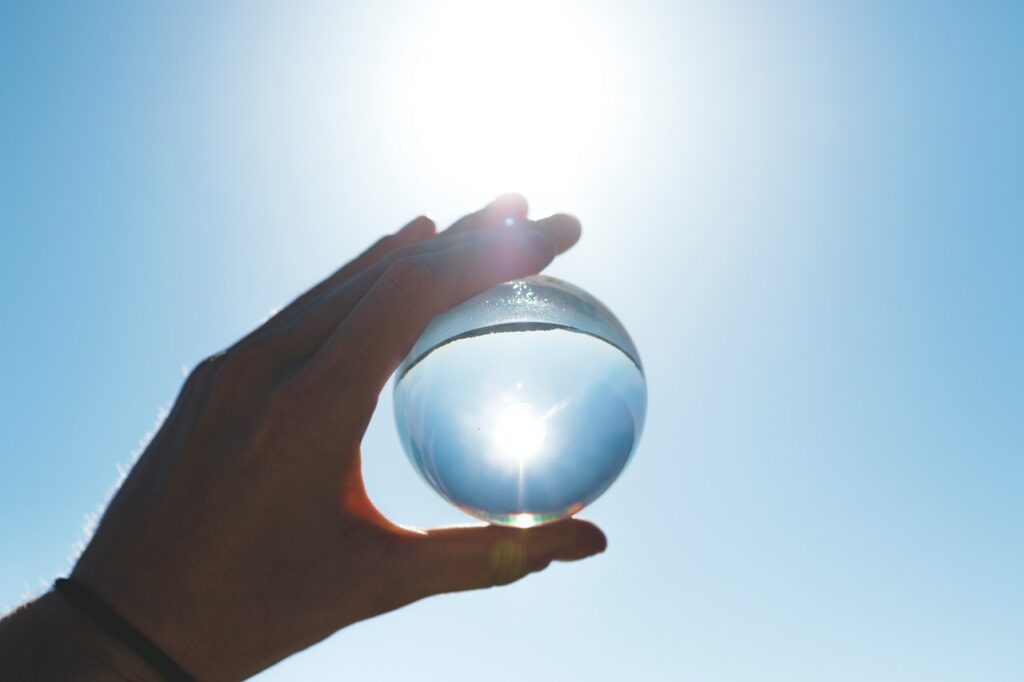
Digital Transformation: A Path to Save the Planet – the Success Story of DOVISTA Poland
Climate and environmental concerns are now entering the arena of investment evaluation on par with financial factors. Though they may not seemingly generate immediate savings, and in some cases, may even incur additional costs, they are undoubtedly worth exploring. Over time, they yield quantifiable benefits. What exactly are these benefits?
At the beginning of our path towards digital transformation at DOVISTA Poland, we faced two fundamental dilemmas. Firstly, how could we provide comprehensive product information to workstations? And secondly, what machining and assembly operations would be required to achieve the desired outcome? In many companies, this is referred to simply as “technology.”
In our business, a conventional approach to technology development has no place due to the diversity of products and the sheer scale of our projects. Today’s construction trends emphasize individuality, driven by increasing manufacturing capabilities and improved thermal insulation in joinery, leading to ever-growing client demands.
Moreover, these demands are becoming more diverse by the day. Manufacturing around 6000 unique windows every week, with each production batch consisting of just one piece, adds complexity to the process. It’s worth noting that we do not maintain a stock of pre-manufactured items, as each window is tailored to a specific client.
To fully grasp the bigger picture, one must understand the product. At first glance, a window or door may not seem overly complex. We interact with these everyday items without realizing the intricacies involved. In our factory’s “window” system, we specify up to 12,000 characteristics for each product. This begins with conscious customers who make decisions on hundreds of these features, such as dimensions, colors, and opening functions.
However, to bring the final product to life, we must supplement the basic information gathered during the sales process with additional parameters for suppliers and production. In many European countries, complying with legislative and environmental requirements is also vital to the process. The diagram (Fig. 1) illustrates how data accumulates at each stage of the production order, growing exponentially as it progresses.
Imagine visiting a car dealership and experiencing the joy of selecting the ideal car. A specific engine determines the compatible gearbox, and certain upholstery options are limited to specific body styles. Similarly, with windows, the sales configuration comprises the aforementioned data that clients perceive or architects specify.
Next, a technical configuration is created to resolve any potential clashes between window elements. The final step involves generating bills of materials and CNC programs to fulfill the client’s unique requests. This entire process is fully automated, requiring no human intervention.
The configuration tool utilizes rules for configuration and validation to generate and verify data. It is then exported to the Manufacturing Execution System, where our competent team handles DOVISTA’s supply chain.
Among the competencies we provide to organizations are SAP (ERP) and AVEVA (MES) systems management. We support facilities in Poland, Lithuania, and Denmark, overseeing the processes of planning, logistics (including purchases and distribution of finished goods to logistics centers), and production, encompassing both MES and ERP. The data prepared in this manner serves as a repository for the manufacturing process.
Two key tasks for an MES in our company are to provide up-to-date information about the production plan and offer detailed data about the technology for each element of a window during its production or machining. This involves creating files with programs for CNC machines. However, data gathered in the MES database at this stage remains of little use to operators. In collaboration with ImFactory (a part of ASTOR group), DOVISTA developed a set of web applications to give the data meaning and defined roles, supporting our goals.
The primary purpose of this application is to oversee the timely execution of the production plan. In contract manufacturing, meeting deadlines is the key to success, especially in the woodwork renovation market. The app provides two views: planner (logistics module) and production (operation module). Each view visualizes data tailored to the needs of its users. The planner view offers a graphic presentation of the manufacturing process’s progress in relation to the plan, also known as routing.
Each completed operation is monitored by a network of scanners working on the company’s Wi-Fi network. After scanning, the actual completion date is compared to the planned time and presented as a colored cell: dark green for on-time completion, light green for completion before the scheduled time, yellow for completed later than expected, and red for delays.
This form, enriched with additional data for each order, provides planners and logisticians with continuous and up-to-date information on the production’s progress. As a result, it significantly reduces the need for phone calls, emails, and meetings to track order execution. This tool becomes particularly valuable when issues arise with an order – for instance, when a product is damaged, such as broken glass. Such information triggers immediate emergency procedures, notifying the distribution center, and in critical situations, the end customer as well.
This approach allows adjustments to the investment process at the construction site, resulting in the facility covered by the system achieving a +95% on-time rate to the distribution center.
The second view in DSP is the operator’s perspective. It provides the same data but from the viewpoint of a specific workstation’s employee (foreman). This view aggregates tasks for the selected manufacturing area, along with basic data about the scheduled task completion. It also enables operators to perform several basic actions from their workstation, such as confirming an order, adding comments (notes relevant to other process participants), recording defects, or generating CNC programs for the machine.
An additional benefit for operators is knowing whether the previous operation has been completed, saving time otherwise spent searching for orders that are not in the buffer.
The most significant achievement of this project, and a true hallmark for us, is the implementation of E-documents for production. When considering its environmental impact, this aspect stands out as the most vital. The numbers behind this project illustrate its scale.
In the entire facility, approximately 200,000 A4 sheets of paper are printed each week, which is the equivalent of 400 reams. This entails significant annual expenses, well over PLN 100,000, considering only the cost of paper and printer toner. Additionally, disposing of used paper adds to these costs.
Once the project is implemented across all facilities, we estimate a remarkable 85% reduction in these expenses. The solution provides up-to-date detailed data on selected production orders to operators. The software is designed to function on tablets, ensuring full mobility and reducing costs. It only requires browser support. One of the functionalities of E-documents is a summary of the details to be manufactured for an order, including detailed information about each item.
Importantly, each operation listed in the documentation serves as a separate link to its corresponding document and instructions. This ensures that every employee has access to the most current documentation at any time without needing paper copies. It also eliminates the need to verify document versions. Whenever an update is made to the documentation, it becomes instantly available to all employees.
In addition to meeting technical and content requirements, E-documentation solutions are analyzed from a User Experience (UX) standpoint to improve document ergonomics and user-friendliness. During employee training, we continuously gather feedback and make adjustments to the document design. Our team follows Agile Project Management, welcoming frequent changes as part of the process.
When mass-producing configurable products, providing dedicated programs for CNC machines becomes a challenge. As part of our implementation, we designed a solution that generates a file (program) for a specific machine at the operator’s request, using the data collected in the MES database. In DOVISTA’s facilities, we work with several dozen computerized numeric controlled workstations from various manufacturers and multiple programming languages.
To address this, we developed translators (xslt) that associate tasks with the appropriate machines. With this mechanism, the program becomes available in the network within seconds, and the operator can proceed with their work. This process has effectively eliminated the need to involve technology services, empowering operators to independently write their own programs.
Another functionality we implemented is the ability to place locks on specific products at selected stages of production to facilitate detailed quality or product supervision. For orders requiring such oversight, such as trade show items or VIP commissions, a lock is activated when attempting to confirm the progress of production. This prompt is then signaled at the operator’s Wi-Fi scanner.
For the order to resume, only authorized personnel, such as a quality inspector or a process engineer, can remove the lock, thereby certifying that the product meets the required specifications. This feature proves particularly useful during the implementation of new products or technologies, allowing for full process validation, even if the new item represents only a fraction of the total volume and is not yet standardized.
Even in the most streamlined manufacturing processes, occasional slip-ups occur. As is common in production, unforeseen incidents may arise and the established plan cannot be fully implemented. This can be especially challenging due to the fact that the standard flow is well-monitored, but alternative flows might not receive the same attention.
To address this, we aimed to monitor and support the defective process. When a defect is identified during production, a rework is initiated. The recorded defect is closely monitored from that point on. In DSP, the defective order is marked with a hatching pattern within a cell (see figure below), alerting the planner that the order is at risk. Additionally, the history of the order can be traced from the DSP level.
Similar to tracking shipment histories, all relevant sequences for a given rework are recorded. The card for each rework also provides statistical information (error coding), which facilitates better analysis of the defect sources and their elimination in the future.
In the age of digital transformation, every manufacturing process leaves a digital footprint through endless data, ultimately resulting in specific services or products after proper analysis and application of specialized technologies. This digital footprint also reflects our commitment to responsible environmental practices. Indeed, digital transformation significantly helps to reduce not only paper consumption but also the carbon footprint throughout the entire supply chain. Each action, no matter how small, contributes to our efforts to protect the planet.
Tomasz Kubach
See also
Want to learn more? Visit our Knowledge Base, where you'll find articles and webinars by experts to expand your knowledge.
Check if Digital Transformation is the Answer to Your Company's Needs

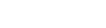
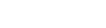
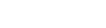
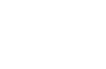
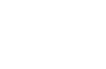
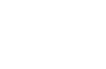
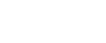
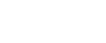
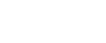
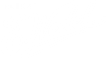
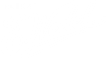
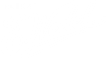
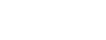
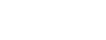
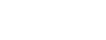






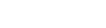
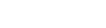
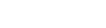
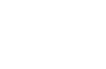
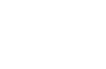
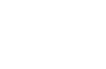
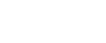
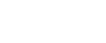
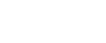
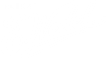
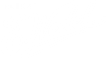
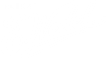
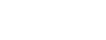
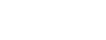
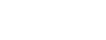






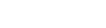
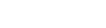
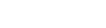
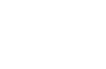
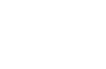
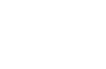
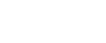
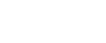
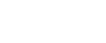
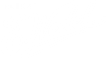
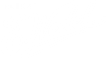
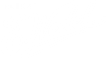
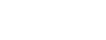
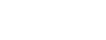
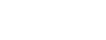






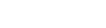
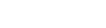
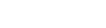
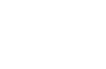
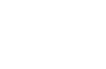
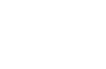
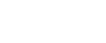
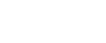
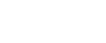
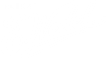
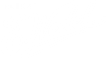
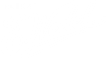
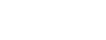
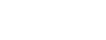
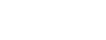


