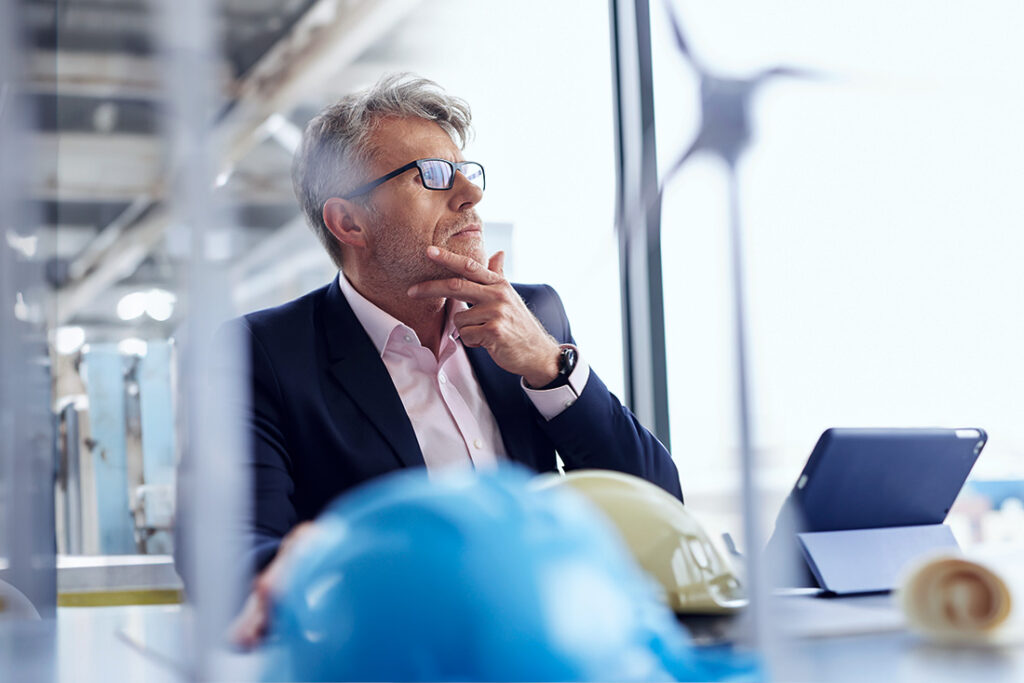
Manufacturing Utilities in the Age of Digital Revolution, Part 3: Smart Energy Management Systems in Practice
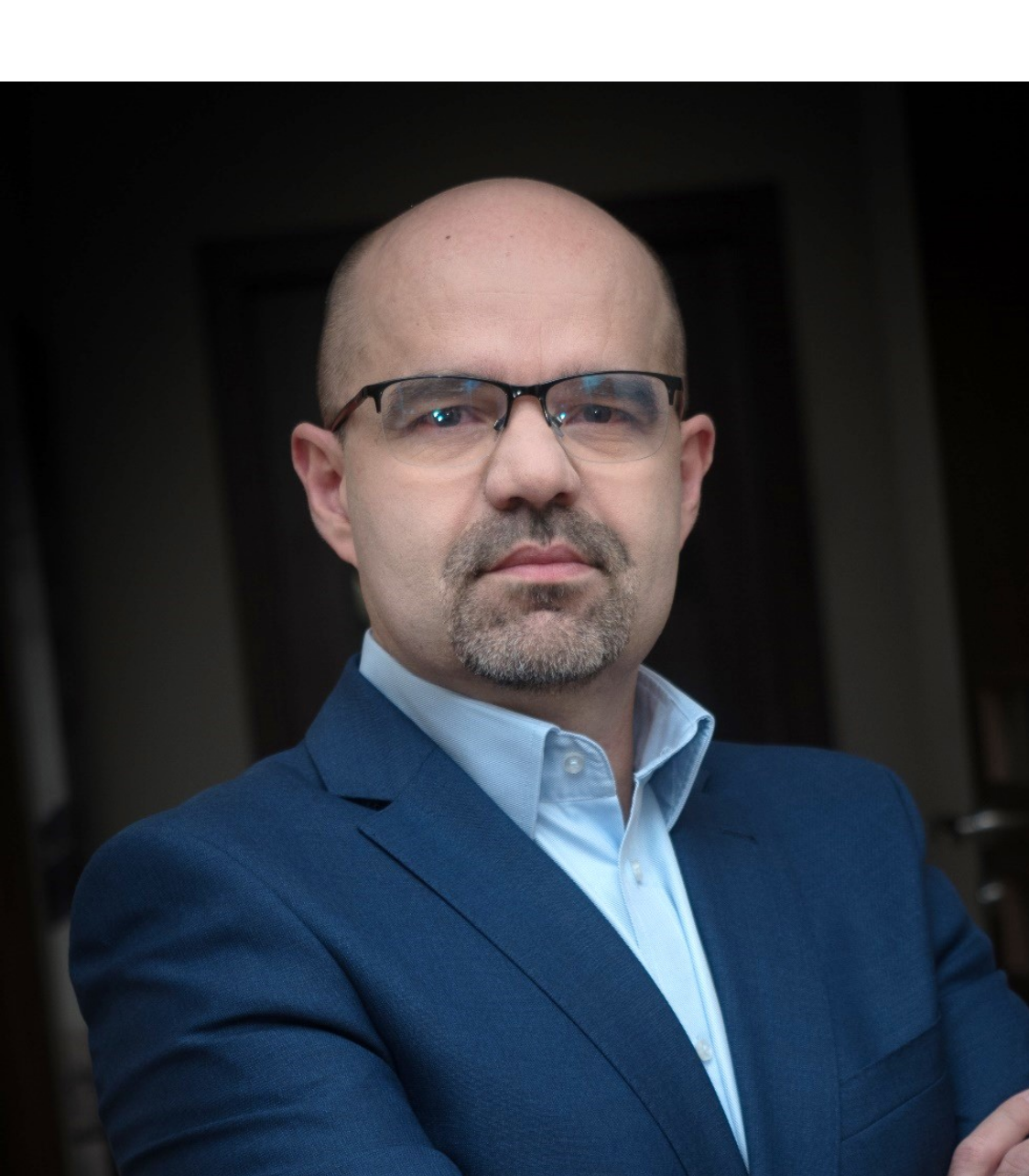
Tomasz Ziąbka
Chairman of the Board at ABZ Consulting Sp. z o.o.
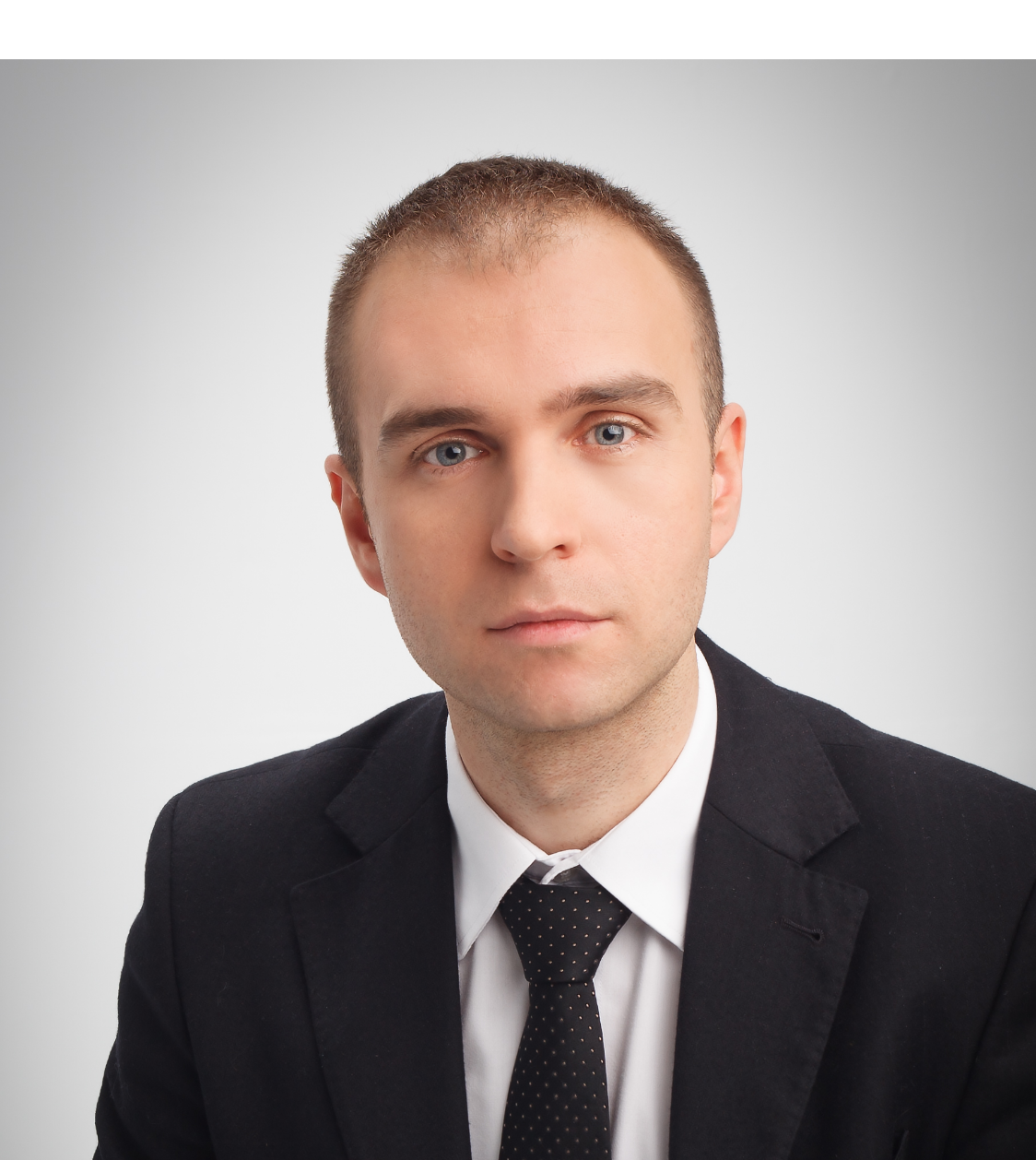
Grzegorz Fijałka
Similar to many other large projects, when planning to invest in energy monitoring systems, it is best to start by clearly defining your goals. What could these goals be? Surely, the most crucial one is to reduce energy bills.
However, defining goals is also an excellent opportunity to analyze the current situation and ask a series of critical questions:
- Why are we paying so much?
- Is it acceptable, or could we be paying less?
- Do we possess all the reliable data necessary for drawing conclusions?
- Are we informed about unusual system working states or potential exceedances?
- Could our data be used in case of dispute claims with the energy supplier?
Why are these questions important? The key lies in having a comprehensive understanding of the energy states and transitions occurring within the company. This knowledge enables us to optimize consumption, enhance the availability and quality of power utilities, ultimately leading to cost reduction.
In addition to the financial aspect, other objectives are gaining importance, such as environmental sustainability, compliance with market regulations, and tracking one’s carbon footprint.
These additional goals should be viewed as opportunities. Some contribute to cost reduction, while others can increase sales by providing access to new markets subject to specific regulations. Furthermore, they offer a chance to create products that attract new clients due to their transparent carbon footprint.
Before proceeding with the implementation of an energy monitoring system, the next crucial step is performing equipment inventory. This step provides knowledge of what needs to be installed or connected and where it is needed.
It is essential to focus on both external energy sources and internal ones such as compressors and boiler plants. Through the analysis of utility distribution in the context of different energy sources, we become aware of the actual flow of utilities. This awareness facilitates a prompt response to anomalies as they occur, rather than waiting until faced with an excessively high utility bill.
Step 2.1: Equipment inventory While for a majority of businesses, conducting a physical equipment inventory is routine, they often neglect software inventory, which is an essential part of this step. Several points are worth considering:
- How will equipment be connected – by cable or wirelessly?
- Is there an appropriate network that can be utilized?
- Do we have PLCs that could serve as data concentrators?
- What opportunities are created by existing systems in the company, such as SCADA or HISTORIAN?
Analyzing these aspects beforehand can help avoid unnecessary complications and additional expenses.
After analyzing motivations, goals, and possibilities at our disposal, it’s time to move on to concrete planning. This typically involves preparing a straightforward proposal that defines the points and parameters we aim to achieve, the equipment and systems to be installed, and the budget allocated for it.
While many firms follow this approach as a good starting point, it might sometimes be too limited. It is beneficial to delve deeper into the specifics of what utilities we want to measure and why. Subsequently, we can relate this information back to our goals and expected outcomes. It’s a good idea to define the parameters of the equipment we plan to install and the utilities we want to monitor.
A broader perspective involves creating a comprehensive concept that considers the strategic, long-term goals of the organization. This allows us to relate these goals to the existing architecture and systemic environment. The concept might include a so-called Roadmap specifying various implementation stages, which will allow us to complete the project gradually. This complex approach of concept preparation, audit, and offer, yields the most benefits in the long run.
What exactly is the comprehensive approach in the context of energy management systems? When we have such a system, signals need to be fed into it, and these signals need to be preserved. Currently, we have access to various modern technologies, such as IoT or Edge devices, embedding information that can be utilized.
Consider both internal (company operations, production events, equipment states) and external (weather, utility availability, tariffs) contexts. All this data should be archived for easy future access.
However, let’s not forget that data alone isn’t information. Processed data, tailored for different needs, creates information that can be delivered to various sources: from employees who are informed how their actions affect utility consumption, to managers who need the same data in a more analytical context. Another context is the business perspective, where everything is considered in terms of money—how much we gain or lose.
Data gathered in an energy management system can be further utilized: transferred to other systems and used to calculate various indicators such as KPI or TMC (Technical Manufacturing Cost). Information can reach specialized systems like CMS, providing insights into energy states or signalling the working states of specific machines.
All of this data gathered directly from energy data or indirectly from different contexts is useful and supports future analyses performed not only by humans alone but also with the help of artificial intelligence.
When implementing an energy management system, several scenarios are available. The first involves a basic starter system that gathers energy data from a specific area.
Often, these systems expand to acquire additional data from broader areas, evolving into systems that combine different contexts into collective information. Sometimes a comprehensive system is created, combining information sources from the whole organization.
Another option is to combine pro-energy systems with others, like Manufacturing Execution Systems (MES) used for the management of manufacturing operations. In comprehensive systems, an industrial data bus can connect not only MES and energy systems but every other system in a company, offering significant information development opportunities.
Considering the extensive possibilities of developing such systems at different stages, the worst possible option is to build a system closed to development. While it may serve its purpose initially, the inability to incorporate expert additions, such as AI algorithms, severely limits future perspectives.
Example 1: starter system
Typical steps in implementing a basic system include:
- Install
- Connect
- Utilize what you already have
The connection can be either wired or wireless, with wireless often being more advantageous for cost reduction and faster implementation.
In starter systems, two elements are defined: what is being measured and the reference parameters during measurements. Sharing this information online enables the analysis by individuals making relevant decisions.
Example 2: Extended system
Starter systems can be extended by expert additions incorporating embedded logic. These additions, based on expert knowledge, provide additional insights, references to classification tables, and notifications about anomalies or failures.
As more data is added, the system expands, offering greater capabilities. A notable example is Krakow Water SA., the city water distribution system, where data had been gathered on several levels for many years, until an idea emerged to develop an AI algorithm supporting the management of a second stage pumping station. This resulted in significant savings, increased technological security, and reduced pump wear.
Example 3: Integrated systems
While information about electricity or gas consumption is crucial, it’s not the only data required in manufacturing. There might be a need for additional data on the quantity of items, machine states, or technological parameters. This aligns closely with a Manufacturing Execution System (MES), whether in the cloud or locally, capable of delivering such data.
How to approach this task when there already is an energy management system implemented in a company? First of all, it is beneficial to leverage the existing infrastructure. As we already have been gathering data, we possess necessary connections, concentrators, data collectors, to which consecutive signals can be connected.
Secondly, if there already is a system that defines some data, maybe some of it can be utilized for the MES? Ideally, this should be implemented in a way that data streams are independent but create a comprehensive system for different recipients.
Just as in any IT system implementation, introducing an energy management system involves certain data sources, infrastructure, and most importantly, people. They are the ones who make the right decisions if they have access to appropriate tools.
These decisions are always oriented towards certain goals. Different departments play key roles, such as technical departments for data sources, IT specialists for infrastructure, and production workers and energy engineers for direct operation and needs.
While the goals are determined by the business, we cannot forget about Continuous Improvement, which also influences future iterations and goals.
Well-tailored smart energy management systems offer numerous benefits but require detailed goal analysis, resource utilization planning, and careful consideration for future development. Building an open and flexible system is key to avoiding limitations in future growth.
More about energy efficiency and energy management systems in the Knowledge Base:
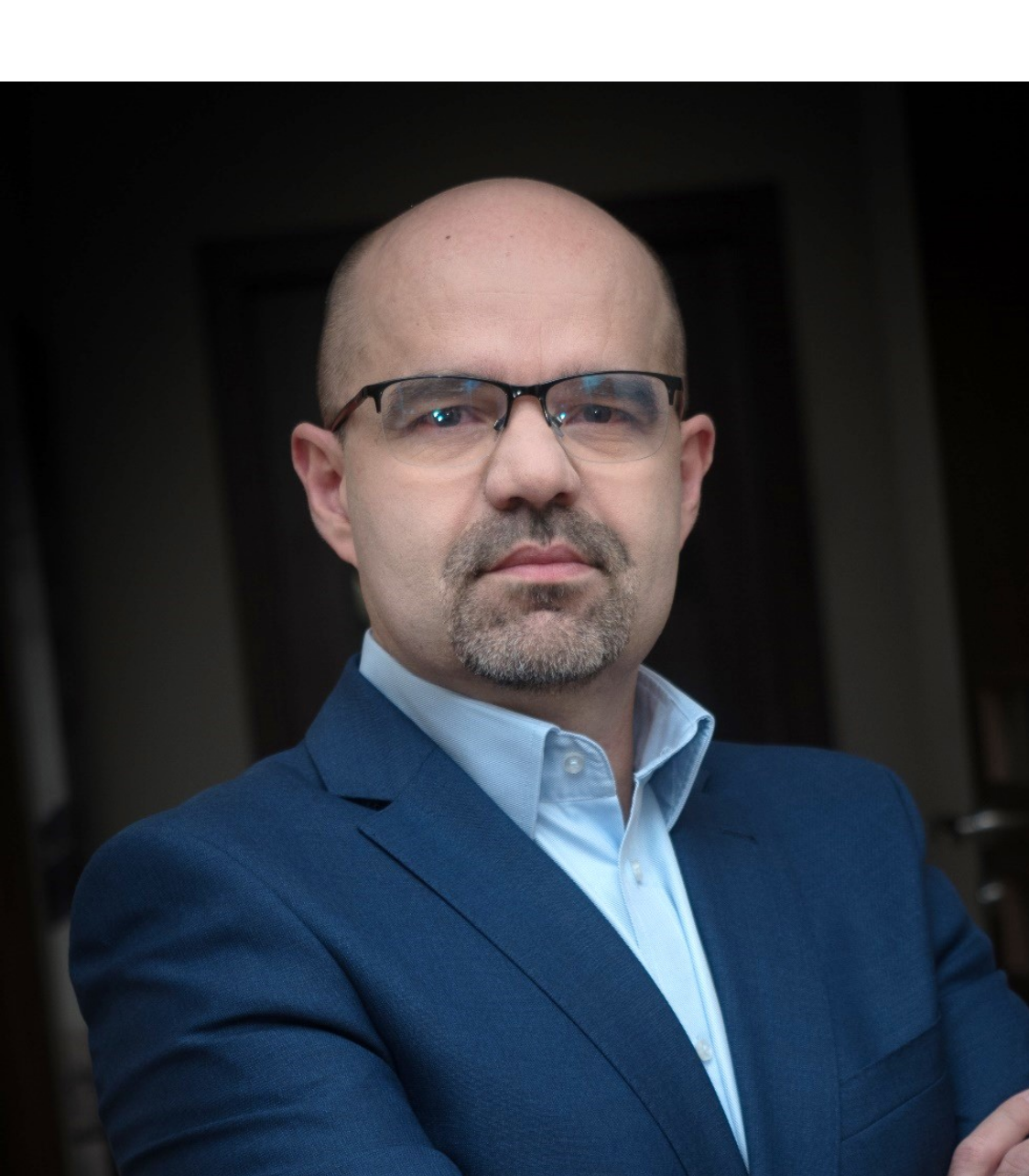
Chairman of the Board at ABZ Consulting Sp. z o.o.
Chairman of the Board at ABZ Consulting Sp. z o.o.
Tomasz Ziąbka has over 20 years of managerial experience within industries related to modern technologies and energy aspects, with a particular focus on energy efficiency. He is recognized as a KSU expert in the fields of innovative projects and energy efficiency. Tomasz graduated from the Faculty of Electronics and Electrical Engineering at the Lodz University of Technology, holding a Master of Science degree in Automation and Robotics. Additionally, he is a graduate of the MBA program, accredited by the University of Lodz and the University of Maryland. Tomasz has personally overseen the successful completion of several dozen auditing and advisory projects, specializing in the energy efficiency of large enterprises.
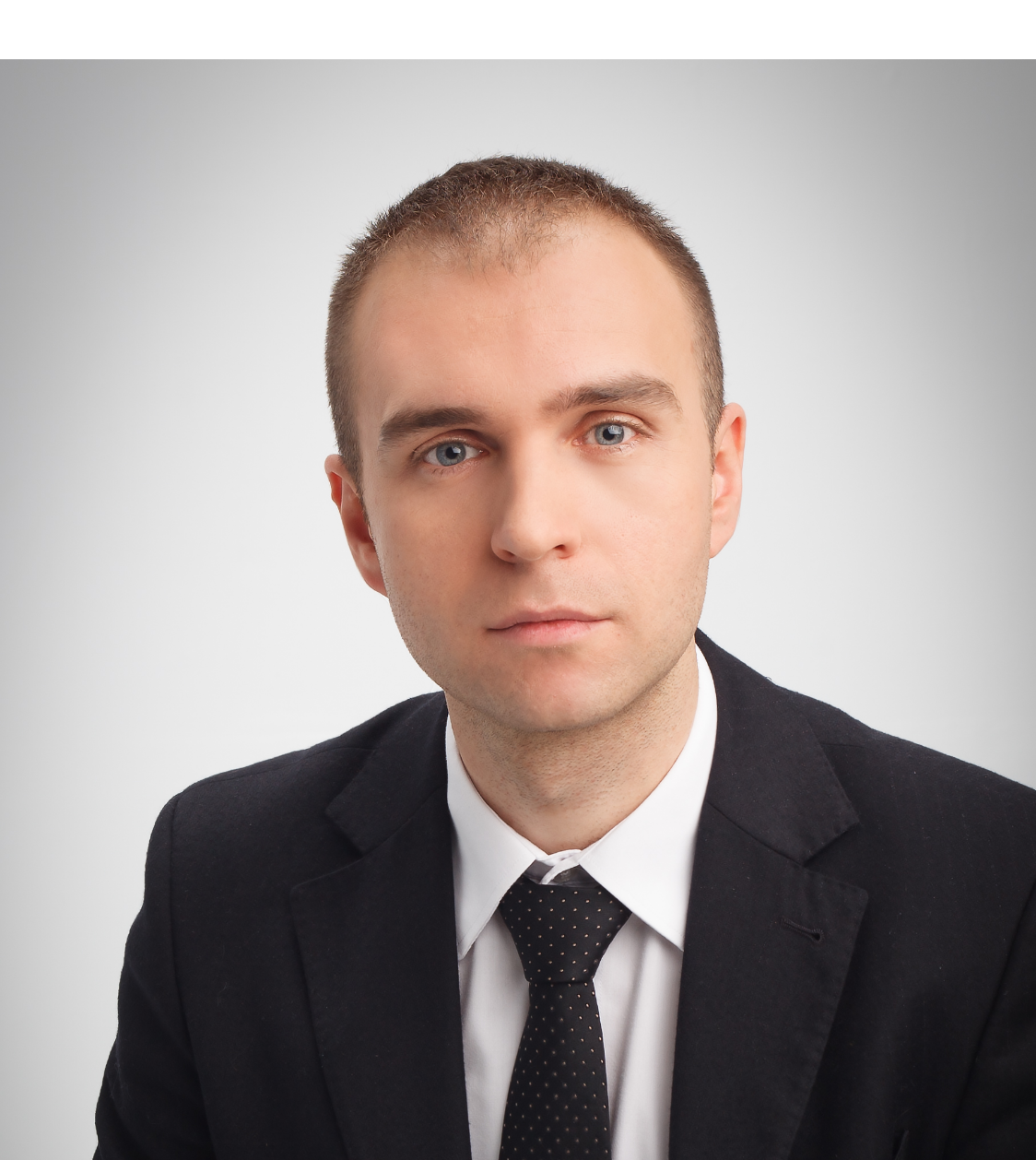
Grzegorz Fijałka completed his studies at the Faculty of Mechanical Engineering at Cracow University of Technology, specializing in Automation of Manufacturing processes). He also holds postgraduate degrees in production management from Tischner European University in Cracow, as well as risk management, forecasting, strategic planning and foresight from Collegium Civitas in Warsaw. Grzegorz is an expert in industrial software, 4.0 technology, and Digital Transformation Roadmap for Manufacturing, among others.
Throughout his career, he has held various positions, ranging from Technical Support and Sales Specialist, through coaching and Project Manager, all the way to the President of ASTOR Consulting, developed from the Account Management formula at ASTOR. Currently, as a Partner at ImFactory, he is responsible for the company’s overall business development. He is passionate about exploring new technologies, fostering creative ideas and embracing agile operations.
See also
Want to learn more? Visit our Knowledge Base, where you'll find articles and webinars by experts to expand your knowledge.
Check if Digital Transformation is the Answer to Your Company's Needs
The Free Consultation Process:

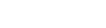
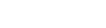
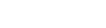
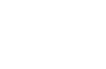
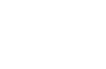
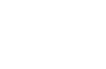
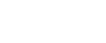
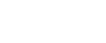
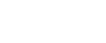
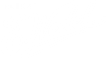
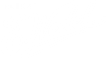
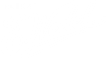
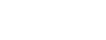
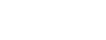
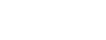






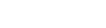
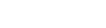
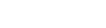
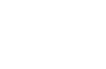
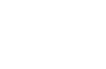
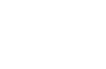
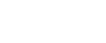
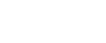
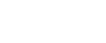
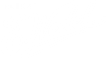
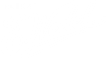
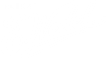
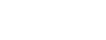
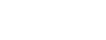
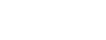






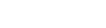
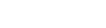
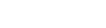
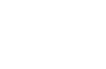
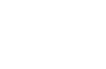
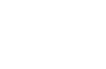
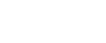
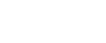
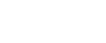
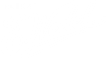
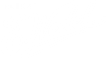
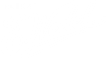
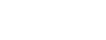
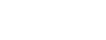
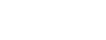






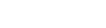
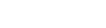
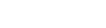
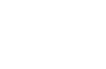
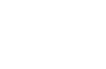
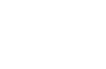
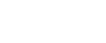
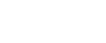
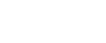
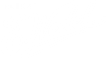
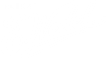
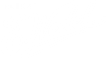
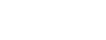
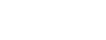
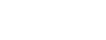


