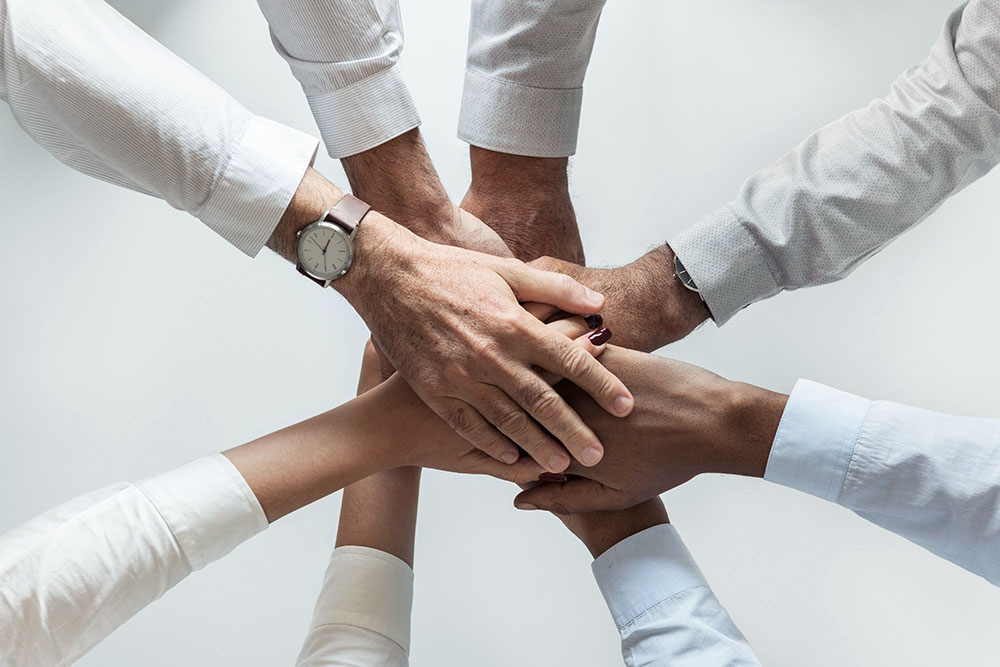
The Team Supporting DOVISTA Poland on Its Digital Transformation Journey
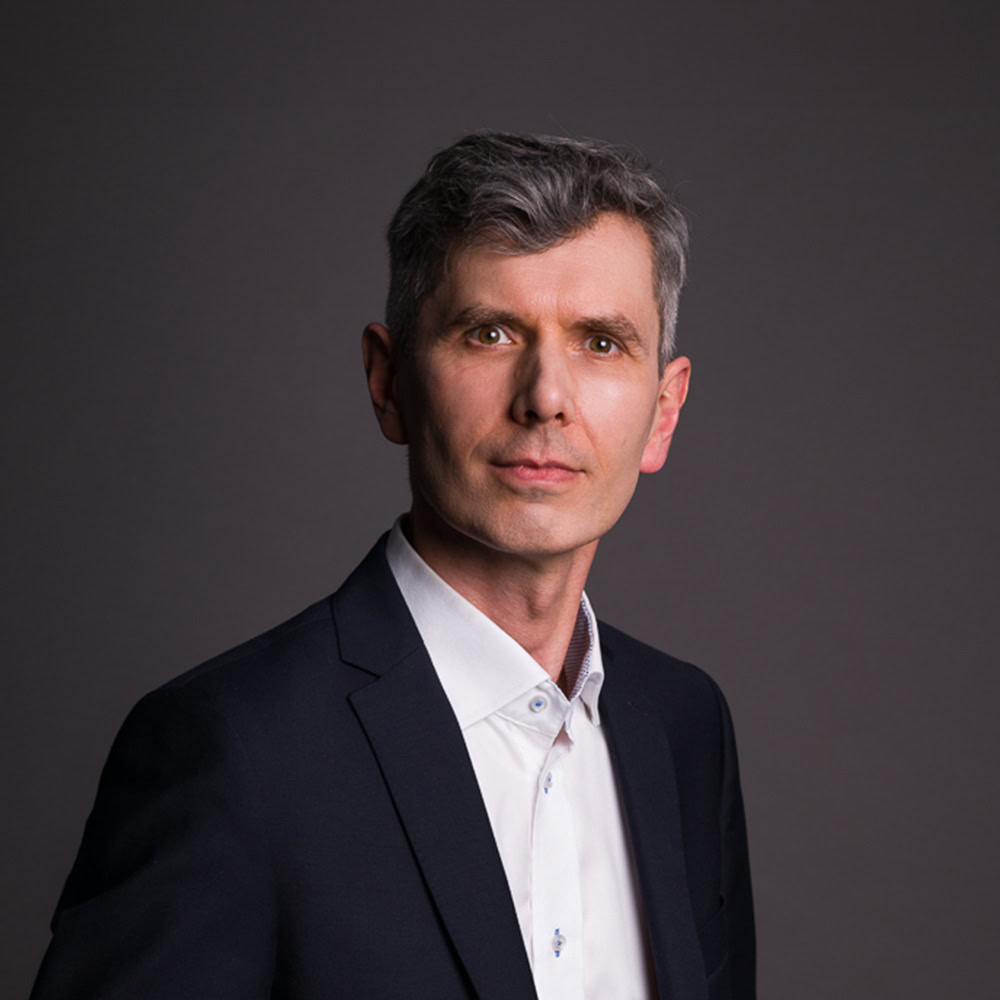
Jacek Daukszewicz
The digitization project of production processes in the DOVISTA doors and windows factory had multiple dimensions and specific objectives – not only from the perspective of the enterprise but also for the team that supported the transformation from the very beginning. An interdisciplinary team was assembled specifically for this project, tasked with researching and defining the requirements for the chosen solution.
The first and most important stage in building the IT system was appointing a project leader, who was responsible for coordinating the team’s work, assigning tasks, contacting the client’s project manager, and conducting a joint business analysis of the client’s key needs.
The requirement for continuous software development led the team to adopt methods and practices not previously used in managing production processes or projects in manufacturing companies. The Agile project methodology allows work to be completed in short cycles known as sprints, lasting several weeks. This approach ensures effective development of applications in line with the client’s requirements at every necessary layer.
A complete system tailored to the requirements of Industry 4.0 consists of three main layers:
- Perception Layer where data acquisition devices operate,
- Transport Layer forming a bridge between the perception pillar and the user (e.g., LAN network),
- Application Layer that allows direct interaction with the user.
The final pillar, which involved designing appropriate applications, was entrusted by DOVISTA to the ImFactory team, whose task was to design the software architecture and support the system’s ongoing development. The key requirements for the application were independence from technology and multi-platform functionality.
The decision was made to use web-based solutions that can be deployed on any type of device. The applications are hosted on local servers, allowing them to function even without an internet connection, which is a crucial feature for industrial applications.
In DOVISTA, the main source of information is the SAP software. The need to manage the integration of multiple applications and monitor production within a reflected MES model set a high bar for the integration system. While many applications offer one-way data transmission without feedback, such a solution is insufficient for complex systems.
The solution was to implement Enterprise Integrator, a stable software that allows the integration of multiple systems – from the ones supporting production to ERP solutions. It includes a Store & Forward mechanism, which stores data internally and forwards it to a server, providing more functionality than one-way data transmission.
Figure 1: Data flow diagram
Data from SAP is properly aggregated and stored in the MES database. The most important principle for this environment is the relational model used. The database comprises a set of tables where information on specific types, referred to as entities, is stored. The diversity of tables, the ability to expand the database structure, and the creation of new objects and procedures provide unlimited opportunities for development.
Using Data Manipulation Language (DML) to select, insert, and modify elements within the database is complex and not very user-friendly. The solution is to use computer, mobile, and web applications that receive raw data and present it according to the client’s expectations.
Each of the prepared applications is based on the structure shown in Figure 2.
The structure consists of two main components: the Back-End, which includes the database and business logic, and the Front-End, which comprises the user interface.
Figure 2: Application structure
A key element is the Web Service, which facilitates data flow over the network between the database and the web application. The Web Service acts as an abstraction layer that uses a set of defined data exchange standards.
The application was developed using the latest Microsoft .NET Framework libraries and based on a layered onion architecture. This structure helps to separate individual layers, making it easier to manage code and quickly locate and fix errors. Most importantly, it ensures high system reliability, being closed to modifications but open to extensions.
The primary goal of this architecture is to distinguish four main layers, interconnected by references:
- Core/Domain: This is the central point of the project, responsible for storing objects. It utilizes an Object-Relational Mapping (ORM) structure to map IT objects to database objects while maintaining proper relationships. The project includes the interfaces necessary for implementing repositories.
- Infrastructure: This area consists of two sub-layers: services and repositories. The repository layer acts as an abstraction platform, linking the previously discussed layer with the main business logic. Its role is to query databases about their availability, retrieve data, and map it to the business logic. This approach is known as the Repository Pattern. The service layer implements interfaces that handle interlayer communication.
- User Interface (UI): This layer manages interaction with the user. It typically consists of a web application and a web API project, which houses controllers responsible for exposing data from lower layers to the client.
Figure 3: Layered application architecture
The visual aspect of the application layer was developed by creating appropriate containers to separate the logic. To achieve this, the latest JavaScript libraries, such as the component-based React, were utilized. These elements enable the user interface to be divided into independent, reusable parts, which is significant because the applications differ thematically but can still incorporate previously developed modules.
The visual layer adheres to Responsive Web Design (RWD) principles. Developers emphasize creating websites that are simple and comfortable to use with both a mouse and a finger on a smartphone or tablet. Additionally, clickable elements on the websites are designed to be no smaller than 40px.
The layout of elements can adjust based on screen size and orientation, as illustrated in Figure 4. Components scale and rearrange to maximize the available space on tablet, computer, or smartphone screens.
Figure 4: A responsive application (displaying elements based on screen size and orientation)
A notable exception to the above standards is the E-Documents application, designed for operators working on production lines. Data shown on tablets gives detailed technological information and dedicated descriptions for operations. Since the MES database contains data for production tracking, there is no need to store additional information such as the dimensions of individual elements with technical drawings.
SAP serves as the primary source of information, so the data mentioned above is also included in this system. Data delivery to the E-Documents application is managed in a specific yet universal manner, allowing the application to be tailored to different departments. As a result, exceptions in specific locations do not affect the overall system’s performance.
Within a production order, SAP generates XML files (IDoc) containing all necessary information about a selected window, including its components, dimensions, and references to PDF documentation.
For each location, dedicated translators were created to extract only the necessary information for that area. To generate personalized result documents, the most popular XML transformation language, XSLT (Extensible Stylesheet Language Transformations), is used.
The application selects the appropriate translator based on the location where it is running. For example, the area responsible for manufacturing slats does not see elements related to espagnolettes. Additionally, operators only view the elements relevant to their specific tasks, avoiding the need to sift through all materials included in SAP documents.
Drawing numbers in the XML file assists in retrieving the appropriate PDF files from the server. The PDF.js library was used to display these documents, providing support for tablet applications, full responsiveness, and all the necessary tools for working with such files. Each application also includes built-in language support, which significantly eases the daily work of operators.
Creating a unique language understandable within a specific environment requires interdisciplinary knowledge and the ability to listen, collaborate, and communicate effectively. When translated into digital code, these skills enable us to develop increasingly architecturally advanced systems, leading to optimized and well-planned production processes.
The solutions implemented at DOVISTA not only enhance production efficiency but also contribute to environmental sustainability. Read more about this in the following article: Digital Transformation: A Path to Save the Planet – the Success Story of DOVISTA Poland.
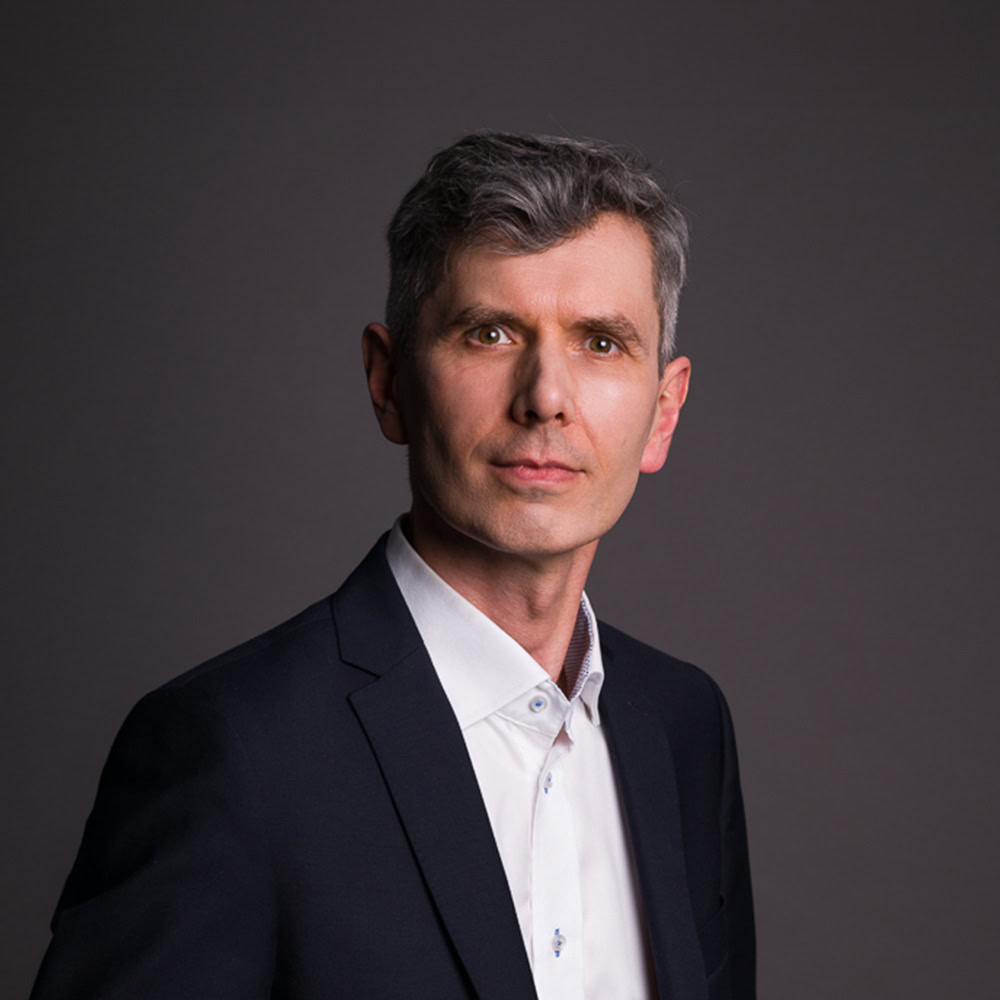
Jacek Daukszewicz is a graduate of Automatic Control and Robotics from the Faculty of Mechanical Engineering at Gdansk University of Technology. With over 20 years of experience, he specializes in IT/OT systems for manufacturing. During his time at ASTOR, he was responsible for selecting solutions and overseeing the technical aspects of implementing Manufacturing Execution Systems (MES). His responsibilities also included conducting economic analyses of investments in automation and manufacturing management solutions. Jacek actively contributed to the development of concepts for manufacturing management systems and supervised projects for Polish and international corporations. He participated in creating the MES Competence Center for the ASTOR Group. Currently, as part of the ImFactory team, he manages teams that coordinate digital transformation projects and the broader scope of Industry 4.0.
See also
Want to learn more? Visit our Knowledge Base, where you'll find articles and webinars by experts to expand your knowledge.
Check if Digital Transformation is the Answer to Your Company's Needs
The Free Consultation Process:

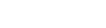
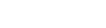
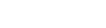
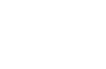
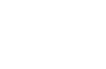
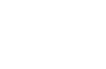
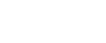
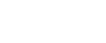
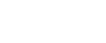
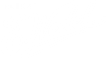
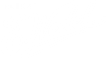
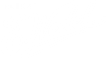
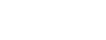
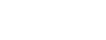
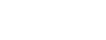






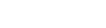
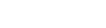
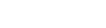
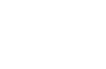
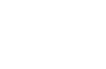
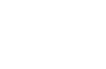
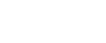
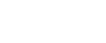
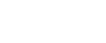
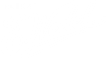
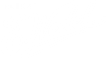
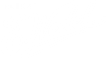
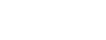
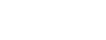
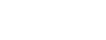






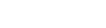
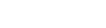
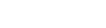
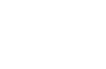
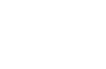
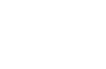
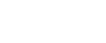
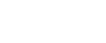
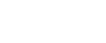
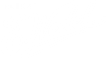
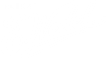
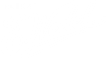
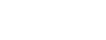
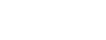
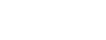






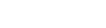
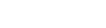
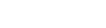
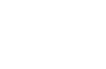
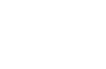
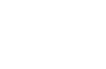
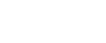
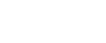
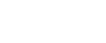
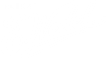
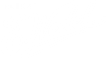
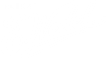
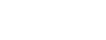
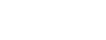
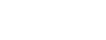


