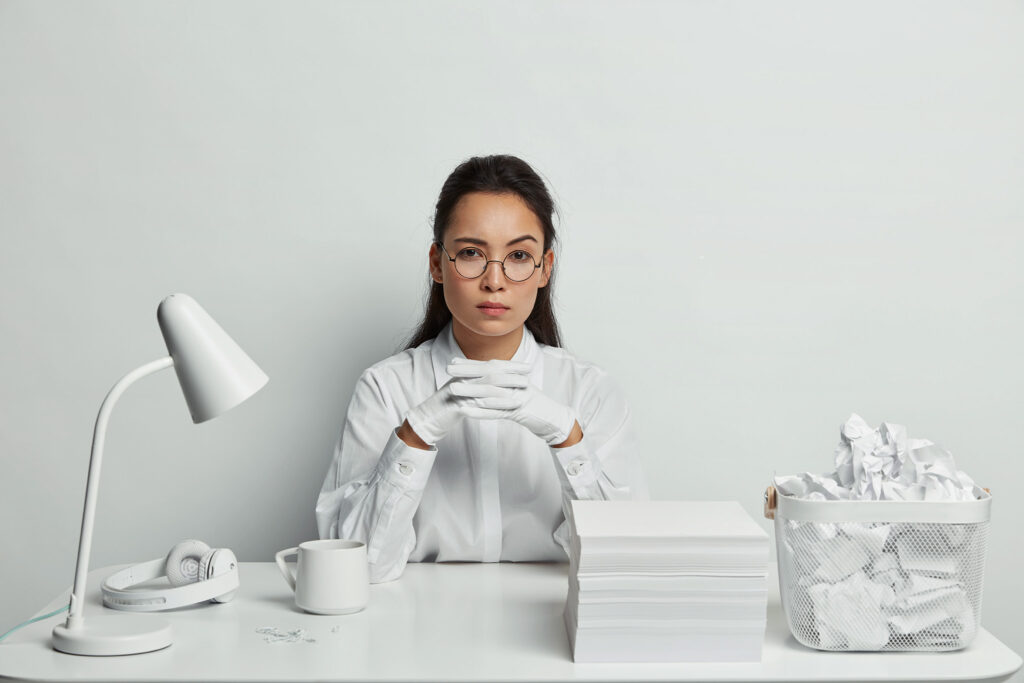
Implementacja koncepcji 5S z wykorzystaniem Lean Management i MES – jak to zrobić?
Czy porządek i organizacja w mogą pomóc w poprawie produktywności i podnieść jakość pracy? Oczywiście, że tak. Doskonale wiedzą o tym japońskie firmy, które już od dziesięcioleci stosują narzędzie nazywane 5S. Metoda ta pomaga stworzyć efektywne i bezpieczne stanowiska pracy oraz utrzymać je w takim stanie, co przynosi szereg korzyści. Metoda 5S jest szczególnie popularna w branżach, gdzie organizacja i porządek są kluczowe, takich jak przemysł produkcyjny, opieka zdrowotna czy obszar usług.
Metoda 5S to narzędzie zarządzania jakością, które zostało stworzone w Japonii i jest używane w wielu organizacjach na całym świecie, zwłaszcza w przemyśle produkcyjnym. Nazwa „5S” pochodzi od japońskich słów, które opisują pięć kroków tej metody. Każda litera „S” reprezentuje jeden z tych kroków:
Seiri (sortowanie): Pierwszym krokiem jest identyfikacja i wyeliminowanie zbędnych przedmiotów i materiałów z miejsca pracy. Cel to zachowanie tylko tych rzeczy, które są niezbędne do wykonywania pracy.
Seiton (systematyzacja): Ten krok polega na ustaleniu stałych miejsc dla pozostałych, niezbędnych przedmiotów i materiałów. Celem jest uporządkowanie miejsca pracy w taki sposób, aby łatwo można było znaleźć potrzebne przedmioty bez marnowania czasu na ich szukanie.
Seiso (czyszczenie): W tym etapie skupiamy się na zachowaniu czystości i porządku w miejscu pracy. To oznacza regularne czyszczenie i utrzymanie wszystkich obszarów w jak najlepszym stanie.
Seiketsu (standaryzacja): Tutaj wprowadza się standardy i procedury, które pomagają utrzymać osiągnięty porządek i czystość. Dzięki temu pracownicy łatwiej przestrzegają 5S w codziennej pracy.
Shitsuke (samodyscyplina): Ostatni krok to utrzymanie i ciągłe doskonalenie wdrożonych zmian. Wprowadzenie 5S w firmie ma na celu stworzenie kultury pracy, która promuje dbałość o porządek, czystość i skuteczność w organizacji.
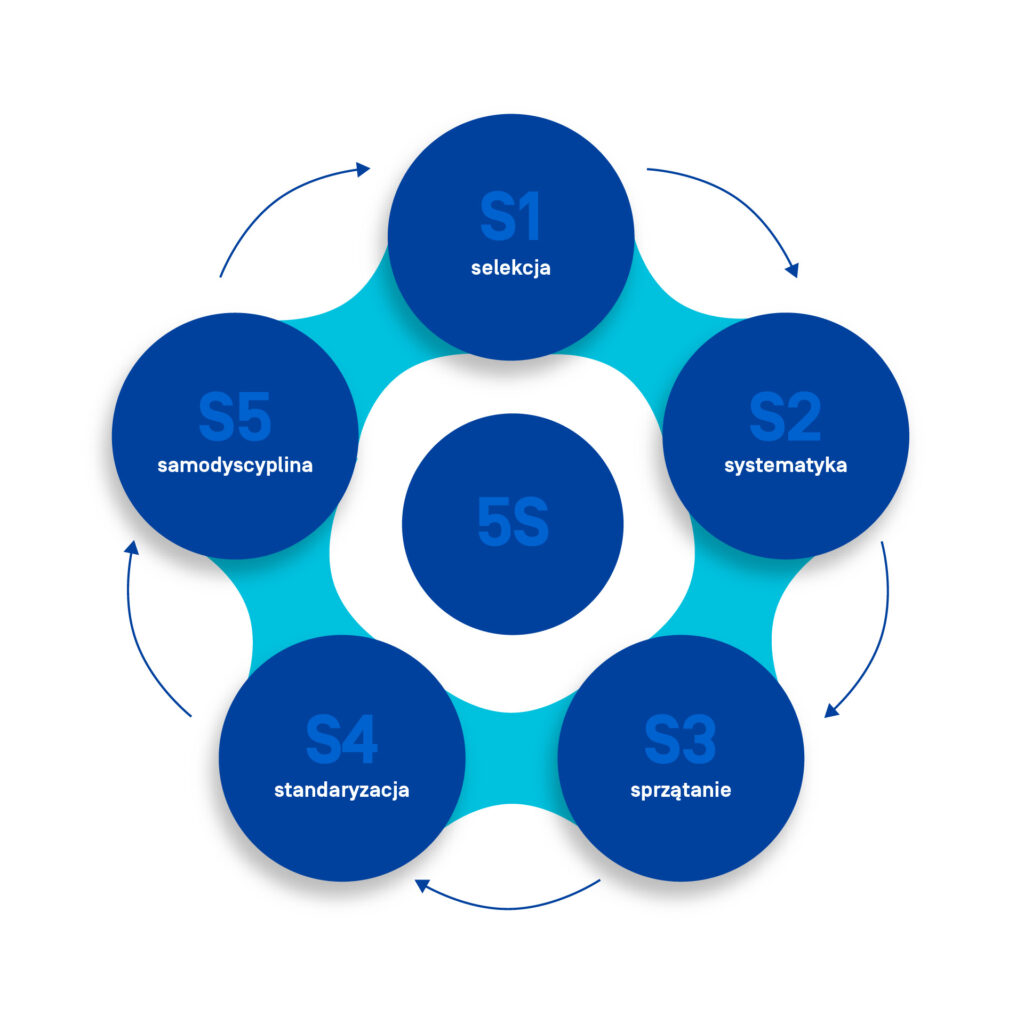
Lean Management, czyli inaczej szczupłe zarządzanie, to strategia i filozofia biznesowa, która skupia się na eliminacji marnotrawstwa i optymalizacji procesów w celu osiągnięcia większej efektywności operacyjnej, a zarazem dostarczeniu klientowi maksymalnej wartości.
Jedną z podstawowych technik tego podejścia jest właśnie metoda 5S, która pozwala skutecznie wdrażać najważniejsze zasady szczupłego zarządzania. 5S w Lean Management pomaga zorganizować miejsce pracy w sposób, który minimalizuje straty czasu wynikające z nieporządku, braku dostępu do narzędzi czy potrzeby szukania materiałów, co przekłada się na podniesienie efektywności.
Również bardzo ważne w Lean eliminowanie marnotrawstwa, czyli unikanie wszelkich działań, które nie dodają wartości dla klienta, jest możliwe przy pomocy 5S, ponieważ unika się nadmiernego składu, niepotrzebnych ruchów, oczekiwania na materiały itp.
Czyste i zorganizowane miejsce pracy ułatwia kontrolę jakości oraz zapobiega pomyłkom wynikającym z nieporządku i chaosu. Łatwiej jest zidentyfikować błędy, uszkodzenia czy problemy jakościowe, co przekłada się na dostarczenie klientowi lepszych produktów.
Metoda 5S w Lean Management to jedna z podstawowych technik, od której często rozpoczyna się wdrażanie szczupłego zarządzania. Może być z powodzeniem stosowana w różnych rodzajach organizacji, nie tylko w przemyśle, ale także w usługach czy innych dziedzinach.
Zasada 5S oraz system MES (Manufacturing Execution System) to dwa różne narzędzia stosowane w zarządzaniu produkcją w przemyśle, ale można je powiązać w kontekście efektywności i optymalizacji procesów produkcyjnych.
Zasada 5S pomaga poprawić efektywność pracy, zmniejszyć marnotrawstwo i stworzyć bardziej bezpieczne i przyjazne środowisko pracy. System MES służy do monitorowania, zarządzania i kontrolowania procesów produkcyjnych w czasie rzeczywistym.
Jak więc mają się do siebie 5S a MES? Wspólnym punktem, który je łączy jest dążenie do optymalizacji procesów produkcyjnych. Przykładowo, system MES może być używany do monitorowania wydajności produkcji, gromadzenia danych na temat zużycia surowców i czasu produkcji, a zasada 5S może być zastosowana na linii produkcyjnej, aby zminimalizować straty czasu związane np. z nieporządkiem i nieefektywnym rozkładem narzędzi i materiałów.
Współpraca między systemem MES a zasadą 5S na hali produkcyjnej może przynieść jeszcze więcej korzyści – prowadzi do bardziej efektywnej produkcji, poprawy jakości wyrobów i redukcji kosztów operacyjnych.
Nie korzystasz jeszcze z systemu MES? Dowiedz się dlaczego warto go wdrożyć w swojej firmie i jak to zrobić. Zobacz nasze materiały:
6 zalet systemów MES – poznaj je wszystkie
Praktyczna ścieżka wdrożenia systemu MES
Wdrożenie metody 5S w firmie produkcyjnej może znacząco poprawić organizację miejsca pracy, efektywność produkcji oraz jakość produktów. Jak skutecznie ją zaimplementować? Poniżej przedstawiamy krok po kroku, jakie działania należy podjąć:
- Zapoznaj się z metodą i zorganizuj zespół
Żeby skutecznie korzystać z koncepcji 5S w swojej firmie, należy przede wszystkim dobrze poznać i zrozumieć jej poszczególne etapy. Zanim przystąpisz do konkretnych prac, wybierz pracowników, którzy będą odpowiedzialni za poszczególne działania. Upewnij się, że zarząd rozumie korzyści wynikające z tej metody i aktywnie ją wspiera.
- Seiri – zidentyfikuj niepotrzebne przedmioty
Przeprowadź audyt miejsc pracy, identyfikując wszystkie niepotrzebne przedmioty, narzędzia i materiały. Wybierz te, które są niezbędne do produkcji, a niepotrzebne lub nieużywane usuń lub przechowuj w innych miejscach.
- Seiton – przypisz przedmiotom konkretne miejsca
Uporządkuj miejsce pracy, aby wszystkie niezbędne przedmioty były łatwo dostępne. Oznacz miejsca na narzędzia i materiały, aby każdy pracownik mógł łatwo zidentyfikować, gdzie się znajdują.
- Seiso – przygotuj harmonogram sprzątania
Przeprowadzaj regularne przeglądanie i porządkownie miejsca pracy. Zorganizuj harmonogram utrzymania czystości i upewnij się, że wszyscy pracownicy go przestrzegają.
- Seiketsu – stwórz standardy
Opracuj standardy pracy i zasady utrzymania ergonomii i porządku. Dostosuj je do konkretnej produkcji i poszczególnych stanowisk.
- Shitsuke – monitoruj i oceniaj
Wdrożenie 5S to ciągły proces. Stwórz system monitorowania i oceny, aby upewnić się, że standardy są przestrzegane. W razie potrzeby przeprowadzaj szkolenia pracowników w zakresie 5S, które wspomogą utrzymanie systemu.
- Udoskonalaj i mierz wyniki
Zachęcaj pracowników do zgłaszania pomysłów na ulepszenia procesów 5S. Regularnie przeprowadzaj przeglądy i aktualizuj standardy w miarę potrzeb. Określ konkretne wskaźniki wydajności, które można śledzić, aby ocenić skuteczność metody 5S, takie jak efektywność produkcji, jakość produktów i bezpieczeństwo pracy.
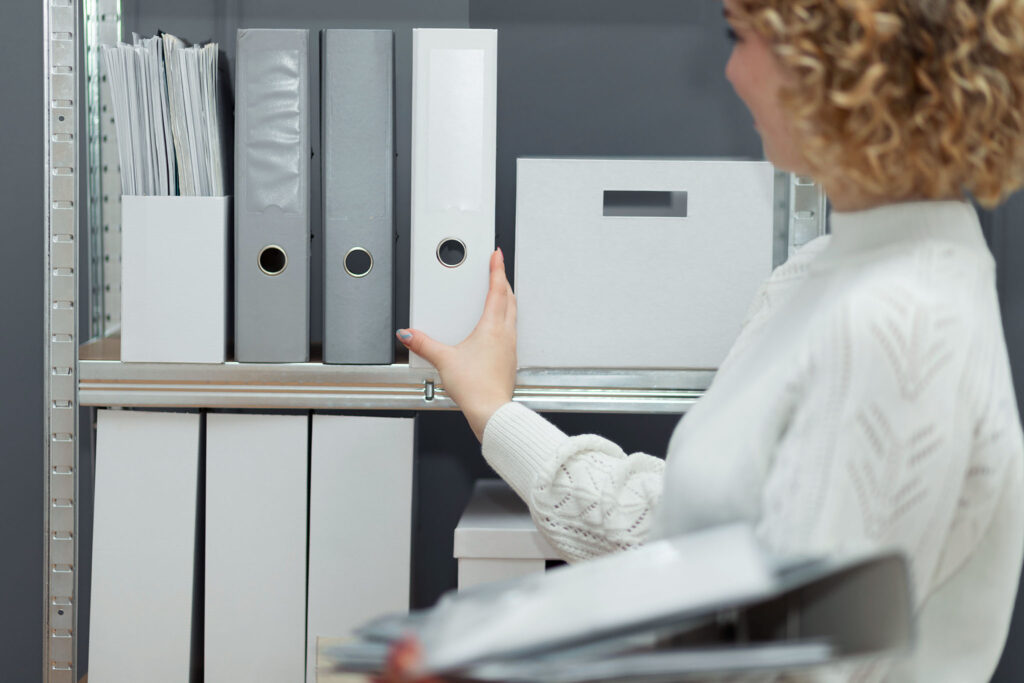
Oto kilka zalet koncepcji 5S:
- Poprawa efektywności – koncepcja 5S pomaga zidentyfikować i eliminować niepotrzebne elementy, narzędzia i materiały. Prowadzi to do zwiększenia przepływu pracy i efektywności operacyjnej.
- Zwiększenie bezpieczeństwa – porządkowanie i oznaczanie obszarów roboczych oraz narzędzi, pomaga zminimalizować ryzyko wypadków i kontuzji w miejscu pracy.
- Poprawa jakości – dzięki uporządkowaniu i oznaczeniu narzędzi oraz przestrzeni roboczej, łatwiej jest unikać błędów, pomyłek i braków, co przyczynia się do poprawy jakości produktów i usług.
- Oszczędność czasu – dzięki etapowi Seiton, narzędzia i materiały są przechowywane w logiczny sposób. Skraca to czas potrzebny na ich znalezienie.
- Wzrost satysfakcji pracowników – porządek i czystość w miejscu pracy mogą przyczynić się do lepszego samopoczucia pracowników, co z kolei może wpłynąć na ich motywację do pracy.
- Łatwiejsze wdrażanie innych metod zarządzania – metoda 5S stanowi solidne fundamenty dla wprowadzania innych metod zarządzania, takich jak Lean Manufacturing czy Six Sigma. Może to dodatkowo zwiększyć efektywność organizacji.
- Redukcja kosztów – poprzez eliminowanie marnotrawstwa, zwiększanie wydajności i poprawę jakości, zasada 5S może przyczynić się do redukcji kosztów operacyjnych firmy.
5S to metoda organizacji i zarządzania miejscem pracy, która ma na celu poprawę efektywności, bezpieczeństwa, jakości i ogólnej wydajności. Jej wdrożenie może przynieść wiele korzyści, jednak sukces tej koncepcji wymaga zaangażowania całego zespołu i utrzymania dyscypliny w dłuższym okresie. Metoda 5S nie może być jednorazowym wysiłkiem. Jeśli jest skutecznie wdrażana i utrzymywana, prowadzi do długotrwałych korzyści w postaci wyższej produktywności, niższego zużycia surowców i mniejszej ilości odpadów.
Przeczytaj o innych metodach, które mogą pomóc Ci w lepszej organizacji miejsca pracy:
Czy system MES może wspomóc zarządzanie procesem metodą Kanban?
Zobacz również
Chcesz dowiedzieć się więcej? Odwiedź naszą Bazę Wiedzy, gdzie znajdziesz artykuły i webinary przygotowane przez ekspertów, które pozwolą Ci poszerzyć swoją wiedzę.
Umów się na bezpłatną prezentację lub rozmowę na wskazany przez Ciebie temat.
Jak przebiega proces bezpłatnej konsultacji?

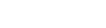
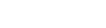
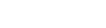
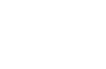
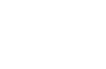
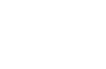
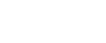
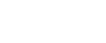
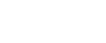
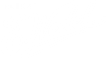
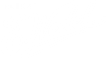
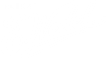



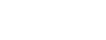
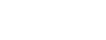
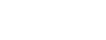



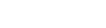
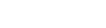
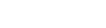
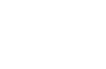
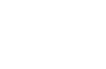
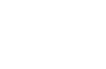
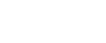
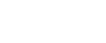
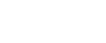
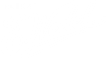
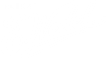
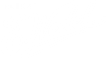



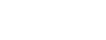
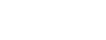
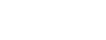



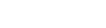
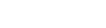
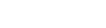
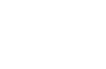
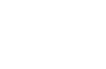
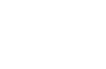
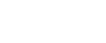
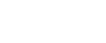
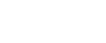
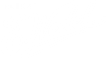
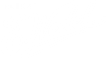
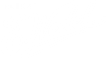



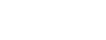
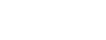
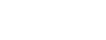



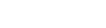
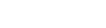
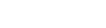
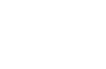
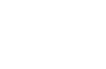
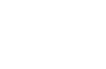
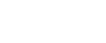
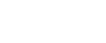
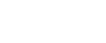
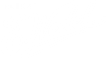
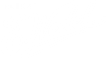
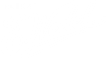



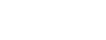
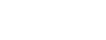
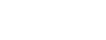