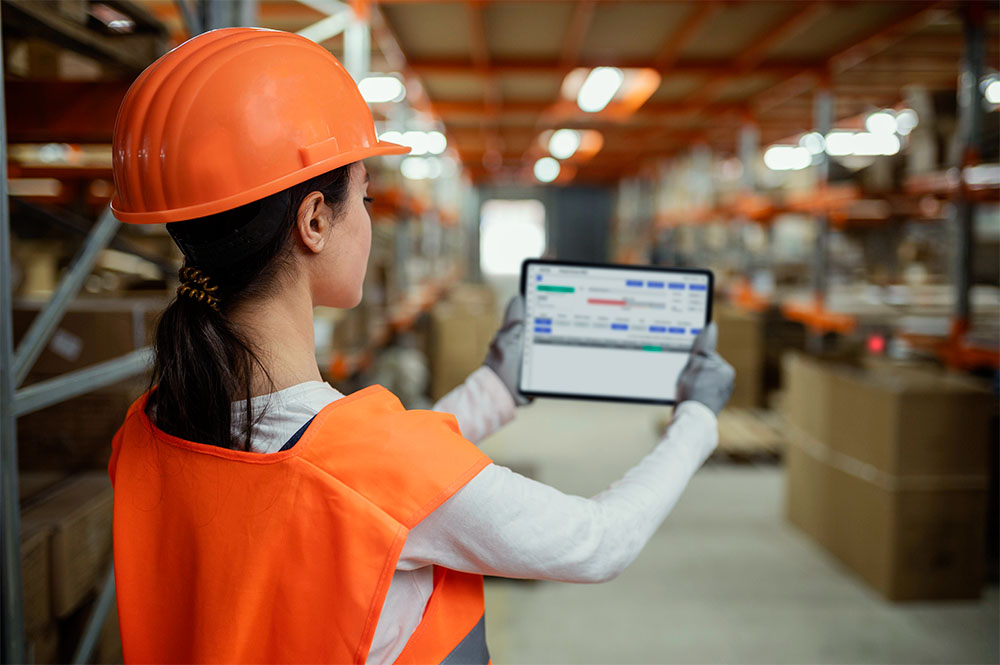
Production support systems and their role
Nowadays, companies operating in the manufacturing industry have a variety of modern tools and technologies to choose from to help them effectively manage and control their company’s processes. These can cover various areas, such as inventory management, production planning, quality tracking, process automation or performance monitoring. Let’s take a look at the most popular production support systems and see which needs of the companies they are addressing.
The basic system for streamlining work in production, which allows to collect data from machines, present it in the form of visualizations, as well as alert if critical parameters are exceeded, is the SCADA system. In this article, however, we will focus on systems from higher levels – ERP, MES and APS.
What is a SCADA system, what applications it has and what role it plays in production you will read in the article: What is SCADA?
Let’s start with the ERP system, which is classically considered one of the first steps in the development of a company. Any organization, even if it grows organically from very small to medium, large, and even later becoming part of some larger structure, will have trouble functioning smoothly without an ERP system.
ERP (Enterprise Resource Planning) is a superior system that is a kind of first interface with the customer. It is in ERP that we gather information about sales, costs and all business aspects of operation.
Just a couple years ago, there was a belief that ERP, as a comprehensive business management system, was capable of integrating all the essential functions needed for the smooth operation of manufacturing companies. Today we look at it a bit more realistically – just as there is no cure for all diseases, even a highly specialized system cannot be the answer to all needs.
ERP systems are not specialized for supervising the production process and planning or optimizing planning. While they do have such functions, they operate in a very limited, merely basic form.
When a company grows, the number of variables increases, and production processes cover even wider range, we come to a situation where better, more detailed supervision of the production process is needed. Thus arises the need to implement another solution – the MES (Manufacturing Execution System). Thanks to it, we can not only monitor our production, but also have a greater influence on the degree of utilization of the machinery park.
With the support of MES, we can check the utilization of machinery and equipment, for example in terms of OEE, to see what is the actual productivity of the equipment installed in the company and whether it is actually used as intended.
MES and ERP systems can be integrated with each other. This allows the exchange of information between them. For example, MES systems send reports, on the basis of which the ERP system can periodically and with a set frequency make records of, for example, the progress of the cost of work-in-progress or the appearance of finished goods.
Learn more about the capabilities of the MES system. Read our article: MES system – how does it work in practice in production? – ImFactory
Production plan can be created both in the ERP system and in the MES system. When it is created in the ERP, so to speak, “top-down” it is then sent to the MES system, which takes over supervision of its implementation. If the MES does not receive such a plan, it creates it on its own, e.g. on the basis of the established marches.
Nevertheless, neither ERP nor MES are systems created strictly for planning. As production processes become more complex, and the organization grows and becomes more aware of its strengths and weaknesses, it usually comes to the conclusion that production plans created with the help of these systems are not quite optimal.
There is a lot going on in the market. Practically every day provides new, sometimes surprising solutions. As a result, the situation of production companies is constantly changing – customers postpone orders, deliveries come late, orders are sometimes incomplete, etc. Also in production things are sometimes different – there are unplanned stoppages, breakdowns or various kinds of slowdowns. In a word, the variables that affect the implementation of the production plan are really a lot. If we blindly follow the plan we sent to the MES and have it oversee execution, we may find that we are not achieving satisfactory results, not using our machinery to its full potential, not completing orders on time or not responding to current market needs. Even if the results are satisfactory, it may turn out that they could be even better if we had the ability to update the plan on an ongoing basis, taking into account all the variables.
Where there is a need for advanced planning, APS-class systems come to the rescue. There are already many such solutions available on the market, providing very good quality. APS, or Advanced Planning and Scheduling, is modern software that, based on the data provided, generates professional plans and schedules for production.
APSs have numerous functions to take into account a variety of factors, and complex plans and schedules are generated instantly, even within seconds. This makes it easy to prepare subsequent versions whenever something changes or new data is received. In theory, APS would be able to edit a plan almost “on the fly,” but in reality various production constraints do not allow this, so it is updated as often as possible.
The system also allows the creation of many alternative scenarios based on various criteria. Thanks to this, it becomes a very good tool for finding the most optimal solutions, continuously improving processes occurring in production or evaluating orders coming in from the market in terms of their profitability.
How to assess whether orders coming in from the market will be profitable for your company you will read in this article: APS and company profitability. Part 2: How to make optimal business decisions?
As a manufacturing company grows, more needs arise for management, organization, data collection, process monitoring and effective planning. The right systems can help with these challenges, helping to increase efficiency, reduce costs, improve product quality and make the company more competitive in an ever-changing market.
Read also:
Production scheduling and related challenges – ImFactory
The article is based on materials from the webinar:
Production scheduling as a tool for improving company profitability (youtube.com)
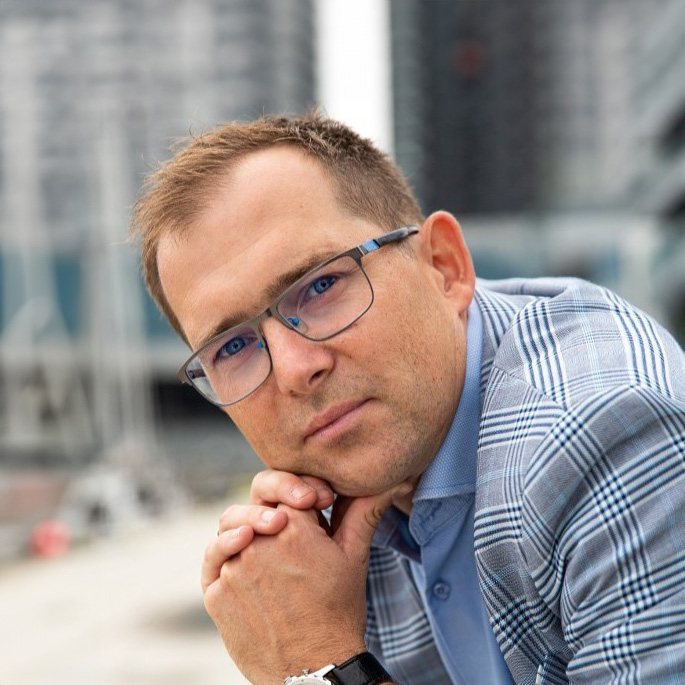
Tomasz is a production management expert with extensive experience in developing programs aimed at improving production efficiency and optimizing resource utilization. He is an advocate of Agile methodologies in project management and has successfully implemented numerous Industry 4.0 solutions. Currently, Tomasz serves as a consultant at ImFactory, specializing in the design of advanced MES architectures.
See also
Want to learn more? Visit our Knowledge Base, where you'll find articles and webinars by experts to expand your knowledge.
Check if Digital Transformation is the Answer to Your Company's Needs

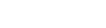
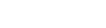
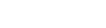
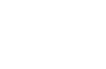
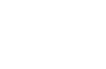
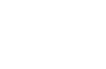
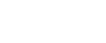
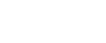
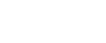
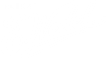
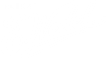
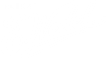
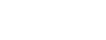
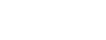
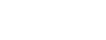






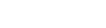
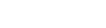
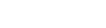
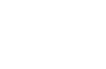
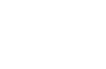
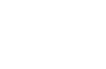
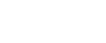
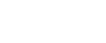
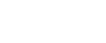
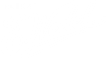
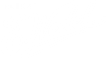
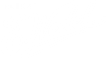
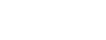
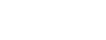
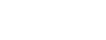






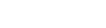
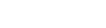
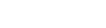
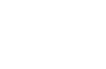
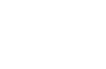
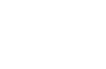
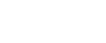
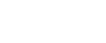
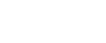
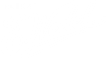
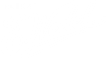
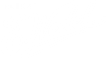
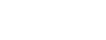
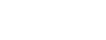
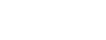






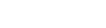
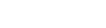
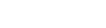
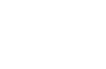
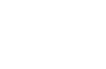
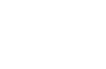
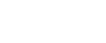
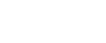
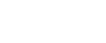
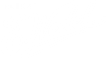
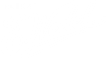
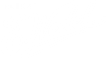
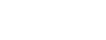
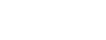
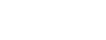


