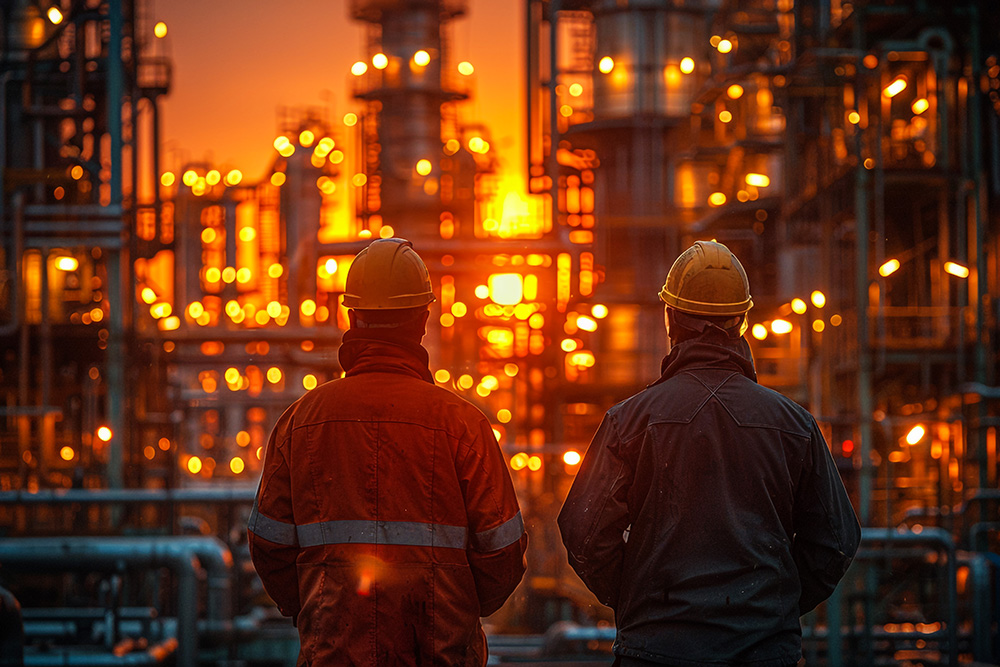
A business relationship resistant to change. About the cooperation between Gdansk Refinery and ImFactory
ImFactory – AVEVA MES Competence Center – was established on the basis of ASTOR Gdańsk. LOTOS Capital Group underwent reorganization, transforming from a production and trading company called LOTOS Asfalt Sp.z o.o. into the Gdansk Refinery, which is a fully production entity and integrates all refining activities in Gdansk. Meanwhile, then Wonderware which is now AVEVA, which has earned its name as a global provider of software for the industry, implemented in 2005 the Application Server solution, today known as AVEVA System Platform.
Practically from the very beginning of its implementation, i.e. for almost 20 years now, ImFactory and Gdansk Refinery (although initially under different names), under a service agreement, have been working together to continuously develop, improve and adapt this solution to the changing needs over the years.
In 2005, DCS (Distributed Control System) class systems, with their own controllers and visualization systems, were already in operation at the facility.
Systems of this type are used wherever the installation is distributed over a large area. Their main advantages are mostly used in places with special requirements, such as power plants, steel mills or refineries.
However, not every type of work requires such advanced solutions. Tasks that are not critical for the plant, but are only of a supporting nature, e.g. show the current working states and statuses of storage tanks, can be successfully carried out with the help of other tools.
Alternatives to DCSs included PLC-based solutions and individual operator stations collecting data from individual plants and visualizing it on InTouch applications. However, due to the need to exchange data between multiple sites and distributed pumping plant systems, the decision was made to use Application Server, today’s AVEVA System Platform.
The solution was very innovative for that time. Moreover, it was one of the first System Platform licenses in Poland. At a time when digital technologies were not yet as widespread as they are today, not only the implementation of such a tool was a challenge. It was also organizational changes and the proper preparation of employees to use it. A challenge undoubtedly successfully completed, because as Piotr Latos, Senior PLC/SCADA Control Systems Engineer at the Gdansk Refinery, says:
„When I started working at LOTOS Group, the staff involved in maintenance and changes within the Platform was well prepared, that is, when the training took place, the cooperation must have been so fruitful that after I was hired here and took over my responsibilities, I was able to carry out maintenance and service work within the Platform itself without any problems.”
One of the important factors in the decision to choose the so-called “ordinary SCADs” instead of a DCS system, in addition to the type of work, which was not critical, was cost. This raises the question: why InTouch alone was not chosen, and instead the decision was made to invest in a nevertheless more complex Platform?
As Piotr Latos explains, “We wanted to avoid a lot of distributed single-station systems, and since the installations serving tanks and control rooms were quite numerous, we decided on a centralized solution. The System Platform gave some unique features and was a reasonable solution in terms of cost and at the same time the capabilities offered. Other systems did not have such functionalities, or if they did, they were much more expensive. We are talking about redundancy mechanisms and historization in external databases. This was quite important at the time.”
Creating a single shared environment that collects data from multiple distributed sites initially requires more effort to implement and is more costly. However, later on, this effort put in initially pays off.
“I am glad that at that moment we managed to convince decision-makers, to take this approach, that it is worthwhile to initially incur a slightly higher outlay of money and work, in order to reap the profits later on”- emphasizes Piotr Latos.
“The cost-benefit ratio of the Platform was definitely a differentiator when it came to this type of system at that time. Despite the higher outlay at the beginning, the investment turned out to be very profitable, which was noticeable in the period of its development and adding more installations, as well as later, when managing the system, administering or servicing it,” adds Jacek Daukszewicz, Vice President of ImFactory.
Today’s Gdansk Refinery, which combines the major part of the refining business in Gdansk in a single entity, came about as a result of numerous transformations – starting with the original Gdansk Refining Plants through LOTOS Group or LOTOS Asfalt. During these changes, the System Platform has continued to play its role, although of course every acquisition or merger requires a system adjustment, if only in formal terms.
“During the changes we became aware of something within the system that may not be strictly an engineering problem, but because of the working relationship we had and the need to manage the system properly in an organizational context, it turned out to be important. Namely, an issue that also needed to be taken care of turned out to be the transfer of licenses and support programs between companies. Taking into account the fact of long-term cooperation, the transfer of licenses or updates to the owner of these licenses, as well as later uploading them to the server went favorably, quickly and pleasantly, and most importantly, without affecting production and without the need to stop the already working applications,” – says Piotr Latos.
Migrations between companies also demonstrated an important technical aspect, namely cyber security. The various companies were isolated from each other, and it was necessary to reconcile both the security of each company and the need to exchange information between them. Although everything was happening within one group, but still in terms of different subnets and domains.
In order for all the programs, and each component of the System Platform or systems in general, to work together, they first had to be confronted with the IT security policies and roles that are in place at the Gdansk Refinery.
Over the course of less than 20 years, the Platform itself has changed, with updates, new versions and functionalities appearing. For the Gdansk Refinery, as a plant with special requirements, such changes are always a challenge. While they bring new opportunities and having an up-to-date version of the tool in use is crucial, one must be careful and act in such a way as not to disrupt production processes.
As Piotr Latos says: “We don’t want to be beta testers. We try to install versions that have been on the market for some time and have had a chance to be tested in different environments. This allows us to rule out initial errors in the application and its cooperation with operating systems. We try to proceed in such a way as to make sure that the application we install is already in a stable version. On the other hand, there is also a need to implement security patches that improve already installed applications. This is very important for us because we are a high-risk facility.”
From the very beginning, the decision-makers were also aware that the chosen solution must have the potential to grow. That’s why they decided on a high System Platform license from the very beginning, with the idea that it would collect, transfer or convert a larger group of points in the future. As it turned out, this approach was the right one, because so far there has been no need to develop the license, although the Platform itself already has about 15,000 points.
However, migrations can be a challenge. The Systems Platform historically dates back a good few decades. Over that time, the programming languages in which the scripts were developed have changed quite a bit. What’s more, the applications running in Refinery are quite extensive, both in terms of integration with other systems and added plug-ins. Therefore, each migration of the Platform carries more work than would be the case if jumping from version to version.
Nevertheless, Piotr Latos emphasizes: “We are satisfied with this system. Every year we have reviews, we try to cooperate and improve this system so that we have as few problems with it as possible. Through this we also develop it in a certain way and make sure it works properly. Overall, I think that over time the amount of problems we have encountered in operating the system is absolutely acceptable.”
In addition to the original installation, which was designed to handle storage tanks, another installation with slightly different needs has since emerged as part of the working system. LOTOS Asphalt, which at the time was operating as a separate company dealing only with asphalt production, had a problem with a large amount of data that was difficult to control. With help came MES system.
Taking over responsibility for the system when LOTOS Asphalt was transformed proved to be a challenge. The Gdansk Refinery brought together two companies that had previously developed their systems in parallel. MES is a more scripted system, based on solutions written strictly for the customer. Therefore, it is difficult to take full knowledge of it, and without having detailed documentation it is difficult to support its operation and expand it.
Maintaining and developing the MES system in-house was consuming too much time. “Wanting to fix something in the MES system, we have to devote potentially more time to it. We don’t have huge experience in this matter, plus the fact that the application was developing outside of our control ultimately led to a lack of understanding of how the application itself works. All these factors significantly limited our ability to do script work within the MES system and interfere with its components,” says Piotr Latos. Therefore, the decision was made to enter into an additional agreement with ImFactory, for support in this area.
As the Platform developed, the Gdansk Refinery’s cooperation with ImFactory also developed. At first it was support for the implementation itself, then training services, later service and maintenance assistance, as well as joint action during application upgrades and annual system reviews.
“The cooperation is going very well, because the experts from ImFactory are available and willing to cooperate. A big advantage is that we have been working together on this system from the beginning. Every year there are reviews, we get reports, based on which we can later plan what moves we should make regarding the Platform itself. It’s also important for us that the ImFactory team is able to meet the requirements of our contracts, such as the recently developed 24/7 support.”
However, it is worth emphasizing that the smooth operation of the System Platform over all these years is primarily due to the full commitment of the employees of the Gdansk Refinery.
“The team in charge of maintaining the Platform has ongoing training and knowledge that has evolved over many years. Although, as ImFactory, we are an external company maintaining this application, by far the first line of support and knowledge of the entire system is with the Gdansk Refinery team. This makes all the changes and migrations go more smoothly.” – Jacek Daukszewicz emphasizes.
The Gdansk Refinery is now a processing refinery, and the key challenge facing the entire plant is to become a leader in terms of reliability, efficiency and safety. Supporting them are the undoubted systems already in place, their maintenance and development.
“We are constantly looking for solutions on how to improve our systems, how to make them more reliable, what to do to make them as user-friendly as possible, to involve us as little as possible, while meeting the required production needs.” – says Piotr Latos.
He adds, “We’re thinking about creating a Road Map showing what we could do with our system, or how to improve it so that we’re even more satisfied with it, in what years to do migrations, and when to abandon them, what can already be changed, how to prepare so that the next time we migrate it will be easier.”
Recently, the area that is served through the Platform has gained some importance, due to the fact that oil transportation is more often carried out by sea rather than using pipes routed over land. Hence, there are expectations for the Platform itself or the system serving the tank park, which has also gained in importance. Managers in the area note that it is good for it to be reliable and as accessible as possible.
There are undoubtedly new challenges ahead for Rafineria Gdanska, and certainly more changes as well, as these are integral part of any business that wants to grow. The approach we have taken so far, combining innovation with pragmatism and long-term thinking with flexibility in the face of everyday difficulties, allows us to go through the transformation without big shocks. It is a path of evolution, not revolution, which is effective through continuous improvement. Step by step.
The article is based on an interview with Piotr Latos, Senior PLC/SCADA Control Systems Engineer at the Gdansk Refinery.
See also
Want to learn more? Visit our Knowledge Base, where you'll find articles and webinars by experts to expand your knowledge.
Check if Digital Transformation is the Answer to Your Company's Needs

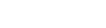
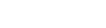
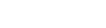
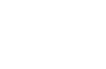
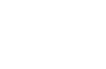
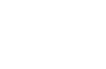
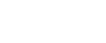
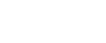
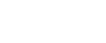
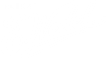
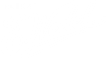
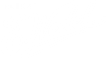
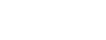
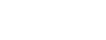
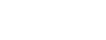






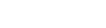
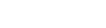
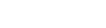
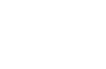
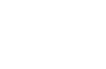
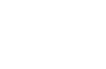
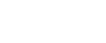
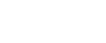
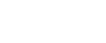
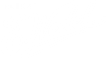
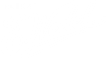
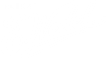
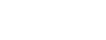
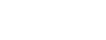
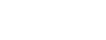






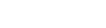
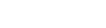
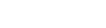
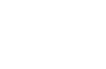
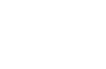
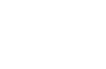
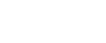
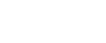
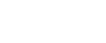
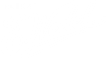
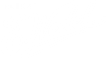
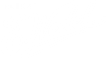
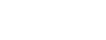
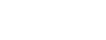
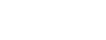






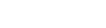
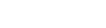
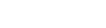
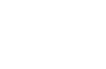
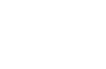
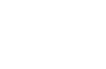
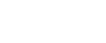
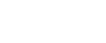
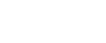
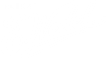
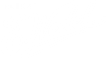
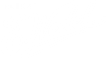
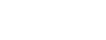
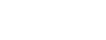
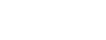


