Many publications geared towards businesses and their management contain plenty of ideas, solutions, and initiatives aimed at cost reduction within an enterprise.While these materials are often valuable and helpful, it’s essential to note a significant detail: the majority of these publications center around costs that are already visible to us. This is hardly surprising, as costs related to materials we use or personnel we employ immediately stand out. Let’s delve deeper into the subject of costs and explore those that may go unnoticed due to their less conspicuous nature.
Let’s examine cost allocation within a company. An area worth scrutinizing, especially when seeking hidden expenditures, is indirect costs. Some may be allocated using specific keys, but others are not directly assigned to a particular product, necessitating further correlation. However, this is not always straightforward, as many companies grapple with costs challenging to classify. Consequently, these costs are often thrown into one huge sack of expenses not categorized in any way.
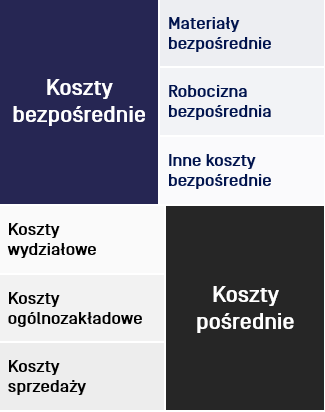
For instance, during a delivery involving multiple products, our attention is typically focused on the tasks associated with the received items. Rarely do we proceed to analyze transportation costs and examine which fraction of these costs should be allocated to each product.
Another area where funds may leak out unnoticeably is energy consumption. Numerous companies strive to optimize energy use by investing in cutting-edge solutions. However, simple practices like turning off the AC when leaving the office or adjusting heaters based on temperature often slip our minds. These solutions are easy to apply, they only require cultivating the right habits among employees. Although these actions may not yield immediate spectacular results, they are integral components of a comprehensive analysis. Understanding the ratio of benefits to costs is crucial in these cases.
At times, rather than pursuing additional investments for long-term savings, it is worth exploring solutions available at hand. Even when it seems little can be done, the question should be asked, “Is that really the case?” A prime example is the shared use of specialized tools in a company.
In a scenario where tools were shared across different products, a strategy was devised to introduce a coefficient determining permissible tool expenses for each workload measured in hours and for each hour.
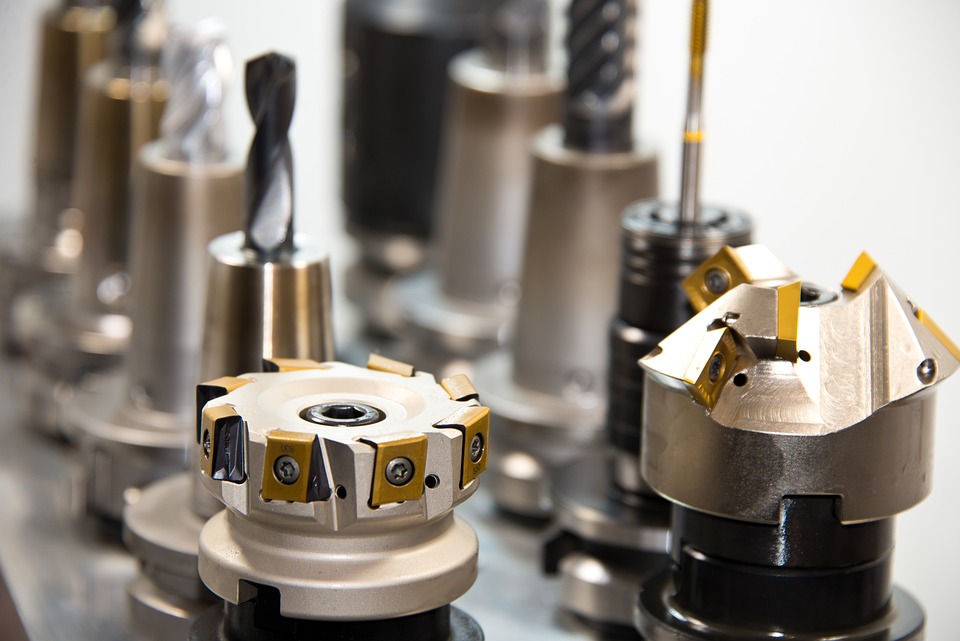
The individuals overseeing this project formulated a production plan for the upcoming 2-3 weeks, establishing ranges and limits for tool expenses. Initially, it appeared that certain tools had reached their maximum capacity, seemingly impossible to optimize further.
However, intriguing initiatives gradually emerged. People engaged in the project began to collaborate, optimizing tool usage and ensuring compliance among operators. While the initial thresholds were relatively high, the tool department consistently reduced these costs upon witnessing positive outcomes. After three quarters, it became evident that the project had generated millions in savings, which no one had initially expected.
The correlation between costs and production volume is an essential aspect of seeking savings. The amount of production is the function that determines the cost. The key objective is not always to achieve the lowest cost but to justify it in the context of the production volume.
While some expenses exhibit a linear correlation with the production volume, this is not always the case. Concerning less apparent costs, an analysis is necessary to understand their relationship to the amount of production and their role in the creation of various products. Without such an assessment, these costs become diluted and irretrievable.
Another complex problem is the cost of preparing to manufacture a new product. This involves a high degree of randomness, initially making it challenging to identify which actions will yield benefits. Nevertheless, it is worthwhile to scrutinize each cost incurred: can it be correlated with expected revenue? Only through this approach can a comprehensive understanding be gained.
Can automation somehow assist in pinpointing these less obvious costs and reducing them? Let’s consider an example from a company where production process was well-metered and equipped.
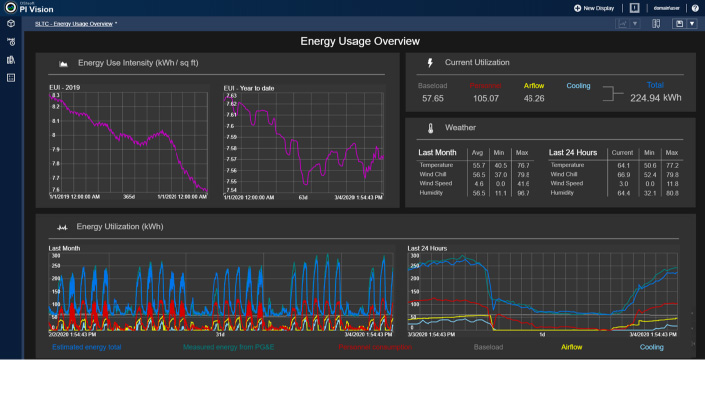
The company used kilowatt-hour per ton of product as its unit of production measurement. At a certain point, one product started exhibiting an unprecedented, momentary increase in costs. The reason for that was soon discovered: on one of the manufacturing lines, a large engine, consuming a considerable amount of energy, was switched into manual mode by the maintenance department turned on without the controller. As a result, the engine operated continuously. None of the employees found this problematic, as it didn’t affect production directly. However, the MES allocated the cost of operating this engine to a specific product, revealing where money was senselessly draining.
This example vividly illustrates that automation enables a swift detection of non-standard cost increases and helps locate their sources. Furthermore, it allows us to shift our focus from the visible and readily accessible to the less apparent cost drivers. The conclusion is simple: if an investment in automation makes financial sense, it’s worthwhile to embrace automation as extensively as possible.
Returning to the cost allocation, department costs constitute a significant group that’s often challenging to optimize due to their ambiguous nature. However, solutions are available.
An American corporation decided to allocate individuals not directly involved in production optimization in optimization programs and employee idea initiatives. Surprisingly, the team demonstrated immense potential, and valuable ideas emerged from the most unexpected sources.While implemented ideas were rewarded, the primary goal of the experiment was to instill a culture of saving among employees.
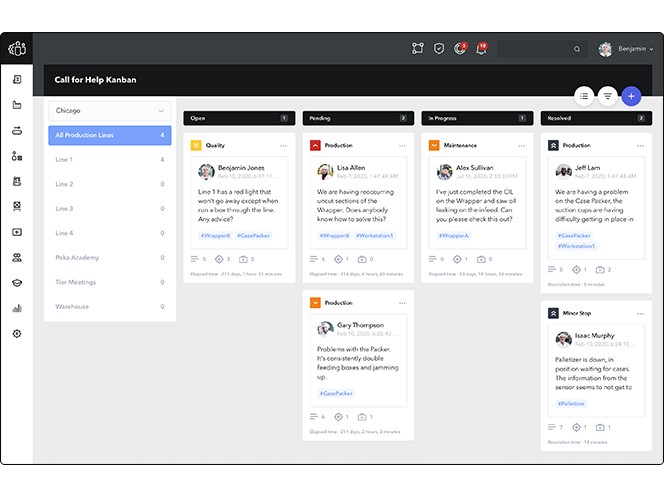
Incorporating employees from various departments in the search for savings is motivating and can yield impressive results. However, it’s crucial to note that initiatives should not revolve around measures like “no coffee or tea for employees” or “no xerox paper”. Souch ideas would introduce nothing but demotivation. Instead, we should seek solutions that do not deprive the company and its employees of quality components but enable a more efficient use of existing resources.
Even if many employee proposals turn out to be misguided, implementing employee idea systems still holds great value, fostering a sense of responsibility among employees for the company’s affairs. Among the proposals, there will invariably be a true gem that ensures a return on investment, often exceeding expectations.
As demonstrated, savings can be found in areas one might not suspect. Optimization, cultivating good habits, embracing automation,and actively seeking new ideas, can significantly reduce costs. Nevertheless, it is essential to possess a detailed understanding of their correlation with production. Even the smallest expenses should not be underestimated, as analyzing them in the context of overall production volume can yield unexpected benefits.
See also
Want to learn more? Visit our Knowledge Base, where you'll find articles and webinars by experts to expand your knowledge.
Check if Digital Transformation is the Answer to Your Company's Needs

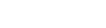
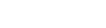
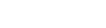
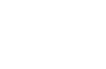
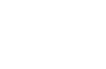
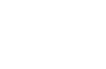
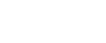
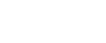
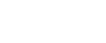
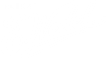
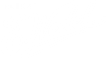
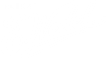
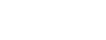
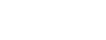
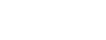






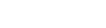
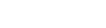
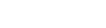
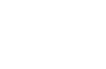
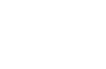
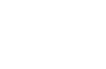
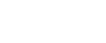
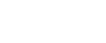
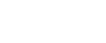
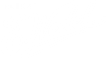
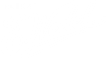
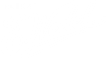
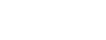
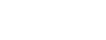
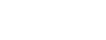






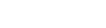
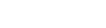
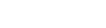
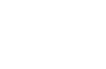
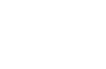
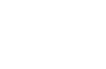
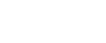
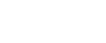
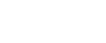
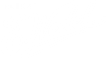
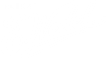
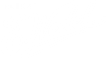
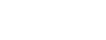
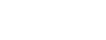
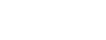






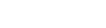
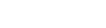
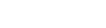
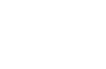
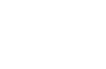
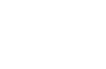
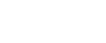
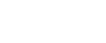
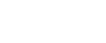
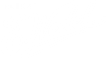
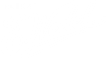
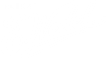
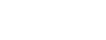
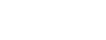
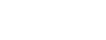


