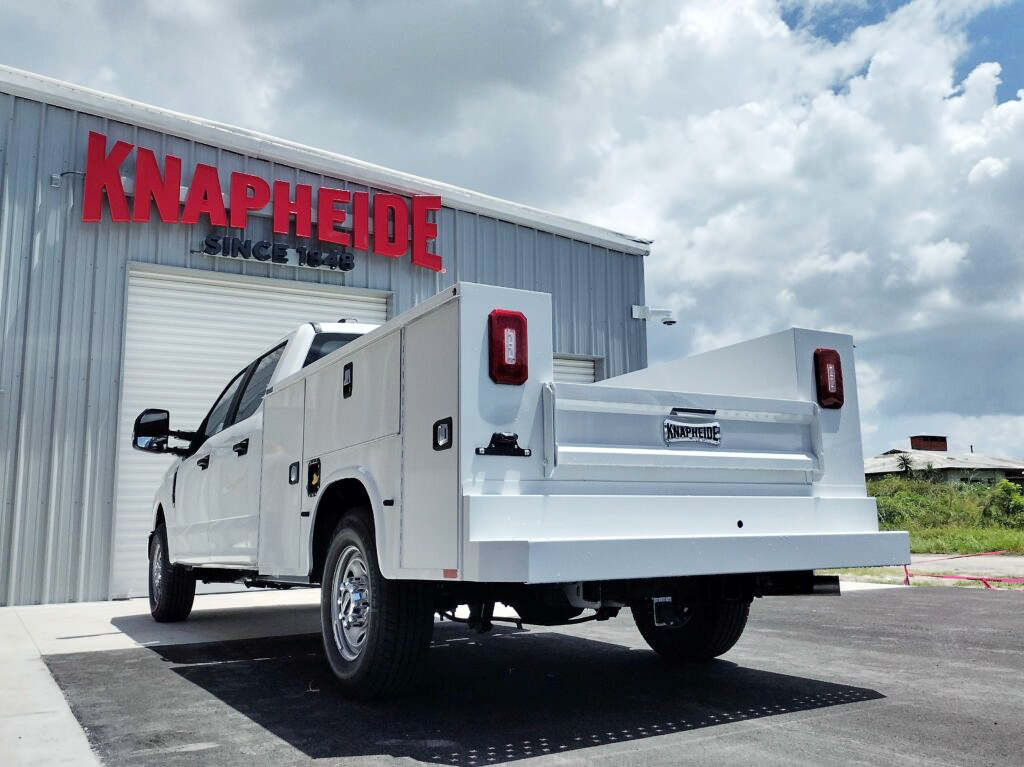
Producent rozwiązań dla transportu ciężkiego Knapheide wdraża system APS od PlanetTogether i notuje zwrot inwestycji po sześciu miesiącach
KLIENT: Knapheide
BRANŻA: Produkcja rozwiązań dla transportu ciężkiego
PROFIL KLIENTA: Knapheide to ceniony producent rozwiązań dla transportu ciężkiego z siedzibą we Flint w stanie Michigan, USA. Firma specjalizuje się w przekształcaniu podwozi półciężarówek Dodge, Ford i GM w wydajne samochody ciężarowe, które przemierzają kraj.
Firma została założona w 2004 roku jako wynik wieloletnich badań naukowych prowadzonych na Uniwersytecie Cornella. W połączeniu z ponad 20-letnim doświadczeniem w przemyśle, PlanetTogether koncentruje się na zwiększaniu zysków producentów poprzez zastosowanie oprogramowania do rozwiązywania problemów z planowaniem i harmonogramowaniem produkcji. Wydajne, proste w obsłudze i zintegrowane narzędzia oraz szkolenia pozwalają firmom przyciągnąć i utrzymać klientów poprzez skrócenie czasu realizacji zamówień, zwiększenie rentowności i minimalizację kosztów materiałów i magazynowania. Misją PlanetTogether jest stworzenie planety pełnej wydajnych producentów, zmieniając przemysł firma po firmie.
Z fabryki Knapheide wyjeżdża rocznie pięć tysięcy ciężarówek. Ponadto firma produkuje nadwozia samochodów serwisowych, nadwozia samowyładowcze, pługi śnieżne, platformy, samochody do transportu ładunków suchych klasy premium, podnośniki oraz nadwozia z żurawiem. W dziale planowania produkcji o każdej porze równocześnie realizowanych jest do dwudziestu zleceń.
Kiedy Dick Marx dołączył do oddziału Knapheide Flint jako kierownik ds. materiałów, z zaskoczeniem odkrył, że firma nadal korzysta z ogromnej tablicy magnetycznej do planowania zleceń. W jego przekonaniu nie do pomyślenia było, żeby producent oczekiwał od inżynierów tworzenia projektów za pomocą ołówka i linijki, dlaczego więc planiści musieli polegać na tablicy i arkuszach kalkulacyjnych?
Manualny proces planowania był pracochłonny i wymagał pełnoetatowego zaangażowania dwóch pracowników. Co gorsza, tablica stanowiła wąskie gardło dla linii produkcyjnych, zagrażając efektywności zakładu.
Tak Marx mówi o poprzednim systemie planowania:
“Ograniczał on nasze zdolności produkcyjne. Stał się wyznacznikiem naszego potencjału rozwojowego, a nie zdolności produkcyjnych.”
Codziennie pracownicy analizowali setki zleceń na tablicy, odważnie próbując robić korekty i prognozy. “Klienci chcieli wiedzieć, kiedy ich ciężarówka będzie gotowa, a my nie byliśmy w stanie podać im dokładnej odpowiedzi,” wspomina Marx. Jako osoba z branży informatycznej, Marx wiedział, że procesy Knapheide mogą zostać zautomatyzowane, dlatego postanowił znaleźć odpowiednie rozwiązanie.
W trakcie poszukiwań w internecie trafił na firmę PlanetTogether, twórcę oprogramowania dla producentów opartego na platformie Microsoft .NET, przeznaczonego do wielozakładowego planowania i harmonogramowania w czasie rzeczywistym. “Fakt, że oprogramowanie opiera się na platformie .NET, był dla nas istotny. To znacznie ułatwiło integrację z naszym oprogramowaniem przemysłowym,” zauważa Marx.
“Po obejrzeniu prezentacji i rozmowie z konsultantami wiedziałem już, że PlanetTogether to dla nas idealne rozwiązanie.”
Knapheide i PlanetTogether rozpoczęli wymianę danych. Wykorzystując możliwości systemu ERP firmy Knapheide konsultanci PlanetTogether zaprojektowali narzędzie do importowania danych dotyczących zleceń oraz dostępnych stanów magazynowych, a także narzędzie do eksportowania obliczeń PlanetTogether z powrotem do systemu ERP w postaci dat realizacji zleceń.
Intuicyjny interfejs typu “przeciągnij i upuść” od PlanetTogether znacznie ułatwił obsługę nowego narzędzia. Pracownicy zyskali natychmiastową informację zwrotną dotyczącą opóźnionych zleceń, które w systemie pojawiają się na czerwono. Co więcej, PlanetTogether optymalizuje harmonogramy, aby dotrzymać obiecanych terminów dostaw. “Dostarczamy systemowi informacje, które posiadamy, a on automatycznie proponuje optymalny harmonogram zgodny z deklarowanym terminem realizacji. Ręcznie nie udałoby się nam tego dokonać,” zaznacza Marx. Ekran planowania PlanetTogether jest wyświetlany na dużym monitorze w biurze brygadzisty. Przedstawiciele handlowi mają teraz dostęp do harmonogramu podczas rozmów z klientami.
Dzięki uwolnieniu się od pracy manualnej Knapheide jest w stanie obiecać klientom realne terminy realizacji zamówień. Szybka identyfikacja wąskich gardeł pozwala opracować odpowiedni plan działania dla poszczególnych działów: “Z wyprzedzeniem dostrzegamy, że dział lakierni będzie przeciążony pracą w nadchodzący wtorek, więc możemy oddelegować na ten dzień więcej pracowników”, wyjaśnia Marx.
Podczas planowania brane są pod uwagę umiejętności i możliwości każdego pracownika, co zapewnia idealny dobór osoby do powierzonego zadania. “W rezultacie poprawiła się nasza jakość”, mówi Marx.
“Oprogramowanie decyduje, komu najlepiej powierzyć konkretną rolę.”
Co więcej, w starym, manualnym systemie niemożliwe było przeprowadzanie analiz warunkowych. Obecnie Marx jest w stanie sprawdzić, jaki wpływ będzie miało dodanie drugiej zmiany lub zatrudnienie dodatkowego pracownika. “Możemy teraz podejmować strategiczne decyzje w celu usprawnienia naszych operacji,” dodaje Marx,
“Proaktywnie przygotowujemy się do przewidywanych wzrostów i spadków zapotrzebowania.”
“Obecnie planowanie zajmuje około 15 minut. Inwestycja w PlanetTogether zwróciła się w ciągu sześciu miesięcy!”
Zobacz również
Chcesz dowiedzieć się więcej? Odwiedź naszą Bazę Wiedzy, gdzie znajdziesz artykuły i webinary przygotowane przez ekspertów, które pozwolą Ci poszerzyć swoją wiedzę.
Umów się na bezpłatną prezentację lub rozmowę na wskazany przez Ciebie temat.
Jak przebiega proces bezpłatnej konsultacji?

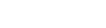
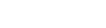
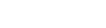
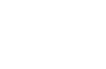
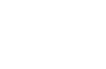
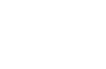
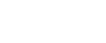
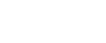
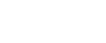
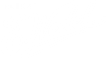
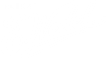
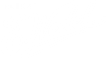



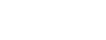
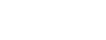
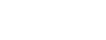



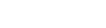
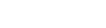
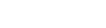
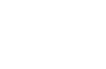
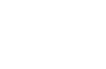
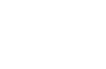
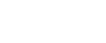
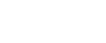
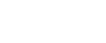
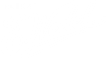
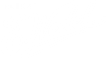
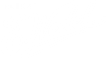



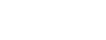
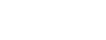
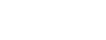



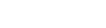
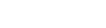
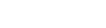
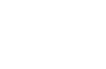
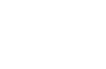
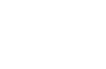
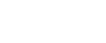
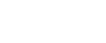
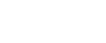
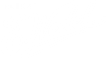
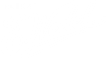
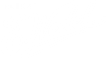



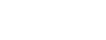
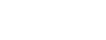
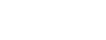



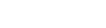
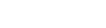
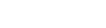
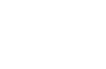
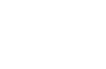
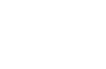
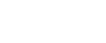
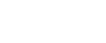
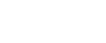
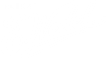
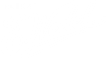
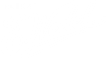



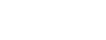
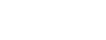
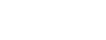