
Digital Transformation in VIGO Photonics S.A.: Transitioning from Analogue to Digital Production
VIGO Photonics S.A. has been in the market since the 1980s. Since its beginnings, the company has been at the forefront of harnessing modern technologies developed by scientists from the Military University of Technology in Warsaw. It specializes in manufacturing semiconductor materials and devices for photonics and microelectronics, with a particular focus on MWIR and LWIR detectors and modules developed using proprietary technologies.
The company’s customers include Emerson Electronics Co., Caterpillar and Safran Aerotechnics. One of the most notable achievements of VIGO Photonics S.A. is the collaboration with NASA, supplying detectors for the Mars rover and contributing to the detection of methane on Mars.
Currently, VIGO Photonics S.A. stands as one of the fastest-growing businesses in the industry, continually expanding its operations. With sales representation in Taiwan and the US, it has become a global company. However, this was not always the case. Despite its significant successes, the company did not fully harness its potential for many years. It wasn’t until entering the stock exchange in 2015 that rapid growth became possible.
Photonics, hailed as the technology of the future, has been rapidly evolving in the era of Industry 4.0. The industry’s demand for innovative solutions continues to soar, intensifying the competition.
VIGO Photonics S.A. possessed the potential to become a key player in the photonics market. However, to gain new clients and establish a leadership position, the company needed to significantly expand its operations.
This required enhanced operational efficiency. The company which had previously operated like a traditional manufacturing plant, heavily reliant on manual labor from highly specialized workers, recognized the need to transform into a modern manufacturing facility.
VIGO Photonics S.A. set ambitious goals for itself, including:
- achieving a three-to-four-fold increase in revenue;
- establishing collaborations with prominent companies;
- increasing production while reducing costs;
- streamlining manufacturing processes and implementing better supervision.
„We faced a significant challenge of increasing our production capacity from a few thousand detectors per year to over one hundred thousand detectors and modules annually. We were aware that this could not be achieved without an effective IT tool to support production supervision and management.”
To address the needs of VIGO Photonics S.A., a transformation in work organization, digitalization, and automation was crucial. Essentially, the chosen solution had to:
- offer automatic production accounting in seamless integration with the ERP system;
- integrate with VIGO’s proprietary measurement software;
- facilitate scheduling and task planning;
- enable standardization of technology descriptions.
The company opted to implement the AVEVA Manufacturing Execution System (MES), a comprehensive solution that fulfilled all these requirements. Its primary objective was to support production supervision and execution. Previously, manual manufacturing management had prevailed, lacking a consistent supervision system, which significantly hindered overall processes.
The implementation of the MES and tailoring it to a company’s specific needs is a long and complex process that requires professional assistance. To accomplish this, VIGO Photonics S.A.partnered with Improvement Factory.
In June 2016, a meeting with the Board was held to establish a clear course of action. After a thorough assessment of the current state, defining the goals, determining the scope of work and a detailed plan, the two companies began fruitful collaboration in September 2016.
The implementation of the MES commenced by outlining the modules to be utilized at each stage of the production process. A standardized user interface format was designed, followed by a reorganization and transfer of technologies. Additionally, the product base was unified, and the need for instructions was identified.
It was crucial to familiarize all employees with the new work standards.
„Together with VIGO Photonics S.A. we have conducted a comprehensive training program for their entire workforce, ranging from line operators, supervisors, individuals responsive for process descriptions, managers, production coordination teams, all the way up to executive-level training with end-users: directors and board members.”
– Michał Zieliński, Project Manager, Improvement Factory sp. z o.o.
The digital transformation of the production process at VIGO Photonics S.A. proved to be a formidable undertaking, given the scale and developmental stage of the company at the beginning of MES implementation. Various tools and applications already in use within the company posed additional challenges.
System integration turned out to be the greatest challenge. The automation and consolidation of manual data collection from various devices and measurement stations into a single system was achieved with the deployment of AVEVA Enterprise Integrator.
Adapting the employees to the new solution presented its own set of challenges. The system’s task was to record the previously unregistered activities. Concerns arose among the employees that the system would become a tool for controlling them and holding them accountable. Through meetings and discussions at different stages of the project, the employees recognized that the changes were primarily intended to expedite processes and support them in their daily tasks.
The implementation of the MES, enabling automation and enhanced control over the manufacturing process, has significantly contributed to the company’s growth, facilitating production on an unprecedented scale. The transformation has yielded several notable benefits, including:
- a consistent increase in production revenue;
- simplification of suboptimal processes;
- reduction in the unit cost of production;
- substantial decrease in the number of complaints;
- establishment of credibility through a standardized and closely monitored manufacturing process.
„The implementation of a system helps us deal with an increased production volume, as well as a higher number of orders to automate certain tasks, actions and processes that are typically performed by humans. As time goes on, this becomes automatic and people begin to recognize and appreciate the benefits of this technology.”
– Marcin Ratajczyk, Production Director, VIGO Photonics S.A.
„The digital transformation of the production process at VIGO Photonics S.A. allowed us to identify gaps that had previously been overlooked. This helped us to organize our production processes, document them, and bring them together as a cohesive whole.”
– Marta Pawlak, Project Manager, VIGO Photonics S.A.
Investing in a MES solution is an ongoing endeavor that extends beyond its initial deployment. Such systems evolve alongside the development of the entire company. VIGO Photonics S.A recognizes this, with the MES serving as a crucial element of its long-term strategy.
„We are constantly improving our MES system, with plans to introduce new areas, technologies, and most importantly, to make work easier and more efficient. As we continue to improve our technology, we are also working on developing software that will make our employees’ work easier, faster, and more convenient.”
– Marcin Ratajczyk, Production Director, VIGO Photonics S.A.
In the coming years, the company aims to maintain an annual growth rate of 20 -30%. The MES will play a pivotal role in achieving these goals. At these following stages, VIGO Photonics S.A can rely on the unwavering support of its partner at each stage of development.
„As the AVEVA MES Competence Center, our role in the project does not end with the implementation and deployment phase. We continuously strive to encourage the organization’s development so that the system evolves to meet the changing needs of our client.”
– Michał Zieliński, Project Manager, Improvement Factory sp. z o.o.
Striving to operate as a modern company and serve the world’s leading technological corporations, which demand the highest quality and customer service standards, VIGO Photonics S.A. recognized the need to enhance its production capacity and exert full control over all processes. This was made possible not only through the implementation of an advanced IT tool, the AVEVA Manufacturing Execution System, but also through invaluable consulting support and collaboration with experts from ImFactory.
VIGO Photonics S.A recently announced another remarkable achievement. The company’s project, initiated in 2020, was the only one from Poland to be selected for EU funding. With the potential to secure over EUR 100 million, VIGO aims to become the world’s first manufacturer of MIRPIC – a mid-infrared source and detector encapsulated in a small chip. This innovative solution has the potential to replace the current bulky detectors and pave the way for the development of new devices. In line with this vision, the company plans to build a semiconductor factory near Warsaw.
See also
Want to learn more? Visit our Knowledge Base, where you'll find articles and webinars by experts to expand your knowledge.
Check if Digital Transformation is the Answer to Your Company's Needs

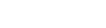
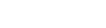
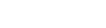
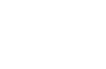
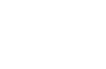
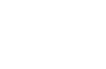
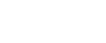
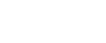
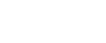
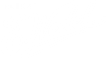
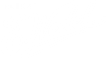
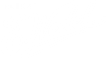
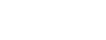
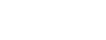
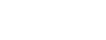






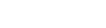
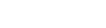
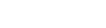
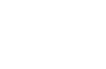
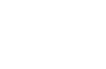
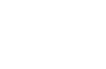
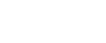
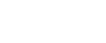
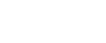
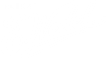
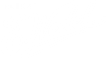
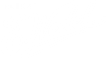
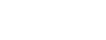
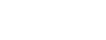
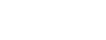






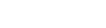
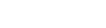
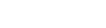
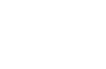
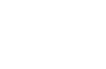
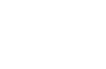
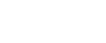
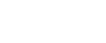
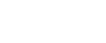
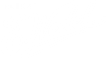
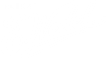
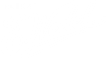
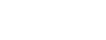
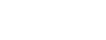
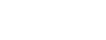






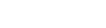
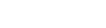
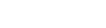
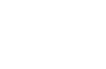
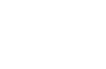
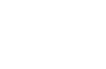
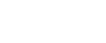
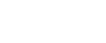
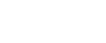
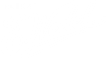
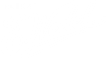
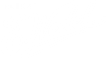
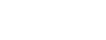
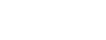
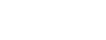


