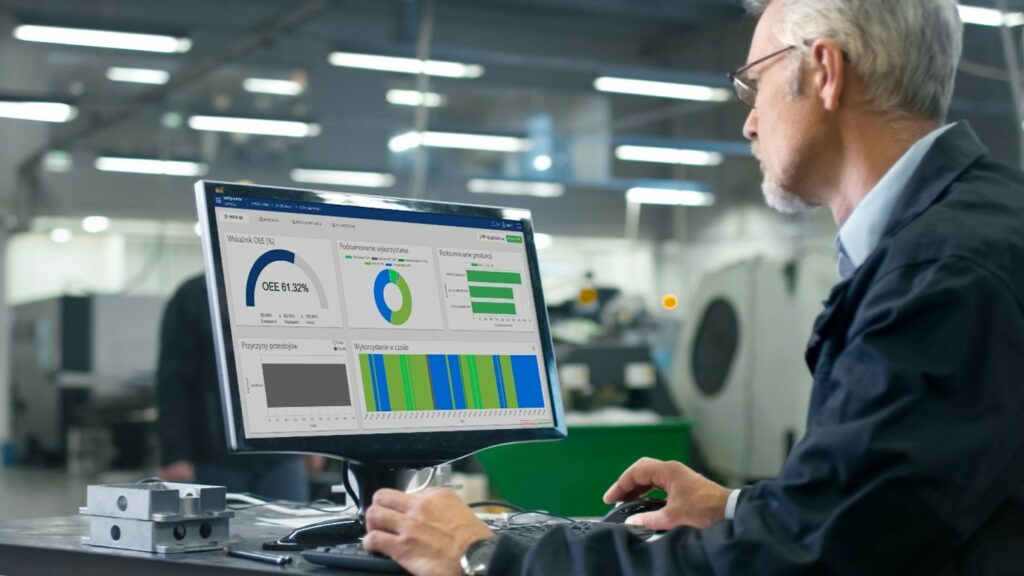
Wskaźnik OEE, czyli jak za pomocą dostępności, wydajności i jakości policzyć efektywność wyposażenia?
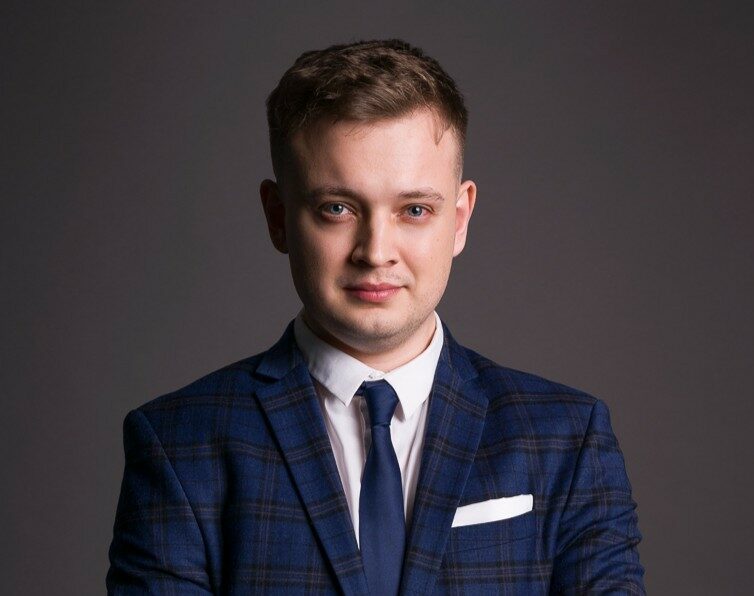
Michał Zieliński
Oczywiście istotne jest to, jak skonstruowany jest wskaźnik OEE. Według jakiego wzoru go obliczyć? Jakie są jego odmiany? Jednak to nie definicje ani wzory są tu najważniejsze. Podstawowe pytanie brzmi: po co w ogóle wskaźnik ten chcemy mierzyć? Podobnie jak w projektach, tak też w systemach wskaźnikowych najważniejsze jest, aby określić cel, wartość i rezultat, który chcemy osiągnąć przez nasze działania.
Zacznijmy od przykładu. Wyobraźmy sobie, że kupiliśmy zupełnie nową maszynę. Czekaliśmy na nią długie miesiące, w dodatku nie był to tani zakup. Producent zadeklarował, że za pomocą tej maszyny będziemy w stanie wyprodukować aż 1000 elementów w ciągu każdej przepracowanej godziny. Oczekiwaliśmy zatem, że zarówno czas oczekiwania, jak i cała inwestycja szybko się zwróci. Okazało się jednak, że realnie uzyskujemy zaledwie 554 sztuk na godzinę. Pojawia się pytanie: „Co poszło nie tak?”
Dr Peter Drucker, jeden z najwybitniejszych ekspertów i teoretyków zarządzania, autor wielu książek, w tym Praktyki zarządzania czy Skutecznego managera mawiał, że „Jeśli nie możesz czegoś zmierzyć, nie możesz tego udoskonalić”. Dlatego też zmierzenie naszej maszyny pozwoli nam nie tylko odpowiedzieć na pytanie dlaczego nie produkuje ona takiej ilości, jak deklarował producent, ale przede wszystkim, co możemy zrobić, żeby pracowała zgodnie z oczekiwaniami. Taką wiedzę da nam właśnie wskaźnik OEE.
OEE to skrót od angielskiego Overall Equipment Effectiveness, czyli „Całkowita Efektywność Wyposażenia”. Jeśli chcemy zmierzyć efektywność naszych maszyn i urządzeń, potrzebujemy wyliczyć właśnie wskaźnik OEE. Definiowany jest jako iloczyn trzech składowych: dostępności, wydajności i jakości. Choć OEE można wyliczyć manualnie, coraz częściej firmy produkcyjne stosują specjalistyczne systemy informatyczne, np. klasy MES, które monitorując prace maszyn w czasie rzeczywistym, w dowolnym momencie wyliczają także wskaźniki produkcyjne. Jeśli taki system został poprawnie wdrożony i jest stabilny, obliczanie OEE następuje całkowicie automatycznie, a my mamy pewność, że otrzymane wyniki są rzetelne.
Wróćmy do naszej maszyny. Podłączyliśmy ją do systemu monitorującego. Dostaliśmy informację, że wskaźnik OEE jest na poziomie 55% – co stanowi tylko połowę wartości nominalnej. To dla nas sygnał, że coś można poprawić. Pytanie tylko co? Aby na nie odpowiedzieć, przeanalizujmy dokładniej poniższy raport. Możemy w nim zobaczyć ile wyniosły poszczególne składowe wskaźnika. Okazuje się, że dostępność była na poziomie 95%, jakość także wyniosła prawie 95%. To bardzo dobre wyniki. Jednak wydajność to już jedynie 61% – i to ona jest polem do poprawy, bo w jej zakresie następują największe straty. To wskazówka do podjęcia konkretnych działań, by poprawić wynik.
Wiemy już, że wskaźnik OEE zbudowany jest z trzech składowych. Przyjrzyjmy się czym one tak naprawdę są, o czym nas informują i co możemy zrobić, aby przeciwdziałać stratom w ich zakresie.
Dostępność – pierwsza składowa OEE
Pierwszy współczynnik, czyli dostępność mówi nam o czasie związanym z brakiem możliwości podjęcia pracy. Opierając się dalej na naszym przykładzie z nieefektywną maszyną, załóżmy, że pracujemy na jedną zmianę, przez 8 godzin dziennie. W czasie tej zmiany mamy jedną 20 minutową przerwę obiadową, dwie przerwy na rozpoczęcie i zakończenie zmiany oraz jedną 15 minutową przerwę na TPM. Po odjęciu tych przerw uzyskujemy czas dostępny na pracę.
Niestety świat nie jest idealny. Załóżmy więc, że w ciągu dnia mieliśmy jedną 10 minutową awarię – zaciął się podajnik materiału, potem nastąpiła krótka przerwa w zasilaniu – skutkowało to 2 minutami dodatkowego postoju, a 3 razy maszyna się zatrzymała na 2 minuty, ale operator nie doprecyzował dlaczego, a żadnego kodu błędu automatycznego nie było.
Dopiero po odjęciu tych nieplanowanych przestojów zostaje nam rzeczywisty, operacyjny czas pracy. Wchodzący zatem w skład OEE wskaźnik dostępności to nic innego jak stosunek czasu pozostałego po odjęciu strat do czasu, który przeznaczyliśmy, czy też udostępniliśmy, do produkcji. Dla naszego hipotetycznego przypadku zamieniamy godziny na minuty i wyliczamy wartość procentową stosunku tych dwóch wartości, co w efekcie daje nam dostępność na poziomie 95%.
Wydajność – druga składowa OEE
Wydajność, czyli kolejny współczynnik OEE, mówi nam o stratach związanych z utratą tempa produkcyjnego. Cały czas pracujemy, ale poniżej normy. Podstawą do wyliczenia wydajności jest czas operacyjny, czyli ten, który był poświęcony na pracę. Od niego odejmujemy czas, który nadmiarowo poświęciliśmy na produkcję np. w wyniku nieefektywności operatora lub złego ustawienia maszyny albo mikroprzestojów.
Pozostaje nam tzw. czas netto, czyli czas, w którym powiedzmy, że produkowaliśmy na 100%. Wydajność to wynik produkcyjny, czyli cała nasza produkcja, zarówno dobra, jak i wadliwa, podzielona przez potencjalnie możliwą do wyprodukowania ilość, w czasie operacyjnym. W naszym przykładzie, jak wspomnieliśmy na początku, nominalne tempo to 100 sztuk na godzinę. Czas operacyjny wyniósł 6,9 godziny. Więc nasza teoretyczna produkcja to iloczyn tych wartości – 6900 sztuk. Jednak rzeczywista, zarejestrowana produkcja w przeciągu godziny to 4225. Iloraz tych dwóch wartości daje nam 61,23% i to właśnie nasza wydajność.
Dzięki analizie składowych wskaźnika OEE odkryliśmy więc, gdzie leży nasz problem. Jak mu przeciwdziałać? Jest kilka sposobów na zwiększenie wydajności. Można m.in.:
- ograniczyć liczbę zadań w toku,
- usprawnić przepływ materiałów i półwyrobów,
- zająć się identyfikacją i eliminacją wąskich gardeł, zwłaszcza na liniach produkcyjnych,
- zautomatyzować procesy,
- zainwestować w nowe maszyny i urządzenia.
Jakość – trzecia składowa OEE
Trzeci współczynnik OEE, czyli jakość, mówi nam o stratach związanych ze złą produkcją lub z nadprodukcją w wyniku właśnie złej produkcji. Podstawą do wyliczenia tego składnika jest czas netto, czyli to, co pozostało po odjęciu strat wydajnościowych z poprzedniego kroku. Jako straty jakości traktujemy głównie braki, błędy np. powstałe w wyniku montażu, odrzuty po rozruchu, odrzuty w procesie czy wszelkiego rodzaju przeróbki. To wszystko odejmujemy od czasu netto. Wynik, który uzyskujemy to ostateczny, efektywny czas pracy.
W takim rozumieniu jakość jest ilorazem dobrej produkcji do całości produkcji. Dla naszego przypadku zarejestrowaliśmy 4225 sztuk, z czego dobrej produkcji było 4005 sztuk. Więc jakość w naszym przykładzie wyniosła 94,97%.
Jak podnosić jakość? Tu z pomocą przychodzą takie narzędzia jak np.:
- Poka–Yoke, czyli projektowanie procesów w sposób odporny na błędy, jak np. przysłowiowa karta sim, której dzięki ściętemu narożnikowi nie da włożyć w niewłaściwy sposób.
- Jidoka, czyli wbudowywanie w proces metod pozwalających na wykrywanie i poprawianie nieprawidłowości, tak, żeby one nie przechodziły dalej w procesie.
- Analiza Przyczyny Pierwotnej, czyli wyszukiwanie najczęstszych defektów i określanie ich przyczyn, aby eliminować je z procesu.
- Standaryzowanie Pracy i stosowanie takich rozwiązań jak One Point Lessons, które wspierają zapewnienie jakości już w procesie.
Jak już wspomnieliśmy, wzór na OEE bierze się z wymnożenia jego składowych. Jednak oprócz wyników, możemy też spojrzeć na straty – to częste podejście w przypadku wskaźnika OEE. W takim kontekście możemy mówić o całkowitej stracie, utracie dostępności, spadku wydajności oraz brakach jakościowych.
Spójrzmy na wskaźnik OEE przez pryzmat tylko zaplanowanego czasu pracy. Jeżeli od tego czasu odejmiemy wszelkie nieplanowane przerwy, zostanie nam rzeczywisty czas pracy. Jeśli dalej będziemy odejmować czas poświęcony na pracę nieefektywną, zostanie nam czas, w którym produkujemy wyroby z zadaną prędkością. Idąc jeszcze krok dalej i odliczając czas poświęcony na produkcję wadliwą, złą, wybrakowaną, zostanie nam wtedy właściwy, efektywny czas pracy, czyli ten poświęcony na produkcję dobrą jakościowo. To właśnie nasz wskaźnik OEE z tym, że wyliczony z perspektywy strat czasu.
Nie tylko wskaźnik OEE mówi nam o efektywności produkcji. Oprócz niego mamy też inne wskaźniki m.in.– OOE (Overal Operation Effectiveness) I TEEP (Total Effective Equipment Performance).
Wszystkie 3 wskaźniki – OEE, TEEP i OOE, uwzględniają zarówno jakość, wydajność i dostępność maszyny. Zasadnicza różnica pomiędzy nimi jest taka, jak definiujemy dostępność w przypadku każdego z nich.
- Maksymalna dostępność dla OEE, czyli ogólnej dostępności wyposażenia, to czas produkcyjny, czyli czas maszyny zaplanowany na pracę.
- Maksymalna dostępność dla OOE to czas zaplanowany (czyli czas pracy maszyn tak jak dla OEE), ale rozszerzony dodatkowo o czas niezaplanowany na produkcję, w którym odbywają sięp.p. planowane przerwy, TPM–y czy inne akcje utrzymaniowe.
- Maksymalna dostępność dla TEEP zakłada pracę maszyny przez 24 godziny, 7 dni w tygodniu, 365 dni w roku – jest to więc wskaźnik najszerszy.
Wskaźnik OEE i jego składowe odgrywają niebagatelną rolę w monitorowaniu procesów produkcyjnych. Co więcej, OEE można mierzyć tak dla poszczególnych maszyn, jak i całych linii produkcyjnych. Dodatkowo, stałe monitorowanie poziomu OEE pozwala trzymać rękę na pulsie i w razie problemów z efektywnością produkcji, szybko znaleźć ich źródło i podjąć stosowne działania. Po to, by wszystko było tak, jak być powinno, czyli zgodnie z założeniami i oczekiwaniami .
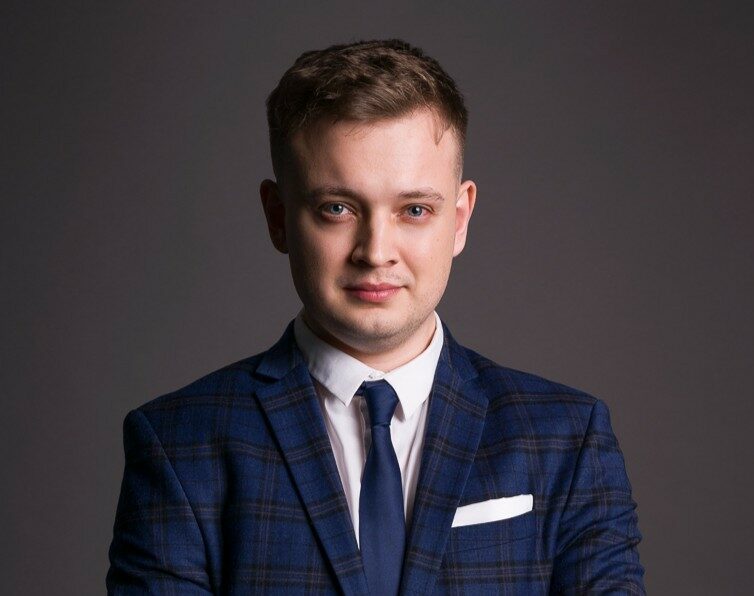
W ImFactory pełni również funkcję Project Managera i konsultanta. Odpowiada za kształtowanie wizji rozwoju systemów IT w środowiskach produkcyjnych. Wspiera przedsiębiorstwa w ocenie ich dojrzałości cyfrowej oraz pomaga im zaplanować cyfrową transformację.
Absolwent Politechniki Gdańskiej. Ukończył Automatykę i Robotykę oraz studia podyplomowe Lean Six Sigma Black Belt. Autor licznych publikacji spod znaku #EfektywnaCyfryzacja. Dzieli się wiedzą na temat efektywności produkcji, cyfrowej transformacji, systemów MES/MOM oraz map drogowych cyfryzacji.
Łączy wiedzę techniczną ze zrozumieniem procesów biznesowych. Dzięki temu skutecznie wspiera przedsiębiorstwa w ich drodze do Cyfrowej Fabryki.
Artykuły i webinary Michała Zielińskiego dostępne są w Bazie Wiedzy ImFactory.
Zobacz również
Chcesz dowiedzieć się więcej? Odwiedź naszą Bazę Wiedzy, gdzie znajdziesz artykuły i webinary przygotowane przez ekspertów, które pozwolą Ci poszerzyć swoją wiedzę.
Umów się na bezpłatną prezentację lub rozmowę na wskazany przez Ciebie temat.
Jak przebiega proces bezpłatnej konsultacji?

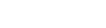
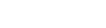
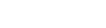
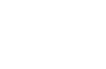
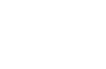
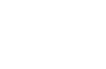
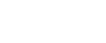
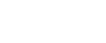
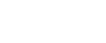
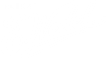
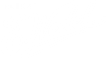
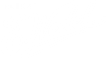



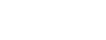
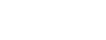
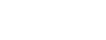



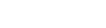
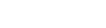
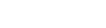
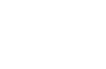
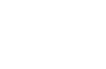
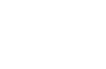
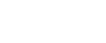
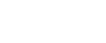
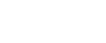
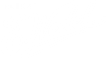
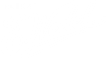
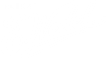



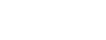
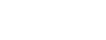
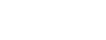



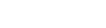
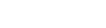
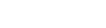
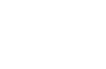
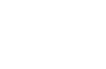
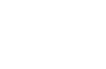
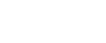
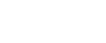
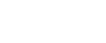
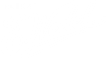
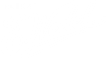
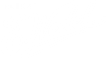



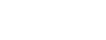
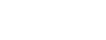
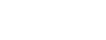



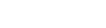
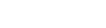
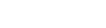
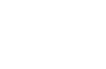
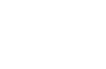
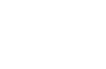
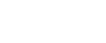
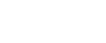
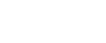
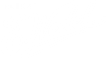
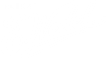
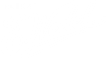



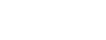
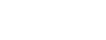
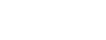