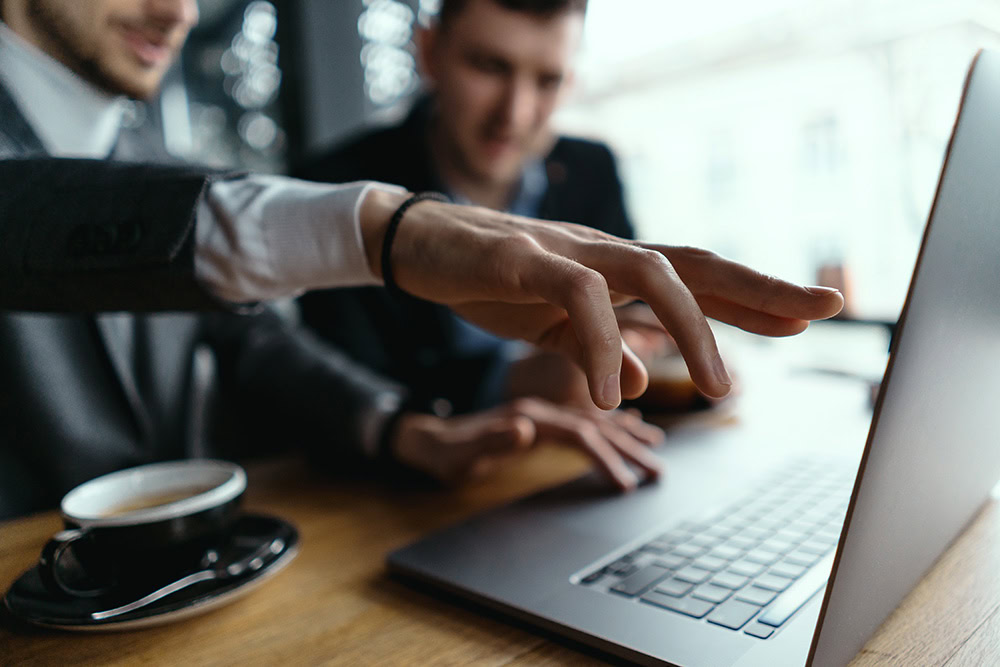
Advanced Planning and Scheduling (APS): Does Your Company Need It?
Effective planning significantly influences the success of any business, regardless of its size or industry. This holds particularly true for manufacturing companies daily facing numerous challenges such as material availability, changes in customer demands, and synchronizing the operations of various departments, lines, and machinery. Effective production planning and scheduling not only streamlines daily operations but also contributes to cost reduction, improved performance, and enhanced competitiveness of your company.
The Advanced Planning and Scheduling (APS) system is primarily used in manufacturing and logistics. Its main objective is to optimize production processes and efficiently manage resources to maximize productivity while minimizing costs.
An APS system can be seamlessly integrated with other systems for production management like Enterprise Resource Planning (ERP) and Manufacturing Execution Systems (MES) to collect information on customer orders, inventory levels, resource availability, manufacturing schedules, and other factors related to production planning.
By utilizing advanced planning algorithms, APS systems analyze the collected data and generate optimal production schedules, considering various factors such as resource availability, delivery deadlines, order priorities, time constraints, and other variables crucial to the effectiveness of our processes.
Additionally, APS systems facilitate simulations of various production scenarios and support decision-making by providing managers with analytical insights.
The implementation of APS offers numerous benefits to organizations, including:
- Agile response to change: APS facilitates swift response to changing market conditions, customer orders, and resource availability, enabling an enterprise to adjust production schedules in real-time, minimizing delays and deficiencies.
- Optimal resource management: APS ensures more effective resource utilization, including materials, machines, personnel, and others, through the process of meticulous planning. With this, excess and deficiencies can be avoided, leading to cost reduction and enhanced efficiency.
- Inventory optimization: APS is a great tool to optimize inventory levels through careful demand forecasting, factoring in delivery times, and keeping track of material flow in the production process. Thanks to this, excess inventory can be reduced along with associated costs.
- Improved production planning at various levels: APS enables users to plan production on the level of finished goods, semi-finished products, components, etc., facilitating supply chain optimization and process synchronization.
- Increased competitiveness: APS implementation impacts the competitive advantage of an enterprise by enhancing efficiency, increasing timeliness of deliveries, optimizing resources and inventory, and improving production planning. It enables companies to meet market demands more effectively.
- On-time deliveries: APS aids in ensuring timely order fulfilment by integrating provision of supplies with careful planning and scheduling, hence minimizing delays in processing customer orders.
- Enhanced production performance: APS is a perfect solution for optimized planning and scheduling, leading to higher efficiency of production processes. It takes account of factors such as resource availability, delivery times, customer demand, using them to generate optimal production schedules.
With various APS systems offered by numerous suppliers, selecting the most suitable one might seem complicated. Before choosing one solution, it is helpful to review user feedback and references to assess its real-world performance. However, the key factors to prioritize are the available functions and adaptability to your industry’s specific requirements.
Before starting the search for an APS system, it’s essential to define the goals you aim to achieve with its implementation. Conducting an audit of your current planning and scheduling processes can provide valuable insights into your company’s needs. This step helps to identify existing challenges and determine the functionalities that an APS must have to address them effectively.
Furthermore, when selecting an APS solution, it’s vital to consider your company’s future needs. The implemented system should be scalable so that it can grow with the whole enterprise. Another critical aspect is its seamless integrability with other systems such as ERP or MES.
Before finalizing your choice, it is advisable to consult APS solution experts who can assist in developing a comprehensive implementation plan, prepare your company for the transition, and organize necessary training sessions.
An APS system for production is an IT tool that offers invaluable support in planning, scheduling, and optimizing processes, leading to improved efficiency, cost reduction, and enhanced customer satisfaction. Investing in such a system can yield significant benefits as long as it is carefully planned and based on a thorough analysis of your company’s unique requirements.
See also
Want to learn more? Visit our Knowledge Base, where you'll find articles and webinars by experts to expand your knowledge.
Check if Digital Transformation is the Answer to Your Company's Needs
The Free Consultation Process:

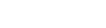
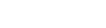
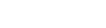
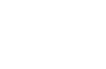
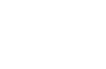
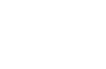
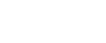
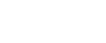
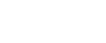
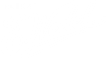
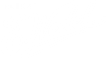
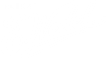
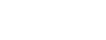
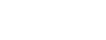
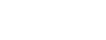






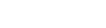
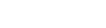
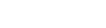
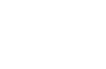
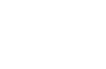
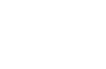
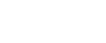
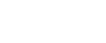
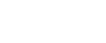
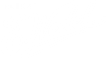
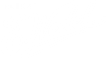
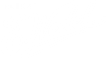
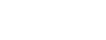
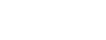
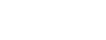






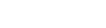
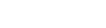
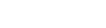
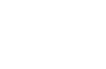
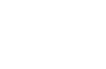
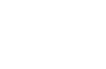
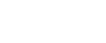
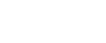
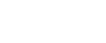
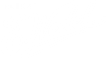
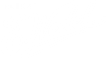
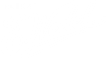
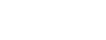
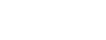
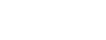






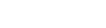
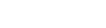
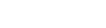
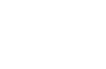
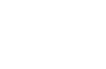
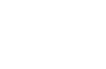
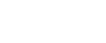
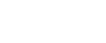
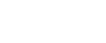
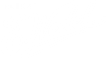
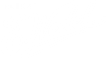
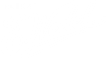
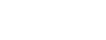
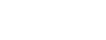
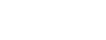


