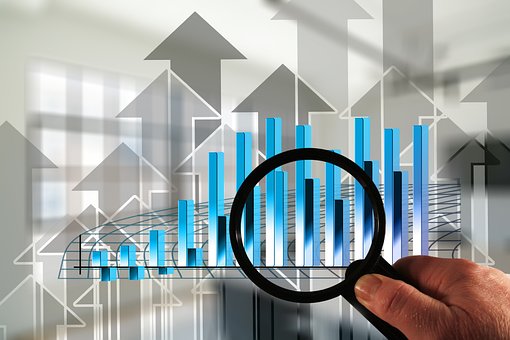
Po nitce do kłębka. Jak znaleźć przyczyny problemów na produkcji?
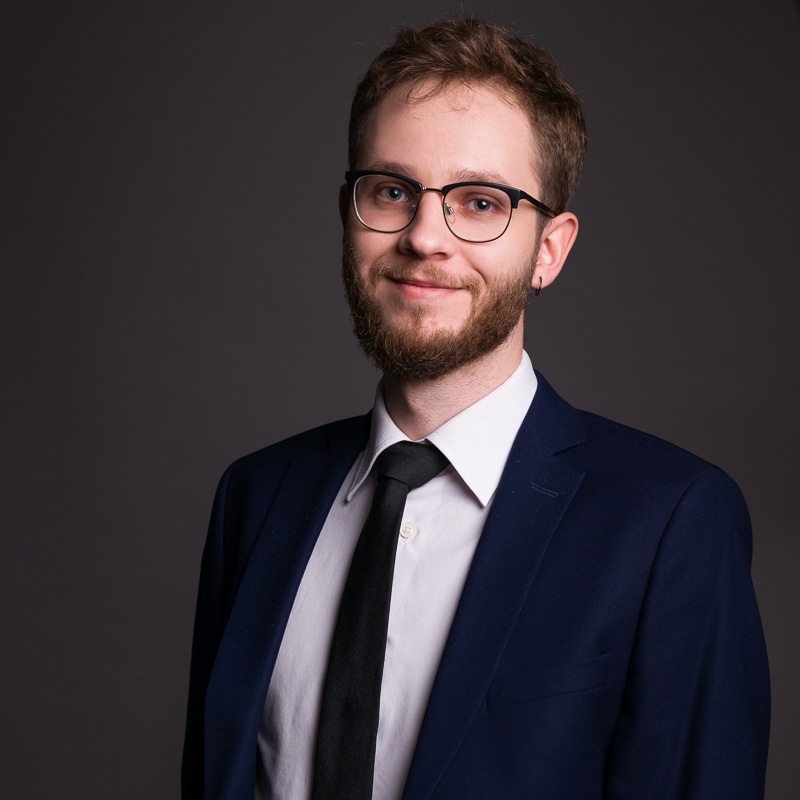
Adam Pachałko
Problemy produkcyjne to wyzwanie, z którym mierzą się wszystkie zakłady, niezależnie od wielkości czy branży. Przytrafiają się najlepszym managerom i liderom i nawet zaangażowani pracownicy z wysokimi kwalifikacjami czy nowoczesne maszyny i systemy nie sprawią, że uda się ich całkowicie uniknąć. Można za to zminimalizować straty. Gdzie szukać przyczyn, których spowodowały problemy produkcyjne i od czego zacząć ich identyfikację? Oto historia, która mogła mieć miejsce w każdym zakładzie produkcyjnym.
Wyobraźmy sobie pewną fabrykę, w której jeden z członków zarządu analizował miesięczny raport. Zauważył, że jednego dnia wskaźnik OEE był niepokojąco niski, co jednoznacznie sugerowało, że pojawiły się jakieś problemy produkcyjne. Niezwłocznie zwrócił się więc do lidera produkcji, z prośbą o wyjaśnienie tak słabego wyniku.
Ogólny raport OEE sugeruje, że 7 lipca miały miejsce jakieś problemy produkcyjne, źródło: ImFactory
Aby znaleźć przyczynę niskiego OEE, lider musiał podjąć szereg działań. Sam raport wprawdzie wskazywał, że dzieje się coś niedobrego, jednak nie wyjaśniał, w czym tak naprawdę tkwi problem. Pierwszym krokiem, który podjął, było wygenerowanie raportów dla wszystkich maszyn pracujących w fabryce tego dnia.
Po przestudiowaniu raportów zauważył, że w tym dniu OEE wszystkich maszyn było nieco niższe, ale od razu rzuciło mu się w oczy, że jedna maszyna zdecydowanie wyróżniała się na tle innych. Kolejnym logicznym krokiem było więc zbadanie, co dokładnie działo się właśnie z tą maszyną, tego konkretnego dnia. Takich danych mógł dostarczyć wygenerowany dla niej raport OEE.
Raport OEE dla poszczególnych maszyn pokazuje, której z nich trzeba się bliżej przyjrzeć, źródło: ImFactory
Analizując raport OEE dla tej konkretnej maszyny, lider produkcji nie tylko spojrzał na ogólny wynik OEE, ale też przeanalizował jego składowe – dostępność, wydajność i jakość, które mogły mu dostarczyć bardziej szczegółowych informacji, pomocnych w dotarciu do źródła problemu.
Od razu zauważył różnego rodzaju anomalie zarówno samego OEE, jak i jego składowych. Ogólny wynik OEE przez cały dzień utrzymywał się na bardzo niskim poziomie, momentami spadając prawie do 0. Tylko na początku i na końcu zmiany wyniki były w miarę zadowalające. Analizując poszczególne składowe OEE, lider zauważył, że czynnikiem, który już pomiędzy godziną 7:00 a 8:00 zaburzał wysokość ogólnego wskaźnika mogła być dostępność, która drastycznie spadła, co oznaczało brak produkcji. W kolejnych godzinach dostępność wzrosła, a następnie znowu spadła. Kiedy maszyna już pracowała, wydajność była nieco obniżona, a przed ostatnia godziną zanotowano jej wyraźny spadek. W ciągu całego dnia również jakość była na niższym poziomie, niż zazwyczaj.
Analiza poszczególnych składowych OEE dostarcza bardziej szczegółowych informacji, źródło: ImFactory
To już całkiem sporo informacji sugerujących, gdzie konkretnie pojawiły się problemy produkcyjne, jednak wciąż niewiele można z nimi zrobić. Jakie działania mógł zatem podjąć nasz lider w kolejnym kroku? Dobrym pomysłem okazało się porównanie uzyskanych informacji z raportem widma stanów maszyny. Dzięki temu zestawieniu można było już się domyślać, co mogło się wydarzyć. Wprawdzie nie były to jeszcze potwierdzone w informacje, które w pełni wyjaśniałyby przyczyny problemów na produkcji, jednak dało się zauważyć, że faktycznie od 7:00 do 8:00 na maszynie wystąpiła duża awaria. Kolor czerwony od razu zwrócił uwagę lidera, sugerując, że w drugiej części dnia doszło do kolejnej awarii, a potem, jak zauważył, miało miejsce duże przezbrojenie.
Zestawienie raportu OEE z widmem stanów maszyny, pozwala wyciągnąć kolejne wnioski, źródło: ImFactory
Mając takie informacje, lider domyślał się, że jakość produktu spadła najprawdopodobniej dlatego, że pomiędzy awariami operatorzy musieli ponownie kalibrować maszynę, możliwe też, że konieczne było wykonanie pewnej ilości sztuk testowych. Przez to spadła nie tylko jakość, ale też wydajność, ponieważ zarówno podczas produkcji testowej, jak i podczas kalibracji przy nastawach maszyn nigdy nie pracuje się z maksymalną prędkością, tylko tempo jest nieco wolniejsze. Choć lider wciąż nie miał stuprocentowej pewności, co dokładnie się wydarzyło, dzięki raportowi OEE mógł samodzielnie wyciągnąć pewne wnioski na temat przyczyn problemów na produkcji.
W poprzednich krokach nasz lider uzyskał już całkiem sporo informacji. Na podstawie zebranych faktów, wyciągnął następujące wnioski:
- Były dwie duże awarie, które spowodowały spadek dostępności.
- Po każdej awarii spadła jakość, wydajność i dostępność, co było naturalną koleją rzeczy przy różnych nastawach i przezbrojeniach.
- Po zlikwidowaniu awarii i powrocie do poprawnego działania, wskaźnik OEE znów wrócił do normy.
To już solidna dawka wiedzy, z którą można coś zrobić. Aby jednak jeszcze lepiej zrozumieć, co konkretnie spowodowało problemy produkcyjne, lider może podrążyć głębiej. Możemy się domyślać, że najważniejszą osobą, która będzie wiedziała najwięcej, jest operator obsługujący maszynę w danym dniu. Lider może więc z nim porozmawiać, żeby jeszcze doprecyzować szczegóły.
Przed rozmową lider postanowił spojrzeć jeszcze na szczegółowy raport stanów danej maszyny, aby zobaczyć kto na niej pracował w danym dniu i czy nie zostawił żadnych komentarzy. Taki raport pokazuje jak wyglądały stany maszyny minuta po minucie, a także czy dany stan był krytyczny i czy mógł wywołać istotne problemy produkcyjne. Dodatkowo za pomocą takiego raportu operator może porozumieć się z liderem za pomocą krótkich komentarzy. W wielu przypadkach jest to bardzo dobre medium, ponieważ różne nieprzewidziane sytuacje udaje się czasem łatwo wyjaśnić za pomocą dosłownie kilku słów. W opisywanym przypadku okazało się, że przyczyną awarii był pęknięty trzpień.
Szczegółowy raport stanów maszyny pokazuje, czy dany stan był krytyczny i pozwala operatorom na dodawanie komentarzy, źródło: ImFactory
Analizując raport OEE nasz lider krok po kroku zdołał wyjaśnić problemy produkcyjne. Czy jednak można mieć pewność, że wskaźnik OEE jest wiarygodnym wyznacznikiem poziomu efektywności produkcji? Czy np. strategia jaką przyjmie dany operator podczas pracy może znacząco wpływać na wysokość tego wskaźnika, powodując przekłamania danych? Wyobraźmy sobie trzy maszyny i przeanalizujmy przykłady, w których trzej różni operatorzy wykonywali na nich to samo zadanie, ale przyjmując różne strategie:
Strategia 1 – wiele przestojów
Operator na pierwszej maszynie pracował z ponadprzeciętną wydajnością i nie wyprodukował żadnych złych sztuk – wszystkie miały w 100% bardzo dobrą jakość. Jednak jego wydajność nieco spadła. Mogło to wynikać z różnych rzeczy – z wielu przerw, powolnych przezbrojeń, nieplanowanych postojów. Ostatecznie ta maszyna posiadała wskaźnik OEE na poziomie 75%.
Raport z maszyny 1, źródło: ImFactory
Strategia 2 – praca na wysokich obrotach
Operator na maszynie drugiej postanowił, że bardzo podkręci jej tempo. Wydajność w tym przypadku wyniosła aż 125%, bardzo dobrze przedstawiała się też dostępność. Ten operator nie miał żadnych długich przerw, a wszystkie przestoje i przezbrojenia były zaplanowane. Niestety przez to, że produkował na wysokiej prędkości maszyny, jakość produktu znacząco spadła – wyprodukował tylko 50% poprawnych sztuk. Ponieważ jednak pracował szybko, również wyprodukował dużo dobrych sztuk. W efekcie jego wskaźnik OEE również wyniósł 75%.
Raport z maszyny 2, źródło: ImFactory
Strategia 3 – stabilna praca
Trzeci operator postanowił pracować spokojnie, nie na pełnej prędkości maszyny, natomiast wszystkie sztuki, które wyprodukował, były dobre. Nie miał też żadnych przerw ani nieplanowanych postojów. Taka stabilna praca doprowadziła do tego, że wskaźnik OEE również doszedł do poziomu 75%.
Raport z maszyny 3, źródło: ImFactory
Powyższe przykłady pokazują, że niezależnie od tego w jaki sposób operator pracował na maszynie, za każdym razem wskaźnik OEE nie dublował pewnych strat i osiągnął ten sam poziom – 75%.
Powyższa historia pokazuje, że podczas rozwiązywania problemów produkcyjnych, niezwykle pomocne mogą okazać się dane zbierane z maszyn, w tym przede wszystkim raporty wskaźnika OEE, który jest w stanie przekazać nam dużo więcej niż tylko informacje o ogólnej efektywności produkcji. Przytoczone przykłady pokazują, że niezależnie od wybranej strategii pracy na maszynie, OEE wygląda tak samo, więc jest wskaźnikiem odpornym na przekłamania, który skutecznie pozwala analizować problemy produkcyjne i wyciągać z nich wnioski.
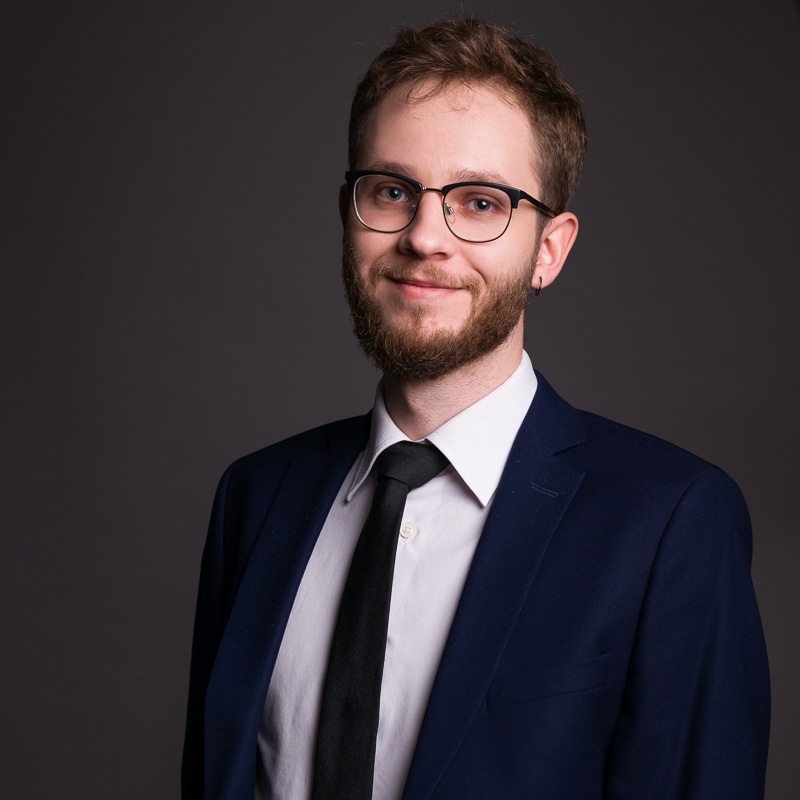
Absolwent Automatyki i Robotyki na Politechnice Gdańskiej. Inżynier ds. oprogramowania przemysłowego. Ekspert w dziedzinie systemów typu MES oraz Business Intelligence. Swoje pierwsze kroki zawodowe stawiał w ImFactory, w firmie, w której od 4 lat rozwija branżę oprogramowania przemysłowego w Polsce. Posiada doświadczenie zarówno w kontaktach z klientami, w pracy developerskiej, jak i w nadzorowaniu prac na obiektach produkcyjnych.
Zobacz również
Chcesz dowiedzieć się więcej? Odwiedź naszą Bazę Wiedzy, gdzie znajdziesz artykuły i webinary przygotowane przez ekspertów, które pozwolą Ci poszerzyć swoją wiedzę.
Umów się na bezpłatną prezentację lub rozmowę na wskazany przez Ciebie temat.
Jak przebiega proces bezpłatnej konsultacji?

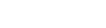
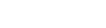
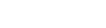
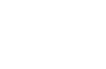
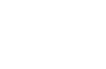
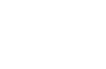
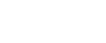
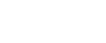
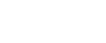
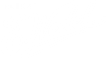
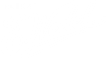
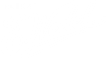



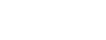
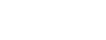
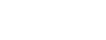



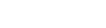
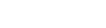
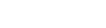
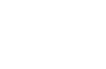
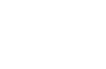
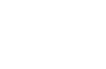
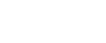
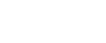
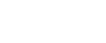
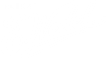
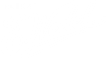
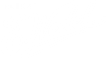



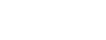
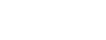
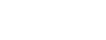



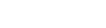
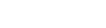
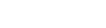
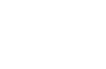
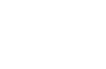
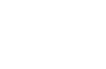
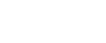
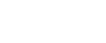
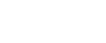
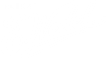
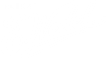
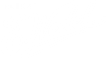



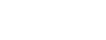
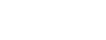
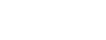



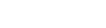
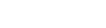
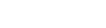
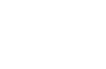
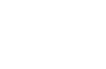
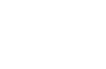
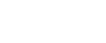
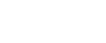
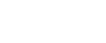
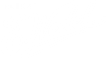
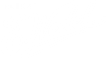
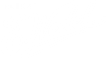



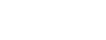
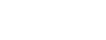
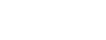