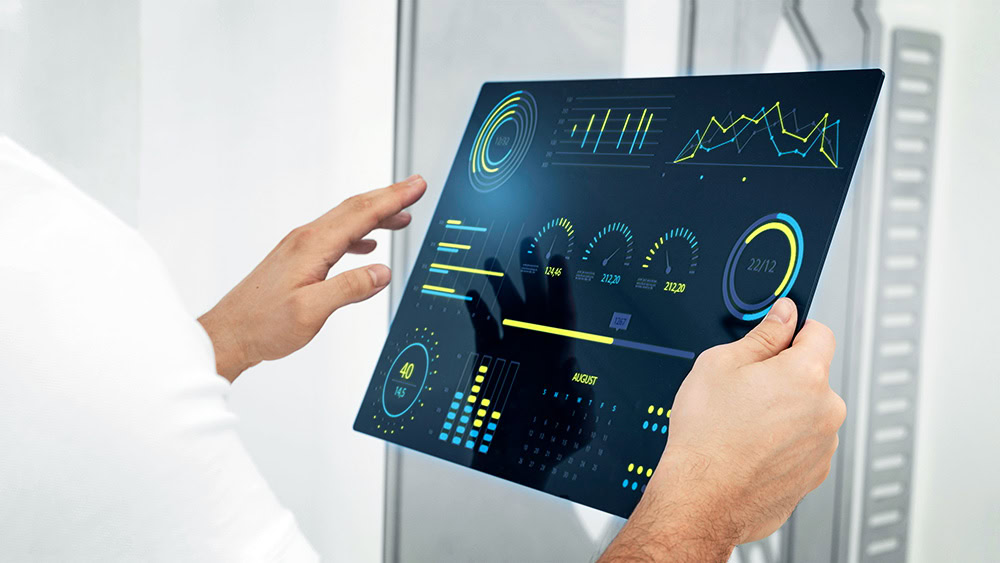
MES and APS: Comparing Two Specialized Systems
MES vs. APS – how do they fare in comparison? Find out in the following article as we outline the key differences between these two systems. What tasks does each system support, and can they be integrated?
Manufacturing Execution System (MES) is a solution designed for manufacturing management in industry. It integrates various production stages such as planning, monitoring, control, and reporting to optimize manufacturing processes.
Its primary functionalities include:
- Production monitoring and control: MES tracks real-time manufacturing data like machine utilization states, the production quantities, process parameters, and others, enabling continuous monitoring of manufacturing processes and prompt issue detection.
- Quality management: MES incorporates in-line quality control features such as sampling, result tracking, deviation management, and audits, ensuring that high product quality is maintained.
- Resource management: MES monitors the inventory of raw materials and consumables, tracking their consumption during production, facilitating efficient inventory management, and preventing deficiencies.
- Reporting and analysis: MES generates reports on various production aspects like efficiency, cycle times, quality, costs, and others, aiding managers in performance analysis and well-informed decision-making.
In summary, Manufacturing Execution Systems optimize manufacturing processes, enhance efficiency, improve quality, and provide production control.
Advanced Planning and Scheduling (APS) is an advanced system widely used across various sectors and industries. Its main goal is to optimize production planning, resource management, and operation scheduling to achieve maximum efficiency, cost minimization, and performance maximization.
By integrating diverse manufacturing data such as resource availability, operation durations, delivery schedules, customer preferences and technological constraints, the APS generates optimal production schedules considering various factors and constraints.
The solution also enables users to track production progress, update schedules in real-time, identify delays, detect potential problems, and make data-driven decisions.
APS systems find applications across various sectors including manufacturing, logistics, distribution, transport, and services.
While both MES and APS find application in manufacturing, they diverge significantly in several aspects. Let’s examine how the systems compare across various factors:
MES vs. APS: Purpose
MES serves as an executive management system, focusing on real-time tracking and oversight of manufacturing processes. It provides information on production progress, resource management, quality control, time tracking, and personnel management. Its main goal is to optimize manufacturing processes within the factory.
APS focuses on optimizing production planning based on available resources like machinery, materials, and time, scheduling production to minimize expenses and execution time while maximizing efficiency.
MES vs. APS: Operational scope
MES operates at the execution level, close to the manufacturing line. Its goal is to monitor and directly manage manufacturing processes such as quality control, time tracking, resource allocation, and operational management in real-time.
APS operates at a higher planning level, developing schedules based on diverse data inputs like resource availability, customer orders, execution time, and other factors. APS comprises long-term, medium-term, and short-term planning to optimize production processes on multiple levels.
MES vs. APS: Operation time
MES operates in real-time and delivers up-to-date information on production states and executive activities.
APS engages in the planning process based on available data, although not necessarily in real-time, forecasting and generating production schedules based on prior information.
MES vs. APS: Scale of application
MES primarily operates within factories and manufacturing facilities, optimizing processes on an operational scale.
APS finds application both within manufacturing facilities and across the entire supply chain. It is used to optimize production planning and scheduling in a broader operational context.
Despite different aims and functionalities, MES and APS can successfully cooperate and complement each other effectively in manufacturing management. In practice, the systems are often integrated to provide a comprehensive solution for production management.
MES data, including machine utilization states, material consumption, quality metrics, and personnel availability, can be entered into APS to comprehensively plan and schedule production, considering current conditions and facility constraints.
Conversely, APS data can be fed back into the MES to monitor production plan execution, report progress, and share schedule information with personnel, based on current APS insights.
The integration of MES and APS facilitates better production management, process optimization, cycle time reduction, cost savings, and quality improvement. The systems complete each other in creating a cohesive information system which encompasses both executive operations and strategic production planning.
Comparing MES and APS across various dimensions highlights that the systems were created for different purposes, and they support companies in different tasks. While MES focuses on real-time process tracking and management, APS is geared towards production planning and scheduling. Despite different approaches, both systems contribute to performance improvement, operational efficiency, and enterprise management. Through integration, their combined benefits can be maximized.
Find out more about MES and APS systems:
Advanced Planning and Scheduling (APS): Does Your Company Need It?
If you’re considering MES implementation in your company, refer to our expert articles for a wealth of practical information:
See also
Want to learn more? Visit our Knowledge Base, where you'll find articles and webinars by experts to expand your knowledge.
Check if Digital Transformation is the Answer to Your Company's Needs
The Free Consultation Process:

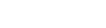
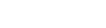
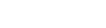
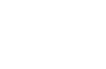
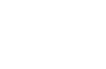
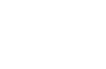
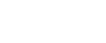
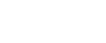
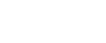
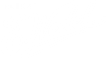
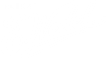
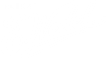
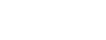
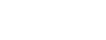
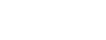






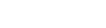
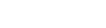
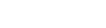
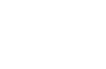
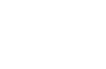
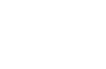
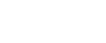
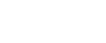
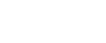
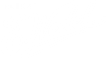
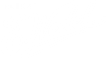
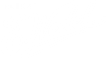
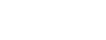
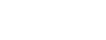
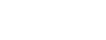






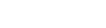
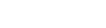
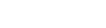
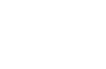
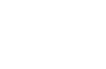
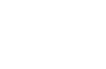
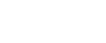
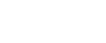
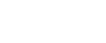
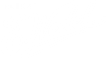
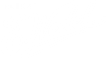
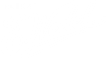
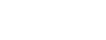
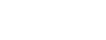
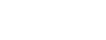






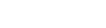
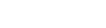
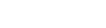
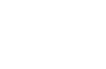
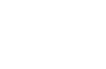
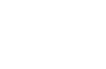
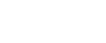
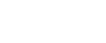
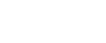
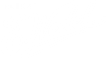
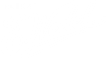
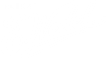
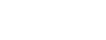
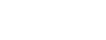
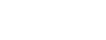


