Process Industry
Process manufacturing requires maintaining continuity, strict adherence to formulas and recipes, and thorough quality control. Specialized production systems such as MES and APS can provide significant support to manufacturers in this industry.
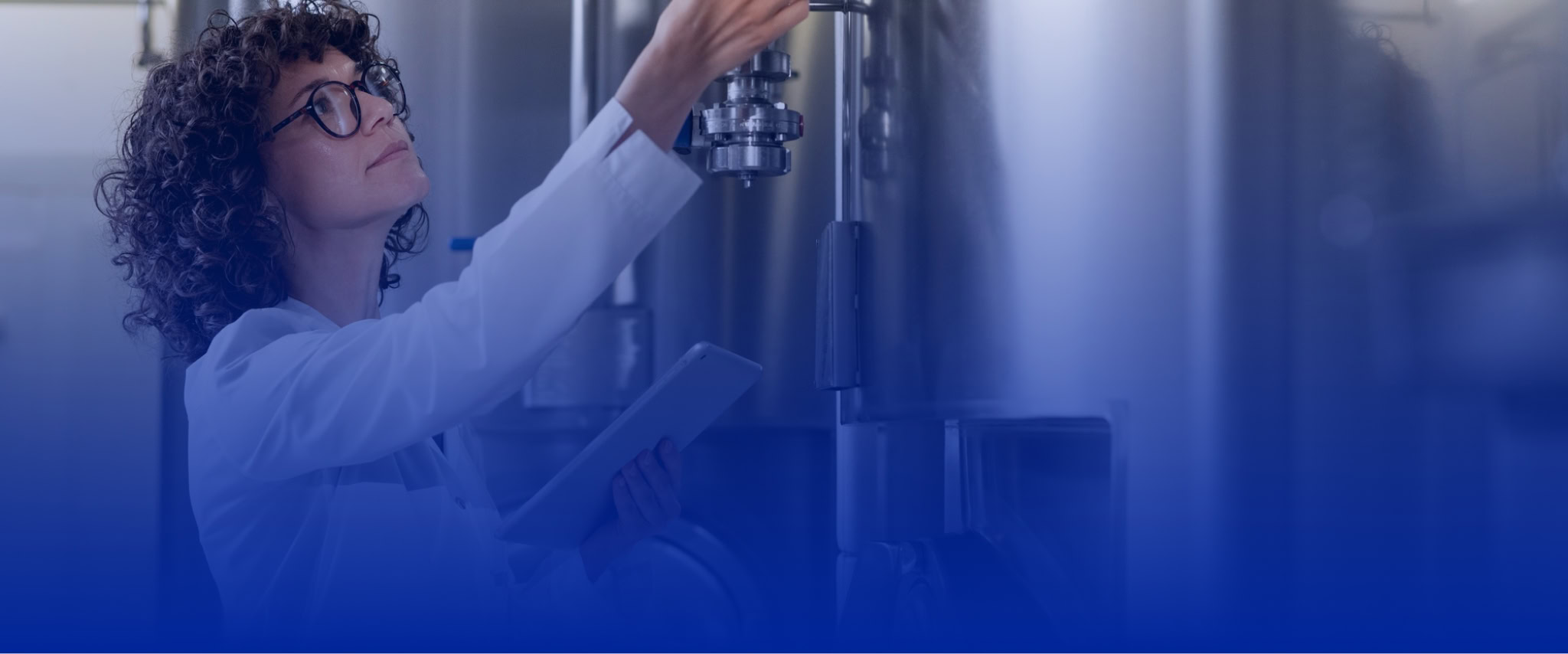
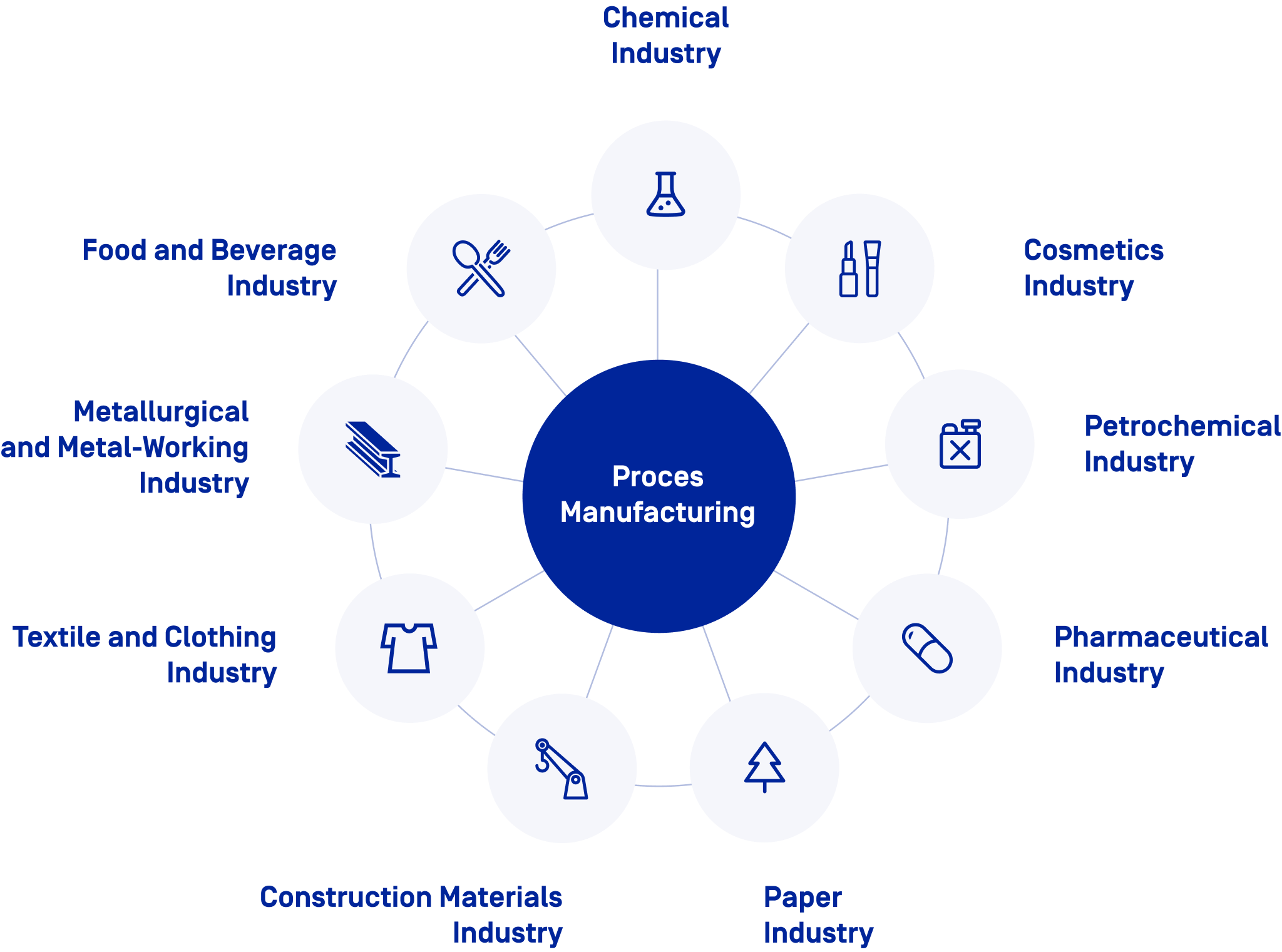
What Is Process Manufacturing?
Process manufacturing is one of the primary production methods, alongside discrete manufacturing. It involves transforming raw materials into finished products based on specific recipes and formulas. The production is organized into a series of interconnected processes, which closely influence one another. Typically, these processes are irreversible.
A defining feature of process manufacturing is that the materials that make up the final product cannot be separated or returned to their original state. While the product itself is mass-produced, it can be divided into smaller units which are then sold to the customer in predetermined quantities or capacities.
Process manufacturing can be divided into two categories: Batch Production, where products are manufactured in batches, based on the capacity of a container, mixing tank, or reactor, commonly seen in the food or cosmetics industries; and Continuous Production, which operates non-stop, on a 24/7/365 basis, as seen in the oil and gas industry.
Process manufacturing industries
Each of these industries requires precise process control and strict adherence to formulas and recipes for each batch, ensuring high quality of final products, enhanced efficiency, and minimal waste. To achieve these goals, process manufacturing often employs advanced technologies for automation, monitoring, and data analysis.
Greatest Challenges of Process Manufacturing and How to Tackle Them
See what the process industry’s biggest challenges are and how to deal with them.
Ensuring Process Continuity
Maintaining continuity is essential for efficient process manufacturing. Even in production involving multiple operations, their consistent progression in a strictly defined sequence is critical. Hence, any unplanned downtime is highly unfavorable, leading to financial losses and potentially causing serious issues related to quality or process safety.
- Manufacturing Execution Systems (MES) provide real-time feedback on the progress of each manufacturing stage, allowing for quick detection of abnormalities and facilitating an appropriate response, such as rescheduling in the APS system. This helps maintain operations within the just-in-time model.
- Advanced Planning and Scheduling (APS) systems support process continuity not only by rapidly generating alternative plans but also by preparing schedules with optimal sequences. For instance, in paint shops, scheduling lighter colors first (so that the jets can be washed only after using the darkest colors), or providing time for planned downtimes (for tasks like cleaning equipment) during post-production hours or at times that won’t disrupt production.
Compliance with Regulations
Numerous industries that utilize process manufacturing must adhere strictly to rigorous regulations and procedures, such as validation, Good Manufacturing Practices (GMP), or the FDA 21 CFR in the U.S.
- APS systems can retrieve equipment validation data from other systems (e.g., CMMS and EAM) and plan production using only approved resources.
- MES ensures complete traceability, tracking products at every stage of their creation, from raw materials to finished goods. It also gathers and stores detailed data on the entire process, including information on formulas, raw materials, machinery, operators, end parameters, providing full product genealogy insight.
Managing Process Complexity
Process manufacturing often involves numerous operations, some of which occur simultaneously, while others must follow a specific sequence or timeline. Perfect synchronization is critical, as a disruption in one process may trigger a domino effect, disturbing the subsequent stages and causing significant losses.
- Through automation, APS can create advanced plans and schedules that account for even the most complex sequences, adhering to various guidelines and restrictions. It also helps quickly identify the optimal plan.
- MES ensures full traceability, offering detailed real-time information about all manufacturing operations. This improves the coordination of complex processes and grants control over every aspect of production.
Strict Quality Control
In process manufacturing, even slight deviations in recipes, formulas, or process parameters may significantly impact the quality of a batch.
- Automated monitoring of all quality parameters with MES enables users to compare their compliance with recipes and Bills of Materials (BOMs), ensuring the correct batches of raw materials are used. Additionally, detailed batch reports, essential for quality control, can be prepared more easily.
- Precise production planning with APS secures time for quality testing in plans and schedules. Some quality tests, such as biological samples, require specific durations for evaluation. APS can incorporate these needs when scheduling the use of semi-finished products in subsequent stages.
Efficient Management of Raw Materials
The raw materials used in process manufacturing are often expensive and have defined expiration dates. While stockpiling excessive inventory is inefficient, the nature of process manufacturing makes it essential to avoid unexpected shortages. Proper BOM management is key to maintaining continuity, profitability, and product quality.
- APS systems enable users to create plans and schedules that account for available ingredients and ensure proper sequencing. They also provide support when certain materials are unavailable, quickly generating alternative plans using substitutes. Additionally, APS can aid the process of ordering raw materials by generating purchase lists that include delivery lead time.
- MES continuously monitors the usage of raw materials throughout the entire process. It checks batch suitability based on expiration dates and quality assessments of raw materials or semi-finished products, as even lower-quality materials can sometimes be used for less demanding products.
Response to Unforeseen Circumstances
Unpredictable events, such as equipment failures or ingredient shortages, can cause a serious disruption in process manufacturing.
- MES not only tracks every production stage in real time but also incorporates Statistical Process Control (SPC) mechanisms using digital Control Cards. This allows for rapid detection of irregularities, such as exceeding control limits, and corrective action before specification limits are breached. Thanks to this, the process is maintained within an optimal range.
- APS generates new plans and schedules within minutes, which proves particularly useful when a backup scenario needs to be created and implemented immediately to minimize disruptions.
MES system in process manufacturing
Expand your knowledge of MES systems. Learn practical functionalities that are a real support for process manufacturing.
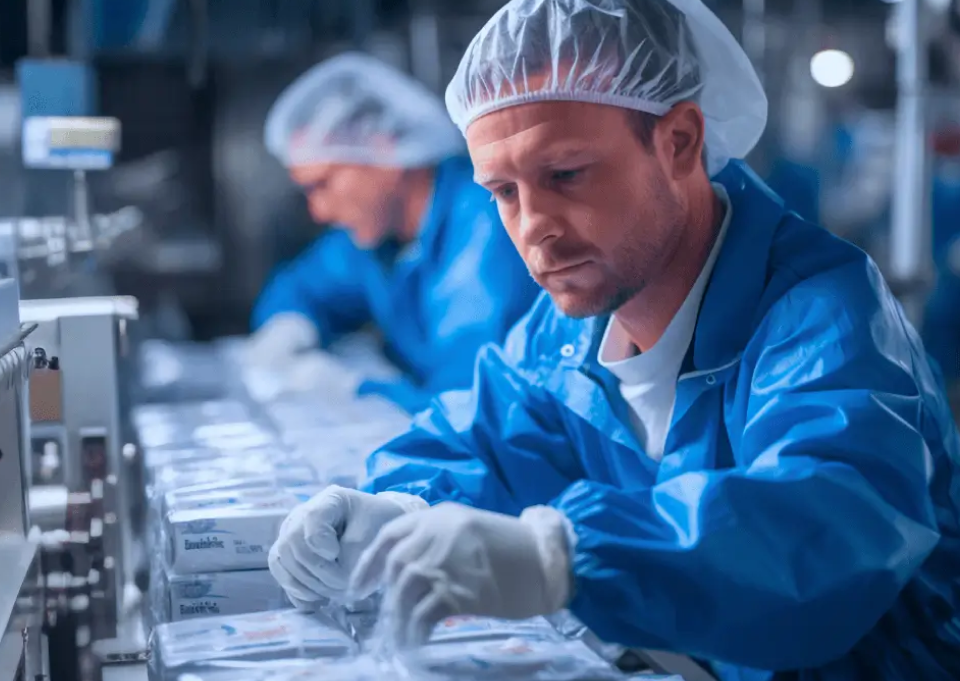
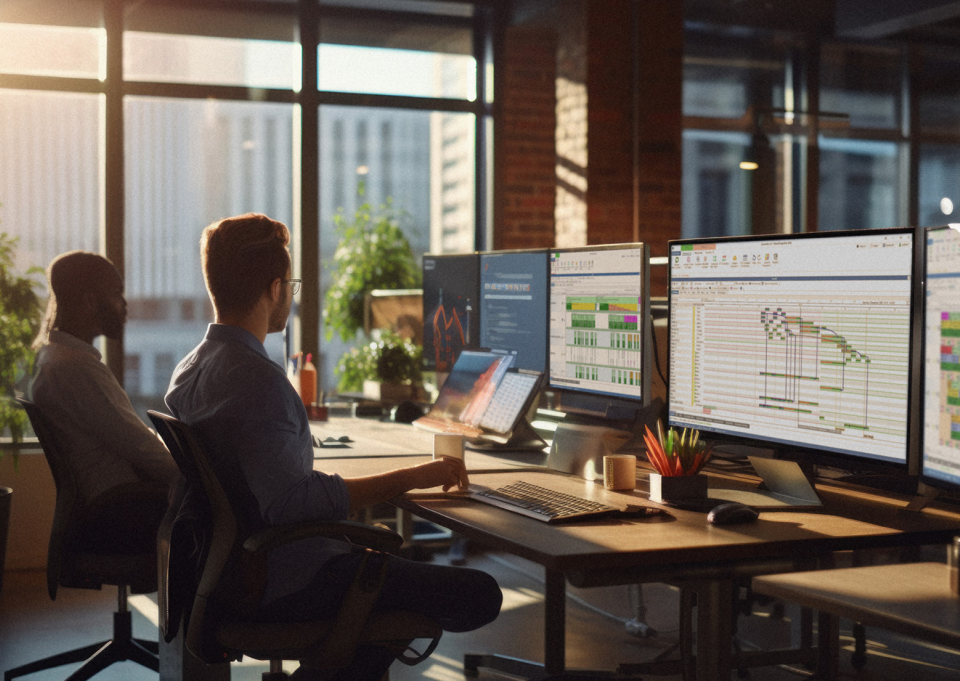
APS system in process manufacturing
Expand your knowledge of APS systems. Learn how to create effective plans and schedules that take into account the needs of process manufacturing.
Success Stories
Discover how businesses operating in process industry have benefited from implementing professional production support systems.
FAQ
MES and APS in discrete manufacturing – learn the answers to frequently asked questions.
A Manufacturing Execution System (MES) is software designed for real-time management and monitoring of production processes. In process manufacturing, MES facilitates precise tracking of production parameters, control over quality and compliance with Bills of Materials (BOM), recipe management, and route modeling. These features are crucial for maintaining process continuity, adhering with specifications, and meeting regulatory requirements.
APS (Advanced Planning and Scheduling) is a system designed to optimize resource utilization and streamline even the most complex production processes. In process manufacturing, APS helps arrange production schedules in a logical, fluent and efficient sequence. What is more, in case of unforeseen circumstances, APS helps minimize downtimes and improve production performance. It also supports batch-based production planning, considering the capacity of containers, mixing tanks, and reactors.
Integrating MES and APS allows for complete synchronization between manufacturing operations and optimized scheduling. This integration enhances responsiveness to changes, process optimization, waste reduction, and compliance with quality and regulatory standards.
MES solutions ensure real-time monitoring of manufacturing operations, with mechanisms like Statistical Process Control (SPC) and digital Control Cards to quickly identify deviations from quality standards. This allows for swift corrections, preventing the production of defective batches and ensuring compliance with quality requirements that are often incredibly strict.
Yes, APS systems support sustainability by creating optimal schedules. For example, careful task arrangement can reduce the number of cleanings, minimizing the use of water and chemicals. Moreover, the most energy-intensive tasks can be planned during periods of highest renewable energy availability. Additionally, APS promotes paperless operation, eliminating paper plans and schedules. These features help minimize the negative impact of manufacturing on the environment, aiding companies in achieving sustainability goals while optimizing their processes with APS solutions.
MES solutions ensure detailed documentation of every production stage, which is critical for auditing and regulatory compliance. For example, pharmaceutical production requires validation to confirm that each stage of production leads to obtaining a final product of the intended quality. Also, industries like pharmaceuticals, cosmetics, and food must follow Good Manufacturing Practices (GMP), which cover not only manufacturing but also product testing. Other regulations, such as the American Code of Federal Regulations for Food and Drugs (FDA 21 CFR), govern the production and distribution of food, drugs, cosmetics, and medical products. Through comprehensive and detailed planning, APS also supports process manufacturers in meeting these requirements.
MES and APS systems help tackle challenges such as maintaining process continuity, optimizing raw material use, quality control, managing process complexity, and meeting regulatory standards. With the help of these systems, companies can improve efficiency, safety, and quality management in process manufacturing.
Implementing MES and APS can be challenging, especially in complex manufacturing environments. It requires careful process analysis, collaboration with experienced implementation partners, and a well-structured implementation plan. However, the long-term benefits of implementation outweigh the initial challenges.
The key factors in successful digitalization of process manufacturing include proper team preparation, clear definition of business objectives, thorough analysis of production processes, and close cooperation with experienced implementation specialists. Active involvement from all stakeholders and continuous progress monitoring are also essential for the success of this endeavor.
Check if Digital Transformation is the Answer to Your Company’s Needs

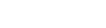
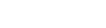
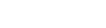
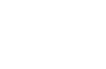
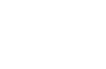
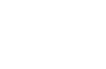
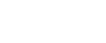
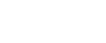
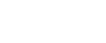
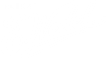
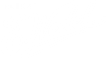
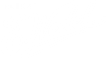
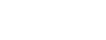
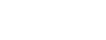
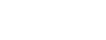






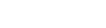
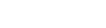
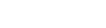
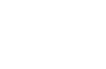
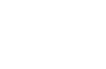
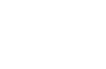
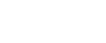
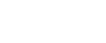
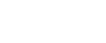
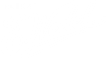
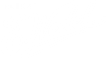
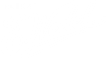
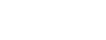
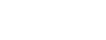
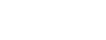






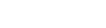
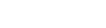
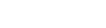
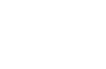
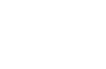
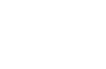
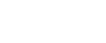
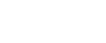
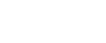
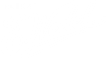
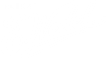
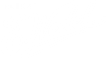
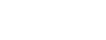
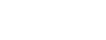
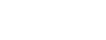






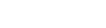
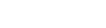
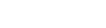
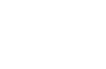
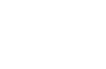
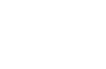
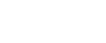
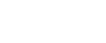
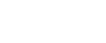
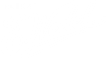
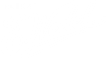
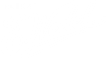
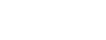
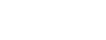
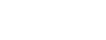


