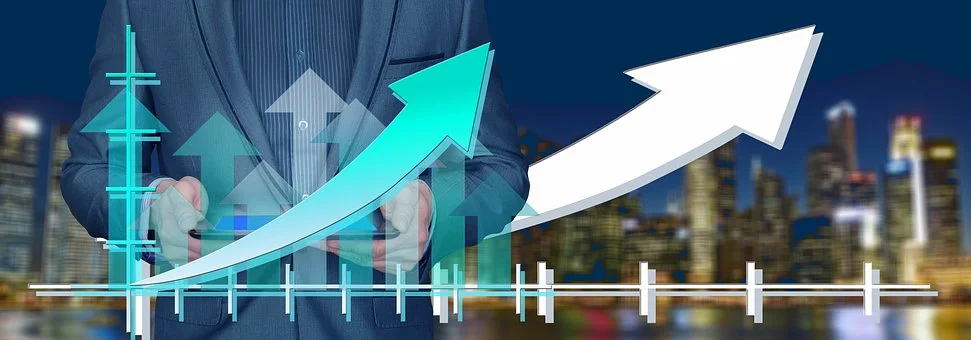
Reliable Manufacturing Data: How to Collect and Qualify It?
The level of technological advancement within an industrial plant or factory has a direct influence on the methods employed for collecting manufacturing data.This, in turn, influences key production indicators like OEE (Overall Equipment Efficiency). This connection is particularly important, as only well defined and categorized individual components yield dependable manufacturing data.
Is there a single, optimal method for gathering manufacturing data from workstations? In truth, the approach depends on the level and manner of digitization at a given workstation.
Data can be collected manually. Nevertheless, even in the case of a fully manual workstation, certain data can be gathered automatically. Examples of such information include specific events, such as shift transitioning according to a schedule, definitions of production breaks, and service schedules adhering to a specific timetable. Through these events, certain aspects can be automated on manual workstations.
Hybrid data collection methods prove effective wherever access to information is limited. In this context, limited access implies that a machine can provide only several simple signals, such as “start”, “stop”, or “item added”.In such scenarios, we can derive additional information from these signals, such as whether a machine is operational, in a downtime state, or actively producing. Operators can then clarify this basic data.
The most advantageous situation arises when dealing with machines offering high levels of information accessibility. This enables the use of automated manufacturing data collection. Consequently, not only is more information gathered, but also less workload is put on operators,allowing them to concentrate on production instead of monitoring machine statuses. Moreover, when manufacturing data is automatically collected in real time, the risk of inconsistencies stemming from manual recording is eliminated. Resultantly, the gathered information is more reliable, enabling management by fact.
Frequently, production staff and management grapple with the classification of manufacturing data regarding changeovers. Should they be included in the availability factor as part of productive work, unplanned downtime, or planned downtime?
There is no one right answer to this query.The most versatile approach involves categorizing changeovers as unplanned downtime. Why this choice? In the absence of standardized changeover durations, considering them as planned downtime will lead to overlooking crucial information.Similarly, designating changeovers as productive work isn’t ideal either – this would increase the time, but lower the performance, thereby affecting overall operational calculations.
The optimal choice is to qualify changeovers as unplanned downtime
To enhance changeover optimization, multiple methods can be employed. One of them is Single Minute Exchange of Die (SMED),which streamlines the duration of equipment changeovers. The initial step of this method involves systematically documenting changeover operations to ensure comprehensive awareness of these processes.
The introduction of automation for standard changeover durations can be advantageous, enabling a detailed examination of each stage. How to achieve this? Firstly, a standard changeover time is established. If this time is exceeded, an automated shift to the state of the corresponding workstation occurs, influencing the OEE indicator differently. This way we know that a changeover occurred, we are able to track it and subsequently analyze its duration and impact on the overarching indicator.
Another element of the manufacturing process that may be difficult to classify is waste.The complexity of quality control charts for individual items often prompts pertinent questions:1. Should all discarded material be designated as scrap? 2. Must every “bad” item be classified as scrap, rendering it permanently excluded from performance calculations? Not necessarily. What if subsequent assessments reveal an item initially deemed scrap was, in fact, salvageable and we’d like to reclassify it? Such scenarios are sufficiently frequent to be taken into careful consideration.
Does waste have an impact on performance? In principle, it shouldn’t, since performance is calculated per all items. In OEE calculation it is crucial that a single loss only affects one specific component of the indicator. Thus, it’s imperative to avoid the duplication of an agent’s influence across multiple OEE factors.
Waste categorization. Source: ImFactory
Reclassification also demands attention. With a change in status, such as when a defective item undergoes repair, the quality factor needs recalibration to incorporate the repaired item. Similarly, we should be vigilant for re-works and repairs. Each repair operation impacts performance. While production time is extended, necessitating appropriate adjustments, the item ceases to be faulty and should be reclassified as a good item.
Another interesting case that often leads to uncertainty in the pursuit of reliable manufacturing data involves the classification of micro-stoppages. This situation introduces additional questions: Should a decrease in production rate impact the availability or performance factor of the OEE indicator? The answer hinges on the specific circumstances.
Production rate decrease – performance or availability? Source: ImFactory
Micro-stoppages should factor into availability when the data collection process is automated. If we are able to clearly determine what constitutes a micro-stoppage and its implications, automated systems can transmit information on these micro-stoppages based on our predefined criteria, which should then be included in the availability factor.
When micro-stoppages are defined manually, they should be included in the performance factor. Why? To minimize additional workload for operators. Given that micro-stoppages can be numerous and brief, it’s essential to avoid burdening workstation operators with excessive responsibilities.
One potential trap during the process of manufacturing data collection is the duplication of losses. This refers to the aforementioned multiple classification of the same type of loss. When defining various indicators, extra caution is needed to prevent configuring the system in a manner where a single loss impacts several different indicators.
For instance, if we were to consider only good items instead of the entire production when calculating performance, we would essentially replicate losses. An analogous situation arises with changeovers – categorizing them as work would influence both availability and performance factors.
Hence, in order to attain reliable manufacturing data, we must avoid duplicating losses. Our objective should be for a single loss to influence only one specific indicator.
What exactly do we mean by “equipment utilization”? This concept encompasses a diverse array of machines and workstations,which may also include highly automated setups.
For instance, let’s focus on a workstation called “workstation X.” Upon receiving an alert of a malfunction, the underlying cause remains unclear.While the machine signals a malfunction and a potential jam, only a worker can determine the cause of this occurrence.In this scenario, it’s the operator who specifies that the issue stems from shaft damage.
To streamline the analysis of manufacturing data, the practice of applying extra flags, such as downtime tags, proves invaluable. These additional tags enable a more comprehensive examination of indicators and machine conditions. Machine signals serve to alert us that something is wrong,yet the specifics often elude such signals. Delving into the data using supplemental downtime root cause tags and their associated classifications helps to discover why, for instance, our availability has experienced a decline.
Hierarchy of equipment utilization classification. Source: ImFactory
Nominal production rate is often the most difficult element to define.This parameter carries considerable significance as it represents the target state we aim to achieve. The problem in defining it arises not due to its inherent difficulty, but rather from the fact that plants or organizations in the process of introducing the OEE indicator may not have previously established nominal production rates. The determinants of the nominal production rate frequently encompass the following factors:
- the machine,
- the product,
- the material,
- staff experience,
- staff availability,
- combination of these variables.
The nominal production rate should reflect individual scenarios that emerge based on the nature of production, type of equipment, and the like. For example, one machine may yield a specific rate for manufacturing product X, while another machine processing the same product might operate at a distinct rate.
How to define the nominal production rate? A few good practices can prove helpful:
Manufacturer’s guidelines
Manufacturers often provide the nominal production rate for a given machine. However, it’s crucial to acknowledge that this rate is typically achievable under ideal conditions As such, it should serve as a starting point for calculating our own nominal rate.
Staff experience
The invaluable insights of operators, leaders, and workers who operate specific machinery or workstations play a pivotal role in determining the nominal production rate. They know best what to be aware of and how to identify factors that impact performance, whether positively or negatively.
The BoB Method
Employing the “Best of Best” method involves analyzing and selecting the five best results from a given period, subsequently calculating their average. This statistical approach provides the most accurate measurement, as it filters out anomalies that might have skewed the production rate.
Continuous feedback loop
While useful, this approach requires caution, as the specific indicator is prone to fluctuations that can influence subsequent measurements. Thus, this method should be implemented over an extended timeframe. If the measurement period is too short, it becomes challenging to make meaningful comparisons and slight changes in our nominal values occur.
Mere collection of manufacturing data falls short of generating truly reliable information. A profound awareness of potential sources of inaccuracies is essential, coupled with an effort to eliminate them through meticulous definition and classification of individual factors. Only through this conscientious approach dependable data can be acquired, establishing a solid foundation for management by fact.
Author: Adrian Szczypski, Deputy Manager | Implementation Department
Adrian Szczypski is a graduate in Automatic Control and Robotics from Gdansk University of Technology. As a Project Manager, he brings a wealth of experience in implementing IT systems in manufacturing environments. Through continuous validation of client needs, he and his team successfully develop products that generate business profits for manufacturing companies. Given his specialization, he also takes on the responsibility of IT resource allocation and client requirements management within the ImFactory team.
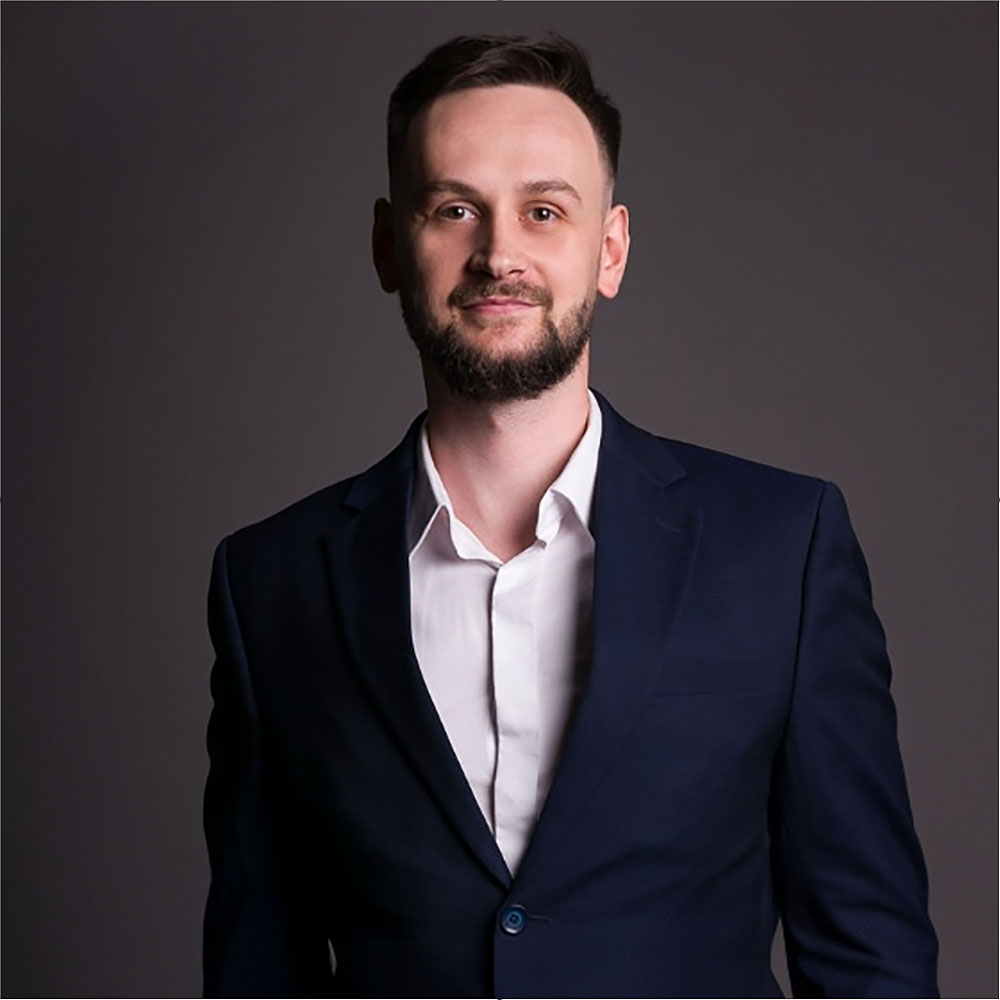
Adrian Szczypski is a graduate in Automatic Control and Robotics from Gdansk University of Technology. As a Project Manager, he brings a wealth of experience in implementing IT systems in manufacturing environments. Through continuous validation of client needs, he and his team successfully develop products that generate business profits for manufacturing companies. Given his specialization, he also takes on the responsibility of IT resource allocation and client requirements management within the ImFactory team.
See also
Want to learn more? Visit our Knowledge Base, where you'll find articles and webinars by experts to expand your knowledge.
Check if Digital Transformation is the Answer to Your Company's Needs

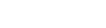
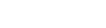
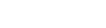
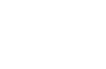
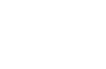
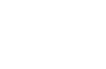
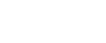
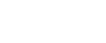
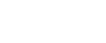
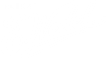
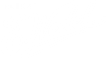
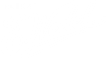
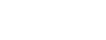
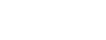
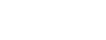






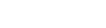
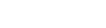
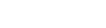
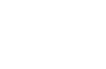
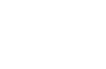
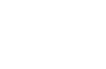
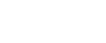
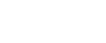
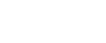
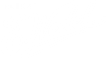
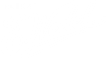
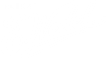
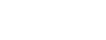
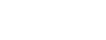
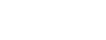






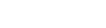
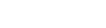
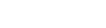
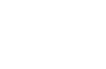
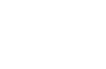
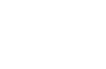
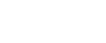
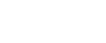
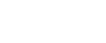
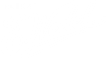
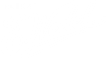
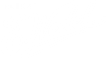
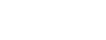
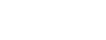
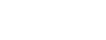






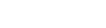
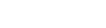
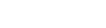
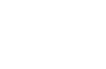
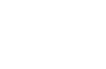
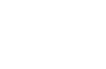
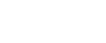
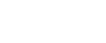
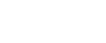
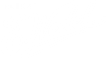
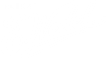
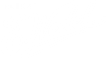
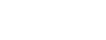
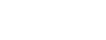
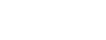


