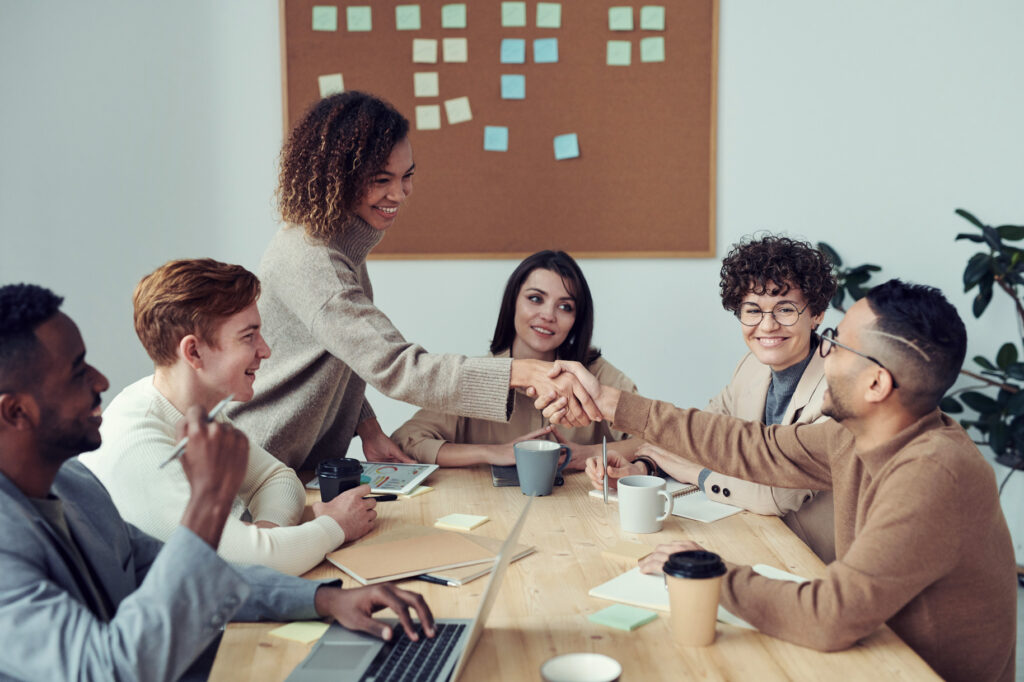
Czy system MES może wspomóc zarządzanie procesem metodą Kanban?
Kanban, czyli metoda sterowania procesami produkcyjnymi, wywodzi się z japońskiego przemysłu motoryzacyjnego i była pierwotnie stosowana w Toyota Production System w latach 50. XX wieku. Przez lata Kanban się rozwijał i obecnie często bardziej przypomina nowoczesny system informatyczny niż pierwotną wersję opartą na przyczepianych do tablicy papierowych karteczkach. Sama idea jest bardzo prosta, choć może być z powodzeniem stosowana do zarządzania skomplikowanymi procesami. Wspomóc ją może dodatkowo system realizacji produkcji MES. Połączenie tych dwóch rozwiązań pozwoli uzyskać pełną kontrolę nad produkcją.
Kanban to metoda zarządzania przepływem pracy, która ma na celu poprawienie efektywności, elastyczności i jakości procesów w organizacji. Jej głównym celem jest zwiększenie wydajności poprzez optymalizację procesu produkcyjnego lub pracy, eliminowanie marnotrawstwa (takiego jak nadprodukcja, nadmiar zapasów, opóźnienia) oraz umożliwienie szybkiej reakcji na zmiany i niestabilności w środowisku pracy.
Podstawowym narzędziem w tej metodzie jest tablica Kanban, która służy do wizualizacji przebiegu pracy. Składa się ona z kolumn przedstawiających różne etapy oraz karteczek Kanban. Kolumny mogą mieć tytuły odpowiadające etapom pracy, na przykład „Do zrobienia„, „W trakcie„, „Zakończone„. Karteczki kanbanowe (lub wirtualne karty) przechodzą przez różne etapy procesu. Każda karteczka zawiera informacje o zadaniu, takie jak opis, priorytet czy osoba odpowiedzialna. W miarę postępu zadania, zmienia się położenie karteczek na tablicy.
W metodzie Kanban funkcjonują limity WIP, czyli pracy w toku. W praktyce oznacza to ograniczenie dla ilości pracy, którą można wykonywać jednocześnie w danym etapie procesu. Ma to na celu uniknięcie przeciążenia zadaniami, co z kolei pomaga zachować płynny przepływ pracy oraz skrócić czas cyklu.
Ważnym terminem związanym z metodą Kanban jest Kaizen, czyli ciągłe doskonalenie za pomocą niewielkich, ale regularnych kroków. Poprzez ciągłe monitorowanie, analizowanie i dostosowywanie tablicy Kanban oraz samego procesu pracy, zespoły mogą znajdować obszary do usprawnienia i wprowadzać udoskonalenia.
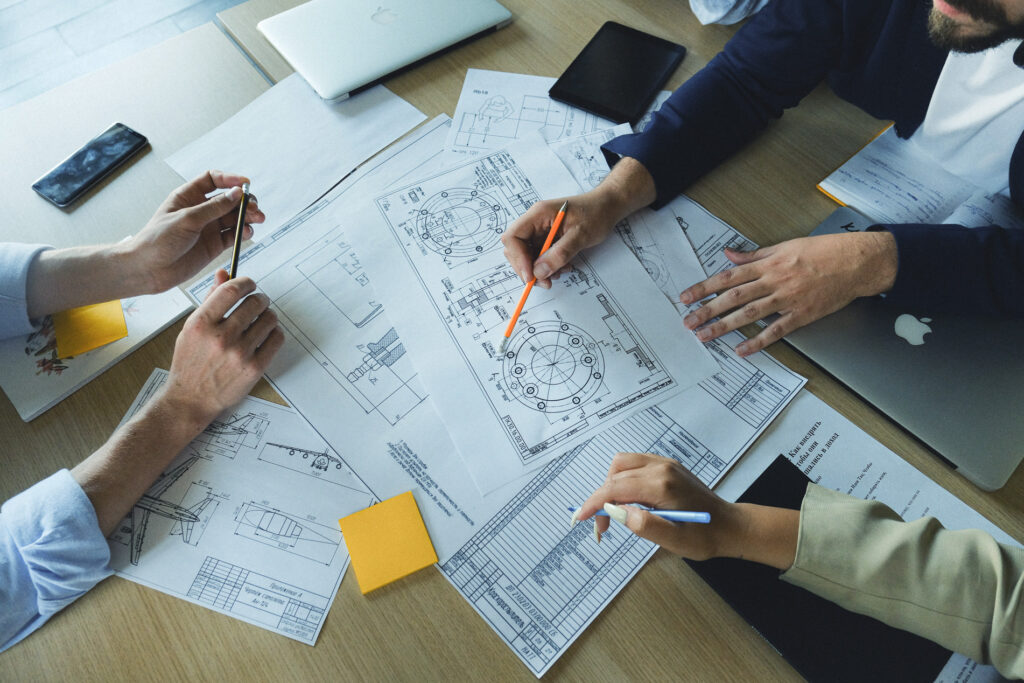
Systemy sterowania produkcją Kanban są elastyczne i umożliwiają szybką reakcję na zmiany w wymaganiach, priorytetach czy warunkach pracy. Kiedy pojawia się nowe zadanie lub zmienia się priorytet, karteczki Kanban mogą być przesuwane na tablicy, dostosowując proces do nowej sytuacji.
Metoda Kanban jest często stosowana w projektach zwinnych oraz w dziedzinach wymagających ciągłego dostosowywania się do zmian, takich jak rozwój oprogramowania, produkcja, zarządzanie projektami, obszar IT czy działalność usługowa. Dzięki wizualizacji, ograniczeniu pracy w toku i elastycznemu podejściu, Kanban pomaga organizacjom osiągać lepsze wyniki poprzez usprawnienie przepływu pracy i skrócenie czasu realizacji zadań.
System realizacji produkcji MES i metodę Kanban można zintegrować w celu efektywnego i zautomatyzowanego zarządzania produkcją. Jakie kroki trzeba podjąć w celu skutecznego połączenia tych dwóch narzędzi?
- Zacznij od przeprowadzenia analizy procesów produkcyjnych, aby zidentyfikować obszary, które można zoptymalizować przy użyciu MES. Następnie ustal priorytety i cele, które chciałbyś osiągnąć przy pomocy tego systemu, takie jak zwiększenie wydajności, redukcja zużycia surowców, skrócenie czasu produkcji itp.
- Kolejnym krokiem będzie implementacja Kanban. Metodę tę warto w pierwszej kolejności wprowadzić w obszarach, które są najbardziej istotne dla produkcji. Na przykład tam, gdzie często występują opóźnienia w dostawach materiałów lub nadmierne skupienia zasobów.
- Zdefiniuj karty Kanban dla różnych rodzajów produktów lub procesów, aby kontrolować ilość prac do wykonania i dostępnych zasobów, a następnie zintegruj system MES z tablicami Kanban lub elektronicznymi narzędziami Kanban, aby umożliwić przekazywanie danych o stanie produkcji i zapotrzebowaniu na surowce między systemem MES a Kanban. Dzięki tej integracji możesz w czasie rzeczywistym monitorować postęp produkcji i dostosowywać przepływ materiałów i zadań Kanban na podstawie danych MES.
- Regularnie monitoruj efektywność połączenia MES i Kanban, analizując wskaźniki wydajności i dostępność materiałów. Wdrażaj ciągłe doskonalenie, dostosowując procesy i procedury w miarę zdobywania doświadczenia i zbierania danych.
Integracja MES i Kanban może przynieść wiele korzyści dla przedsiębiorstwa produkcyjnego. Oto kilka z nich:
- Optymalizacja przepływu pracy – metoda Kanban pomaga w zarządzaniu przepływem pracy poprzez wizualizację i kontrolę ilości materiałów oraz etapów produkcji. Integracja z systemem MES pozwala na skuteczniejszą optymalizację procesu produkcyjnego, uwzględniając dostępność zasobów, harmonogramowanie zadań i monitorowanie postępu w czasie rzeczywistym (online).
- Dokładne prognozowanie zapotrzebowania – poprzez połączenie danych z systemu MES dotyczących aktualnej produkcji i stanów magazynowych z zasadami Kanban, przedsiębiorstwo może dokładniej prognozować swoje zapotrzebowanie na surowce i komponenty.
- Minimalizacja nadmiernego gromadzenia zapasów – kombinacja Kanban z MES pozwala na kontrolowane zamawianie materiałów i komponentów na podstawie rzeczywistych potrzeb, co minimalizuje koszty magazynowania i zapobiega przetrzymywaniu przestarzałych zapasów.
- Dostosowywanie priorytetów – korzystając z MES można dynamicznie dostosowywać priorytety produkcji na podstawie bieżących potrzeb i warunków rynkowych. Te priorytety mogą być odzwierciedlone w systemie Kanban, umożliwiając bardziej elastyczne zarządzanie produkcją.
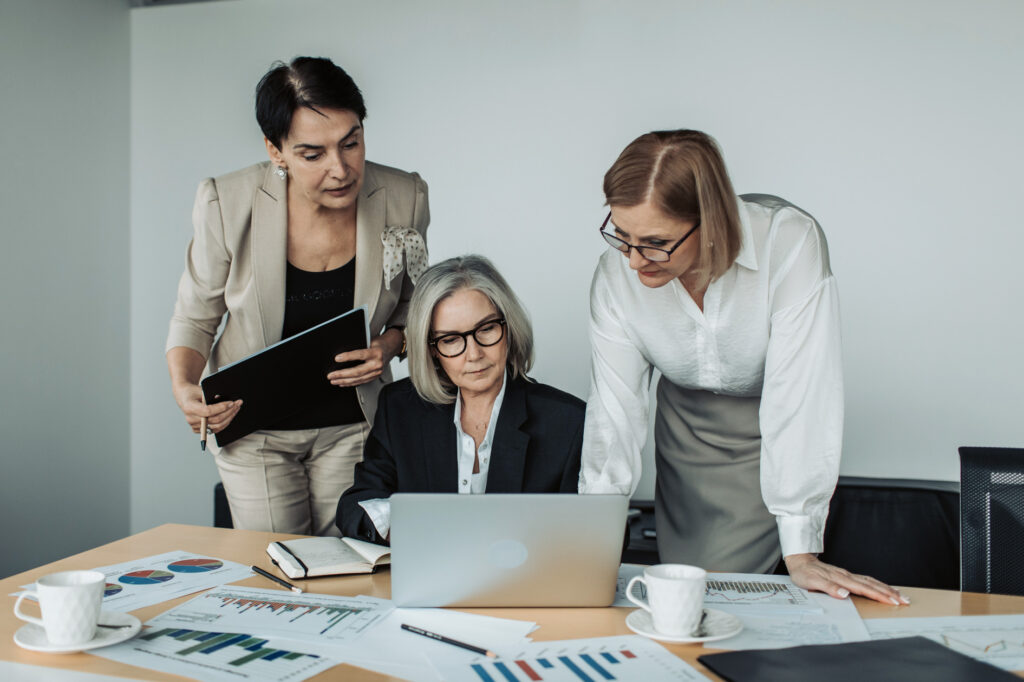
- Pełna kontrola nad procesem – połączenie danych Kanban z danymi MES pozwala na uzyskanie pełnej kontroli nad procesem produkcyjnym. To z kolei umożliwia dokładną analizę wydajności, identyfikację obszarów wymagających poprawy i podejmowanie decyzji na podstawie rzetelnych informacji, otrzymywanych online (w czasie rzeczywistym).
- Zwiększenie efektywności operacyjnej – integracja MES i Kanban może prowadzić do zwiększenia ogólnej efektywności operacyjnej, poprzez lepszą synchronizację produkcji, minimalizację strat i opóźnień oraz zoptymalizowanie wykorzystania zasobów.
Integracja MES i Kanban może znacznie poprawić zarządzanie produkcją, umożliwiając lepszą kontrolę nad procesami i zapewniając bardziej elastyczne dostosowanie do zmieniających się warunków. Ważne jest jednak, aby dopasować te koncepcje do specyficznych potrzeb i warunków w danej firmie. Skuteczne wdrożenie takiego połączenia wymaga dobrze zaprojektowanego systemu informatycznego, odpowiedniego przeszkolenia pracowników oraz ciągłego monitorowania i doskonalenia procesów produkcyjnych. Przy wdrażaniu tych rozwiązań warto skorzystać z pomocy doświadczonych specjalistów.
Zobacz również
Chcesz dowiedzieć się więcej? Odwiedź naszą Bazę Wiedzy, gdzie znajdziesz artykuły i webinary przygotowane przez ekspertów, które pozwolą Ci poszerzyć swoją wiedzę.
Umów się na bezpłatną prezentację lub rozmowę na wskazany przez Ciebie temat.

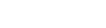
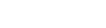
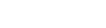
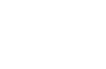
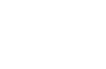
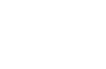
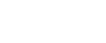
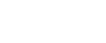
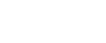
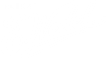
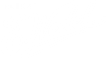
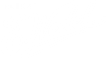



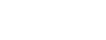
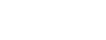
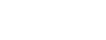



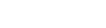
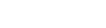
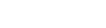
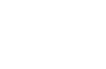
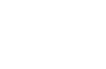
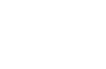
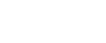
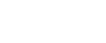
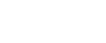
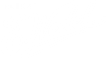
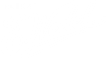
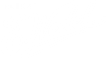



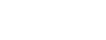
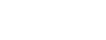
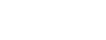



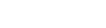
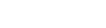
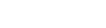
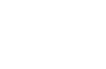
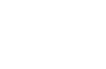
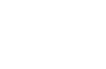
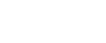
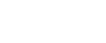
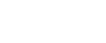
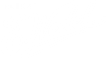
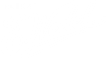
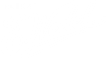



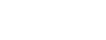
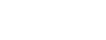
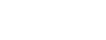



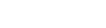
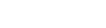
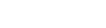
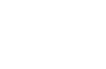
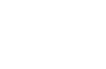
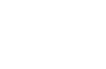
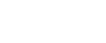
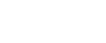
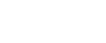
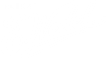
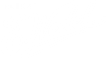
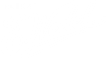



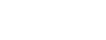
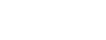
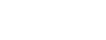