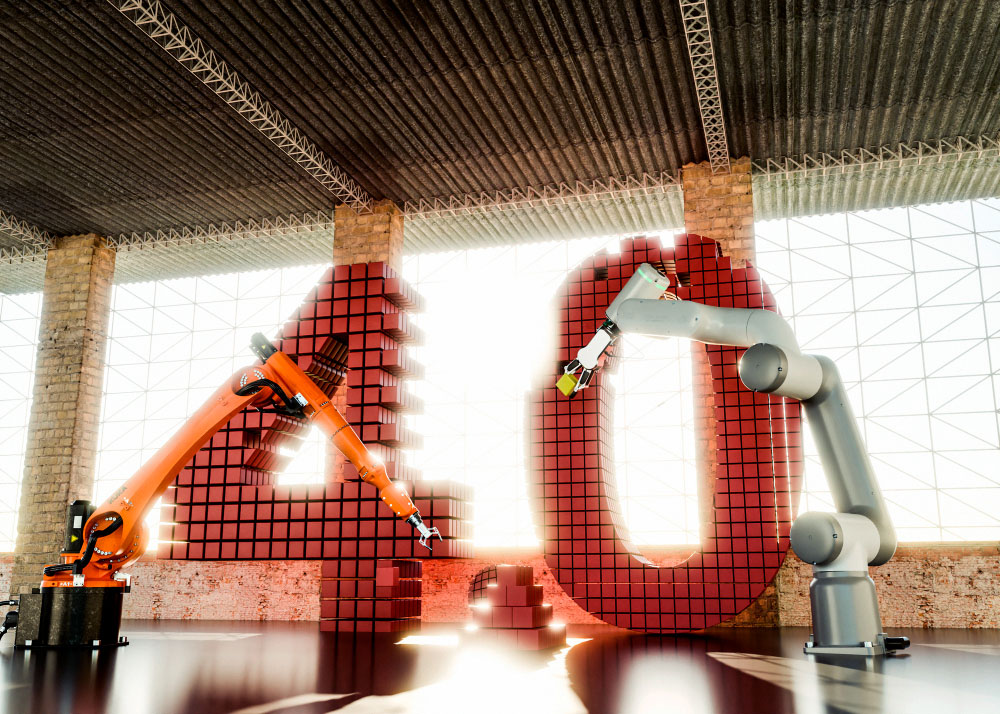
Is machine monitoring already MES?
Machine monitoring, communication with machines, collection of data from machines – these are terms that are becoming increasingly important in the context of the modernization of manufacturing companies and their transformation towards Industry 4.0. The purpose of such monitoring is to automatically collect data from production. And although it is most often referred to in the context of machines, in fact automatic monitoring, thanks to the metering of tools or the recording of input/output to such workstations, can also include manual workstations.
Automatic collection of data from machines and their processing are tasks in which production management systems of the MES class, i.e. Manufacturing Execution Systems, are a great support. However, is this the only solution? Recently, one hears more and more about machine monitoring systems, and a lot of solutions of this type have appeared on the market – machine monitoring, availability monitoring, fleet efficiency monitoring, etc. Marketing messages mainly talk about the advantages of such solutions, such as connection to machines in as little as 15 minutes and visible results in a short time. Is machine monitoring really a quick and easy solution worth investing in? Before making a final decision, it is worth analyzing the pros and cons of such systems, as well as looking at them from a broader perspective – in the context of the operation of the entire enterprise and future plans.
To clarify what place machine monitoring systems have and how they relate to MES-class systems, let’s start by looking at the hierarchy of systems in a company. Level one is based on the machines that make production possible. Level two is responsible for controlling these machines, while level three is production management in the broadest sense. At the very top we have the planning level.
Undoubtedly, machine data is essential at level two, where it is used to directly supervise the production process in the technological sense. Process information such as machine settings, temperatures, pressures, electrical parameters, etc. are monitored here. Appropriate alarms are generated based on this information. In this way, the entire process can be run safely and stably, within the established limits.
At the third level, data is needed for the broad management of production and production resources. This is most often where automation and information collection deficiencies occur. This level can make use of a range of data, collected from machines by the aforementioned second level, the control level.
In addition to this, the production management level also needs a lot of other data that is not necessary for level two and is often absent there. These include, for example, information about orders, products, operators, machine states, production buffer states or warehouses. Their absence means that even in companies that have strongly developed data collection at level two, the need arises for additional communication with machines and workstations from the MES level or indirectly through the existing level two.
This leads to the conclusion that even in companies where data collection is not yet developed to level two (PLC/SCADA), it is possible to develop level three, i.e. production management, as much as possible, starting with the automatic collection of data from machines and workstations needed just for this level.
Machine monitoring systems are tertiary level systems, or production management systems. They have three main technical components:
- automation means, which make it possible to collect data from machines and workstations at all;
- operator interfaces, allowing for the collection of that information which cannot be, or at a given time is not worth collecting automatically;
- interfaces (of the operator and possibly other users) and a reporting system through which we can access the data obtained.
Machine monitoring systems most often claim to provide knowledge about availability, productivity and quality of production. OEE calculation is also a common option.
An enterprise is a complex organism. Many workstations, machines, lines, departments, people, and often many plants geographically dispersed in one country or even around the world. The larger the enterprise, the more complex the information flow process, and the more effective it is, the more efficiently the enterprise functions. Therefore, full digitization of such a complex organism requires a holistic view and the right approach. This is facilitated by models developed by specialized committee.
ISA 95
One such international standard is the ISA 95 model, developed by the International Society of Automation ISA organization. It defines how information is processed at the third level, i.e. between machines and the company’s ERP business management systems. This approach is designed to meet the needs necessary for a company’s operation at the production and production management level, and to ensure a two-way and automated flow of information between machines, production management and enterprise systems such as ERP.
ISA used to use the term MES. Nowadays, following the path of digitization, one can come across a new definition – MOM (from Manufacturing Operations Management). It is an extension of MES with several additional functionalities. MOM has four roles: manufacturing operations management, maintenance management, quality management and inventory management.
Model SIM
Another popular model for digitization in the production management layer is the model developed by MESA International. The current model is the SIM model (from Strategic Initiatives Model), the successor to the previously known c-MES and MES-11 models. The SIM model defines 10 functional areas of production in collaboration with business operations, all in the context of the company’s strategic initiatives
Both ISA 95 and the related MOM model and the SIM model are based on years of experience of specialists from manufacturing and implementation companies and software vendors. Both models show that the situation in companies is complex, and there are a number of topics associated with the digitization of production management that will need to be addressed over time. Otherwise, they will become a bottleneck in the flow of information, and thus have an adverse effect on company management.
On the market you can find various types of information systems, supporting production management, which are used to implement these models. The widest range of functionality is offered by MES class systems, which allow management of operations and production efficiency and quality.
Additional classes of systems we often encounter in the market are APS (Advanced Planning and Scheduling) – for managing planning and scheduling, CMMS (Computerized Maintenance Management Systems) – for automated maintenance support, or WMS (Warehouse Management System) – for managing inventory, warehouses.
How does machine monitoring compare to the previously mentioned models? Compared to MES-class systems, it has a much smaller range of functionality, focused mainly on the area of performance management, or performance management. Although other elements from the scope of the models presented can also be seen, but for the most part machine monitoring is focused not on the whole, but on a slice of issues related to production efficiency management.
The area of production performance management is usually an important step in the digitization of enterprises. Often during the development of a digitization plan in the form of the recently popular Digital Transformation Road Maps, it is in this area that the first initiatives for implementation appear. This is because of the potentially large benefits that can be gained by addressing this particular area.
So can machine monitoring, operating mainly in the area of production management, be an effective step in digitization? It depends on various factors. It is certainly worth taking into account the future plans of a given company and carefully reviewing the pros and cons of this solution.
Advantages:
– Digitization – this is the most frequently highlighted advantage of machine monitoring. It involves the elimination of paper, and thus not only supports ecology, but brings savings to the company. However, the most beneficial effect of digitization is primarily the elimination, or at least minimization, of errors during data collection and processing, which enables management by facts.
– Speed of implementation – depending on the complexity of the system in question and the various dependencies, implementation counts in weeks or even days, and connecting the machine itself to the system can literally take 15 minutes.
– Financial benefits – the area of production efficiency management, where machine monitoring can be applied, is attractive for investment and usually has very short payback periods. This is because any change in machine availability or performance translates directly into higher production, and therefore higher revenues and potentially higher profits.
Potential disadvantages:
– Functionality limited to only a select portion of performance management functionality – machine monitoring systems do not include the “quality” component in OEE calculations, and sometimes fail to account for the fact that on a given machine, different products can be made at different nominal capacities, resulting in skewed OEE rates when producing different products. Sometimes the data is devoid of order context or the correlation with order context is in the time domain.
– Limited integration capabilities – access to data intended for use for other purposes is limited or sometimes there is no integration with other systems at all.
– No or limited possibilities to develop the system with further functionalities – there are limited possibilities, for example, to calculate one’s own KPIs or to expand with further elements of the previously mentioned ISA 95 and SIM models.
Experience shows that the application of a machine monitoring system solves many of the problems in the area for which the solution is dedicated, while at the same time it quite quickly exposes further bottlenecks in the company and thus generates further needs for digitization, including outside the area of production performance management.
How many constraints or opportunities to develop machine monitoring applications with further functionalities we will have to deal with depends mainly on the IT architecture in which the application was implemented. Generalizing, there are currently 3 main architectures, giving companies 3 methods of digitization. These are:
– integration of multiple stand-alone applications,
– a suite of integrated, specialized modules,
– flexible digitization platforms with specialized modules.
Each of them brings different consequences and further opportunities for digitization. The third option, a flexible digitization platform with specialized modules, is the most favorable in terms of development. When a machine monitoring system is part of such a platform, it paves the way for further full digitization.
A machine monitoring system is not yet MES system, but it can bring visible benefits to a company and be the first step towards digitization. When deciding on such a solution, it is worth looking ahead, also keeping in mind future steps in digitization, delineated on the basis of global experience and presented in models developed by specialists.
Read also: Different ways to monitor machines and workplaces. Usability and future prospects
The article is based on material from the webinar: Connecting machines in 15 minutes – marketing vision vs. actual usability
Read also: Different ways of monitoring machines and workplaces. Usability and future prospects
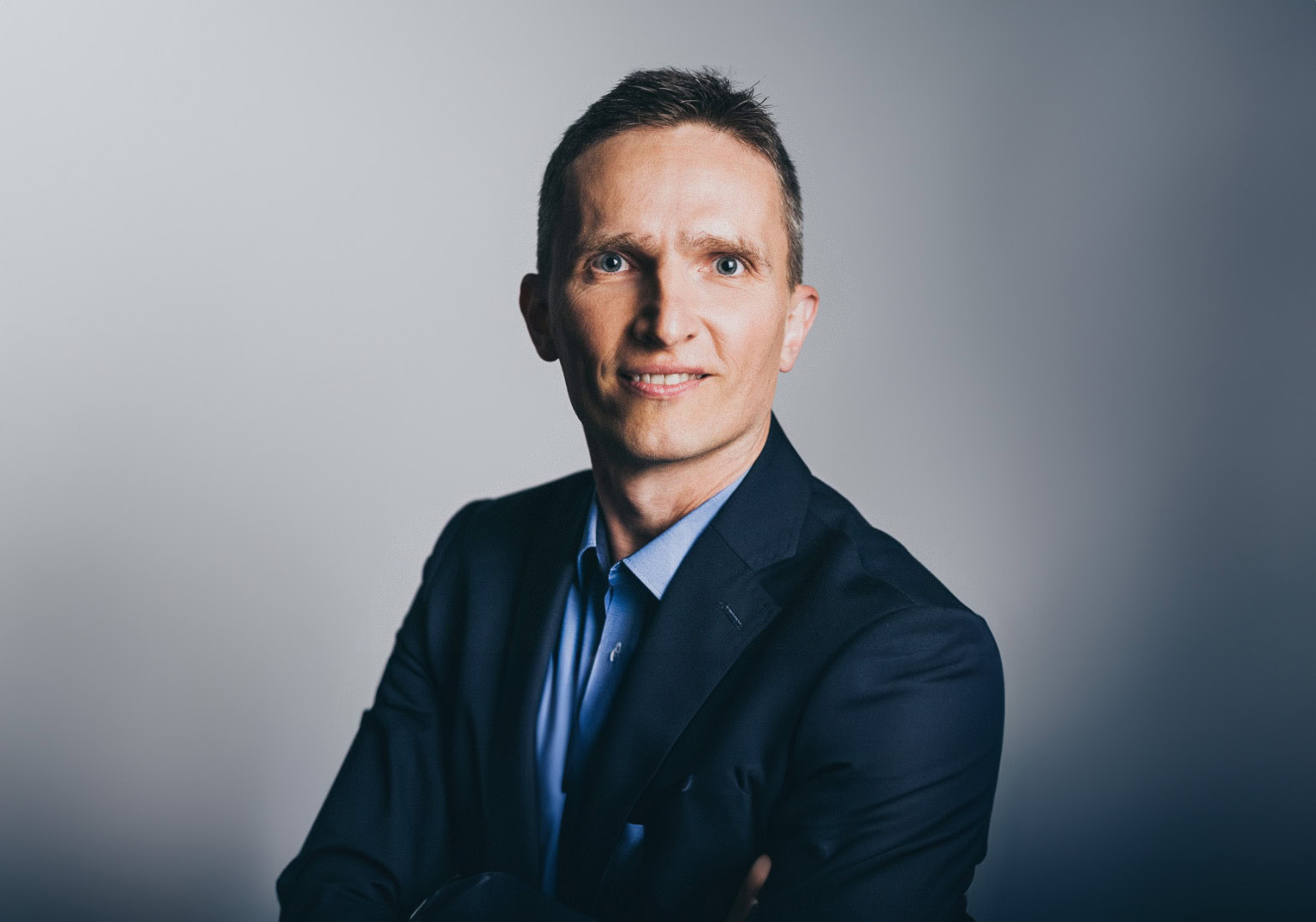
Artur Masłowski graduated in Automation and Robotics from Szczecin University of Technology. For nearly 20 years as a member of the ASTOR Group, he had actively focused on improving efficiency, quality, and process optimization in manufacturing and infrastructure companies, employing solutions in automation, industrial IT, and robotics.
Since 2018, he has contributed his skills to the Improvement Factory team, where his responsibilities include the comprehensive business development of organizations, consulting on industrial IT solutions, formalizing and negotiating project agreements with clients, and overseeing the successful implementation of projects.
See also
Want to learn more? Visit our Knowledge Base, where you'll find articles and webinars by experts to expand your knowledge.
Check if Digital Transformation is the Answer to Your Company's Needs

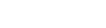
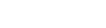
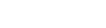
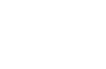
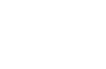
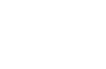
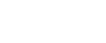
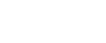
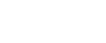
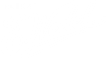
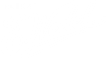
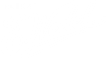
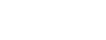
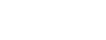
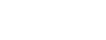






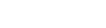
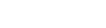
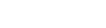
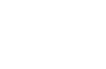
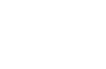
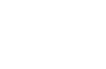
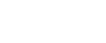
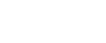
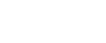
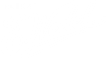
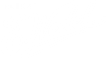
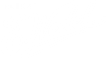
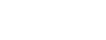
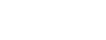
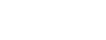






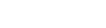
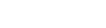
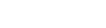
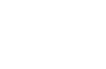
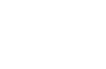
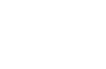
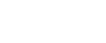
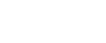
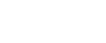
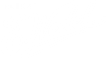
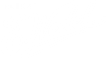
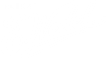
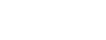
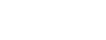
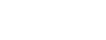






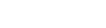
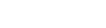
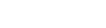
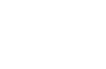
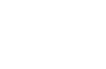
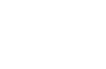
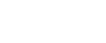
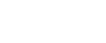
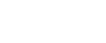
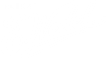
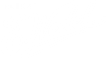
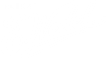
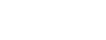
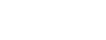
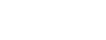


