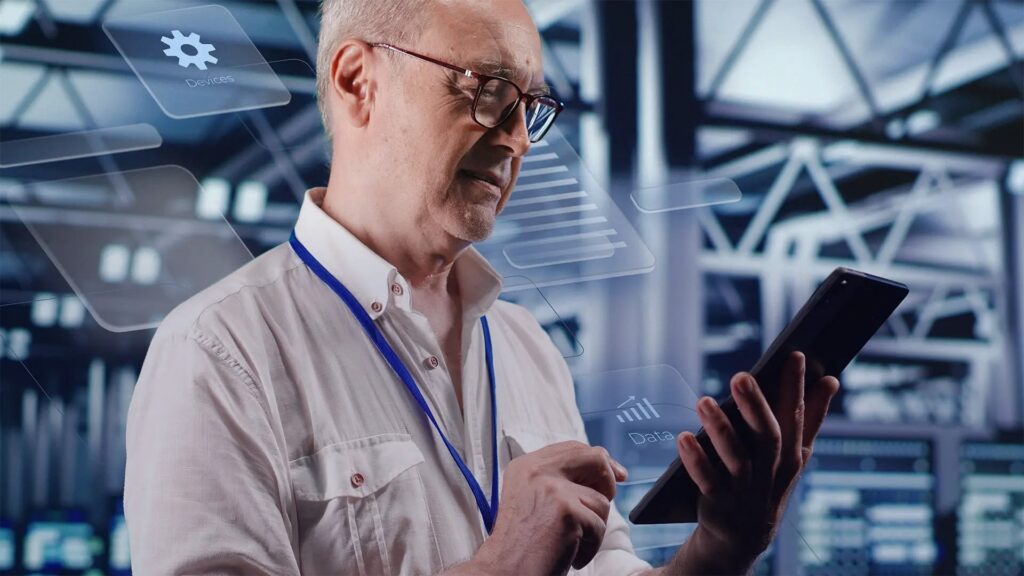
DIP – The Platform That Drives Digital Transformation
DIP, short for Device Integration Platform, is a multi-functional platform integrating tools, processes, and resources. It provides reliable data and facilitates data acquisition, processing, historization, and analysis. It forms the base for implementing modern systems that streamline work in manufacturing companies. DIP helps to combine all elements into a comprehensive, smoothly functioning whole.
DIP is industrial software designed to control processes in manufacturing plants. It provides a basis for the comprehensive management of processes, data, and operations, while also laying the foundation for implementing advanced solutions such as MES. It enables the effective creation and development of industrial applications at many levels of management, from monitoring the operation of machines, production lines, and entire factories, to alerting and reporting on any deviations.
DIP is the application layer between the two most important levels of a manufacturing company’s IT structure – the production level and the operational management level. The production level is where machines, controls, sensors, and other equipment and systems directly related to production operate. This is where real-time process control takes place. The operational management level is supported by various IT tools, such as MES systems, for analyzing and planning the production process in all its dimensions, with a particular focus on productivity, efficiency, and quality.
Thanks to its modularity, DIP offers more possibilities than just “simple” SCADA. It could be considered a link between two worlds – the world of physical devices with OT control and the world of software and IT applications. At the production level, it helps handle the logical layer of signals. It reads current values from data sources, and then archives, standardizes, processes, analyzes, and helps visualize them accordingly. Data prepared in this way (both current and historical) is passed higher up to the operational management level, where it is given the right context, and is then analyzed by the appropriate tools and used to make business decisions.
DIP is a versatile tool that enables communication with multiple data sources, such as programmable controllers from different manufacturers, using a wide range of dedicated industrial communication protocols as well as open standards (such as OPC or MQTT). This allows for efficient exchange of information. DIP connects systems, devices, and technologies into a single coherent architecture, bridging the barriers between them. It can manage the transfer of data to other modules operating within the platform, making it possible to centralize and control the information flow throughout the system. The platform is the source of process logic and a central tool for control, monitoring, and alerting.
The platform collects, processes, and analyzes data in real time, which enables real-time control of the process and immediate fact-based decision-making. With developed reporting and data archiving features, it supports users in analyzing the collected information and facilitates identification of areas for optimization.
DIP also provides the ability to create advanced visualizations of processes across the enterprise. It helps to give proper context to processes, alarms, events, and historical data.
The platform provides a basis for designing applications, supplying standards based on objects and templates. This allows easy management and modification of individual components. What’s more, applications can be handled by different teams, making it easier to collaborate and manage the project at different stages of its implementation.
DIP is a solution for companies in various industrial sectors – from manufacturing, energy, and natural resources to infrastructure. The platform can be used by small and medium-sized companies as well as global corporations. It offers a variety of features that allow versatile application in different projects and support different users. It can help, among others, the following groups:
- Engineers who are responsible for designing, implementing, and managing industrial automation systems. DIP makes it easy for them to integrate multiple devices and systems.
- Operators overseeing daily production operations. It enables them to understand and control processes through SCADA/HMI interfaces.
- Managers responsible for optimizing and effectively managing production. It provides them with access to data analysis and reports, facilitating informed decision-making.
- IT professionals, for whom combining multiple functions within a single platform makes it easier to monitor and maintain infrastructure.
- DIP is also a great solution for system integrators and implementation partners – DIP’s flexible tools allow them to tailor solutions to their customers’ needs.
With the help of DIP, it is possible to lay the groundwork for a so-called digital twin, a virtual equivalent of a physical resource that integrates real-time data from the real world with the virtual model. By doing so, it ensures a full understanding of the processes and opportunities provided by the resource. The twin can be created for signals, but also alarms, logic, history, or energy.
How is a digital twin created? The platform integrates data from various sources (IIoT, HMI, control systems, sensors, actuators, etc.) to create a unified model combining process, design, and historical data, which is the basis for the digital twin. It then shares the data with the higher levels of the digital twin model.
The digital twin operates on real data, faithfully reflecting the status of equipment, performance, and failure risk. This provides more reliable data for analysis and allows flexible adaptation to changes in production resources. With digital twins, “what if” simulations can be run to evaluate different scenarios before implementing changes. This solution can also help companies track environmental indicators, such as energy consumption and CO₂ emissions, and support resource optimization, which fits in with sustainability goals.
Reliable data: DIP automates the data collection process. This is vital, as the more data is collected automatically, the more reliable it is and the more time we save. Recording the exact moment when an event occurs translates into the reliability of the information obtained, and this, downstream, leads to better management, both at the operational and business levels.
Relieving the operators’ workload: DIP provides operators with a better overview of the current situation. With clear visualizations and advanced alarm management, it helps to keep operators focused on the most relevant process information, reducing their distraction and fatigue, and making their work more efficient.
Operational efficiency: Thanks to better data management and automated operations, it is possible to improve production processes and eliminate downtime associated with maintaining applications or implementing changes to production systems, resulting in increased efficiency.
Saving time and reducing costs: Comprehensive, pre-configured applications contribute to significant time saving, while optimizing resources, monitoring performance, and minimizing downtime translates into cost reduction.
Better security: The platform offers advanced features for data protection and security compliance (such as ISA/IEC 62443).
Better insights: Integrating IT and OT systems eliminates information silos and provides easier access to information. Practical visualizations, easy-to-access charts, intuitive dashboards, and rapid data processing make it easier to solve problems, help identify inefficiencies, and eliminate time-consuming steps to find the information you need.
DIP offers a wide variety of capabilities, creating a consistent, unified environment for monitoring and controlling production processes. As a stepping stone to data integration, it not only facilitates automatic data collection but also combines information from different sources and makes it possible to present it in an appropriate and understandable context. This translates into decision-making based on reliable, up-to-date information, which creates a basis for Digital Transformation of enterprises. What is more, the platform forms an ideal foundation for implementing advanced Industry 4.0 technologies, such as IIoT, real-time data analytics, automation, digital twins, artificial intelligence, and predictive analytics.
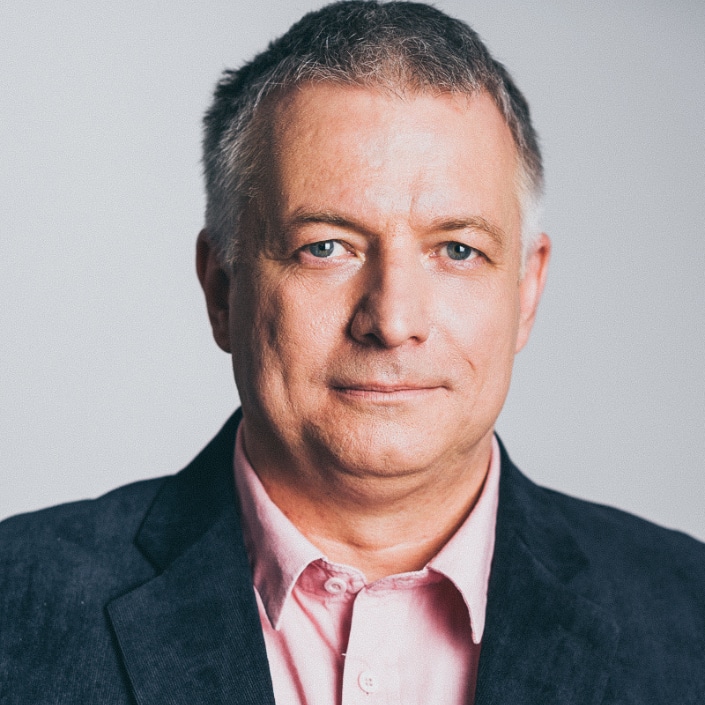
He has more than 20 years of experience in SCADA/MES systems for manufacturing. He gained it in an integrator company, where he was a programmer, then a project manager responsible for industrial software scopes (SCADA/MES/CMMS), mainly AVEVA (former Wonderware). He was also responsible for large industrial automation investments including industrial software. He deepened his experience with OT/IT projects at software distributor AVEVA in Poland, where he was responsible for the selection and implementation support of SCADA/MES systems in many companies and industries.
For more than 10 years at Improvement Factory, he has held the role of Senior Project Manager of digital transformation projects in multinational corporations, mainly clients in the food industry.
See also
Want to learn more? Visit our Knowledge Base, where you'll find articles and webinars by experts to expand your knowledge.
Check if Digital Transformation is the Answer to Your Company's Needs

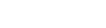
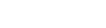
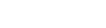
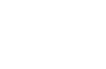
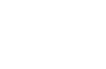
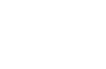
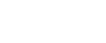
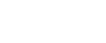
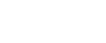
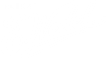
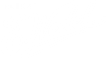
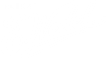
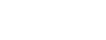
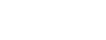
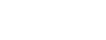






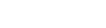
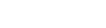
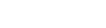
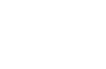
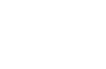
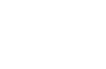
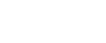
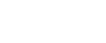
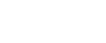
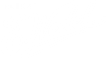
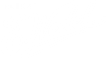
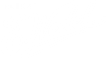
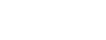
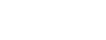
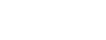






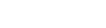
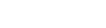
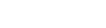
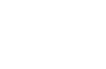
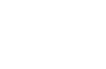
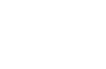
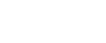
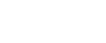
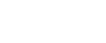
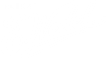
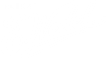
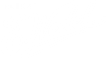
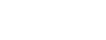
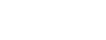
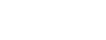






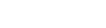
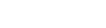
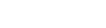
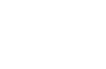
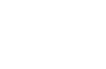
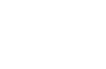
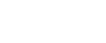
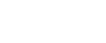
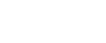
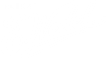
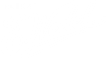
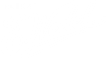
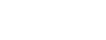
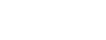
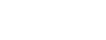


