Discrete Manufacturing
Discrete manufacturing brings forth many challenges, such as the need for flexible adaptation to current customer requirements, market demands, or the specifics of a given product. Specialized systems for discrete manufacturing can be the answer to the needs of manufacturers in this sector. Such systems facilitate process control, help implement even unexpected changes efficiently, quickly identify potential problem sources, manage quality, and much more.
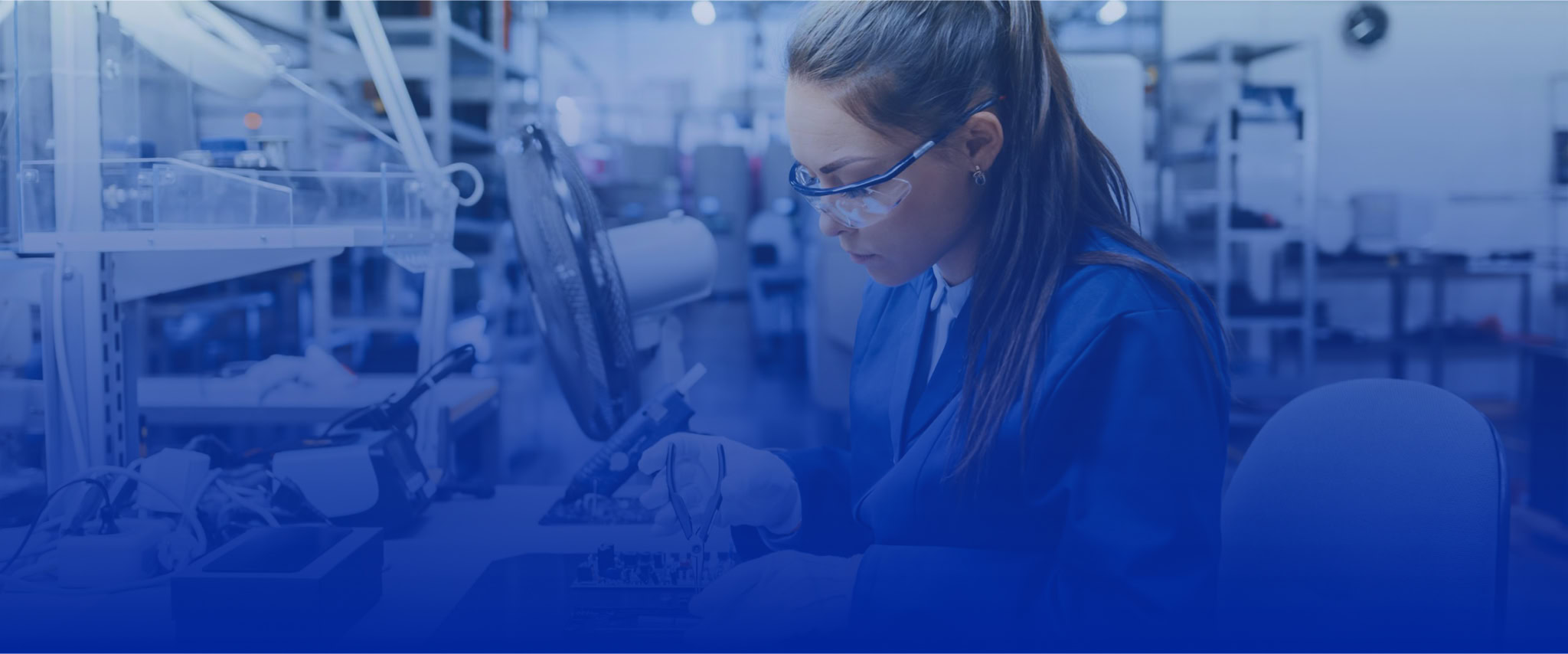
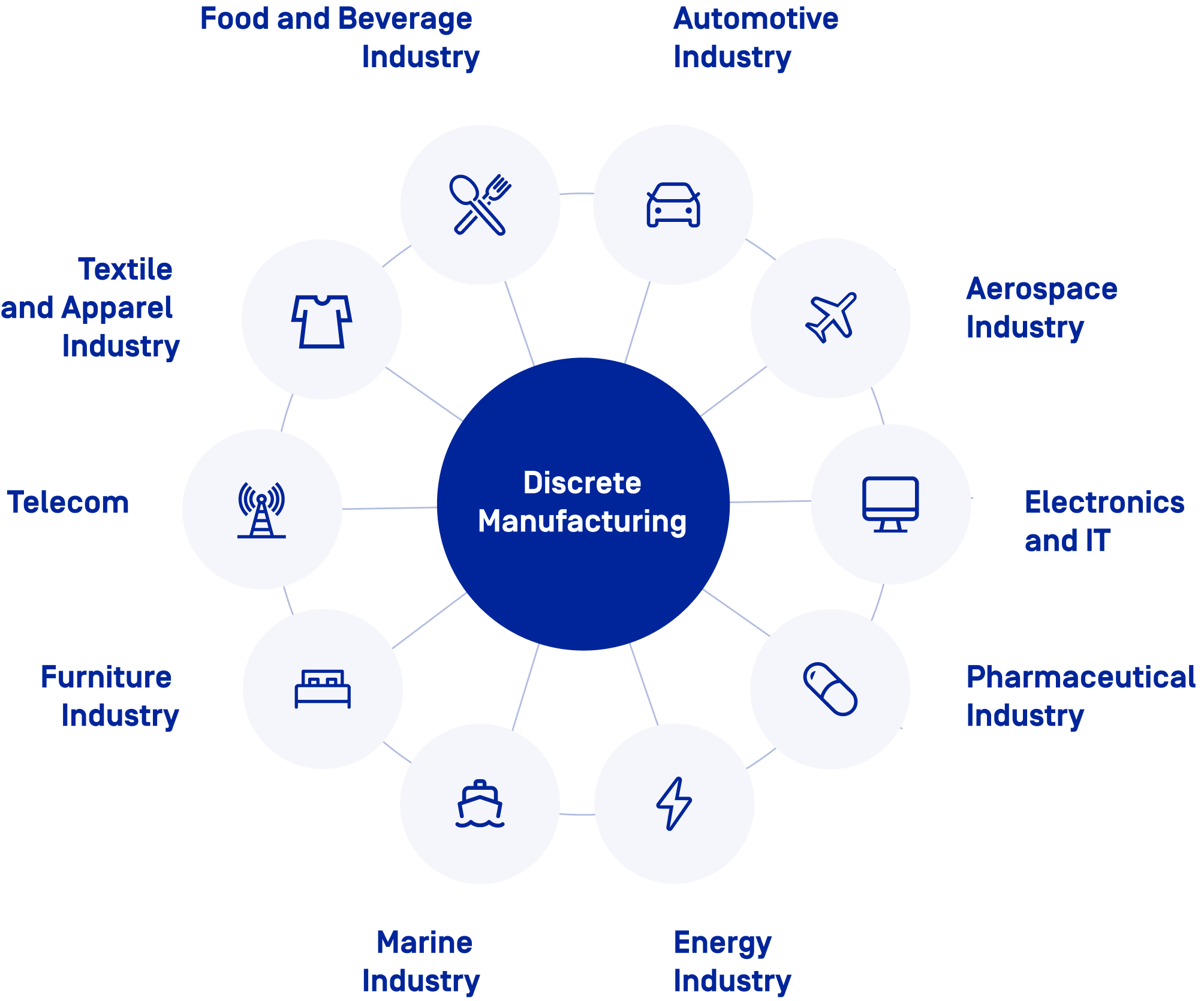
What is Discrete Manufacturing?
Discrete manufacturing is one of the main forms of production, focusing on manufacturing items in an individual way. It differs from process manufacturing, which involves continuous production of a specific product, and batch manufacturing, where processing occurs in batches.
In practice, the products made in discrete manufacturing are concrete, individual, countable and sometimes serialized. Each is a distinct entity, like a car, a piece of furniture, or a computer. One facility can manufacture various products, each with its own specifications.
Discrete manufacturing can include raw material processing, prefabrication, assembly of different components, quality testing, and packaging. Later in the process, these elements can be parts of larger items, but they are separate entities on their own – visible, tangible, and countable.
Success Stories
Discover how discrete manufacturing companies benefit from implementing professional manufacturing support systems
Discrete manufacturing – challenges
See what the discrete industry’s biggest challenges are and how to deal with them.
Integrating All Stages of the Process
Manufactured products often consist of many parts from different suppliers. Ensuring the availability of all elements and the smooth execution of their assembly is crucial for seamless running of the entire process.
- MES (Manufacturing Execution System): Helps integrate the process by automatically tracking each production stage, providing information about available resources, individual operations, and deliveries. The system aids smooth collaboration between warehouse, logistics, and production.
- APS (Advanced Planning and Scheduling): Creates plans and schedules for various departments based on data from MES, taking account of numerous factors and integrating elements of even the most complex processes.
High Variability and Customization of Products
Adapting to individual customer needs, changing industry requirements, and ever-advancing trends requires flexibility, which can only be achieved with appropriate manufacturing management tools. Traditional planning methods using spreadsheets or basic ERP systems can be too time-consuming and inefficient.
- APS: As a professional scheduling system, it can generate both simple and complex plans within seconds, considering various factors. With the “What if” functionality, it facilitates the analysis of various options and alternative scenarios, which can be compared to choose the best version.
- MES: Flexible modeling of production technologies supports manufacturing execution even with high variability and short series.
Short Delivery Times
Efficiency in meeting promised delivery times enhances competitiveness and builds customer trust. Eliminating unnecessary operations and optimizing schedules is key for quick and seamless delivery.
- MES: By automatically collecting detailed information on the entire process, the system helps identify inefficient actions that affect product development process.
- APS: allows realistic delivery time estimation using the Capable-To-Promise function.
Unforeseen Downtimes and Failures
Unexpected machine downtimes can disrupt the whole production process and cause significant delays. Although they cannot be eliminated entirely, continuous monitoring can minimize their impact by addressing problematic issues immediately after they occur.
- MES: Monitors key parameters of machine and manufacturing line operation in real-time, identifying causes of downtimes and issuing alerts for preventive actions.
- APS: Facilitates quick response to changing resource availability, eliminating the missing resources from production plan, remodeling the schedule, and sending it as an update.
Effective Inventory Management
Both excessive stockpiling and shortages are problematic. Excess leads to storage issues and generates unnecessary costs, while shortage of even one element can cause delays and disrupt the whole production schedule.
- MES: Tracks the flow of materials and semi-finished products in real time, from the beginning to the end of the process. This enables users to monitor usage, identify deficiencies, and take appropriate action to prevent both production halts and overstocking.
- APS: Its functionalities are particularly beneficial in supporting smooth MRP (Material Requirements Planning) run and ensuring effective planning of subproduct manufacturing and order preparation.
Order Changes
In discrete manufacturing, order modifications are not uncommon. Changes in orders, such as delivery dates, quantities, or variants, are a major obstacle and require frequent schedule updates and increased workload, for example in the form of overtime.
- APS: Thanks to advanced algorithms, the system quickly reacts to changes and unexpected situations, generating updated plans that account for new requirements.
- MES: Through advanced integration mechanisms, any changes at the level of ERP and APS are promptly transferred to MES and implemented in production.
Bottlenecks
Identifying and eliminating process bottlenecks is essential for preventing delays. This can only be done with detailed knowledge about what happens at every stage of production.
- MES: Provides detailed knowledge of production stages, helping identify problematic areas and eliminate the underlying cause.
- APS: By reporting real work progress from MES to APS, it is possible to detect potential performance issues and react accordingly by adjusting resources and schedules as needed.
Discrete manufacturing industries
The flexibility of discrete manufacturing facilitates using individual components in various configurations and incorporating additional elements. Thanks to this, products can be customized to individual customer needs or quickly changing market trends. Discrete manufacturing is prevalent in many industries, including:
MES system in discrete manufacturing
Expand your knowledge of MES systems. Learn practical functionalities that are a real support for discrete manufacturing.
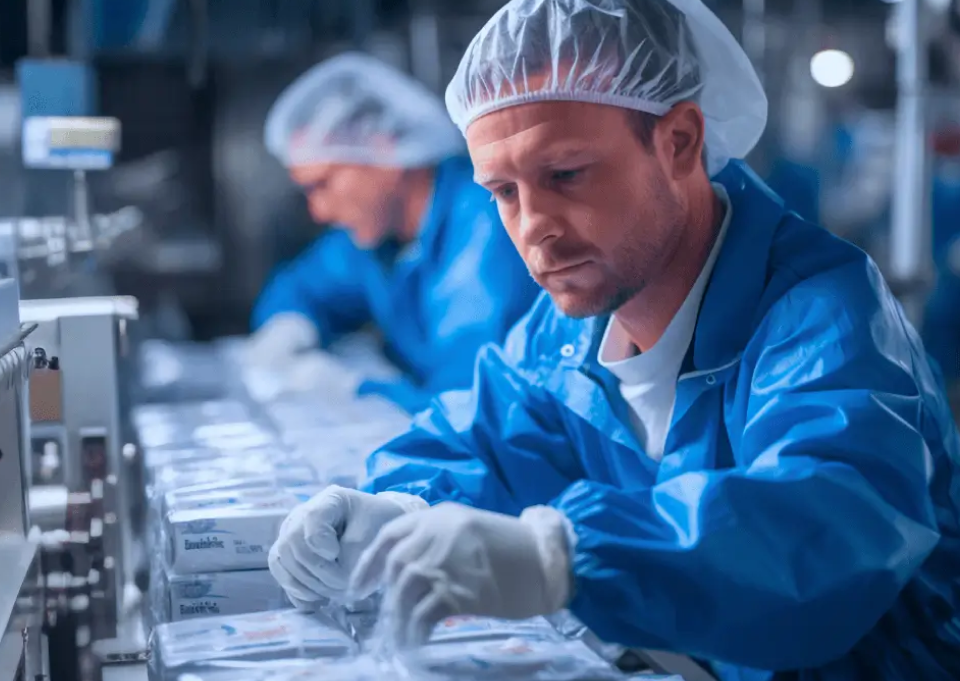
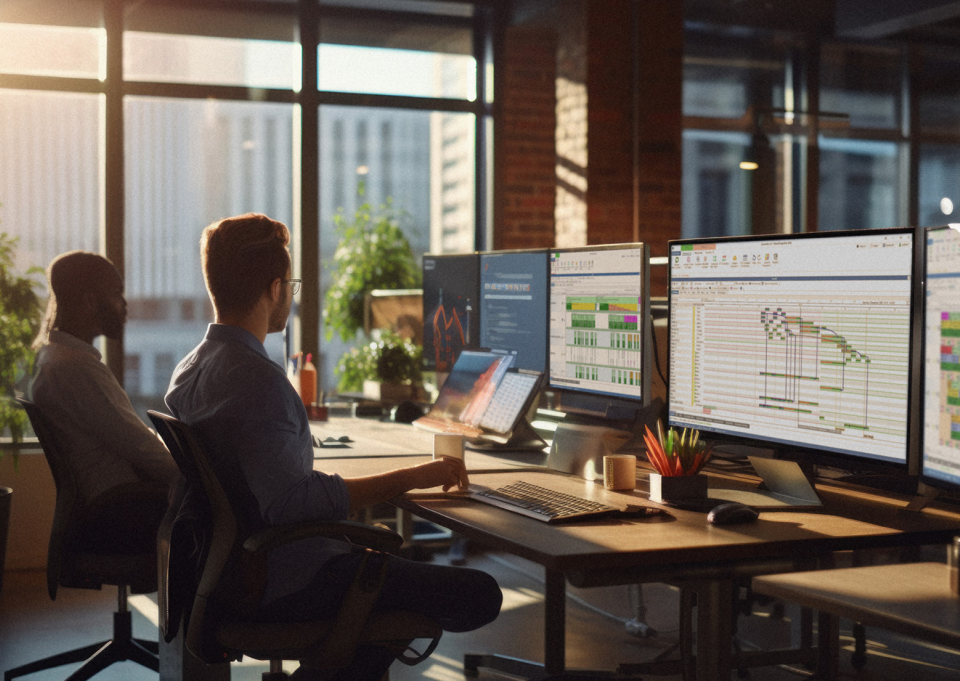
APS system in discrete manufacturing
Expand your knowledge of APS systems. Learn how to create effective plans and schedules that take into account the needs of discrete manufacturing.
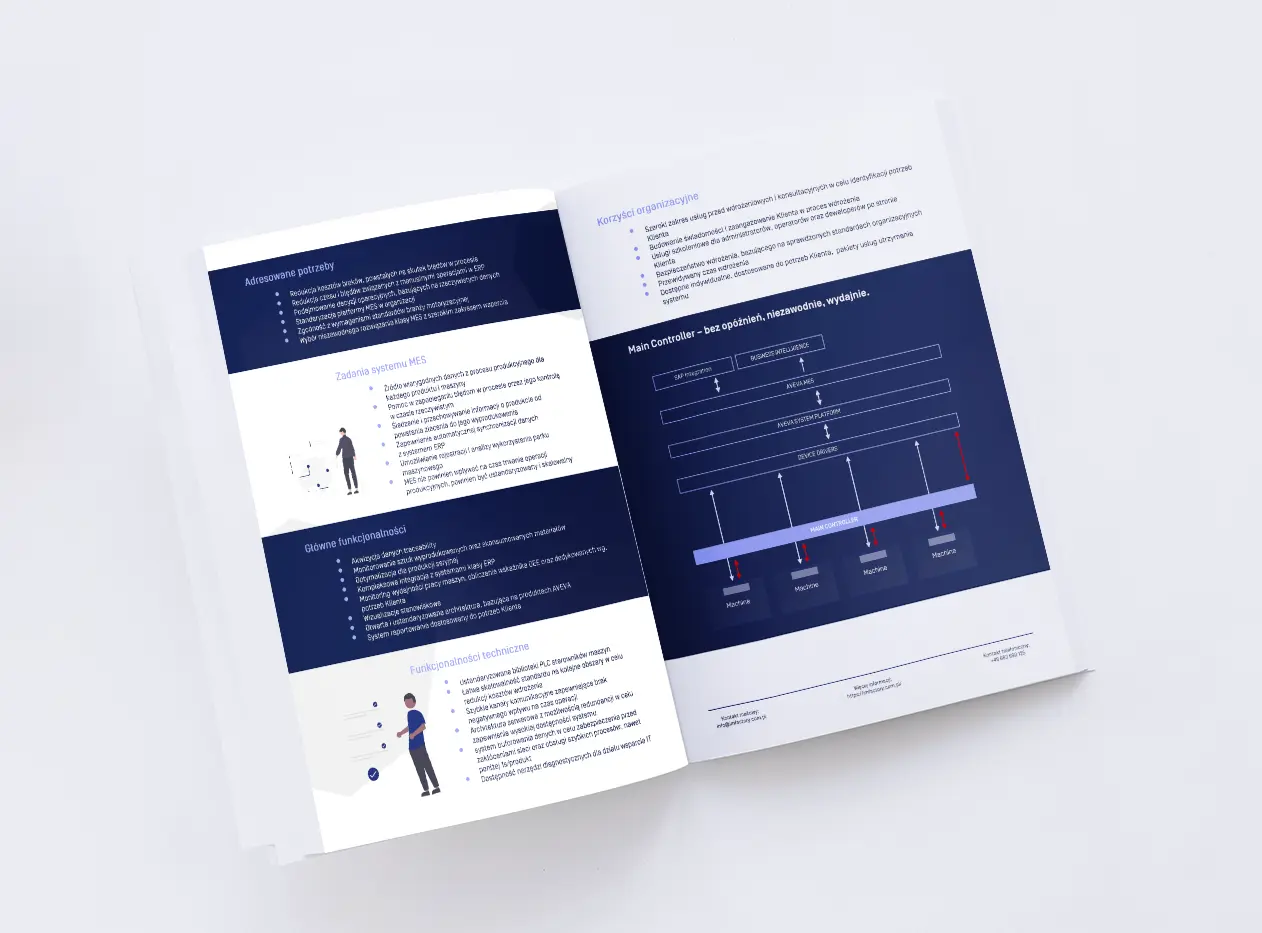
FAQ
MES and APS in discrete manufacturing – learn the answers to frequently asked questions.
MES (Manufacturing Execution System) is software that supports real-time manufacturing operations management. MES in discrete manufacturing helps improve efficiency, track processes, reduce waste, enhance product quality, and provide better production order control.
APS (Advanced Planning and Scheduling) enables advanced planning and scheduling. APS in discrete manufacturing brings such benefits as optimizing resource utilization, planning production based on material and machine availability, managing order deadlines, and predicting and minimizing delays.
MES focuses on real-time production monitoring and management, while APS is used for production planning and scheduling. MES provides current production data, while APS helps create optimal production plans.
Yes, integrating MES and APS creates an efficient production management solution. APS provides optimal plans, executed and monitored by MES. This cooperation ensures better production planning and execution, leading to higher efficiency and flexibility of production processes.
MES closely monitors each production stage, quickly identifying and correcting errors, maintaining high product quality, reducing waste, and eliminating quality issues. MES facilitates tracking and documenting all operations, which simplifies the auditing process and helps to meet quality requirements.
Challenges in implementing MES and APS include integration with existing ERP and IT systems, the need to train employees, managing organizational changes, and adapting the systems to the specific needs and processes of an enterprise. What is more, the implementation often involves high initial costs.
Best practices include conducting thorough analysis of the needs and production processes before implementation, choosing systems that fit the specific nature of the enterprise, engaging stakeholders in the implementation process, and providing suitable training to employees. You should also remember to implement the systems gradually, regularly monitor their functioning, and make necessary adjustments.
The business benefits of MES and APS in discrete manufacturing include increased production efficiency, better resource utilization, reduced operational costs, improved product quality, shorter order fulfillment times, and greater flexibility to market changes. As a result, the enterprise can increase competitiveness and achieve better financial results.
There are no universal principles to choosing the specific system for discrete manufacturing. Each company should be treated individually, based on a needs analysis and specific processes. You should also consider system scalability and compatibility with existing solutions. It is worth choosing a provider who offers not only a product but also implementation support and ongoing assistance.
Discrete processes are associated with various types of raw material preprocessing and element prefabrication. Therefore, companies in this sector typically use machinery such as CNC stations (numerical machines), saws, presses, rolling machines, milling machines, lathes (generally machining equipment), as well as assembly stations. Corresponding operations include cutting, stamping, rolling, milling, turning, machining, and assembly.
Check if Digital Transformation is the Answer to Your Company’s Needs

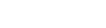
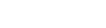
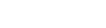
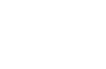
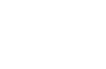
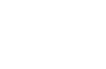
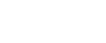
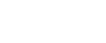
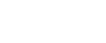
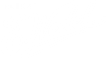
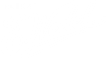
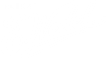
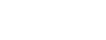
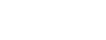
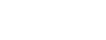






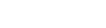
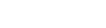
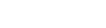
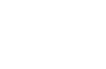
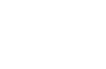
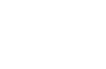
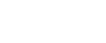
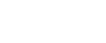
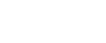
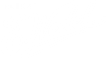
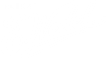
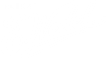
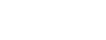
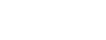
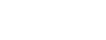






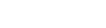
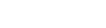
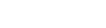
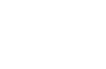
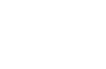
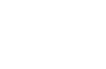
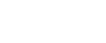
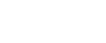
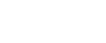
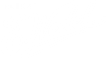
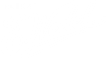
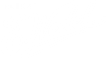
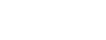
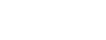
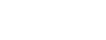






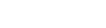
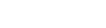
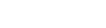
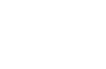
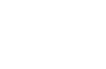
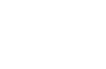
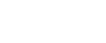
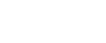
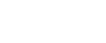
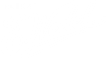
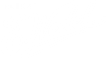
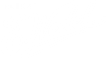
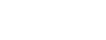
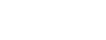
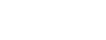


