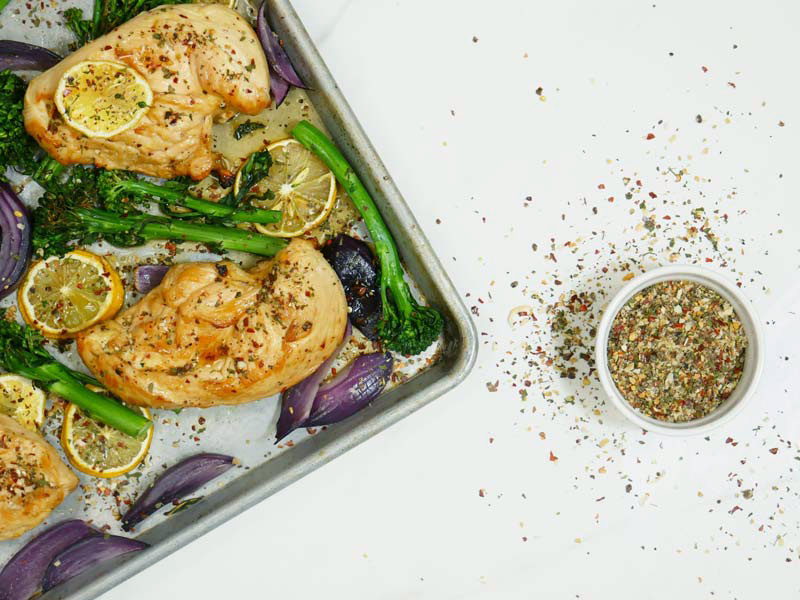
How Illes Seasonings & Flavors Benefited from PlanetTogether Software
CLIENT: Illes Seasonings & Flavors
INDUSTRY: Food
CUSTOMER PROFILE:
Illes Seasonings & Flavors has made various food ingredients for more than 85 years. They’re a privately held company that has a proud legacy of innovating and developing unique flavors with an entrepreneurial spirit. Based out of Dallas, Texas, Illes has expanded into a national food powerhouse that continues to provide quality products and excellent customer service within their industry.
Today, they work with the largest retailers, food processors, national restaurant chains, and food manufacturers across the nation. This sustained growth, however, presented a manufacturing challenge for Illes. As a result, they looked to PlanetTogether to optimize their production schedule.
PlanetTogether was founded in 2004 as the culmination of decades of academic research at Cornell University. Combined with over 20 years of industry experience, we focus on making manufacturers more successful by applying software that solves production planning and scheduling problems. With our powerful, easy to use, integrated software tools and education, manufacturers can attract and retain customers by delivering faster — and do it more profitably by minimizing resource and inventory costs. PlanetTogether is on a mission to make the planet more productive, one manufacturer at a time.
Illes went through a 6-month Proof of Concept before committing to PlanetTogether. Following their purchase, they experienced immediate results. “Before, it took hours to schedule [our production] manually because scheduling was based on reports, now it only takes seconds,” said Les Howell, Executive Director of IT.
Following implementation, communication improved between planners and departments. Other enhancements include a better response time for instances such as expedited production order change and capacity availability requests. After seeing early results, Illes can now have a greater focus on long-term planning and scheduling.
We needed an APS System that has the ability to:
- Handle Jobs with multiple Process Stages
- Dry blending -> Dry packing
- Liquid tank blending -> Bottling Line filling
- Automatically create Plan Jobs based on
- Sales Order demand
- Forecast demand
- Customer Floor Stock agreements (safety stock) demand
- Automatic schedule jobs to be completed before demand need dates
- Including Manufacturing lead times
- Identify material constraints (RM shortages intermediate jobs)
- Automatically sequence jobs on a resource machine based on:
- Kosher/Non Kosher products
- Allergens constraints
- Pathogen testing products
- Resource capacity constraints
- Easily move jobs from one resource to another like resource
- Based on capacity constraints
- Manage jobs between multiple plants
- Manage resource capacity
Business growth
- 20% increase in sales over past 24 months
Increased complexity
- Products requiring multiple resources
- Product mix allergens, religious dietary laws, FSMA
Ross limitations
- Manual job creation & job maintenance process
- Limited view of capacity
- Increased clerical workload in Planning Department
- Not enough time for proactive planning
- Data, Data, Data!!! Exposed areas where our data is weak
- Daily data cleansing
- Standardized master planning data set up on new products
- Optimization – Building rules set-up tables, etc.
- Gathering product mix data
- Adding foreign country allergen data
- Reconstructing the sequencing matrix
- Enhancements to further improve efficiency & accuracy
- Tank resources
- Beta testing latest software version
- Ross limitations – Process Flow & Process Specs
- Cross-department collaboration
“PlanetTogether’s software is by far the best and most encompassing planning software package offered today,” said Ed Czysz, Illes’ Production Scheduling Manager.
By implementing planning software, Illes can react swiftly to an unforeseen impact that may potentially affect the system.
Drawing information from all departments within the company, the scheduling tool helps expose areas where processes are weak. Namely, the Gantt chart tool with label features made quick work of identifying late/early jobs, material shortages, and job statuses. With the help of planning and scheduling software, Illes continues to be at the forefront of technology as an industry leader in food production.
Provided a total solution that satisfied our business needs:
- Handle Jobs with multiple Process Stages
- Automatically create Plan Jobs
- Automatic schedule jobs to be completed before demand need dates
- Automatically sequence jobs on a resource machine
- Easily move jobs from one resource to another like resource
- Manage
See also
Want to learn more? Visit our Knowledge Base, where you'll find articles and webinars by experts to expand your knowledge.
Check if Digital Transformation is the Answer to Your Company's Needs
The Free Consultation Process:

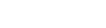
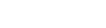
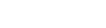
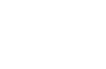
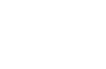
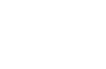
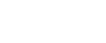
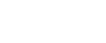
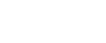
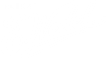
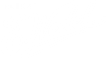
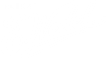
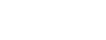
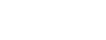
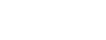






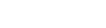
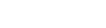
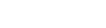
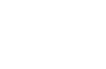
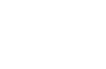
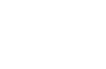
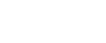
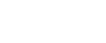
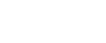
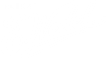
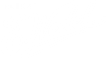
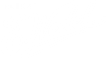
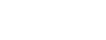
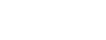
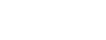






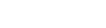
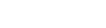
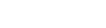
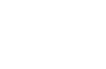
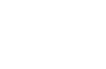
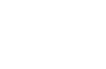
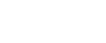
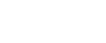
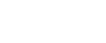
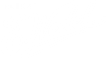
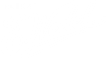
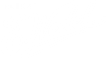
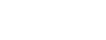
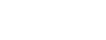
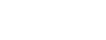






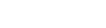
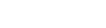
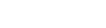
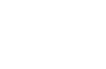
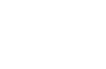
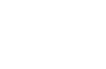
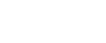
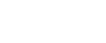
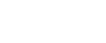
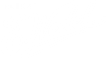
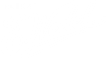
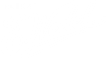
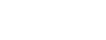
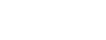
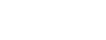


