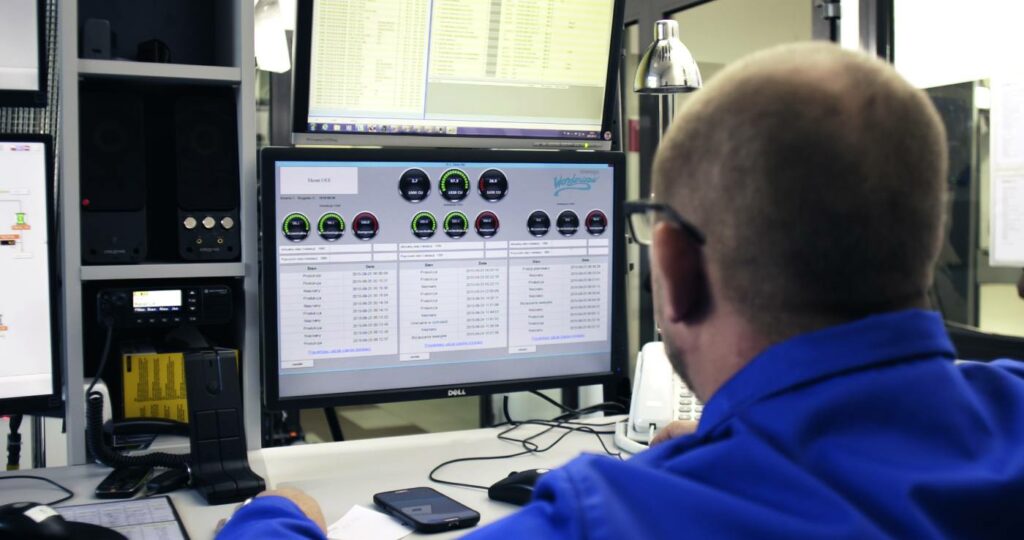
Effective MES Implementation in 5 Steps
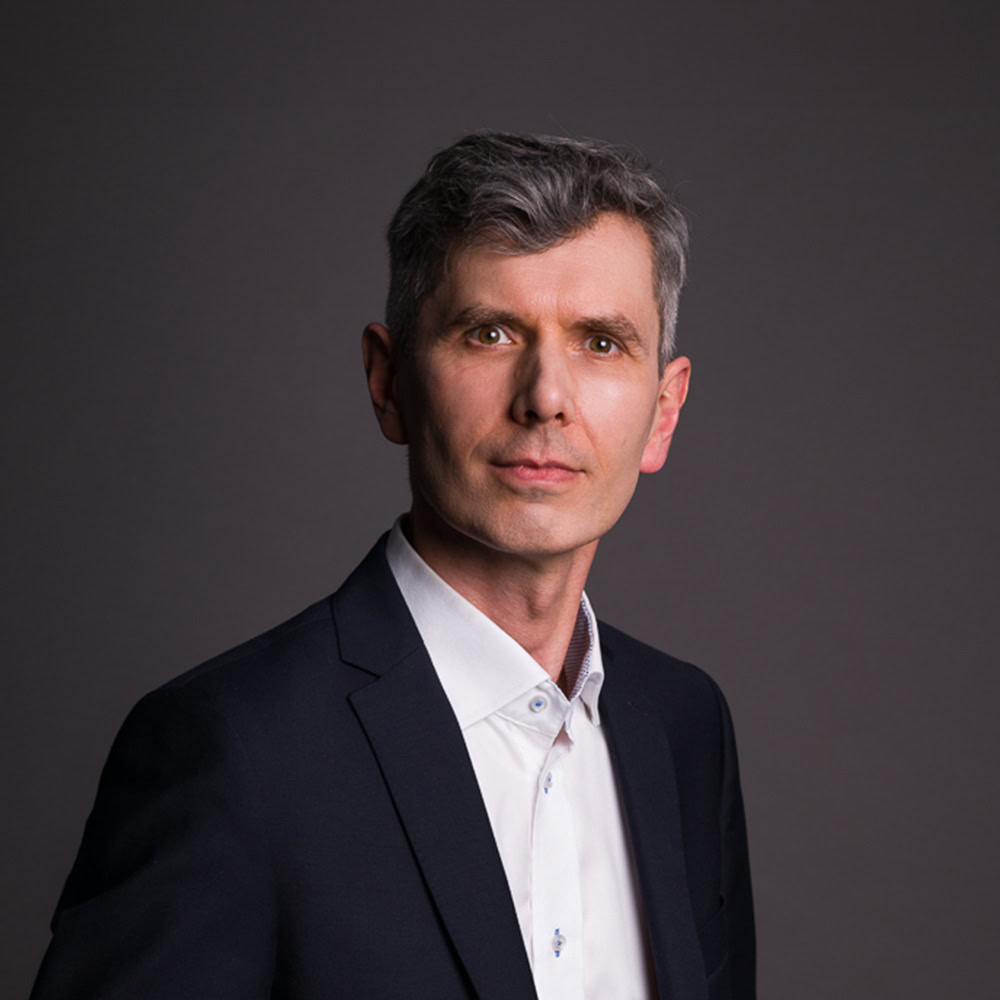
Jacek Daukszewicz
The decision to implement an MES isn’t solely driven by market conditions; it can also originate from within the organization, stemming from management directives or the ambition of the production improvement department. Regardless of the source of inspiration, the decision to introduce an MES is made. While the project may appear challenging and complex, with adequate preparation and competent execution, such concerns prove groundless.
Effectively and seamlessly, an MES can be implemented in enterprises of all sizes. This requires appropriate preparation for the implementation teams and users. Additionally, we must possess the knowledge to describe and streamline production processes in the company, while selecting the appropriate tools and implementation model. Proper planning is paramount to the project’s success.
Analyzing critical processes in each area of production reveals the following matters:
- the complexity of information flow,
- numerous data measurement and analysis points,
- the intricate flow of raw materials, semi-finished products, and finished goods in both production and warehouses.
The MES should reflect this complex structure. Naturally, this prompts the question: where should we begin, and how do we achieve our goals amidst various potential scenarios, considering the complexity and possibility of alternative initiatives, including the option to “do nothing”?
Fig. 1. Map of MES capabilities. Source: ImFactory, AVEVA MES Competence Center.
To address these questions, the first step requires developing a pre-implementation analysis, conducted by an implementation team consisting of competent end-customer representatives and the implementation company. The analysis includes the following:
- a professional assessment of the current state,
- recommendations for the future state,
- description of the requirements and critical goals of each stakeholder,
- the process of selecting a solution that meets the real needs of user groups,
- a plan for enhancing competencies in user teams,
- definition of the implementation model.
A thorough pre-implementation analysis helps articulate and communicate clearly defined and agreed-upon project objectives, thereby eliminating one of the main risk factors associated with MES projects.
Fig. 2. An exemplary MES implementation risk map highlighting key risks. Source: ImFactory, AVEVA MES Competence Center.
The pre-implementation analysis should commence with a well-prepared Roadmapwhich outlines the most general framework plan for the project. It should include an ambitious end goal, even if it’s to be achieved over the course of several years. The Roadmap defines a series of stages that must be completed successively to reach the final goal. Having a Roadmap facilitates a shared understanding of the system’s development vision. In essence, everyone involved knows where we currently stand, where we are going, and what path we must traverse.
Building on the overall plan, a detailed specification of each Roadmap stage is developed. This specification should verify the current state (description, inventory) and plan changes for individual levels (areas) of the production facilities, including:
- existing data sources in the process (sensors, PLC),
- visualization stations (HMI, SCADA),
- the level of production process management,
- information flow to superior (business) systems,
- and other relevant aspects.
The analysis should encompass all production areas, precisely defining the present state and desired outcomes after project completion. As a result, the analysis provides elements of the Roadmap that accurately identify the areas to be addressed at each implementation stage.
Successful MES implementation relies heavily on selecting an appropriate implementation model and employing a suitable project management methodology. While ensuring the required quality remains the most critical success criterion, the approach to achieving success may vary based on various factors. In practice, two popular methodologies are commonly used for professional MES implementations:
The first is the PRINCE2 project management methodology based on a cascade model of project implementation.
Fig. 3. Project stages in the cascade model. Source: ImFactory, AVEVA MES Competence Center.
This methodology is effective for both simple and complex processes. MES implementation projects following the PRINCE2 methodology and cascade model are successful when:
- the system specification is known,
- the completion date is specified,
- the project budget is specified and must not be exceeded.
The second common approach is Agile Project Management Methodologies.
Fig. 4. Agile project management. Source: ImFactory, AVEVA MES Competence Center.
This approach is utilized in the following scenarios:
- the scope of implementation is not definitively determined at the project’s commencement and may be modified during the implementation process,
- the completion date is not strictly defined,
- the budget is flexible.
For the success of any project, it is crucial to engage the right individuals from the very beginning of the preparation stage. Identifying and assembling the appropriate team members is of utmost importance, ensuring that no essential stakeholders are overlooked.
For instance, when applying the PRINCE2 methodology, , the central component of the standard Project Team is the Steering Committee, which can be regarded as the highest authority in the project. This committee holds responsibility for making key decisions concerning the project’s course.Consequently, it should represent the business objectives of all parties involved and include representatives from the end-customer management board (accountable for justifying the business case), implementation support personnel (such as representatives from the IT or automation departments), as well as the individuals that will be actual users of the planned solution (including the production director and lower-level line workers).
Internal teams are important
Building internal teams at the end-customer’s site is crucial. It is vital to emphasize that the successful MES implementation requires a strong collaborative effort between the integrator and the end-users, with the active participation of the latter. Building internal teams within the end-customer’s organization is absolutely necessary for the project’s success.
In the past, projects of this nature were solely executed “from the outside.” The client would order the system along with its installation and activation. The integrator would build, test, and launch the system, moving on to the next client right away. There were no proper project teams and the system users were not adequately involved in the design and implementation process. Consequently, without this involvement or appropriate handling, the system would eventually fade away, as it was not genuinely cared for or understood.
Fig. 5. Project management structure. Source: ImFactory, AVEVA MES Competence Center.
When selecting individuals to participate in the project, it is vital to ensure that they share a common vision of the project’s goals and possess an understanding of the anticipated end product. While competencies play a vital role, creating a positive and cohesive atmosphere within the team is equally essential. In simpler terms, having good “chemistry” among project participants is priceless in achieving success.
Development of competencies and the recommended training path
Indeed, mentioning awareness, it is essential to highlight that possessing the right knowledge is conducive to increasing awareness among all involved parties. At ImFactory, we actively transmit this knowledge to the end-customer throughout the entire implementation and system launch process. We follow the principle inspired by an old Chinese saying: “Tell me, and I forget. Teach me, and I may remember. Involve me, and I learn.” While presenting knowledge is important, active engagement is crucial (in accordance with Bloom’s taxonomy).
The specific path of training and workshops is custom-tailored to the scope and complexity of each project. Engagement is a multi-level and multi-stage process, involving various stages: from shaping the vision by the Project Team and defining requirements during the design stage by user representatives, through user testing, up to system stabilization, maintenance and final handover to the client.
Engineer 4.0 Competency Development Program™
effortlessly navigates at the intersection of two realms: the “digital” and the “physical.” Effective Industry 4.0 professionals must combine expertise in the specifics of the production process (such as working with robots or machine recalibrations) with IT skills – ranging from fundamental abilities (e.g., using spreadsheets and handling interfaces) to advanced proficiencies (e.g., programming and data analysis competencies). With the digitalization of the physical systems comprising the production line, Industry 4.0 technologies will necessitate even closer integration between the IT department and the operational department of a company. Programmers must thoroughly understand how and why production relies on IT solutions, and production operators should be conscious of how IT solutions impact the production process.
Consequently, there arises a need to expand qualifications beyond the employee’s core domain. As research by the ASTOR Academy shows, many engineers are already aware of this requirement. The interaction between IT developers and operators should be designed in a manner that ensures seamless execution of complex IT tasks – not only calling for close collaboration but also challenging existing decision-making hierarchies.
Fig. 6. Competency areas of an Industry 4.0 Engineer. Source: ImFactory, AVEVA MES Competence Center.
The work accomplished in the previous step paves the way for the next phase, which involves implementing the MES in production. It might seem like a straightforward and natural progression. Let’s review what we have achieved so far:
- a professional assessment of the current state and recommendations for the future state,
- preparation of a description of requirements and goals from key stakeholders,
- selection of a solution that meets the real needs of user groups,
- establishment of a competency development plan within user teams
- preparation of an implementation model along with several scenarios:
- implementing a new system for a single facility,
- piloting in a group of facilities and utilizing the experience gained,
- upgrading the current system or performing necessary updates.
However, the decision to initiate the implementation is not an easy one, primarily because it entails budget allocation and requires significant commitment from project participants. Nevertheless, it is essential to note that the more groundwork we lay in the first step, the easier the decision-making process for the second step and its subsequent implementation.
The planning and launch of an MES do not differ greatly from managing any other major project. We execute this process by using a selected methodology and based on a predefined scenario. Naturally, each project management methodology imposes specific rules of conduct.
A critical – if not the most important – aspect of the implementation is the Project Team. This team operates both within the enterprise as the end-customer of the system and within the implementing company. Other companies, such as necessary subcontractors, may be involved as well.
The ultimate success depends on the collaboration between these teams. Let’s revisit the primary areas covered by the MES:
- IT (integration with ERP, network, infrastructure),
- production processes (equipment, operators, technology, production management),
- warehouse and logistics (raw materials, semi-finished products, finished goods),
- automation and maintenance (machine control systems, metering),
- recipients of information at production, operational and management levels.
The principles of collaboration between the members of the Project Team, responsible for the aforementioned areas, should be defined during the project’s preparatory stage. The involvement of these individuals should be high-ranking (with necessary support from the management board) and included in the project schedule.
Fig. 7. An MES interface, source: Source: ImFactory, AVEVA MES Competence Center.
Therefore, we know which solution will help us achieve our goals, we have described the processes, prepared specifications, and identified success criteria. The following steps are:
- Appointment of an implementation team, preparation, and project initiation,
- Creating a schedule (for a given sprint, stage, or the entire project – depending on the chosen methodology).
- Setting up the development environment. This involves configuring the environment for the Project Team, which may include servers belonging to either the system integrator or the client. Usually, the IT teams are responsible for server installations.
- Creating templates based on the specifications (for a given sprint, stage, or the entire project – depending on the chosen methodology). The purpose of these templates is to prepare parts of the application for reusability.
- Implementing the application using the templates.
- Conducting tests in the development environment.
- Setting up the test and production environment. This includes installing servers in the production environment and preparing an Ethernet network with access to devices.
- Deploying the application in the test environment.
- Conducting tests in the test environment.
- Deploying the application in the production environment.
- Providing training for operators.
- Performing comprehensive testing and verification against success criteria.
- Handing over the application along with documentation.
At this point, some questions naturally arise. How can I implement all of this in my production facility? After all, every factory is different. My facility is unique and I work in a unique way. What impact does the industry in which I operate have on these processes?
This is where we return to the starting point – the first step of the pre-implementation analysis. It is at this stage that we must consider our uniqueness. Here, we determine the project’s functional scope and identify the requirements that arise from operating within a specific industry.
The project has been successfully completed, the system has been tested, launched, and… what comes next? Is that all? Well, not necessarily. Surprisingly, effective and efficient MES implementation doesn’t end with the project’s completion. The most crucial aspect is that it fulfills its objectives and brings tangible benefits. To achieve this, post-implementation actions are essential.
The necessity to develop the competencies of the individuals involved in the project applies not only to the initial two stages but even more significantly to the third stage. This is the moment when the system is operational, providing data, and enabling real-time production management. It is of utmost importance that the employees responsible for its operation possess the knowledge and skills necessary to effectively utilize the system’s capabilities.
Hence, the engagement of the expert team that was part of the entire project doesn’t conclude with the system’s deployment. Together with the client, we analyze data, provide assistance in decision-making, explore potential optimizations, and demonstrate how to draw accurate conclusions. Simultaneously, we ensure that this essential knowledge and expertise are transferred to the users. Thanks to this approach, a competent internal team is formed at the client’s end, becoming entirely self-reliant after a certain period.
A well-executed MES implementation brings significant financial, organizational, and environmental benefits, such as paper and energy savings. Moreover, it opens up further possibilities for digitizing processes within the facility. An excellent example of this is the successful implementation of AVEVA MES at DOVISTA Poland. A well-designed MES serves as a digital foundation, allowing the production organization to achieve additional business outcomes by integrating new modules.
Fig. 8. Benefits of MES implementation. Source: ImFactory, AVEVA MES Competence Center.
The companies with whom we have implemented projects and maintained long-standing partnerships consistently prioritize maintaining competencies within their MES/Improvement teams. They also emphasize continuous analysis and process improvement. This approach enables them to not only tackle new market challenges but also retain highly skilled specialists who are engaged in this area.
Author:
Jacek Daukszewicz
Jacek Dauszkiewicz is a graduate of Automation and Robotics from the Faculty of Mechanical Engineering at Gdańsk University of Technology.
With 20 years of experience in IT/OT systems for production, he played a pivotal role in ASTOR, where he was responsible for selecting solutions and handling technical aspects of Manufacturing Execution System implementation. He conducted economic analyses of automation investments and production management systems, assisted in developing the concepts of production management systems, and supervised projects in various Polish and international corporations. He participated in the creation of the ASTOR Group’s MES Competence Center.
Currently, he leads teams at ImFactory, coordinating projects related to the digital transformation of production and the broader scope of Industry 4.0.
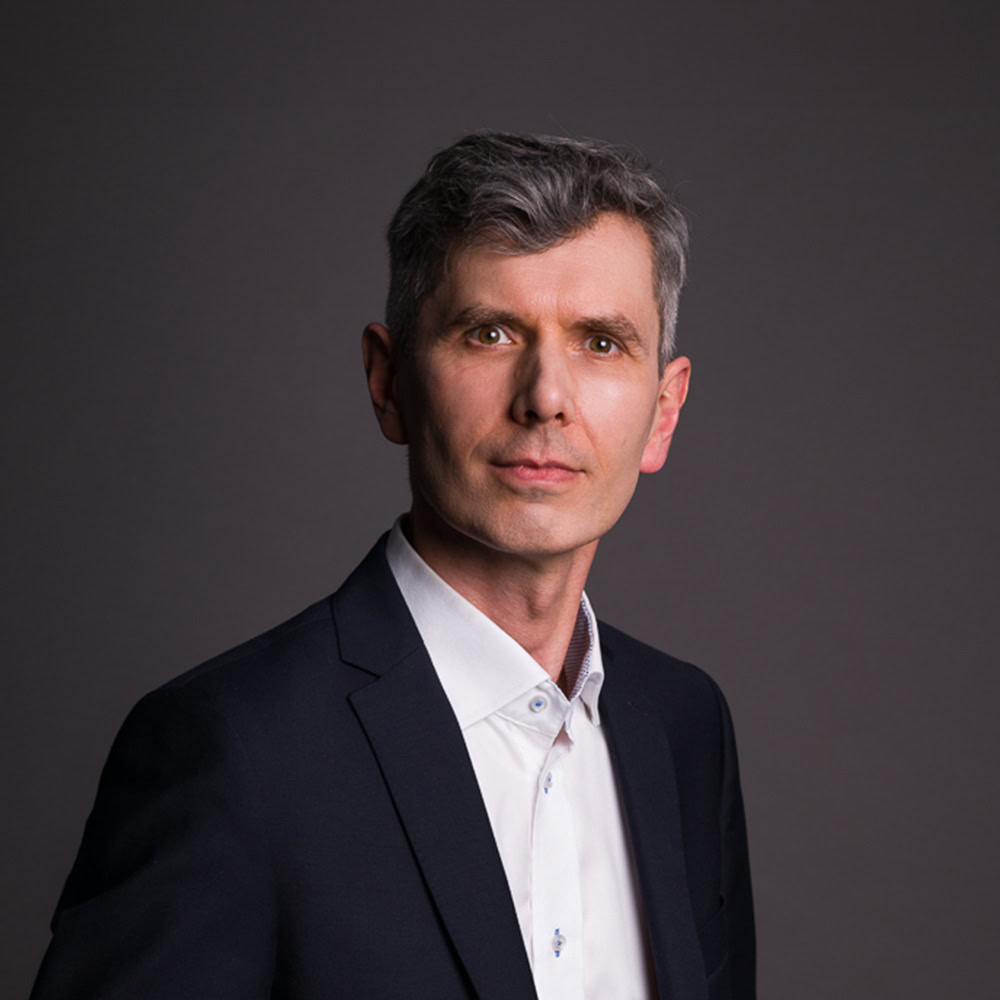
Jacek Daukszewicz is a graduate of Automatic Control and Robotics from the Faculty of Mechanical Engineering at Gdansk University of Technology. With over 20 years of experience, he specializes in IT/OT systems for manufacturing. During his time at ASTOR, he was responsible for selecting solutions and overseeing the technical aspects of implementing Manufacturing Execution Systems (MES). His responsibilities also included conducting economic analyses of investments in automation and manufacturing management solutions. Jacek actively contributed to the development of concepts for manufacturing management systems and supervised projects for Polish and international corporations. He participated in creating the MES Competence Center for the ASTOR Group. Currently, as part of the ImFactory team, he manages teams that coordinate digital transformation projects and the broader scope of Industry 4.0.
See also
Want to learn more? Visit our Knowledge Base, where you'll find articles and webinars by experts to expand your knowledge.
Check if Digital Transformation is the Answer to Your Company's Needs
The Free Consultation Process:

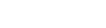
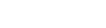
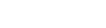
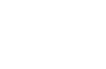
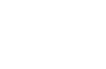
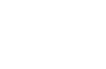
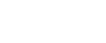
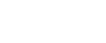
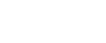
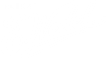
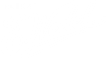
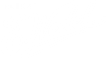
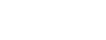
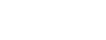
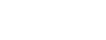






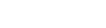
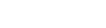
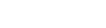
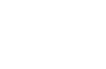
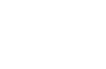
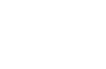
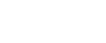
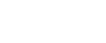
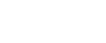
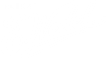
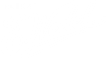
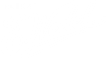
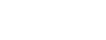
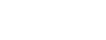
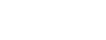






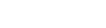
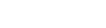
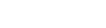
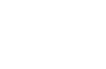
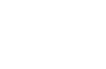
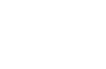
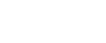
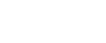
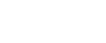
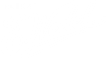
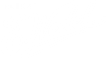
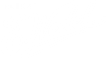
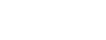
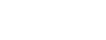
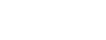






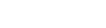
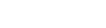
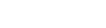
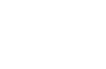
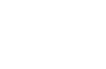
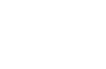
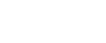
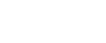
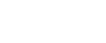
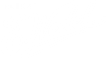
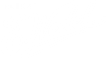
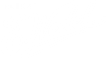
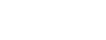
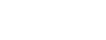
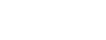


