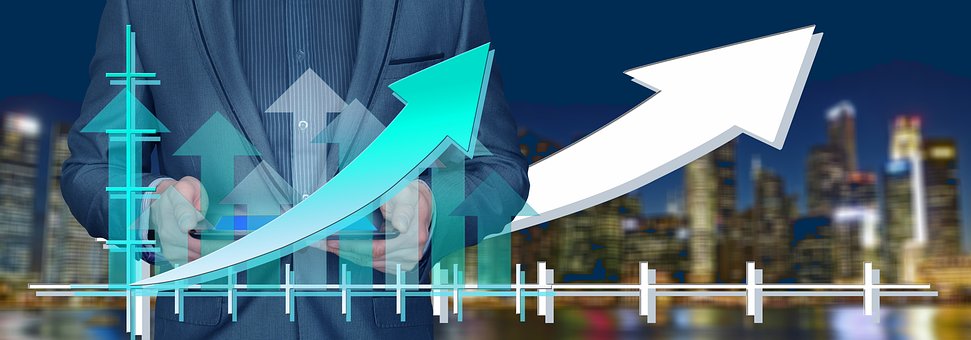
Wiarygodne dane produkcyjne. Jak je zbierać, a potem kwalifikować?
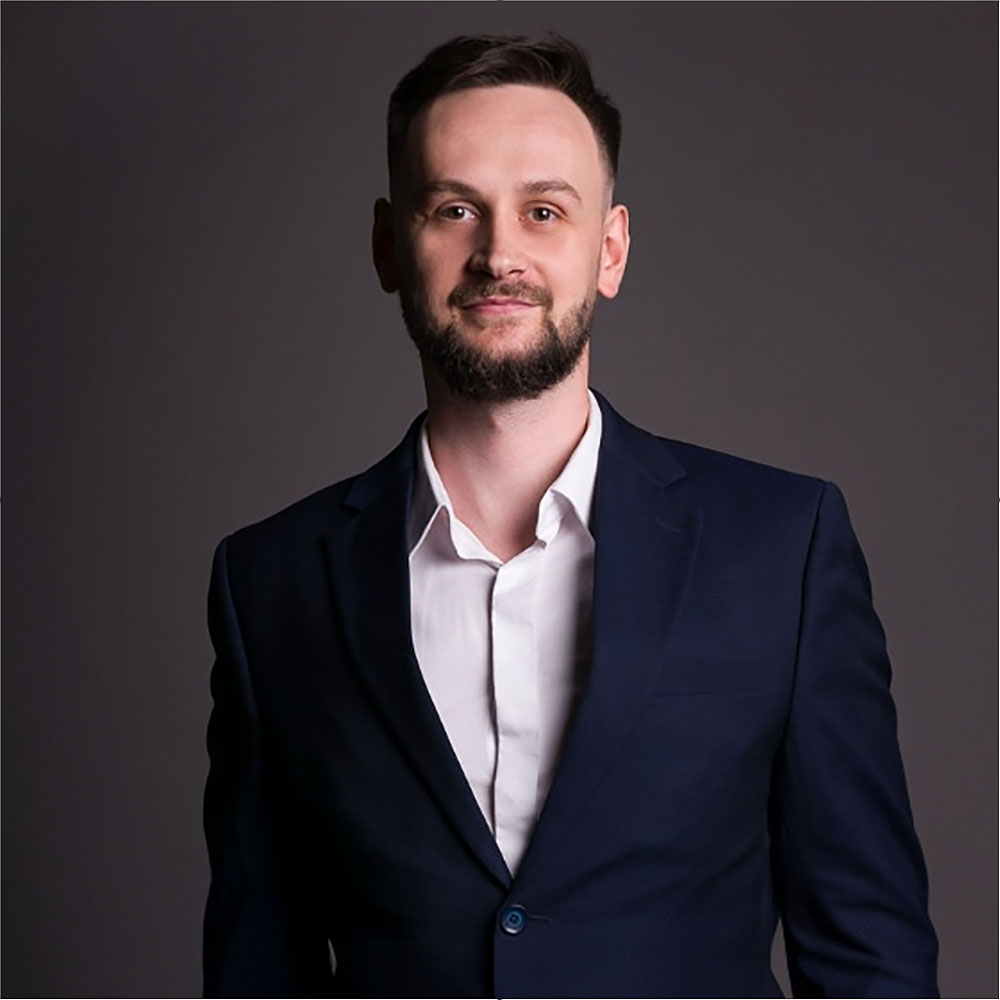
Adrian Szczypski
Stopień zaawansowania technologicznego zakładu przemysłowego czy fabryki ma bezpośrednie przełożenie na sposoby zbierania danych produkcyjnych. A to z kolei wpływa na kluczowe wskaźniki produkcyjne, takie jak OEE. Jest to o tyle istotne, że dopiero odpowiednie zdefiniowanie i zaklasyfikowanie poszczególnych elementów pozwala nam uzyskać wiarygodne dane produkcyjne.
Czy istnieje jeden najlepszy sposób na zbieranie danych produkcyjnych ze stanowisk? Wszystko tak naprawdę zależy od stopnia i sposobu cyfryzacji danego stanowiska.
Dane mogą być zbierane ręcznie. Warto jednak podkreślić, że nawet gdy mamy do czynienia z całkowicie manualnym stanowiskiem, nie wyklucza to zbierania niektórych danych w sposób automatyczny. Takimi informacjami mogą być pewne zdarzenia, jak np. przejście zmiany produkcyjnej według jakiegoś harmonogramu, definicje przerw produkcyjnych, harmonogramy serwisowe realizowane według pewnego kalendarza – za pomocą tego typu zdarzeń możemy automatyzować pewne rzeczy na stanowiskach manualnych.
Wszędzie tam, gdzie mamy niski poziom dostępu do informacji, dobrze sprawdzą się hybrydowe sposoby zbierania danych produkcyjnych. Niski poziom informacji w tym przypadku oznacza, że maszyna jest w stanie dostarczyć pewne, bardzo proste sygnały. To może być „start”, „stop”, „dodanie sztuki” itd. W takim przypadku możemy wykorzystać pochodne tych sygnałów, czyli z jednego sygnału wyciągnąć więcej informacji, np. że maszyna pracuje, ma postój, aktualnie produkuje. Takie podstawowe dane mogą być później doprecyzowane przez operatora.
Najlepiej sytuacja wygląda tam, gdzie mamy maszyny z wysokim poziomem dostępu do informacji. Dzięki temu możemy wykorzystywać automatyczne zbieranie danych produkcyjnych, dzięki czemu nie tylko uzyskujemy więcej informacji, ale też odciążamy operatorów, którzy mogą skupić się na produkcji i nie muszą tracić czasu na doprecyzowywanie stanów maszyn. Co więcej, gdy zbieranie danych produkcyjnych odbywa się automatycznie, w czasie rzeczywistym, eliminujemy ryzyko pojawienia się nieścisłości czy pomyłek związanych z ręcznym zapisywaniem, i w efekcie uzyskujemy wiarygodne informacje, które pozwalają na zarządzanie przez fakty.
Bardzo często pracownicy produkcji lub osoby nią zarządzające zastanawiają się, jak powinny być traktowane dane produkcyjne dotyczące przezbrojeń. Czy wliczać je do czasu dostępności jako pracę, jako postój nieplanowany, czy może jako postój planowany?
Nie ma jednej właściwej odpowiedzi na to pytanie. Najbardziej uniwersalne jest zaliczanie przezbrojeń do postojów nieplanowanych. Dlaczego? Jeśli nie mamy standardowych czasów przezbrojeń, to traktowanie ich jako czas planowany sprawi, że stracimy o nich informacje. Również zdefiniowanie przezbrojeń jako pracy nie jest najlepszym rozwiązaniem – zwiększylibyśmy w ten sposób czas, ale obniżylibyśmy wydajność, co miałoby wpływ na ogólny czas rozrachunkowy.
Przezbrojenia najlepiej kwalifikować jako przestoje nieplanowane
Aby optymalizować przezbrojenia zaleca się stosowanie różnych metod. Jedną z nich jest SMED [Single Minute Exchange of Die], która pozwala na skracanie czasów przezbrojeń maszyn i urządzeń. Etapem wyjściowym tej metody jest przede wszystkim rejestrowanie operacji przezbrojeń, tak żeby w ogóle mieć o nich wiedzę.
Pomocna może się okazać automatyzacja standardowych czasów przezbrojeń, która pozwoli badać etapy przezbrojenia. Jak to zrobić? Najpierw określa się standardowy czas na przezbrojenie, a po jego przekroczeniu automatycznie następuje przepięcie na stan danego stanowiska, który już inaczej wpływa na wskaźnik OEE. Dzięki temu wiemy, że przezbrojenie w ogóle nastąpiło, jesteśmy w stanie je śledzić, a później przeanalizować ile ono trwało i jaki miało wpływ na ogólne rozrachunki całego wskaźnika.
Kolejnym elementem procesu produkcyjnego, który bywa kłopotliwy do zaklasyfikowania są odpady. Często grafy dotyczące obsługi jakościowej poszczególnych sztuk są bardzo skomplikowane. Pojawiają się więc pytania: 1. czy wszystko powinno iść do tzw. „scrapu” [ang. scrap: złom, odpadek, ścinek itp.], 2. czy każda „zła” sztuka musi trafić na odpad i nie powinna już nigdy więcej być uwzględniana przy wyliczaniu wydajności? Nie do końca. Co, jeśli okaże się później, że to jednak nie był „scrap” i zechcemy go przemianować? Takie przypadki są na tyle częste, że należy brać je pod uwagę.
Czy odpady zatem wpływają na wydajność? Teoretycznie nie powinny, bo wydajność jest liczona per wszystkie sztuki. Przy wyliczaniu wskaźnika OEE bardzo ważne jest, żeby jedna strata wpływała tylko na jedną składową wskaźnika. Trzeba więc uważać, żeby nie dublować wpływu danego czynnika na kilka składowych wskaźnika OEE.
Kategoryzacja odpadów, źródło ImFactory
Warto też zwrócić uwagę na re-kwalifikacje. Przy zmianie statusu, np. przy naprawie danej sztuki, trzeba ponownie przeliczyć wskaźnik jakościowy, aby uwzględnić naprawioną sztukę. Podobnie należy uważać też na tzw. re-worki i naprawy. Wszelkie naprawy będą miały wpływ na wydajność. Czas wyprodukowania będzie wtedy dłuższy i trzeba go odpowiednio uwzględnić, ale to już nie jest zła sztuka i trzeba ją przemianować na sztukę dobrą
Kolejnym ciekawym przypadkiem, który budzi sporo wątpliwości, gdy chcemy uzyskać wiarygodne dane produkcyjne, jest kwalifikacja mikroprzestojów, z którymi pojawiają się kolejne pytania. Na jaką składową wskaźnika OEE powinien wpływać spadek tempa produkcji? Na dostępność? A może na wydajność? Wszystko zależy od konkretnej sytuacji.
Spadek tempa produkcji – wydajność czy dostępność?, źródło: ImFactory
Mikroprzestoje powinny mieć odzwierciedlenie w dostępności wtedy, gdy informacje o nich zbierane są w sposób automatyczny. Jeżeli jesteśmy w stanie w jasny sposób określić, czym jest mikroprzestój i co on dla nas oznacza, wtedy automat na podstawie zdefiniowanych przez nas wyznaczników przekaże nam informacje o mikroprzestojach, które powinny być uwzględnione w dostępności.
W przypadku, kiedy mikroprzestoje są definiowane ręcznie, należy uwzględniać je w wydajności. Dlaczego? Aby nie dokładać pracy operatorom. Takich mikroprzestojów może być sporo i bywają one bardzo krótkie, a nie chodzi przecież o to, by pracownicy obsługujący stanowiska mieli jeszcze więcej pracy.
Pułapką podczas zbierania danych produkcyjnych może okazać się duplikowanie strat. To wspomniane już wcześniej, wielokrotne kwalifikowanie tej samej straty. Przy definiowaniu poszczególnych wskaźników trzeba zachować szczególną czujność, aby nie ustawić systemu w taki sposób, że jedna strata będzie mieć wpływ na kilka różnych wskaźników.
Przykładowo, gdybyśmy przy liczeniu wydajności brali pod uwagę tylko dobre sztuki, a nie wszystkie wyprodukowane, to dublowalibyśmy straty. Analogiczny przykład można podać w przypadku przezbrojeń – jeśli zdefiniujemy je jako pracę stanowiska, to wpłyną one zarówno na dostępność, jak i na wydajność.
Zatem jeśli chcemy uzyskiwać wiarygodne dane, trzeba unikać duplikowania strat. Należy dążyć do tego, aby jedna strata wpływała tylko na jeden wskaźnik.
Co rozumiemy przez „wykorzystanie maszyny”? To może dotyczyć przeróżnego rodzaju maszyn czy stanowisk produkcyjnych, mogą być to także stanowiska wysoce zautomatyzowane.
Załóżmy, że mamy stanowisko produkcyjne, które nazwiemy „stanowiskiem X”. Dostajemy sygnał, że pojawiała się na nim awaria. Jednak nie wiemy, co jest przyczyną tego stanu. Maszyna daje nam sygnał, że jest w awarii, coś się zacięło, ale to dopiero pracownik musi określić, jaka jest tego przyczyna. W tym przypadku operator doprecyzowuje, że było to uszkodzenie wału.
Analiza danych produkcyjnych będzie ułatwiona, jeśli do oznaczania takich stanów wykorzystamy dodatkowe flagi, np. znaczniki przestoju. To są dodatkowe znaczniki, które umożliwiają dalszą analizę wskaźników i stanów maszyn. Sygnały z maszyny mają za zadanie powiedzieć, że coś jest nie tak, ale niekoniecznie zdefiniują co dokładnie. Analiza poprzez dodatkowe znaczniki przyczyny przestoju i ich kwalifikacje, pomaga dojść do tego dlaczego np. nasza dostępność spadła.
Hierarchia klasyfikacji „wykorzystania maszyny” (dostępność), źródło: ImFactory
Często najtrudniejszym do zdefiniowania elementem jest nominalne tempo produkcji. Jest ono istotne w kontekście gromadzenia danych produkcyjnych, ponieważ pokazuje stan, do którego dążymy. Problem z jego zdefiniowaniem pojawia się nie dlatego, że jest to trudne, ale często zakłady czy organizacje, które dopiero wprowadzają wskaźnik OEE nie miały wcześniej zdefiniowanych nominalnych czasów produkcyjnych. Nominalne tempo produkcji może zależeć od:
- maszyny,
- produktu,
- materiału,
- doświadczenia kadry,
- dostępności kadry,
- połączenia tych elementów.
Nominalne tempo produkcji powinno uwzględniać indywidualne przypadki, które pojawiają się w zależności od charakteru produkcji czy rodzaju wykorzystywanych maszyn itp. Przykładowo jedna maszyna produkuje produkt X z pewną prędkością, a druga maszyna ten sam produkt X może produkować z inną prędkością.
Jak zatem zdefiniować nominalne tempo produkcji? Jest kilka dobrych praktyk, które można zastosować:
Wytyczne producenta
Zazwyczaj producenci powinni wskazać, z jaką nominalną prędkością powinna produkować dana maszyna. Trzeba jednak mieć świadomość, że jest to wartość uzyskiwana w idealnych warunkach, więc możemy ją zastosować bardziej jako element wyjściowy do obliczenia naszego nominalnego tempa.
Doświadczenie zespołu
Niezastąpionym elementem do określenia nominalnego tempa produkcji jest doświadczenie operatorów, liderów czy osób, które pracują na danej maszynie lub stanowisku. To właśnie oni najlepiej wiedzą, na co należy uważać, co może obniżyć wydajność, a co ją podnieść.
Metoda BoB
Metoda BoB, czyli Best of Best – mierzymy, analizujemy i wybieramy 5 najlepszych wyników z danego okresu, a następnie wyciągamy z nich średnią. Statystycznie będzie to najlepsze dla pomiaru, ponieważ odfiltrujemy wszelkie nieprawidłowości, które zaburzały tempo produkcji.
Ciągłe sprzężenie zwrotne
To rozwiązanie, które można zastosować, ale trzeba mieć na uwadze, że ten wskaźnik może się dość często zmieniać i wpływać na nasze przyszłe pomiary. Dlatego powinien być on w odpowiednio szerokim horyzoncie czasowym. Jeśli przyjęty okres będzie za krótki, nie będziemy mogli porównać np. dnia do dnia, a nasze wartości nominalne będą się trochę zmieniały.
Samo zbieranie danych produkcyjnych to jeszcze za mało, aby uzyskać naprawdę wiarygodne informacje. Trzeba mieć świadomość tego, gdzie mogą pojawić się nieścisłości i dążyć do ich wyeliminowania poprzez właściwe definiowanie i klasyfikowanie poszczególnych czynników. Dopiero takie podejście pozwoli na uzyskanie wiarygodnych danych, które będą solidną podstawą zarzadzania przez fakty.
Absolwent Automatyki i Robotyki na Politechnice Gdańskiej. Project Manager z bagażem doświadczeń w projektach związanych z wdrożeniami systemów IT na produkcji. Poprzez ciągłą weryfikację potrzeb klienta wraz z zespołem z sukcesami buduje produkty, które umożliwiają szybkie osiąganie korzyści biznesowych w firmach produkcyjnych. Dzięki swojej specjalizacji odpowiedzialny jest także za dobór zasobów IT oraz zarządzanie wymaganiami klienta w zespole Improvement Factory [ImFactory].
Zobacz również
Chcesz dowiedzieć się więcej? Odwiedź naszą Bazę Wiedzy, gdzie znajdziesz artykuły i webinary przygotowane przez ekspertów, które pozwolą Ci poszerzyć swoją wiedzę.
Umów się na bezpłatną prezentację lub rozmowę na wskazany przez Ciebie temat.
Jak przebiega proces bezpłatnej konsultacji?

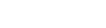
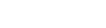
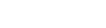
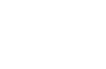
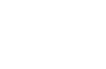
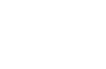
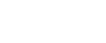
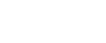
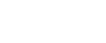
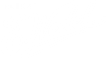
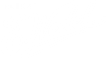
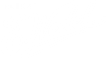



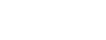
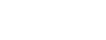
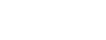



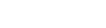
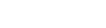
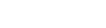
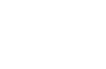
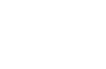
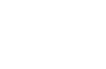
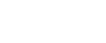
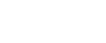
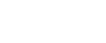
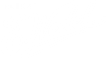
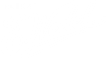
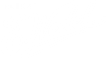



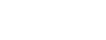
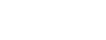
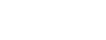



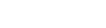
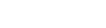
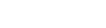
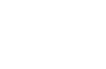
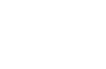
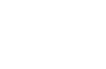
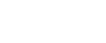
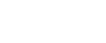
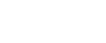
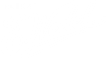
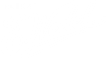
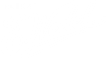



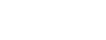
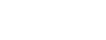
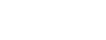



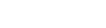
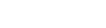
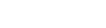
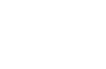
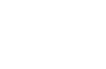
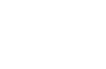
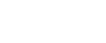
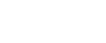
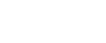
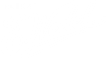
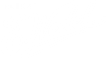
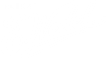



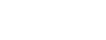
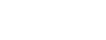
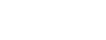