communication through Archestra Identity Manager, facilitating data transfer between AVEVA systems.
Recording the history of product creation, known as genealogy or traceability, is one of the MES functionalities as outlined in the ANSI-95 standard. However, it is important to note that not all MES offer a complete range of functionalities, and specific functions may require corresponding modules.
AVEVA MES stores data in a standard Microsoft SQL database, which is accessible to users with appropriate permissions. This accessibility allows the MES database to be seamlessly connected as a data source to any BI solution and other tools, including Excel spreadsheets, Google Sheets, Minitab, or Statistica.
The MES serves the purpose of managing production execution and monitoring the equipment. This functionality is achieved with Device Integration Platform (DIP), which acts as a middleware between the deterministic OT world housing the machines and automation systems, and the event-driven IT world where the MES operates. AVEVA System Platform is an example of such a solution, offering native integration with both the MES and the execution devices and control systems. This setup provides a wide array of communication drivers available as standard.
The MES serves as a valuable source of accurate manufacturing data for departments focused on Continuous Improvement, Lean, and SixSigma. These departments can leverage this data to identify sources and root causes of losses, plan corrective and optimization actions, and monitor progress.
A typical MES provides information on various indicators, including Overall Equipment Effectiveness (OEE) and its components: performance, availability and quality. It also covers Mean Time to Repair (MTTR), Mean Time Before Failure (MTBF), and for quality modules, metrics such as % Out of Scope (OOS) determining the percentage of samples outside specifications, as well as Cp and Cpk (process capability). The MES’s openness to reporting allows for the calculation of additional KPIs that can be defined in custom reports using the rich data source provided by the MES.
Tracking Work in Progress (WIP) is another function of the MES outlined in the ANSI/ISA-95 standard. However, an MES doesn’t always provide this functionality, or it may require specific modules.
Quality modules within the MES enable the definition of in-line process control quality tests according to predefined patterns. These tests can be conducted cyclically based on production volume or in response to specific events. Each test specifies a set of measured characteristics (quantities) and corresponding limits for interpretation.
SPC/SQC control cards are part of the MES’s quality module. The AVEVA MES includes a set of frequently utilized cards for numerical evaluations and alternative evaluations (non-compliance). This enables monitoring of both continuous and discrete processes.
Operator instructions are an integral component of the MES. Depending on the chosen interface, these instructions can be presented in various formats, such as PDF files, presentations, videos, or CAD files.
Check if Digital Transformation is the Answer to Your Company’s Needs



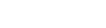
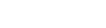
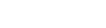
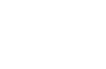
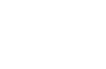
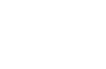
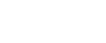
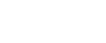
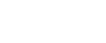
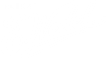
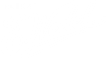
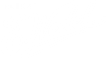
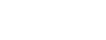
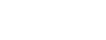
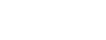






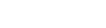
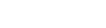
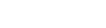
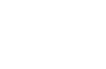
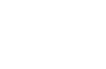
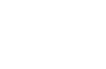
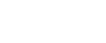
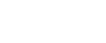
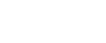
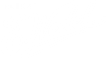
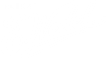
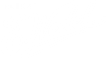
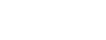
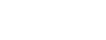
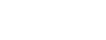






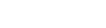
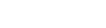
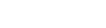
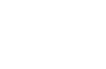
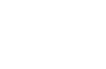
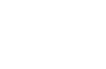
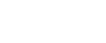
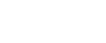
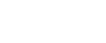
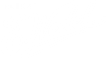
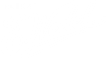
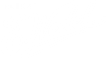
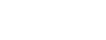
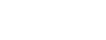
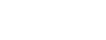






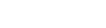
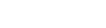
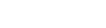
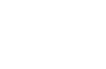
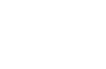
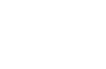
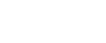
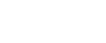
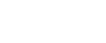
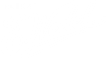
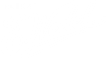
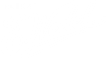
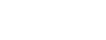
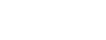
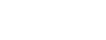


