What machines can be connected to the monitoring system? Do they necessarily have to be new machines? Or would it be better to include in the monitoring the old ones? Should they be highly automated machines? Can information be automatically obtained from manual workstations?-these and similar questions are usually asked by people who begin to think about introducing machine monitoring into their enterprise.
For the systems used to automatically collect data from machines – either a machine monitoring system or an MES system, whether the workstation is highly automated is irrelevant. We can include in the monitoring any machine that sends signals carrying useful information. And what we consider useful information is up to us.
So the key question to start with when thinking about monitoring machines and entire workstations is not what machines can be connected, but why connect the machines at all?
In order to get reliable data at the level of higher class systems, one must first of all take care of the quality and reliability of data from the lowest level, the machine level. This is where information about the product, about orders or about the positions of such machines flows.
Therefore, the decision on whether to connect a particular machine does not depend only on the type of production station. Much more important is what we want to achieve with the collected signals. Do we just need to get real-time data? Do we want to make the data we already have more reliable? Or is it important to us to relieve the burden on the people who do the manual entry of information, so that they can deal only with production? – These are the right questions to think about at the beggining.
Electrical signals
One of the frequently suggested ways to monitor production equipment is to collect signals from the electrical circuits of the machines. This solution has the advantage that there is no need to add additional sensors to the machines. One uses the already existing infrastructure. This is made possible by using auxiliary contacts of relays, which makes it possible to use already existing signals from machines in parallel. In this way, data can be collected, for example, using data hubs that convert electrical information (whether discrete or analog) into data in a specific protocol. The information thus obtained can be sent further into the system and processed in the next step.
Direct communication with the device
In this solution, data can be retrieved using PLC systems. A machine monitoring system or an MES system should include a number of communication drivers to connect to controllers from different PLC manufacturers. It is very important here that the variety of equipment used in production plants, which sometimes come from different manufacturers, does not limit the connectivity in any way.
Data protocols
Sometimes we have to deal with modern workstations that are prepared as a single unit – a complex workstation or production line. In the case of such solutions, it happens that their manufacturer has already provided some software for collecting or transmitting data. Such information from production stations does not have to come directly from the machines at all. To collect them, we can use a so-called intermediary data source such as an API, cloud or IoT controllers, which are already in the existing solution of a given manufacturer. Then all we need to do is download data from them and use it for further analysis whether historical or real-time.
Other ways
In addition to those mentioned, there are other ways to collect data. They can be, for example:
- CSV flat files, for example, historical data such as logs, alarms. Workstations very often save them for their own systems.
- Dedicated I/O modules, from manufacturers, who very often provide for the possibility of buying add-ons, designed specifically for specific, sometimes highly digitized, machines.
- Indirect signals such as energy analysis, where, based on energy, we can infer whether a machine is running or not, and with what load and sometimes even what product it is running.
- Wireless sensors to measure vibration or temperature. They do not require external power, so the need to wire the machine, which is often problematic and sometimes impossible, is dropped.
Classic sensors, i.e. optical, inductive or mechanical encoders, allowing you to collect reliable data. It is always possible to re-arm the machine with them if the signals we already have are not reliable enough, or we simply want to get even more reliability or better response time.
Sometimes it turns out that the reality of the machines and the expectations of the system user are two different worlds. Signals collected at the level of equipment and production stations, are needed to obtain reliable data that will be used to make key decisions for the company. It is therefore necessary to provide them to the system of the class above. It’s just that the upstream system expects already finished data, not raw signals.
Raw signals from machines can sometimes be noisy and require filtering. Another problem is that they may carry incomplete or not fully reliable information. The solution may be to combine several signals. For example, one signal can tell us that the machine is on, while a second signal, electrical or otherwise, can tell us that the spindle is running, thus also giving information about the operation of the machine. By combining the two signals together, we get even more reliable information.
But reliability is not the only thing that matters here. This combination of two signals sometimes allows us to see new context. It gives us additional information without increasing the costs associated with, for example, connections to further signals.
By using platforms that allow data to be modified, e.g. merged, scaled or processed to be as useful as possible for higher-end systems, new contexts can be created from it. Very often, this is an essential part of the puzzle to connect the user’s end result expectations on the system side with the reality of the machines.
Therefore, whether you use a machine monitoring system or an MES-class system in your enterprise, it is very important that it does not limit the possibility of further analysis and use of the obtained signals in a variety of ways, not just the one for which it was initially selected.
DIP ( Device Integration Platform) is a digitization platform that helps handle the logic layer of signals. What’s more, it also allows us to process the acquired data and create a so-called digital twin, i.e. a replica of a given system within a monitoring or MES system.
Having a physical resource, we can create a digital twin in terms of not only signals, but also alarm, logic, history or energy. This gives even more possibilities for later analysis.
What are the benefits of such an integration bus? For starters, it is the automation of data collection. This is very important, because the more data collected automatically, the more reliability we gain and the more time we save. Automatically recording the exact moment an event occurs, translates into reliable data. We can also relieve the workload of operators, which is very important, because such a system is not supposed to add responsibilities to employees, on the contrary, they are supposed to have fewer of them so they can focus on the most important tasks.
DIP also takes into account other benefits and needs of digitization. By creating a digital twin, it provides new opportunities for arbitrary processing of signal data, as well as allowing flexibility to adapt to changes in production resources and develop the system with new functionalities.
When choosing how to monitor machines, it’s good to think ahead and not close off more opportunities down the road, as this may only show further bottlenecks or potential areas for digitization that we would like to achieve.
Read also: Is machine monitoring an MES yet?
This article is based on material from the webinar: Connecting machines in 15 minutes – marketing vision vs. actual usability
See also
Want to learn more? Visit our Knowledge Base, where you'll find articles and webinars by experts to expand your knowledge.
Check if Digital Transformation is the Answer to Your Company's Needs

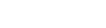
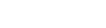
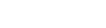
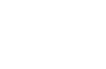
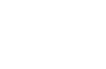
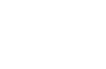
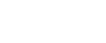
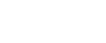
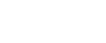
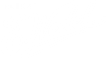
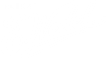
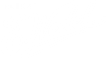
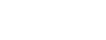
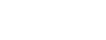
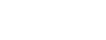






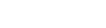
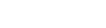
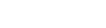
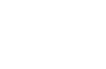
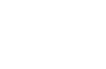
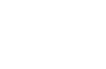
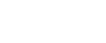
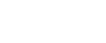
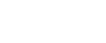
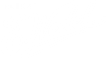
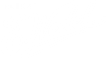
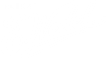
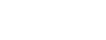
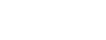
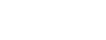






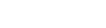
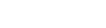
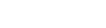
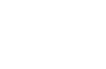
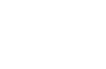
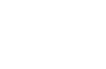
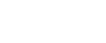
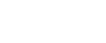
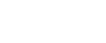
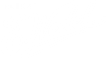
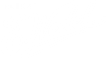
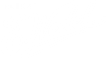
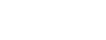
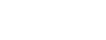
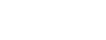






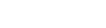
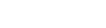
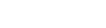
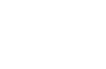
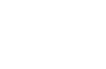
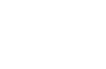
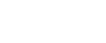
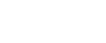
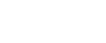
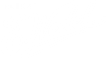
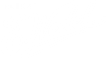
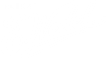
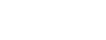
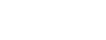
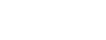


