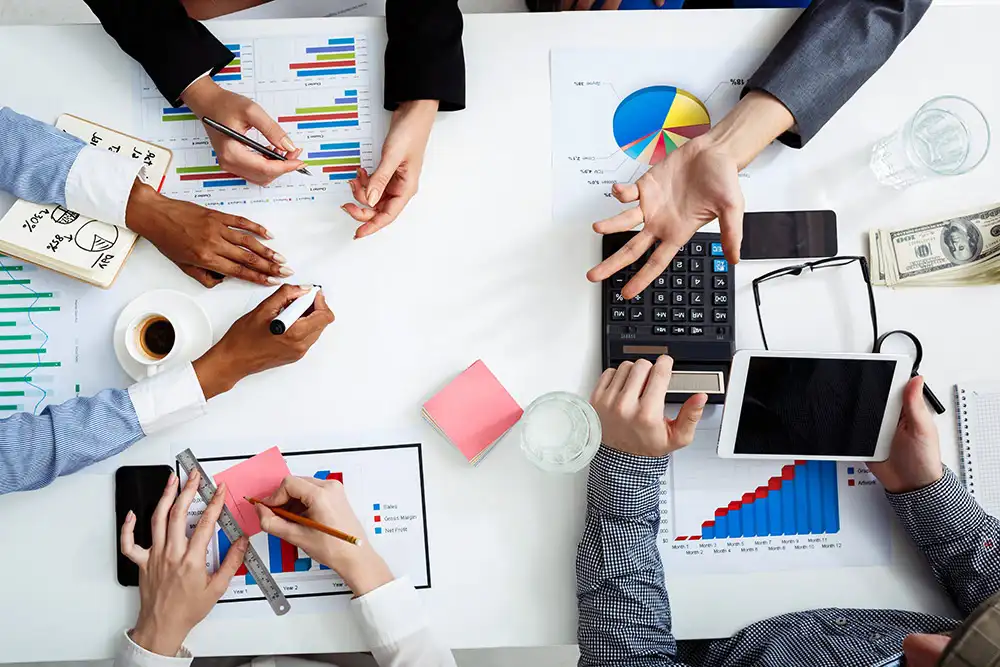
Total Manufacturing Cost and Cost Allocation in a Company, Part 3: The Role of MES and ERP in Cost Management
In today’s landscape, envisioning the day-to-day operations of manufacturing companies without sophisticated systems is challenging. These systems automate numerous tasks, relieving the workload of employees while providing essential data. The systems employed by manufacturing companies vary, each serving a unique role – from recording operational time and machinery usage to collecting process-related information. In today’s article, we will delve into a closer examination of two systems utilized at different tiers within a manufacturing enterprise – MES and ERP systems – highlighting the advantages of their seamless integration.
The ISA-95 model is a representation of the hierarchical knowledge structure in a manufacturing company – beginning with raw data, which is then processed, contextualized, and presented in a manner conducive to informed decision-making. The model comprises four principal levels:
- Level 1: Shopfloor – The production layer situated at the bottom. Data located here is raw, lacking any context. We only know where it comes from: programmable controllers, robots, machines, sensors, additional detectors– essentially, anything generating signals.
- Level 2: Process Control – This layer involves SCADA, a data acquisition software exchanging information with the Shopfloor through manufacturing communication protocols. Raw data transforms into ‘tags,’ defining the nature of the data.
- Level 3: Operational Management – In this layer, data is structured into objects with defined relationships and contexts. This can be achieved through systems like MES. Additionally, SCADA facilitates process analysis on this level.
- Level 4: Business –This top layer houses business systems such as ERP, BI for reporting, specialized tools like LIMS, and others supporting engineers in process optimization, such as CAD tools.
Simplified structure of information flow in a company. Source: ImFactory
The above segmentation provides a comprehensive context and an extended time perspective for operational activities, offering a closer insight into what happens within a production process. However, for the model to function optimally, the layers of operational management and business must be supplied with identical data.
Therefore, the role of an Enterprise Service Bus (ESB) between the third and fourth levels is invaluable. Data shared across these levels ensures a single source of truth, eliminating errors and unnecessary costs associated with manual data entry or manual processing of such data between the two systems. The ESB is the element that binds the structure into a cohesive whole.
To ensure proper functioning of the above model, the optimal approach often involves deploying two systems – MES and ERP. Nevertheless, this solution often raises doubts. Will the proliferation of systems lead to chaos? Can employees effectively manage both systems? While such concerns are valid, a different perspective sheds light on the topic.
First attempts to integrate MES and ERP during their early development stages might in fact have proven inefficient. Information transmitted from one system sometimes arrived distorted at the other.
Presently, there are solutions that facilitate seamless integration of both systems (the ESB) to eliminate any distortion on the way. Concerns about data flow are relieved, as modern integration systems enable collaboration on a shared database without the need for complex mapping.
ERP systems play a vital role in supporting business decision-making at both high and middle levels. They rely on extensive data aggregations that do not necessarily require highly accurate and detailed information but often demand cost quantification.
Every ERP system available on the market offers a manufacturing module. This raises doubts whether additional implementation of an MES is necessary. To address this query, it’s crucial to understand that ERP was created and designed by specialists in the area of business and finances. Therefore, ERP-managed production may not be the most optimal solution as it perceives manufacturing only from a cost perspective. Such an approach might not support operational decisions taken at the bottom layer.
An MES is primarily used for manufacturing data management. Source: ImFactory
Similarly to ERP systems, MES possess functionalities that can be utilized for business decision-making. However, this solution is also suboptimal. It is important to note that the MES was developed by and for engineers focused on the technical approach, emphasizing the need for real-time data to make instantaneous process decisions.
Information processed within an MES can be transmitted in aggregated form to an ERP system for cost analysis. This collaborative approach is highly recommended. It facilitates using the available tools exactly in the manner they were designed for and utilizing their greatest assets.
Let’s explore the complementarity between ERP and MES by examining examples of how these systems contribute to various cost groups, forming the Total Manufacturing Cost (TMC).
Direct materials
ERP: Provides information on prices (e.g. the prices at which individual batches were purchased) and aids in calculating markups on unregistered resources not directly listed in the Bill of Materials (BOM).
MES: Enhances the above calculations with precise amounts and batch numbers. It assists with the inventory of unregistered materials found in “supermarkets” within production and determines average consumption from these “supermarkets.”
Direct labor
ERP: Offers information on hourly rates for employees involved in production and presents cost models based on their skills and grade.
MES: Provides details on specific amounts of registered time in the context of cost centers (e.g., equipment, line) considering an employee’s role in a given order, their skills, and grade.
This combination enables determining whether simple tasks are being performed by staff with higher competencies, making it potentially more costly.
Other direct costs
ERP: Gathers all financial information, such as the prices of manufacturing utilities, depreciation of specialized tools, costs of hiring contractors and subcontractors, technology development, asset acquisition, production preparation, and funding costs.
MES: Records the use of manufacturing utilities. Usually, such data is retrieved e.g. from SCADA, but the information aggregated around a specific order appears in the MES, similarly to the information on the number of cycles or tool runtime in relation to a cost center.
The MES also facilitates recording work by contractors and subcontractors. There are systems which allow sharing a mobile interface or specific information with outside workers providing services to the company. In such systems, it is possible to record trials and test rounds similarly to normal production, including all its aspects.
Department costs
ERP: Manages the depreciation of the whole support system for core processes, including equipment, tools, premises, and unquantifiable wear and tear. This includes materials, utilities, and salaries of supporting and supervising departments – in summary, all that supports main processes.
MES: Provides support for the creation of allocation keys, pivotal in this process. It shows the shares of specific cost centers, registers maintenance service operations to determine the shares of specific cost centers in their work, and facilitates recording on-site transport and warehousing, through methods like movement tracking based on RFID Tags.
Seamless integration of MES and ERP provides a comprehensive perspective on all company processes, facilitating more effective cost management. By connecting these systems through a data bus, the risk of distortions and chaos is eliminated, enabling the full exploitation of each system’s potential. Decisions are technically supported by MES and substantively and financially by ERP.
Read also:
Total Manufacturing Cost and Cost Allocation in a Company, Part 1: The First Step Towards Savings
See also
Want to learn more? Visit our Knowledge Base, where you'll find articles and webinars by experts to expand your knowledge.
Check if Digital Transformation is the Answer to Your Company's Needs
The Free Consultation Process:

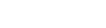
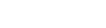
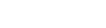
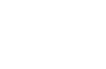
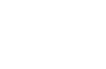
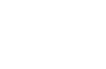
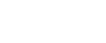
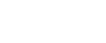
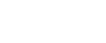
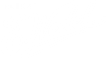
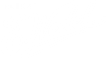
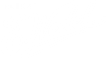
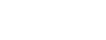
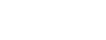
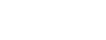






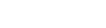
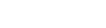
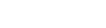
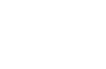
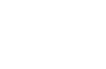
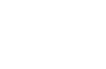
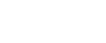
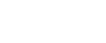
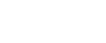
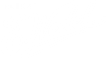
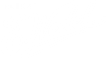
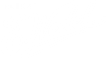
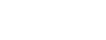
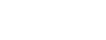
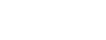






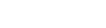
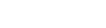
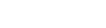
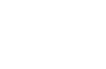
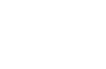
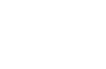
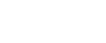
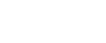
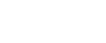
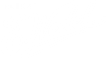
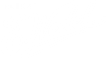
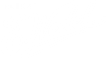
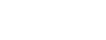
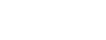
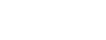






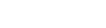
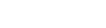
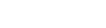
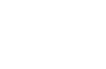
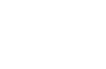
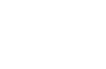
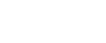
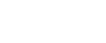
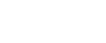
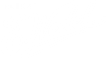
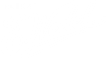
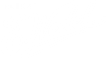
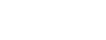
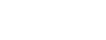
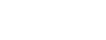


