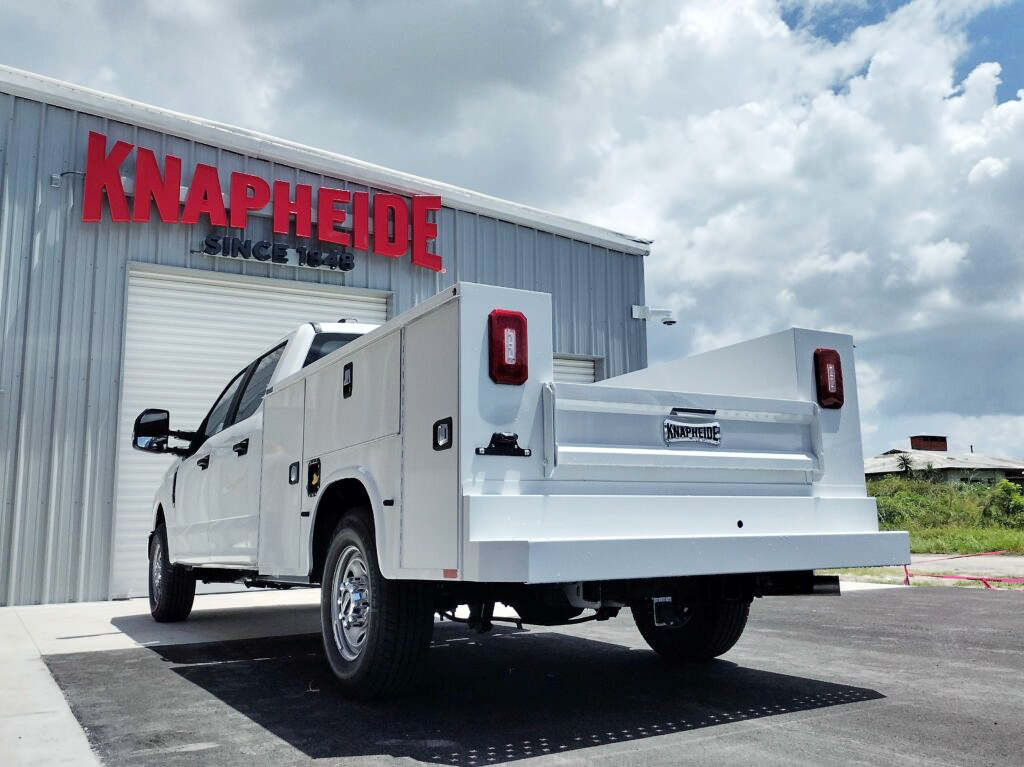
Equipment Upgrades to PlanetTogether APS – Posts ROI in Six Months
CLIENT: Knapheide
INDUSTRY: Truck Equipment
CUSTOMER PROFILE:Knapheide Truck Equipment Company of Flint, Michigan (Knapheide Flint). The venerable manufacturer transforms truck chassis from Dodge Ford and GM into the hard-working trucks that move the nation.
PlanetTogether was founded in 2004 as the culmination of decades of academic research at Cornell University. Combined with over 20 years of industry experience, we focus on making manufacturers more successful by applying software that solves production planning and scheduling problems. With our powerful, easy to use, integrated software tools and education, manufacturers can attract and retain customers by delivering faster —and do it more profitably by minimizing resource and inventory costs. PlanetTogether is on a mission to make the planet more productive, one manufacturer at a time.
Five thousand trucks roll off the line at Knapheide Flint each year. Service truck bodies, dump bodies, snow plows, platforms, premium dry freight vans, lift gates, van interiors, and crane bodies. Up to twenty jobs run concurrently at any time in the production scheduling department.
When Dick Marx joined Knapheide Flint as Materials Manager, he was surprised to find that the company still relied on an enormous magnetic board to schedule jobs. In his mind, manufacturers wouldn’t expect their engineers to design with a pencil or ruler; why make planners/schedulers use a white board or spreadsheets?
The manual scheduling process was labor intensive, required two full-time workers. Worse yet, that board loomed over production as the singular bottleneck on the company’s manufacturing line.
“Our scheduling system was limiting our production capabilities,” says Marx, “It had become the determinant of growth potential, not capacity.”
Every day staff scanned hundreds of board jobs, valiantly trying to make adjustments and predictions. “Customers want to know when their truck will be ready, and we weren’t able to give them a very accurate answer,” recalls Marx. Marx came from a computer background and knew Knapheide’s process could be automated. He set out to find a solution.
An Internet search led Marx to PlanetTogether, a Microsoft .NET based, multi-plant, real-time Advanced Planning & Scheduling (APS) software developer for manufacturers. “The fact that their product was .NET-based was important. It meant we could easily integrate with our manufacturing software,” Marx notes.
“I saw a demonstration, spoke with consultants, and was convinced PlanetTogether was the solution for us.”
Knapheide and PlanetTogether began to exchange data. Using Flint’s ERP software, PlanetTogether consultants designed the import utilities to accept job data and available inventory, and the export utility to send PlanetTogether’s calculations back to Knapheide’s ERP system in the form of job completion dates.
The familiar drag-and-drop interface of PlanetTogether made the scheduling tool simple to use. Staff has immediate visual feedback as all late jobs appear in red. PlanetTogether even optimizes the schedule to meet promised delivery dates.
“We feed it the facts we know, and it automatically proposes an optimized schedule that allows us to meet those dates. It’s something we tried, but never could do manually,”
notes Marx. PlanetTogether’s scheduling screen displays on a large monitor in the foreman’s office. Now the sales representatives can access the schedule when communicating with customers.
No longer stuck in manual mode, Knapheide Flint now provides its customers with realistic estimates of project completion dates because it can quickly identify bottlenecks and work out a plan, right down to paint
or equipment installs.
“We can see if our paint department will be swamped next Tuesday, and bring in more staff to meet the need,” explains Marx.
Skill levels and capabilities of each staff member are considered during scheduling to ensure the right individual is assigned to the right task. “OUR QUALITY HAS IMPROVED AS A RESULT,” says Marx, “the software assigns the best person to the job.”
Also “what-if” analyses were impossible with the old manual system. Now, Marx is able to see the impact of adding a second shift, or hiring an additional person. “WE’RE ABLE TO MAKE STRATEGIC DECISIONS THAT IMPROVE OUR OPERATIONS,” he says. “We can proactively prepare for anticipated increases or slowdowns in demand.”
“Scheduling now takes about 15 minutes,” Marx beams. “PlanetTogether paid for itself in six months!”
See also
Want to learn more? Visit our Knowledge Base, where you'll find articles and webinars by experts to expand your knowledge.
Check if Digital Transformation is the Answer to Your Company's Needs

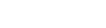
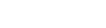
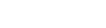
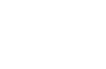
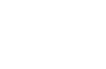
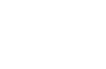
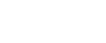
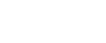
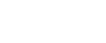
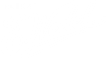
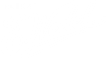
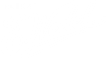
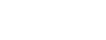
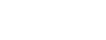
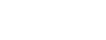






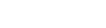
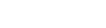
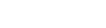
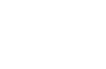
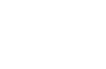
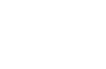
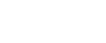
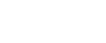
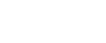
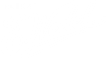
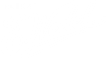
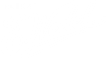
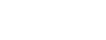
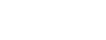
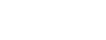






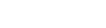
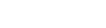
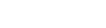
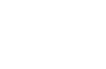
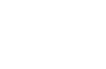
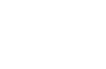
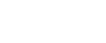
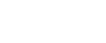
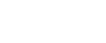
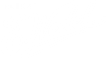
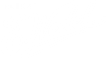
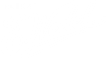
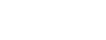
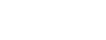
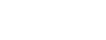






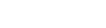
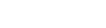
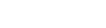
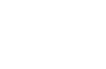
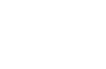
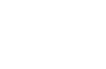
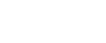
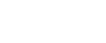
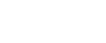
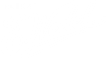
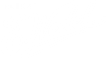
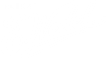
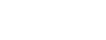
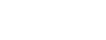
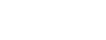


