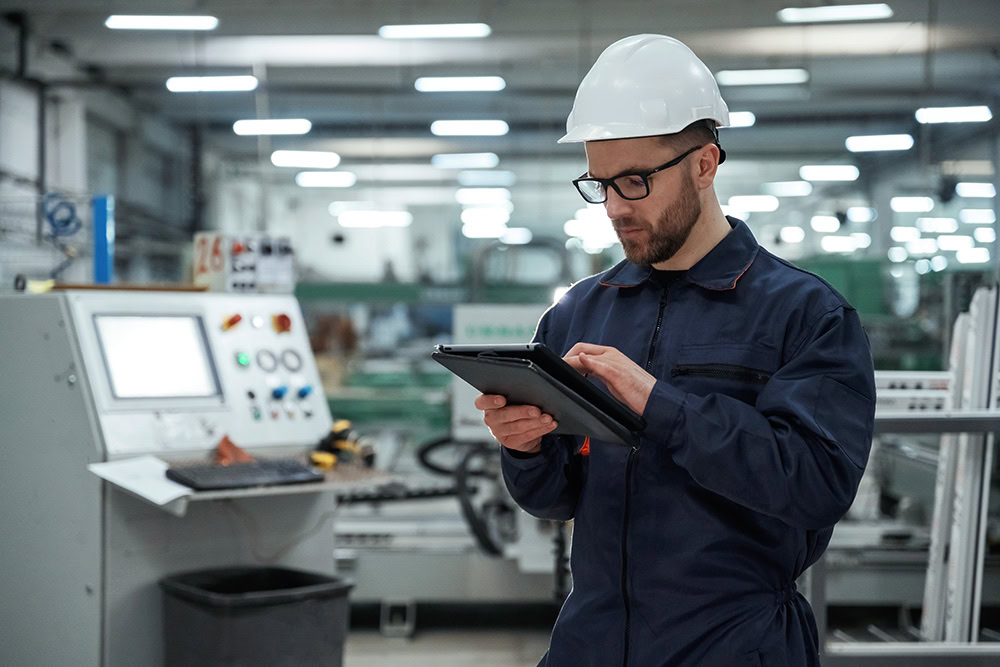
Shopfloor Management Systems for Quick and Effective Digitalization
Investing in new technologies and specialized equipment is a critical component of digital transformation, essential for reaching the status of a Factory of the Future. Still, even the best equipment won’t bring the expected outcome if not utilized effectively. This is where shopfloor management systems, like ImProdis or AVEVA MES, come to help. Let’s examine such systems more closely.
In our article on OEE, we presented an example of a company that invested significant funds in a new machine with the goal of increasing profits. The assumption was that the machine would operate throughout the full 8-hour shift. However, planned breaks and downtimes reduced that time by 45 minutes. Another 21 minutes were lost on unplanned events, and performance and quality issues took almost three hours of production time.
In the end, the machine operated efficiently for only half of the scheduled time. It goes without saying that this is a highly unsatisfactory result. Unfortunately, this situation is far from uncommon – numerous manufacturing companies struggle with this issue on a daily basis.
So, what can be done? Why is effectiveness at this level, and how can we improve it to fully utilize our assets while minimizing losses? The answer to these critical questions can be found with the help of shopfloor management systems.
Shopfloor management systems form an essential element of digital transformation. What role do they play in this process? If we define digital transformation as a temple founded on three pillars – people, processes, and technology – shopfloor management systems fall under the last pillar. These technologically advanced tools support the development of manufacturing firms.
Read more about digital transformation and its pillars in the article: Cyfrowa Transformacja – czym jest i dlaczego warto do niej dążyć?
And what is the place of shopfloor management systems in an enterprise? According to ISA-95 levels, they are positioned on the third level, where direct management and supervision of production processes occur.
The Manufacturing Execution System (MES) also operates on this level. However, it’s important to note that shopfloor management systems and MES are not identical. MES is a much broader concept, whereas shopfloor management systems can fulfill some of MES functions. Hence, they could be considered a subgroup of MES, just as MES is a subgroup of Manufacturing Operations Management (MOM) systems.
Who can benefit from implementing a shopfloor management system? In fact, the entire company can. This tool finds practical applications at various levels, although its role is different in every context. Here are several of these contexts based on the three basic structures that can be distinguished in every enterprise:
- Management Level: This includes the management board, plant director, and people responsible for setting goals. Their main objective is to shape the company’s mission and develop strategies over the long-term, encompassing years, half-years, and quarters. They need general knowledge on key areas, provided through metrics like KPIs, which indicate how effectively the company functions.
- Operational Level: This level is formed by managerial staff, process supervision, production supervision, and the maintenance department. They need specific, smaller goals, coherent with the company’s strategy. These people focus on shorter periods, ranging from a month to a single day, and base their work on contextual information that can be quickly transformed into specific tasks.
- Production Level: This level consists of production operators and line or cell operators, focused on specific tasks to complete. They are primarily interested in the present moment, the current shift, and the immediate outcome. They work closest to the process, so they both use and generate the data for higher levels.
Now that we understand what shopfloor management systems are, what place they have in the digital transformation process, which level they operate on, and who can benefit from them, how is all this reflected in practice? What kind of support do these systems provide?
Simply put, the key objective of shopfloor management systems is to ensure that each of their users receives the needed information at the right time, tailored to the context in which they operate.
This information is the foundation of efficient operations at all levels of the company. What is more, a feedback loop is created: from the management level, goals are cascaded down into plans and tasks, which are then executed, generating data that is turned into information and knowledge, feeding back into the highest level to support strategy development.
Read more about the role of data in manufacturing companies and management by fact: Reliable Manufacturing Data: How to Collect and Qualify It?
As technology developed, several models of the architecture of shopfloor management systems were created.
The following diagram shows the ISA levels and various elements representing IT systems that function within a manufacturing facility. At the highest level, where the enterprise is managed, there are: Enterprise Resource Planning (ERP), Customer Relationships Management (CRM), and Supply Chain Management (SCM) systems.
Model 1: The first shopfloor management systems operated by connecting PLCs and a version of HMI, where individual indicators could be calculated for specific production cells.
Model 2: In the second, more advanced model, shopfloor management systems are based on SCADA functionalities and a reporting platform, which doesn’t necessarily need to be a full Business Intelligence (BI) platform.
Model 3: The third model is significantly more advanced, representing a full-fledged shopfloor management system based on MES or MOM, with full BI. This model is commonly combined with additional analysis.
Model 4: The fourth still-evolving model is based on industrial application platforms, where various functionalities interconnect within a shared infrastructure. We can develop essential functions within this structure, spanning across increasingly broader areas.
As previously mentioned, the primary purpose of shopfloor management systems is to ensure that each user receives the exact information they need, in the appropriate context and form. This not only simplifies their work but also delivers numerous benefits to the entire company.
Having access to up-to-date information facilitates better business decision-making, sensible resource management, greater control over production processes and order statuses, easier identification and elimination of bottlenecks, improved performance, and enhanced quality.
All these factors contribute to better management of the whole facility, hence the term “shopfloor management systems”. Efficient production is often accompanied by cost reductions, which can, in turn, enhance a company’s competitiveness.
Are you interested in reducing costs? Read our article: Costs Under Control: Effective Financial Management in a Manufacturing Enterprise
Shopfloor management systems offer comprehensive support to an entire enterprise, increasing efficiency by delivering accurate information to the right people and departments, at the right time and in the right context. These systems can operate within various architectures, depending on the developmental stage of the company. Shopfloor management systems are continuously evolving, offering increasingly advanced functionalities to support manufacturing companies on their path to digital transformation.
Are you thinking about implementing a shopfloor management system in your company and searching for the right solution? Contact us!
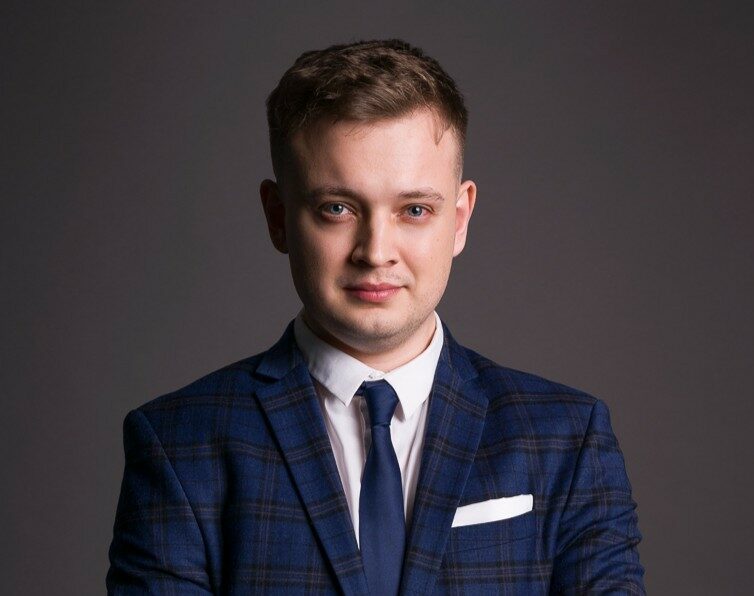
Michał Zieliński is a graduate in Automatic Control and Robotics, as well as a postgraduate Lean Six Sigma Black Belt from Gdansk University of Technology. He is a partner at ImFactory, where he works as a Project Manager and Head of the Digital Consulting Department. At ImFactory, he is involved in shaping a vision for the advancement of IT systems in manufacturing environments, evaluating the digital maturity of enterprises, and planning their Digital Transformation journey. His projects encompass a wide range of activities, from overseeing surveillance and monitoring installations to implementing comprehensive integrated manufacturing management systems.
See also
Want to learn more? Visit our Knowledge Base, where you'll find articles and webinars by experts to expand your knowledge.
Check if Digital Transformation is the Answer to Your Company's Needs

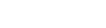
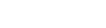
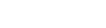
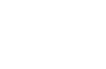
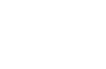
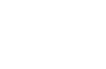
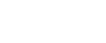
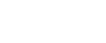
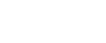
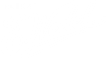
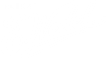
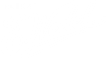
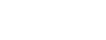
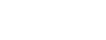
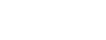






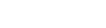
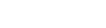
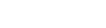
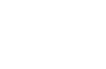
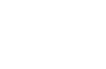
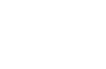
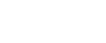
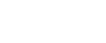
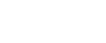
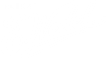
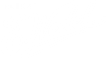
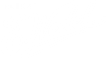
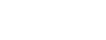
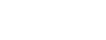
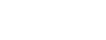






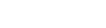
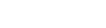
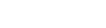
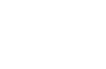
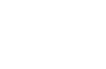
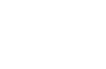
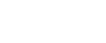
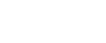
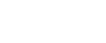
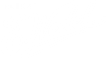
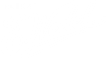
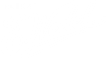
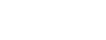
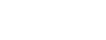
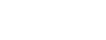






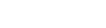
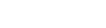
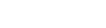
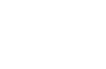
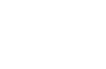
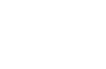
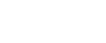
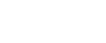
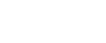
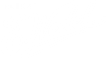
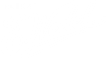
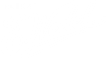
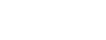
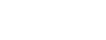
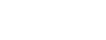


