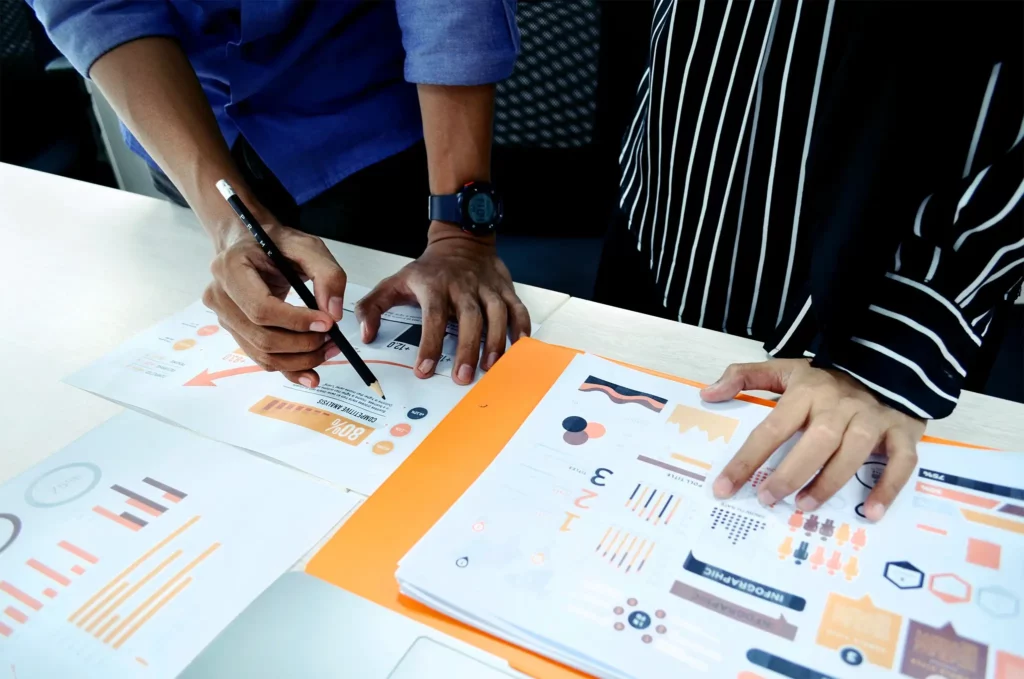
Is MES Profitable for Small Companies?
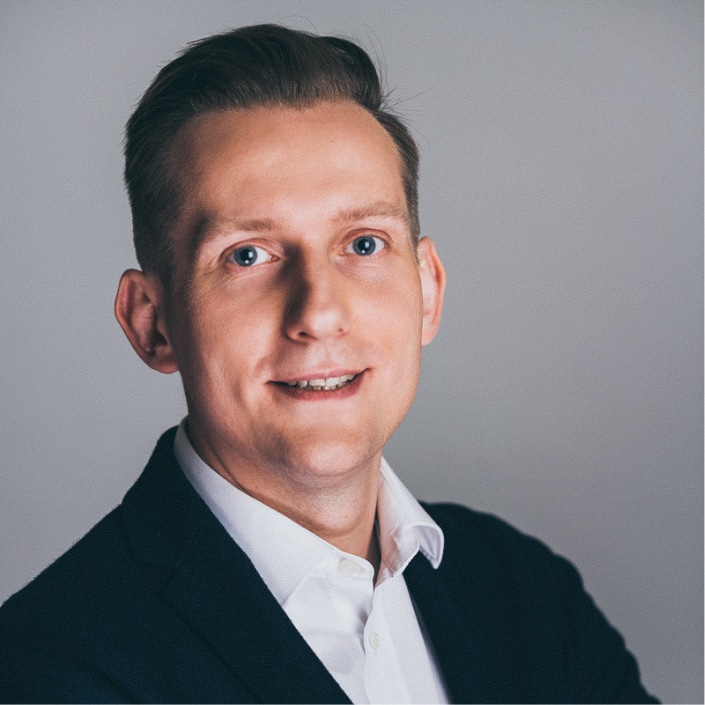
Paweł Firek
Manufacturing Execution Systems (MES) are among the most effective tools for manufacturing management. While these systems offer a wide range of functionalities beneficial to both manufacturing giants and small companies, they also mean significant investments and a long implementation process. Therefore, particularly small enterprises should carefully assess not only the benefits but also the challenges associated with the implementation.
MES is primarily used in the manufacturing industry to manage and optimize processes at the plant level. As one component of the broader category of manufacturing management systems, MES connects operational activities with enterprise management.
The system operates by collecting data from various stages of the manufacturing process, including materials consumed, operations performed on specific products, and changes made during production. Additionally, MES solutions facilitate real-time data analysis, aiding strategic and operational decision-making within the manufacturing plant.
Furthermore, MES can integrate with other systems such as Enterprise Resource Planning (ERP) and Supervisory Control and Data Acquisition (SCADA), making it possible to exchange data between systems and create a comprehensive source of information at both production and business levels.
Implementing MES in a small company can yield similar benefits to those seen in larger enterprises. These benefits include increased production efficiency, improved quality, tighter process control, better documentation, optimized inventory management, and cost reduction.
It is worth mentioning that the benefits of MES implementation may vary depending on the company’s industry and specific needs. Although introducing an MES requires adequate personnel preparation and workflow adjustment, it can contribute to the long-term competitiveness and stability of a small company in the market.
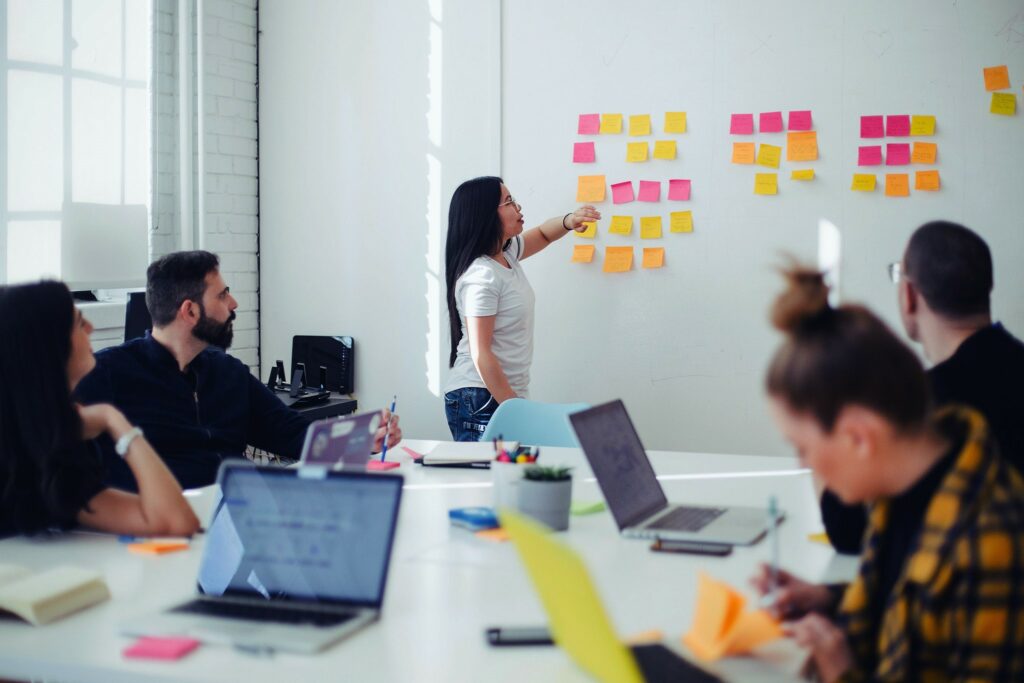
However, introducing an MES in a small company may present several challenges, including:
- Additional expenses: MES implementation can be expensive, covering software purchase, employee training, and adapting processes to the new system.
- Complex implementation process: Introducing an MES may require significant organizational and process changes, which can be more challenging for small companies with limited resources.
- Integration with existing software: Small companies often have pre-existing IT solutions that might need to be integrated with the MES, making the process difficult and time-consuming.
- Personnel training: Staff requires training in system operation and understanding its role in production processes.
- Employee resistance: Introducing the system may cause resistance from employees who are often wary of the change or perceive the system as unnecessary.
- Process standardization requirement: MES is based on manufacturing process standardization, which might pose a challenge for small companies accustomed to more flexible operations.
- Customization to specific needs: Some MES solutions are more universal and may not fully meet the unique requirements of small companies. Adjusting the system accordingly can be difficult and expensive.
- Maintenance and support: Post-implementation, the company must take care of regular maintenance and technical support, which requires additional resources.
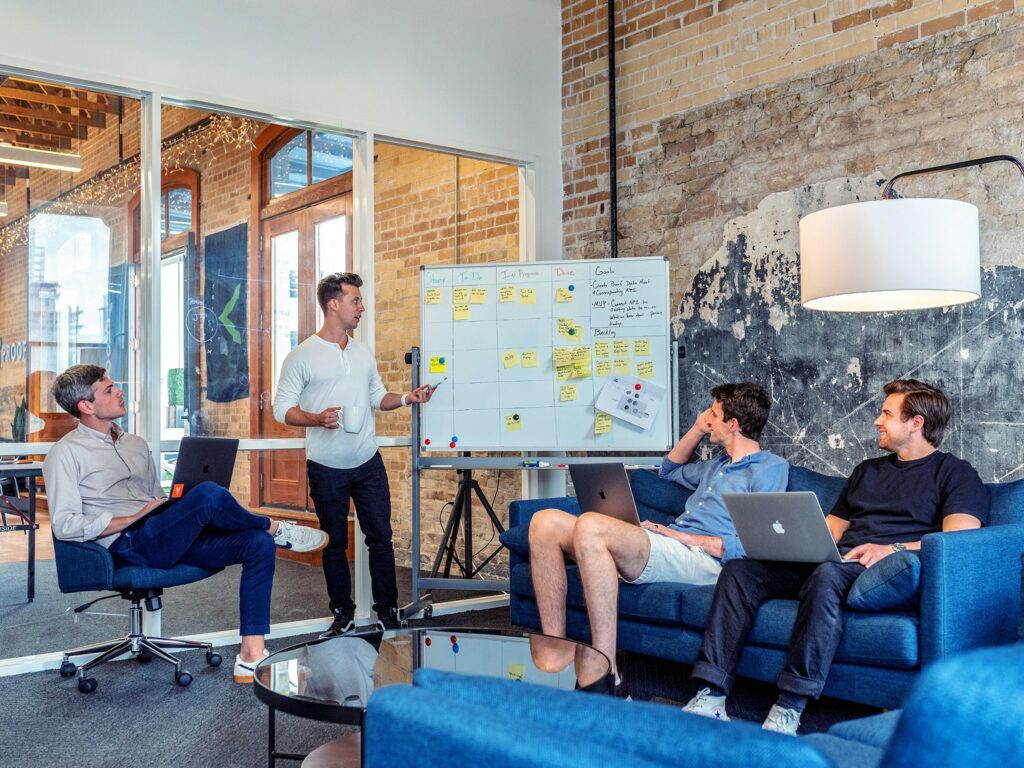
Should a small company invest in MES?
Does it make sense to invest in an MES solution? There is no universal answer, as the profitability of MES implementation in a small company depends on numerous factors. Before making the decision, consider the following points:
- Production scale: Implementation benefits may be less evident for companies with smaller-scale operations, while implementation costs remain significant.
- Complexity of manufacturing processes: MES implementation can be a great success for companies with complex production processes prone to errors, significantly improving process control and reducing the number of defective products.
- Expected benefits: You should analyze potential benefits of MES implementation such as efficiency improvement, cost reduction, product quality improvement, resource management optimization, and comprehensive data analysis.
- Implementation costs: MES implementation is often associated with investments in equipment, software, training, and adjustment period during which production can be disrupted. Such costs need to be included in the profitability assessment.
- System integration: It must be verified if the MES solution can be seamlessly integrated with existing systems like ERP and production automation systems.
- Long-term perspective: it is worth examining the implementation in the context of the company’s long-term growth plans. For enterprises planning to expand their operations, MES may turn out to be particularly profitable in the long run.
In conclusion, the profitability of implementing MES in a small company depends on various factors. While it can offer significant benefits for companies with complex manufacturing processes, a thorough analysis of costs and benefits is crucial before making a decision. Adequate preparation, planning, employee commitment, and stakeholder support are vital for successful implementation.
If you’d like to know more about MES implementation, feel free to reach out to us. We’re here to address all your questions and provide personalized assistance to help you choose the best solution for your company.
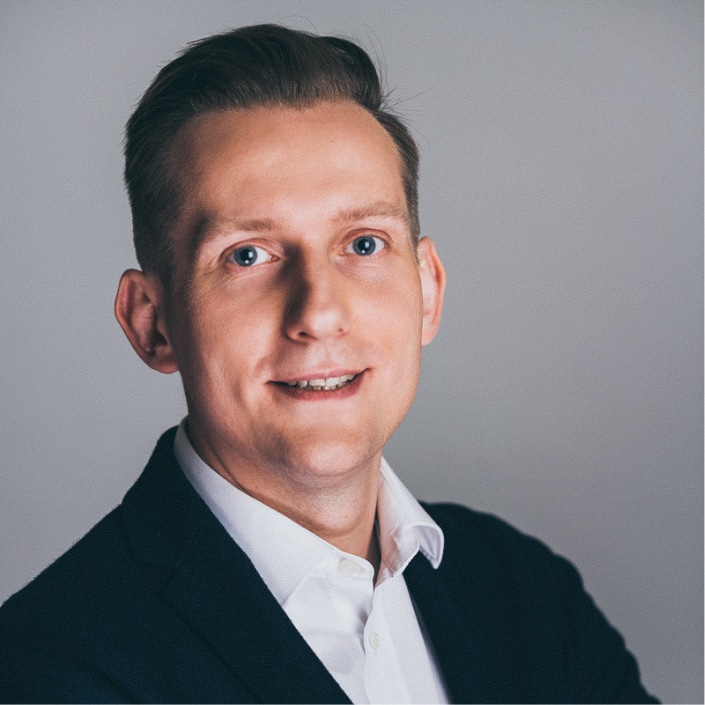
Paweł Firek is a graduate in Automatic Control and Robotics from Silesia University of Technology. With 15 years of experience in various aspects of industrial software, including technical, sales, marketing and development, he has collaborated with renowned global companies, such as ArcelorMittal Poland, Electrolux. Currently, his primary focus is supporting the Digital Transformation process in Polish manufacturing companies through Improvement Factory, while also contributing to the development of the MES market in Central and Eastern Europe as the AVEVA MES Competence Center.
See also
Want to learn more? Visit our Knowledge Base, where you'll find articles and webinars by experts to expand your knowledge.
Check if Digital Transformation is the Answer to Your Company's Needs
The Free Consultation Process:

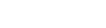
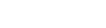
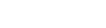
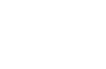
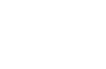
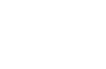
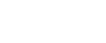
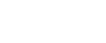
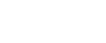
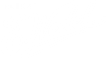
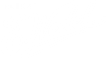
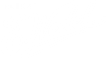
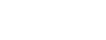
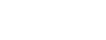
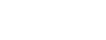






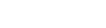
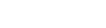
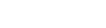
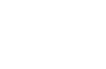
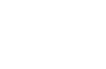
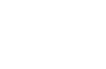
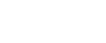
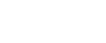
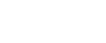
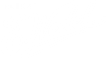
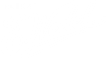
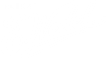
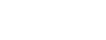
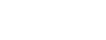
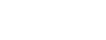






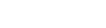
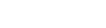
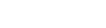
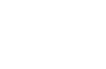
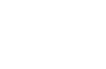
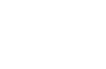
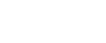
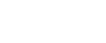
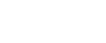
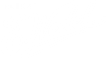
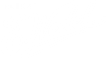
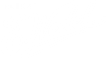
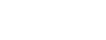
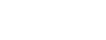
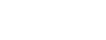






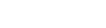
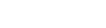
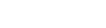
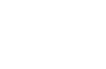
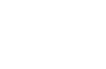
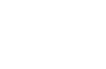
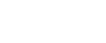
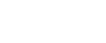
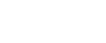
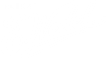
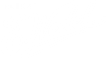
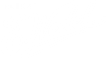
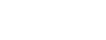
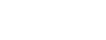
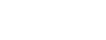


