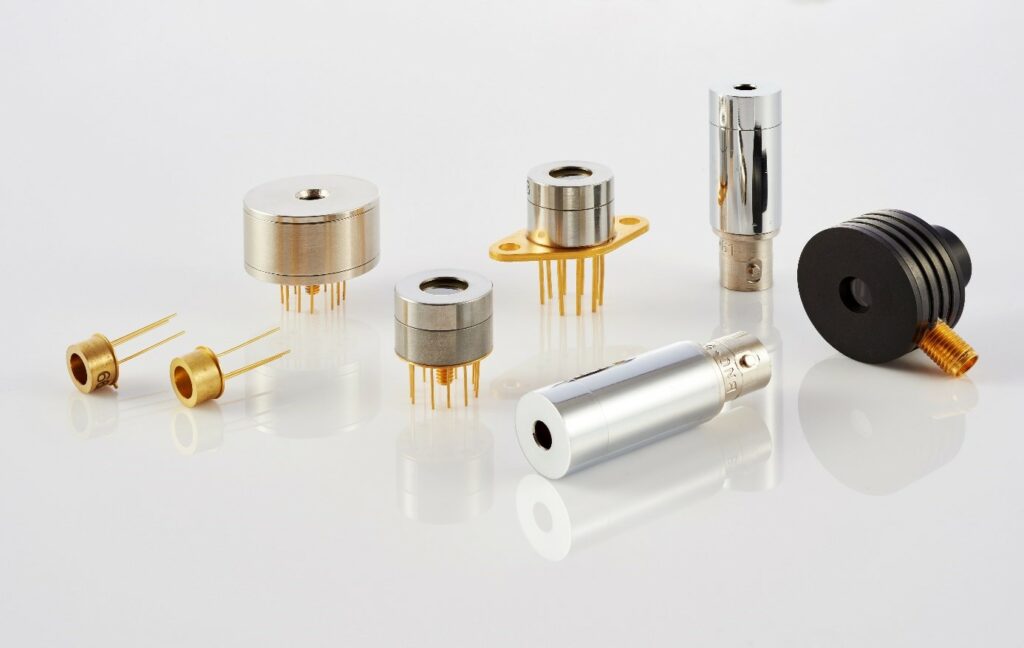
VIGO System SA: Revolutionizing Manufacturing Process Management with Digital Transformation
VIGO System SA is a manufacturer of semiconductor materials for photonics and microelectronics with over 30 years of experience. It was founded in 1987 as one of the earliest Polish startups. Right from the start, the company’s founders focused on the most advanced markets, enabling VIGO SA to become a supplier for NASA, with its detectors contributing to the detection of methane on Mars.
The story of VIGO System SA. Source: the company’s YouTube Channel
VIGO System SA manufactures various types of detectors for rapid temperature measurement, gas analysis,and the monitoring of hazardous substance emissions, among others. In Poland, VIGO supplies products to the Polish Armaments Group (PGZ SA), but the majority of its production is exported to Europe, China, and Japan. The company’s clients include NASA, Safran Aerotechnics, Emerson Electric Co., Caterpillar, and TRUMPF.
Photonics, the field in which VIGO System SA specializes, is a rapidly evolving field with substantial business potential. Numerous projects that were once confined to laboratory testing and scientific research are now transitioning into industrial applications. There is a growing emphasis on environmental protection, leading to an increased demand for monitoring CO2 emissions and hazardous substances in the air and water.
Known as the technology of the future, photonics is driving the development and modernization of solutions rooted in electronics and information technology. Consequently, a natural progression for modern technologies is to adopt photonics solutions. The fourth industrial revolution, with digitalization as its integral component, cannot exist without photonics, which plays a pivotal role in data gathering (sensors, cameras), processing (algorithms and optoelectronic systems), and transmission (lasers, optical fibers, data transfer systems, and displays).
The photonics market is expanding at an annual rate of 20-30%, accompanied by a corresponding increase in competition. Despite its achievements and recognition within the industry, VIGO SA aimed to become a major player for a prolonged period. Until 2015, its annual turnover hovered around EUR 5-6 million. To establish fruitful partnerships with large companies and become a competitive force in Europe and worldwide, the owners of VIGO System SA had to embrace significant changes. These changes, once implemented, would allow the company to flourish. Consequently, there arose the need to plan the company’s development over a longer time horizon and adopt a new strategy, with digital transformation as a key component.
“In 2016, after many years of organic growth, we adopted a new, considerably more aggressive company development strategy. We were aware that our potential to become a dominant player in the photonics market could only be realized through a successful transformation from a manufacturing plant into a modern production facility operating in accordance with semiconductor industry standards”, explains Łukasz Piekarski, CFO at VIGO System SA, regarding the rationale behind the investment.
The decision to chart a new course for VIGO System SA was made in 2015. The strategy crafted at that time primarily aimed to introduce new materials (due to regulatory requirements to phase out mercury and cadmium) and to secure additional contracts and a leadership position in the global market. To achieve these goals, an increase in operational scale was imperative.
VIGO System SA set forth ambitious objectives: the company aspired to maintain a healthy profit margin while growing its revenue by three to fourfold. Up until then, the facility had been producing approximately five thousand detectors annually, a figure that fell short of enabling substantial growth. To meet these objectives, several key parameters had to be fulfilled:
- Significantly increase the volume of detectors released into the market;
- Reduce production costs and enhance cost monitoring;
- Accelerate and streamline the entire process.
Moreover, they aimed to reshape the company to position it favorably for future growth. Given the constantly evolving technologies and emerging trends, the changes needed to be adaptable to market dynamics. Automation emerged as the optimal solution, with a particular focus on streamlining information flow and implementing comprehensive organizational changes.
“Digitalizing production posed a significant challenge, not only due to the scale of the task and the company’s developmental stage at the beginning of the project but also because of the need to shift employees’ mindset. Lab-like working habits had to be replaced with newly established operational patterns suited for serial and repetitive production. We required software capable of supporting these changes and systematizing employee tasks”, explains Marcin Ratajczyk, Director of Production at VIGO System SA.
Hence, the overarching objective for VIGO System SA became providing systematic support in the digital transformation process while ensuring stable growth and expanding production capacity. The most suitable solution was found in the implementation of an MES, primarily tasked with supporting production oversight and execution.
Two crucial aspects of these changes were the ability to automate production accounting, seamlessly integrated with an ERP system, and the integration with measurement software. The company needed a tool that would facilitate scheduling and task planning, standardize descriptions of applied technologies, and provide an efficient means of implementation. As Marcin Ratajczyk, Production Director, notes:
“The process of digitalization unfolded during a period of rapid company growth and numerous organizational process changes. Starting with the implementation phase and continuing over the following years, both our proprietary POTOK software (Pomiary, Obliczenia, Testy Oraz Kwalifikacja, meaning Measurements, Calculations, Tests, and Qualification) and the AVEVA MES had to undergo multiple modifications and enhancements to meet the evolving challenges of our dynamically transforming organization. The dedication of our programmers and a strong partnership with ImFactory (formerly MES Solutions by ASTOR) enabled the software to evolve alongside the company, encompassing more and more facets of production and delivering new functionalities.”
VIGO System SA approached ASTOR Group consultants for assistance in implementing the planned changes. The initial stages of the transformation were challenging. There was a lack of standards related to the description of the technologies being used. Individual processes were known only to their respective managers and varied significantly depending on the specific product. Foremen manually accounted for materials in the ERP system, which was not only time-consuming but also prone to errors, and each team organized their work according to their own rules.
Fig. 1: One of the as-is state maps created as a result of consultations.
Grzegorz Fijałka, Key Account Manager at ASTOR, recalls the beginning of the collaboration:
“In June 2016, ASTOR Warsaw received a typical email: “One piece of MES, please”, listing eleven functional areas that such a system should cover, as extracted from the definition. A few days later, during a meeting with the Board, as we presented best practices for preparing investments in these types of systems, the course of action was approved, and work on the consulting proposal began. The goal was to create a thorough diagnosis of the as-is state, including business goals and usage scenarios, leading to a set of technical and organizational recommendations. After refining the scope, plan, and tasks, collaborative work began in September. We were particularly pleased that the recommendations for production optimization provided by ASTOR and its expertise partner were diligently followed by the team of VIGO System SA, who did a great job of preparing the organization for changes.”
Through several hours of workshops, systemic standards were established. Based on these standards, an interface was created to expedite the development of new technologies for VIGO System SA products, building upon existing ones. A unified interface format was introduced for all teams, significantly enhancing production supervision.
Fig. 2: User interface for production order supervision and management
“The implementation of a production management system necessitated the identification and subsequent filling of previously unaddressed gaps. Technologies and their delivery methods were reorganized, a unified product database was created, material nomenclature was standardized, and the need for instructions was defined. This entire endeavor can be summarized as the integration of the company’s activities. From a point where each team managed its area independently and in ways convenient to them, but not necessarily coherent with other areas, the organization transitioned to a state where everyone operates according to defined standards. This transformation profoundly affects the sense of belonging to the organization”, concludes Marta Pawlak, Project Manager and MES Supervisor at VIGO System SA.
Previously, most work was performed manually, which was not only inefficient and time-consuming but also prone to quality issues. A pilot project in this context involved the automated assembly of windows onto detector enclosures.
An equally significant challenge at VIGO System SA was data organization. At the production stage, each detector undergoes multiple measurements and characterizations. This used to take place at over a dozen workstations, where various parameters were recorded using a range of measurement devices, each equipped with its own data transfer protocols. All this information had to be manually transcribed between different systems.
Using the AVEVA Enterprise Integrator tool, it became possible to consolidate multiple measurement workstations into a single system. This eliminated the need for manual data transcription. The data is now automatically collected in a software solution developed by VIGO System SA engineers, “POTOK”, for further measurements, calculations, tests and qualification. This software not only determines whether a detector meets standards but also provides a vast dataset for various analyses, serving as the foundation for device certification.
Fig. 3: Enterprise Integrator and POTOK+ in the system communication structure at VIGO System SA
Michał Zieliński, Partner at ImFactory, Project Manager, and Head of the Digital Consulting Department, shares insights into their collaboration with VIGO System SA:
“Our collaboration with VIGO System SA employees was an incredibly enriching experience. High-tech technology, developed over years by a team of top-notch scientists, needed to be described properly, in order to provide the necessary information for advanced analyses, while streamlining the work of operators – assembly workers and technicians who prioritize effectiveness and ergonomic work. Striking the right balance between these two aspects was a genuine challenge. Fortunately, the AVEVA MES standards, refined over many years in the market, provided valuable guidance.”
The real challenge lay in changing the mindset among employees, particularly concerning the specific operation of the system. The task of the implemented tool was to record all actions that were previously left unrecorded. Initially, concerns arose among the employees that the system was there to control rather than support them. The key to changing this mindset proved to be a series of discussions held at every stage of the change, coupled with training sessions and demonstrations of the benefits the system could offer in streamlining daily work. The process of adapting to the new MES went through several stages. Initially, it was seen as a mere “clicking” tool, which significantly hindered the process of convincing employees about its implementation and the benefits it could provide. Gradually, there was an understanding that MES, by processing vast amounts of data, could impact not only the quality of work but also the efficiency of the overall change. Finally, employees actively engaged in the changes. This was made possible because the system also addressed their needs, and the introduced modifications and enhancements were in response to their voices. This approach allowed for successful MES implementation, despite the initial challenges. Users at every level now see their role in shaping the system and recognize the system’s role in reducing their workload. This achievement was made possible through open collaboration, both from VIGO System SA and ImFactory.
As Marta Pawlak emphasizes:
“The invaluable collaboration and advice provided by the ImFactory team were essential. A project of this magnitude is no easy endeavor, as it requires stepping out of one’s comfort zone and departing from the familiar to adapt to a structure that is still being created. We experienced ImFactory’s support at every moment during the project, and we could rely on their assistance not only in terms of system solutions but also in Lean management and overall organization. The coordinator of all these activities plays a significant role in such a project, as it demands full commitment and the ability to adjust the changes in a way that everyone can benefit from them. Despite the challenges, working on MES maintenance together with ImFactory has brought me immense satisfaction.”
Fig. 4: Interface for managing in-house orders for production
Automation and increased supervision over the manufacturing process supports the ability to produce tens, or even hundreds of thousands of detectors annually. Revenues from production have been steadily increasing, with an average annual growth rate of over 20% in recent years.
The transformation and implementation of a manufacturing management system were essential to accommodate the company’s growth plans and solidify its position in the market. One of the visible outcomes of the transformation is the improved control over production and the simplification of suboptimal processes achieved by establishing uniform standards and automating previously manual tasks.
The implementation of the MES was just one part of the successful transformation process for the company and the adoption of new operational standards. The introduction of new management systems using appropriate IT tools, including the MES, allowed VIGO System SA to increase production, save time, reduce the number of complaints, and significantly boost profits, as confirmed by Łukasz Piekarski, CFO at VIGO System SA.
What does digitalization offer to companies? It signifies progress not only in the technological realm but also in the development of engineers in every conceivable aspect. This includes improvements in collaboration, project management, communication, and adaptability to change. All these soft skills are essential for the success of digital transformation. In essence, the synergy between technology and people is a guarantee of elevating a company and its production to a higher level. VIGO System SA is already there.
PRODUCTS PROVIDED BY ImFactory:
- AVEVA System Platform,
- AVEVA Supervisory Client,
- AVEVA InTouch,
- AVEVA MES Performance,
- AVEVA MES Operations,
- AVEVA Enterprise Integration,
- Rob-Ex Scheduler,
- Microsoft SQL Server and CAL licenses,
- Microsoft Windows and RDS CAL licenses,
- DELL servers and disk array.
See also
Want to learn more? Visit our Knowledge Base, where you'll find articles and webinars by experts to expand your knowledge.
Check if Digital Transformation is the Answer to Your Company's Needs
The Free Consultation Process:

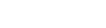
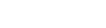
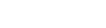
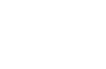
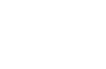
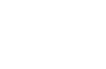
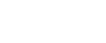
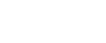
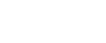
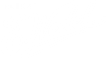
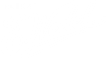
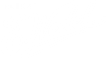
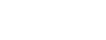
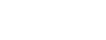
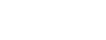






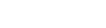
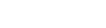
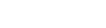
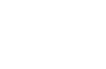
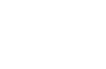
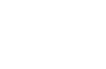
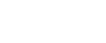
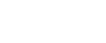
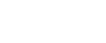
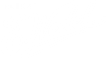
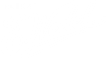
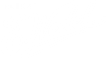
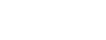
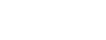
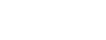






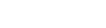
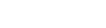
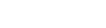
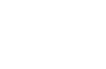
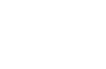
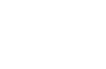
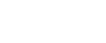
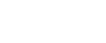
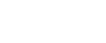
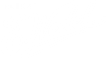
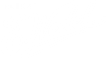
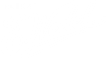
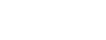
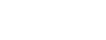
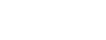






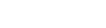
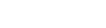
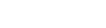
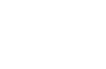
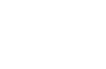
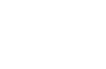
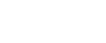
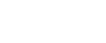
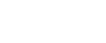
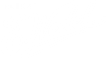
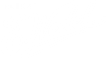
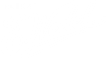
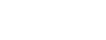
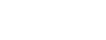
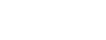


