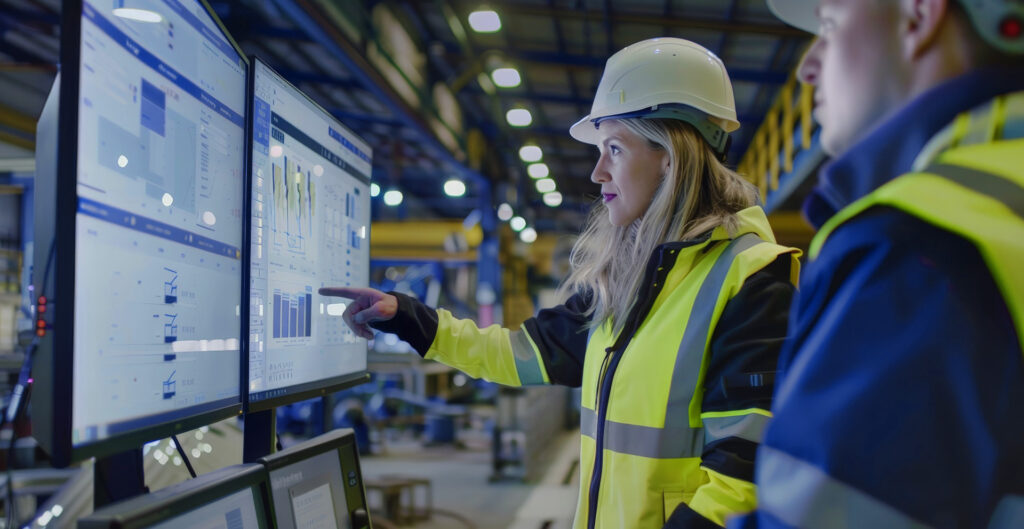
Production Planning and Scheduling in the Food, Pharmaceutical, Cosmetic, and Chemical Industries. Specifics and Challenges.
The industries in question are characterized by the fact that their production processes are clearly divided into two parts – the first involves operating on batches of products, which can be liquid, semi-liquid, free-flowing or in the form of mass. The second part of the process is the packaging of the finished products into individual and bulk packages.
In many respects, scheduling issues in these industries are similar to other industries – after all, the idea is to make sure that the products are made on time and raw material purchases as well as intermediate production are properly coordinated. In any company, it is also necessary to bear in mind that production capacity is not infinite, and that individual products must be produced on the right equipment.
However, the technology, especially regarding batch production, as well as the nature of raw materials and finished products, bring unique challenges to planning and scheduling in the industries in question. Let’s discuss the most important ones.
The equipment on hand and the time available to complete a given order are two extremely important aspects. Without taking them into account, it is impossible to successfully plan the execution of any order. Let’s analyze this with an example.
Suppose we have one large mixer with a capacity of 1,000 liters and three small ones, 300 liters each. They can all handle the same type of material. The small mixers finish their work in 45 minutes, while the large one takes 1 hour. The order we have to complete involves a batch of 900 liters. In which mixer should it be prepared?
It would seem logical to complete small orders in small mixers and large orders in large mixers. However, is this always the best option? Not necessarily. It should be considered what the priority is at a specific moment. It could be time, but also, for example, the availability of particular mixers at a given time. We have to keep in mind that once the mixing process has started, it cannot be stopped, so it must be scheduled in the way that the whole process ends at the right moment.
In the above example, in a large mixer, the whole order will be ready after one hour. If we decide to use small mixers and run them all in parallel, the whole batch will be prepared faster – in as quickly as 45 minutes. However, if we use only one small mixer to execute the entire order, then the batch will be ready after 2 hrs 15 mins, but the remaining mixers will be available for other orders.
In batch production, the transfer of raw materials and semi-finished products between operations is often carried out using direct transport equipment without manual intervention. Therefore, it is vital to consider the dependencies between machines when setting schedules.
For example, a semi-finished product may be stored in a tank that directly supplies many other machines. Since the flow of material is direct, second-stage equipment (e.g., packaging lines) is limited to using the same semi-finished product (i.e., currently in the tank) in production at all points in time. Therefore, these machines should only be assigned orders that use the same semi-finished product.
In a more complex version, material can flow directly from one unit to the others continuously. That is, the semi-finished product formed at the first stage is continuously passed on to the next stage. For example, one machine continuously prepares the stuffing by grinding and mixing the proper ingredients, and at the same time passes on this stuffing to several machines that form dumplings.
During scheduling, it should be taken into account that dumpling-forming machines may start working either simultaneously or at different times. They may also not work all at once or work each at a different pace. For the plan to be feasible in this case, it is important to verify the cumulative values of production and material consumption over time. That is, in practice, it should be planned to prepare enough stuffing to supply the dumpling-forming machines at the right time.
A vital aspect related to product safety and quality is avoiding cross-contamination, that is, the transfer of certain substances from one product to another. This should be thought of as early as the planning and scheduling stage. What should be taken into account?
In some production facilities, certain machines are designed to handle specific products such as those containing an allergen. It is important to assign orders for such products only to the allowed machines already at the scheduling stage. However, it often happens that the same machine manufactures different products. The risk of cross-contamination can then be minimized by appropriately setting individual sequences – for example, so that products that do not contain a certain substance (allergen) are launched at the beginning of the week, and products containing it at the end. In the meantime, the two types of production are separated by an appropriate cleaning operation.
Sometimes multiple product processing lines are located in the same room or area. In those cases, there is a risk of transferring substances between lines by workers or even through the air. When planning such production, it may be necessary to avoid the simultaneous processing of incompatible products – for example, allergenic and non-allergenic products which, although on different lines, are still in the same area.
Another aspect to include in production schedules is equipment cleaning. It is necessary not only because of cross-contamination, but also to maintain hygienic conditions and product quality.
However, we must keep in mind that cleaning takes up time that could be spent on production. Therefore, the optimal solution is to schedule necessary cleaning during non-production hours, such as weekends or other dedicated periods. Depending on your needs, you can schedule minor cleanings during production hours and longer ones outside of those hours.
Another relevant factor is the degree of incompatibility of individual products, which determines the need to spend more or less time on cleaning. Grouping compatible tasks and arranging their sequences accordingly can minimize the number of cleanings and reduce their duration, thus maximizing production efficiency.
In the discussed industries, production often requires a wide range of ingredients – both raw materials and semi-finished products. Ensuring their availability at the right time is a critical and difficult task, especially given the complexity of supply chains and the volatility of market availability. In addition, many ingredients have limited durability or require special storage conditions, further complicating inventory management.
All of these factors mean that managing material availability requires constant monitoring, flexibility, and rapid response to changing conditions. It is necessary to generate the right material requirements well in advance, and to respond quickly in the event of supply delays: when possible, by introducing acceptable substitutes for raw materials to meet lead times confirmed to customers, or by resequencing orders to avoid costly production downtime.
This requires a new version of the schedule, taking into account the current supply situation, to be quickly generated, which in the worst-case scenario will at least provide the opportunity to inform the company’s contractors of potential supply delays and allow them to prepare – something they will certainly appreciate.
Raw materials and semi-finished products used for production in the food, pharmaceutical, cosmetic, and chemical industries must be stored in appropriate conditions. They not only require adequate storage space, as is the case in other industries. In addition, appropriate storage containers as well as time constraints must be considered.
For the sake of the quality of manufactured products and, in particular, their safety, it is absolutely necessary to observe the expiration dates of raw materials or semi-finished products. On the one hand, it is necessary to plan the retrieval of materials for production in the right order, e.g., “older” first (to prevent waste as a result of waiting too long for further processing), and on the other hand, to effectively block their inclusion in the schedule after exceeding the so-called shelf-life, specified for each type of material.
Moreover, the same is true of finished goods – many of them cannot wait too long to be shipped, as they could then reach the end user after their shelf-life has already expired.
As you can see, there are many dependencies and constraints that must be taken into account in the scheduling process in the discussed industries. The presented examples are not an exhaustive list, and in addition to the mentioned constraints, there are large amounts of other data related to production resources or the products themselves that must also be considered in scheduling.
Why do production schedules most often fail during their implementation in production? The problem often lies in the lack of appropriate tools to prepare the schedule based on all the necessary criteria. Initial production plans are often created in ERP systems. While they are very useful in the preliminary assessment of material requirements or production resources, they are not accurate enough to constitute a plan for daily work. Thus, it is needed to translate them into detailed production schedules – planners most often have only spreadsheets for this purpose, which, despite many efforts, is the source of many missed opportunities in the effective use of the company’s production resources.
A schedule created with spreadsheets, even very simplified, takes a long time to form, up to several days. Moreover, because of these simplifications, it is most often not optimized to avoid inefficiencies or to target specific and evolving operational or business goals.
The subject was covered in detail during our webinar: Production Scheduling as a Tool to Improve a Company’s Profitability.
The result? Such a schedule is not only suboptimal but often infeasible already at the moment of publication, regardless of the type of manufactured products. And in the industries like cosmetics, pharmaceutical, chemical, and food, this method of scheduling may also deteriorate the safety and quality of products due to cross contamination or exceeding expiration date.
The answer to the complex issues of preparing schedules in the cosmetic, pharmaceutical, chemical, and food industries are APS systems. These are modern tools that allow automatic inclusion of the required dependencies and constraints, even very complex ones. Most importantly, this translates into the feasibility of the schedule, but it also has a significant impact on product safety.
APS systems most often greatly enhance the speed of operation. In minutes and sometimes even seconds, they are capable of generating and continuously changing schedules that consist of thousands or tens of thousands of production operations. This is a huge improvement in demanding industries that focus on batch production and its packaging.
APS systems provide a number of algorithms and optimization criteria to consider even very complex dependencies that are characteristic of production in the cosmetic, pharmaceutical, chemical, and food industries. These systems enable, among other things:
- Assigning specific machines to certain products requiring special conditions (e.g., those containing allergens).
- Configuring production sequences to minimize the risk of substance transfer between products (e.g., scheduling compatible production runs on a single line).
- Scheduling the manufacturing of products close to their demand dates (e.g., defining maximum delays between operations).
- Taking into account different cleaning and machine changeover times depending on the degree of product incompatibility, and scheduling these processes during non-production hours.
- Grouping production orders into sequences that minimize the number of cleanings and changeovers.
- Accounting for differences in processing times on different machines, making schedules realistic and feasible.
For more detailed information on APS and the functionalities that support production planning and scheduling, click HERE.
Production planning and scheduling in the food, pharmaceutical, cosmetics, and chemical industries is an extremely complex task that requires consideration of specific challenges: process time and continuity management, avoidance of cross-contamination, or raw material availability. Traditional methods based on ERP systems and spreadsheets often prove insufficient here. The solution to the complex needs in this area are APS systems which create detailed schedules based on advanced algorithms. And this is extremely important, because the more accurately the schedule reflects the company’s reality, the more the prepared plan will be tailored to production capabilities, and the more effectively such a schedule will plan effects and avoid inefficiencies.
This article is based on the webinar: Applying APS to Scheduling in the Food, Pharmaceutical, Cosmetics, and Chemical Industries.
For more on process manufacturing, of which batch production is a part, and tools to help improve it, click HERE.
See also
Want to learn more? Visit our Knowledge Base, where you'll find articles and webinars by experts to expand your knowledge.
Check if Digital Transformation is the Answer to Your Company's Needs

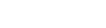
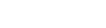
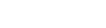
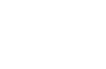
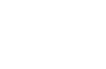
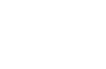
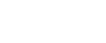
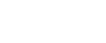
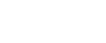
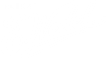
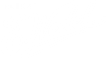
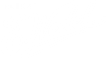
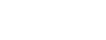
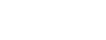
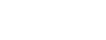






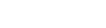
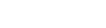
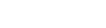
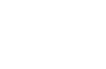
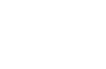
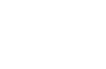
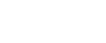
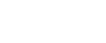
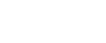
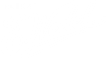
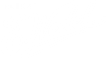
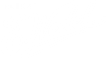
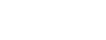
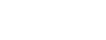
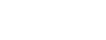






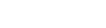
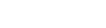
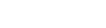
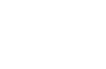
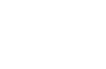
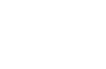
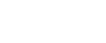
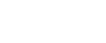
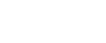
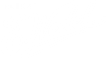
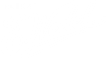
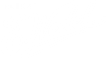
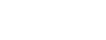
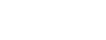
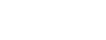






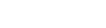
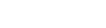
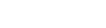
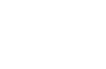
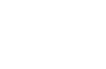
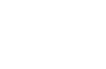
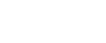
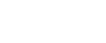
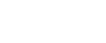
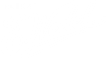
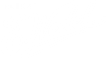
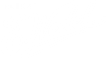
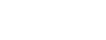
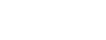
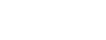


